#3DExpress: Pelagus 3D and Doosan to Push 3D Printing Adoption in Korea
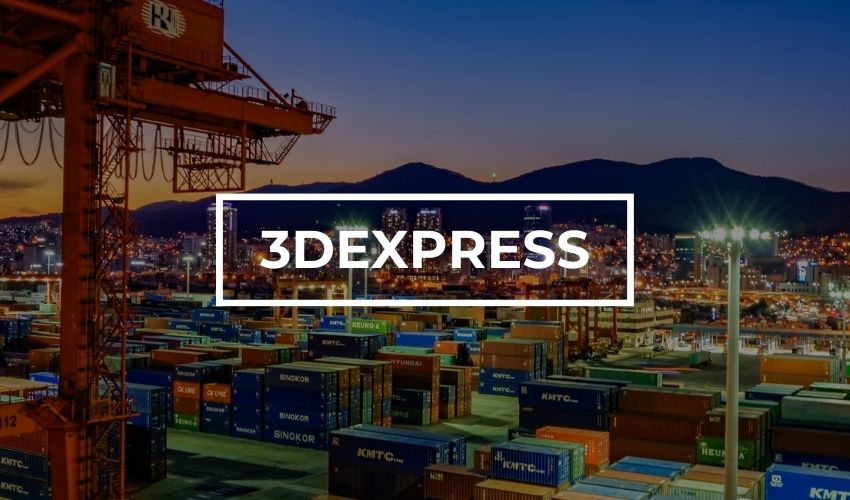
To round off the week, we’d like to take a look back at five news items that have left their mark on the additive manufacturing sector. And we’ll start with news from Pelgas 3D and Doosan Enerbility who are seeking to further push adoption of on-demand 3D printing in Korea in the maritime and offshore industries. We’ll then take a look at the medical world, where 200 patients have received a 3D-printed ocular prosthesis. Finally, we’ll meet up on a Formula 1 circuit to see the performance of a 3D-printed drone. Happy reading and have a great weekend!
Pushing 3D Printing in Korea
A peninsula surrounded by water on all sides, it is perhaps not surprising to hear that Korea’s maritime industry is quite robust. However, its adoption of additive manufacturing has been less so, though two companies hope to change that. Pelagus 3D, a joint venture company of thyssenkrupp and Wilhelmsen, has signed a memorandum of understanding to push the adoption of 3D printing in the Korean maritime sector. The collaboration is expecte dto bring together Pelagus 3D’s experience in maritime AM with Doosan Enerbility’s experience in spare parts to address supply chain issues in the country. Knelip Ong, CEO of Pelagus 3D, commented, “The MOU signing with Doosan Enerbility marks a pivotal milestone in creating a more resilient and efficient spare parts supply chain. This collaboration will drive technological innovation and deliver enhanced value to our network in Korea. The Pelagus Platform will ensure seamless integration and accelerate adoption of AM among OEMs and end users.”
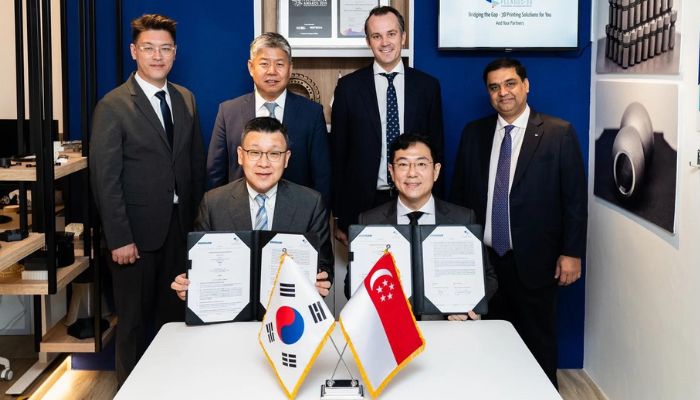
The signing of the MOU between Pelagus 3D and Doosan to promote 3D printing in the maritime sector in Korea (photo credits: Pelagus 3D)
3D Printed Eye Prostheses
At the Fraunhofer Institute, a team of researchers has used additive manufacturing and artificial intelligence to more quickly design and make customized eye prostheses. According to them, this combination could reduce manufacturing time by 80%, thus overcoming certain production challenges. The prosthesis has a very realistic appearance and is said to be very comfortable, avoiding the need for the wearer to change the implant every 5 to 10 years. Created using PolyJet technology in just 90 minutes, it can be installed in 15 minutes. After 10 successful clinical trials at Moorfields Eye Hospital, a further 200 adult patients have been fitted with a 3D-printed ocular prosthesis.
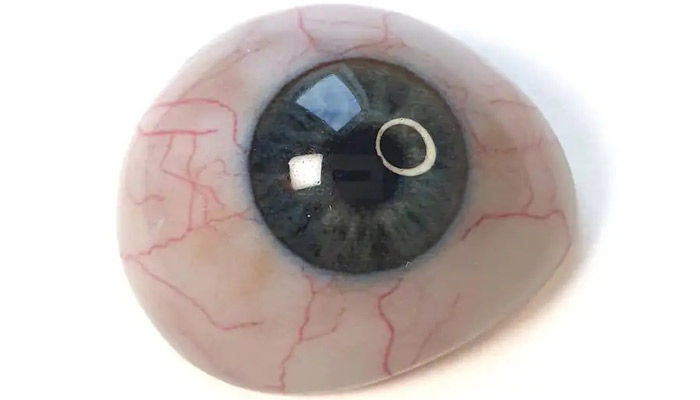
Photo Credits: Fraunhofer Institute
A New Feature in Velo3D’s Software
Velo3D, a manufacturer of metal 3D printers, has developed an additional tool for its print preparation software, Flow. Called Developer, it offers greater flexibility and control to users of the American company’s technology. Specifically, Developer enables users to access print parameters at the software editor level, import parameters already developed on previous projects, or optimize them for specific applications. Thomas Pomorski, Head of Additive Manufacturing at Ursa Major, comments: “It can be a challenge to produce repeatable results across different metal 3D printers—even when they’re the same model of printer—however, Velo3D’s solution can consistently produce parts within spec across any of its printers, which provides huge benefits for companies looking to scale production of their parts.”
A 3D Printed Drone That’s Faster Than a Formula 1 Racecar?
Dutch company Dutch Drone Golds has designed a highly original drone: a system capable of accelerating twice as fast as a Formula 1 car! It can reach speeds of 300 km/h in just four seconds. And the reason we’re talking to you about it today is that it was designed in part using 3D printing. Multiple iterations were created using 3D technologies, enabling us to test the device and see what maximum speed it could reach. We’ll let you watch the video, as it speaks for itself: the drone was able to follow racer Max Verstappen around the Silverstone Grand Prix circuit for a full lap. The result is amazing!
Two New 3D Printing Dental Resins
Healthcare professionals are making increasing use of additive manufacturing, especially dental specialists. They can count on a method of producing their prostheses, guides, tooling, etc. that is more precise, faster and of higher quality. Resin 3D printing processes are particularly popular, as they can achieve very high levels of detail and resolution. To meet these growing needs, 3D Systems has announced the development of two resins, NextDent Jet Denture Teeth and NextDent Jet Denture Base, to enable dental professionals to design durable, wear-resistant monolithic dental prostheses. The first material has been developed to reproduce the rigidity and aesthetics of teeth, while the other resin is designed to absorb shocks.
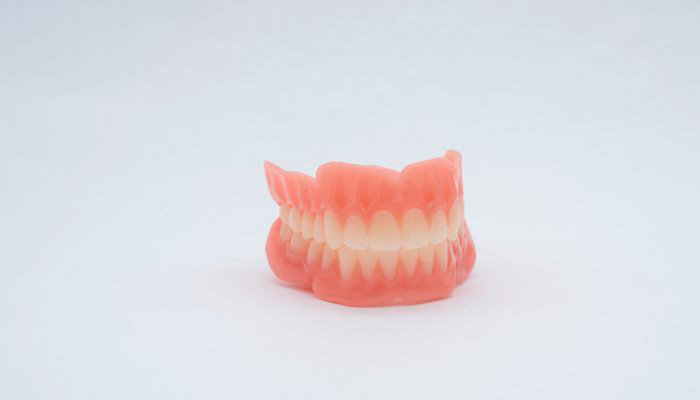
Photo Credits: 3D Systems
What do you think of Pelagus 3D and Doosan Enerbility’s MOU to push adoption of 3D printing in Korea? Let us know in a comment below or on our LinkedIn, Facebook, and Twitter pages! Don’t forget to sign up for our free weekly newsletter here, the latest 3D printing news straight to your inbox! You can also find all our videos on our YouTube channel.