3DExpress: 3D Printed ‘Ice Dollhouse’ to Pave the Way for Construction in Cold, Remote Areas
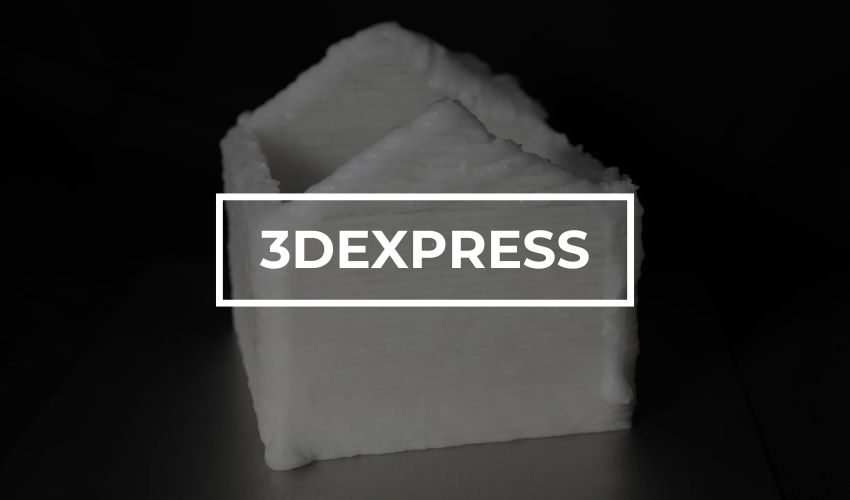
In this week’s #3DExpress, we welcome the wintry winds of December with a rather chilly offering. U.S. army scientists have successfully 3D printed an ice dollhouse, which they hope will open up possibilities for construction 3D printing in cold, remote areas for things like igloos and road repair. Next, AI is dominating the 3D printing market and will continue to grow, according to a new research study. Then, learn more about a case study from Dyndrite, Aconity and Equispheres which looks at how to have speed, cost-effectiveness and superior surface quality with metal 3D printing. Wrap it up with a 3D printed lightweight frame being used for a project that is simulating bees and sports shoes that can be made using AI, 3D printing and a smartphone. Happy reading and have a great weekend!
Army Scientists Made an Ice Dollhouse With 3D Printing
In what is not quite a Christmas miracle, but certainly a huge advancement for construction in cold, remote areas, the U.S. Army Corp of Engineers has successfully 3D printed an ‘ice dollhouse.’ Made using a modified ceramic 3D printer, the structure was made at the Cold Regions Research and Engineering Laboratory (CRREL) using water mixed with tiny fibers of wood pulp that needed to be frozen layer by layer during the deposition processes. “In scenarios where your usual construction methods don’t work, can you use 3D printing with the natural available materials and take advantage of the cold temperatures to use ice instead, to get you whatever you need through the winter?” comments Kiera Towell, a research materials engineer at CRREL when explaining the goals of the project. Although challenges still remain, especially with the material itself, ensuring that it’s fluid enough to flow through a nozzle and then solid once extruded to hold its shape, the scientists are working on expanding the project to use a larger printer to make bigger, taller structures that will freeze faster to go from an ice dollhouse to an ice doghouse!
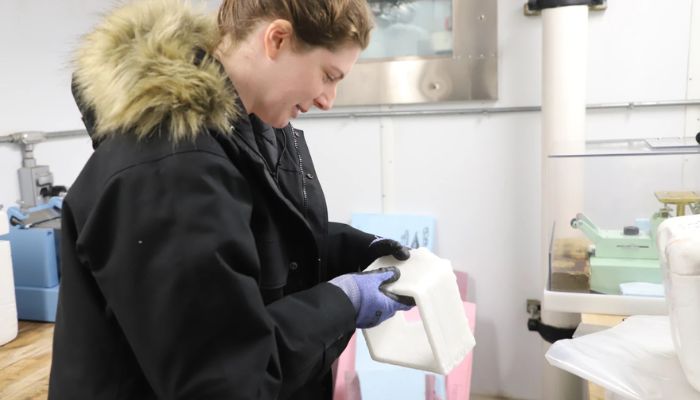
Photo Credits: Justin Campfield/US Army Corps of Engineers
Global AI 3D Printing Market Set for Sharp Growth
Artificial intelligence seems to be on everyone’s mind. Over a year since ChatGPT showed its capabilities, we have continued to see how AI can be used to improve processes in our daily lives. This includes in 3D printing. In fact, AI is so well-suited to additive manufacturing that a recent report from the Business Research Company estimates that the market size for AI in 3D printing will grow from an already impressive $1.7B in 2023 to $9B with a compound annual growth rate of 39.7%. Drivers of the growth can be attributed to a need for increased efficiency and reduced production costs, coupled with an increasing demand for more customized products, more optimized 3D printing and increasing automation. A trend to certainly watch in the years to come!
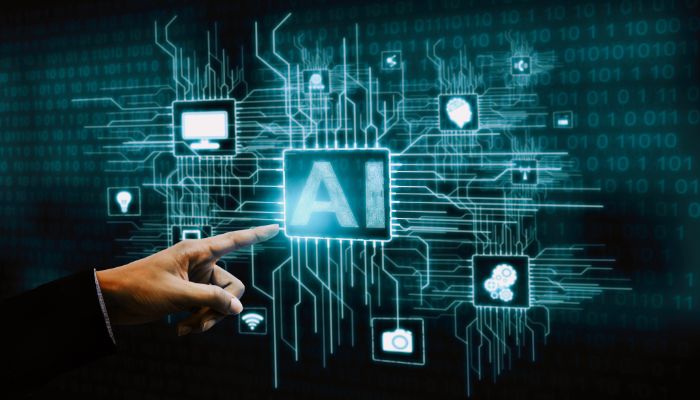
AI 3D printing is showing sharp growth
New Case Study on LPBF
A collaboration between Equispheres, Aconity3D, and Dyndrite has produced a case study on how to achieve high productivity, improved surface quality, and significant cost savings with LPBF. This so-called ‘Holy Grail’ of metal 3D printing, as claimed in a press release from Dyndrite, comes from the combination of laser beam shaping with highly engineered AM powders, which by themselves led to 7-9X productivity gains, with Dyndrite LPBF Pro then added to ensure high surface quality. The case study is downloadable and will help users to understand not just how the combination of software, material and process contributes to better 3D printing, but also real-world applications.
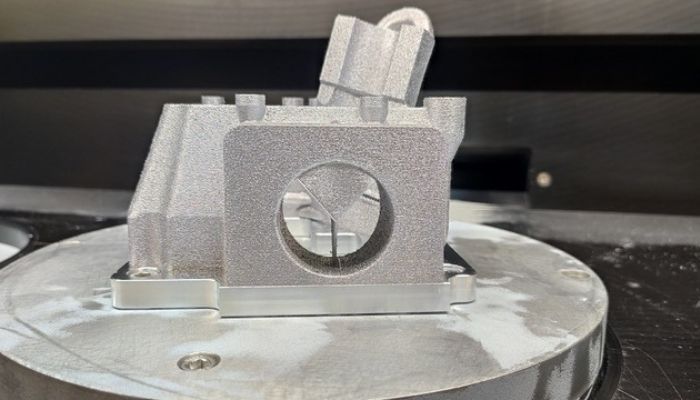
A part made by Aconity3D and Equispheres (photo credits: Equispheres)
FDR Technology From 1zu1 is Used for Lightweight Support Frames in the Festo Flight Project
1zu1 Prototypen GmbH & Co. KG is a high-tech company and expert in the field of 3D printing. Together with automation specialist Festo, the companies developed a lightweight support frame using FDR (Fine Detail Resolution) technology as part of an autonomous flight project. This frame is used in the BionicBee, which simulates the swarming behavior of bees and from which Festo hopes to gain important insights for automation technology. During production, FDR laser sintering technology made it possible to manufacture functional plastic parts with intricate structures and strong mechanical properties, which allowed a detail resolution of 0.05 millimeters and thus led to particularly precise printing results. As weight is of central importance in aviation, the frame was made from PA 11 and the 3D-printed frame weighed just 3 grams, with the struts only 0.9 millimeters thick. As a result, the construction provides an extremely light yet stable support structure. In addition to the low weight, the frame offers further advantages such as stability, flexibility and the possibility of individual customization. “The results are visually equivalent to particularly detailed stereolithography, but many times more robust. The feather-light and flexible parts withstand take-off and landing without any problems,” explains Mattias-Manuel Speckle, Head of Additive Manufacturing Prototyping at Festo.
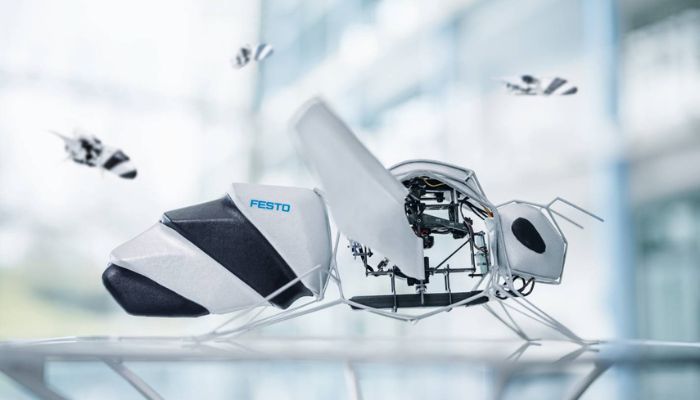
Festo’s BionicBee sets new standards for autonomous flight and, thanks to 3D-printed components from 1zu1, the flying object weighs just 34 grams (photo credits: Festo SE & Co. KG)
Fitasy Makes Customized 3D-Printed Sports Shoes Using smartphone Scanning and AI
The last piece of news in our #3DExpress is aimed primarily at sports enthusiasts. At the ISPO sports trade fair in Munich, the US company Fitasy presented customized 3D-printed shoes that are manufactured using a smartphone scan and 3D printing. AI modeling is also used to develop a shoe that is perfectly tailored to the individual’s needs. But how exactly does the production process work? Using the Fitasy app, customers can easily take a 3D scan of their feet with their smartphone. The data is then sent to Fitasy, which uses AI modeling to create a customized shoe model. The shoe is then produced from thermoplastic using a 3D printing process. It is particularly important to Fitasy that the person’s medical factors are also taken into account, as are lightness and comfort when worn.
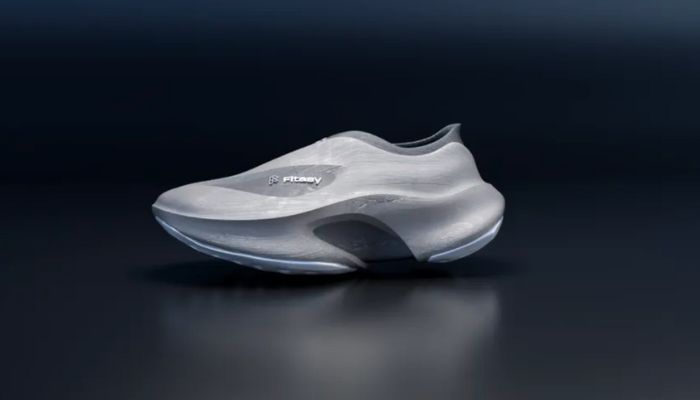
Fitasy combines mobile 3D scanning, AI technology and 3D printing to create customized shoes (photo credits: Fitasy)
What do you think of this ice dollhouse? Let us know in a comment below or on our LinkedIn, Facebook, and Twitter pages! Don’t forget to sign up for our free weekly Newsletter here, the latest 3D printing news straight to your inbox! You can also find all our videos on our YouTube channel.
*Cover Photo Credits: Justin Campfield/US Army Corps of Engineers