#3DExpress: Facial Implants Made Using 3D Printing
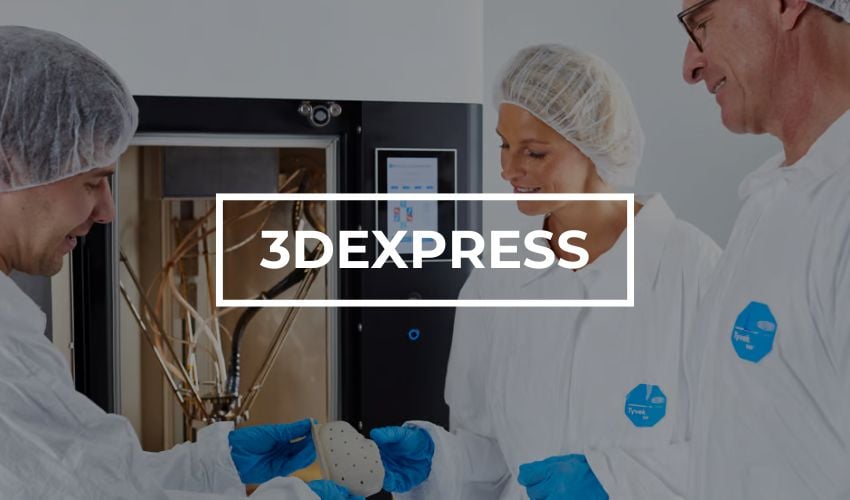
In this issue of #3DExpress, we once again present five exciting news items from the world of 3D printing that have caused a stir this week. First up: the 3D-printed facial implant that the University Hospital Basel has produced and successfully used on site. Next an underwater drone, a 3D-printed bridge made from a wind turbine blade, more affordable metal 3D printing and a concrete arch! Enjoy reading and have a great weekend!
3D Printing Facial Implants With PEEK
On March 18, the first 3D-printed facial implant was inserted in an operation at the University Hospital Basel. The implant was manufactured directly at the point of care in coordination with the patient data. The hospital used the XT 220 MED medical 3D printer from 3D Systems for this purpose. This printer was designed to be used in a clean room specifically for medical applications. The post-processing processes are also validated. On-site production enabled doctors and technicians to work closely together to produce a custom-fit implant for the patient. Prof. Florian Thieringer from the University Hospital Basel summed up the advantages of 3D printing at the point of care, “By being directly involved here at the hospital in both the design and manufacture of patient-specific implants, we can tailor treatments precisely to individual needs, respond more quickly and improve surgical outcomes.”
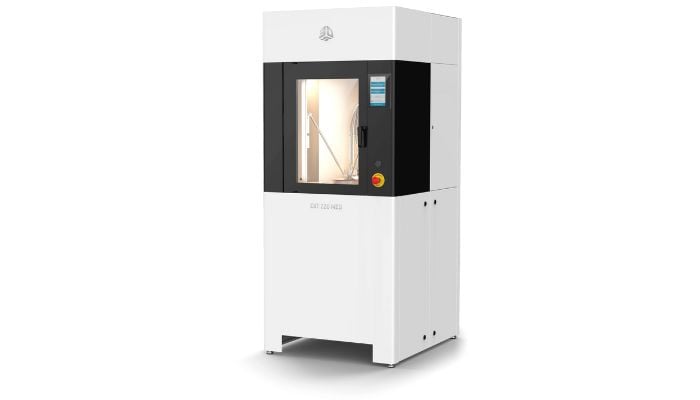
Photo Credits: 3D Systems
ROYAL3D presents prototype of a water drone for maritime operations
Royal3D, a Dutch company specializing in 3D printing services, has unveiled the prototype of the ShearWater Aquatic Drone, an autonomous drone designed for operations in the maritime sector. This modular and parametric drone is designed to improve maritime operations by facilitating monitoring, data collection and risk mitigation in extreme environments. The project was partially supported by the European Union’s CrossRoads program and features the use of Royal3D’s advanced 3D printing technology, which uses infrared cameras to accurately control the adhesion of layers during the manufacturing process. The ShearWater is reinforced with PETG fibers, giving it a combination of lightness, stiffness and durability. Although the drone is only a prototype, Royal3D has stated that it is a stepping stone for companies looking to integrate their own autonomous systems into maritime operations.
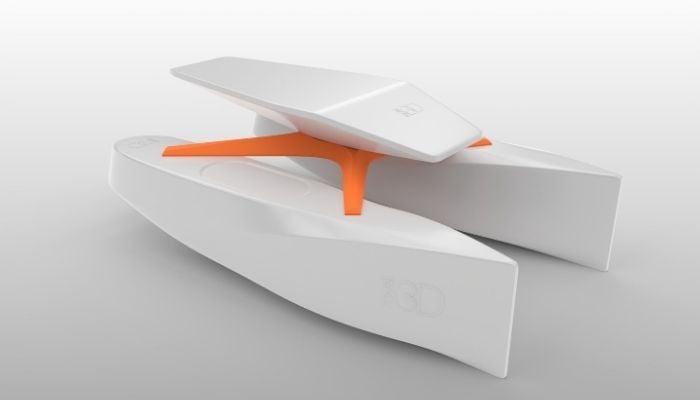
Photo Credits: ROYAL3D
Making Metal 3D Printing More Profitable
Californian start-up Additive Plus this week unveiled a new range of metal laser powder bed fusion machines. The goal? To make the technology more affordable and easier to use. Its three 3D printers, the A30, A50 and A100, differ in terms of built (from the smallest to the largest, respectively) and laser power (200 or 300 watts). They are compatible with steel, various alloys and aluminum. Additive Plus claims that the AO range has been designed for research and development applications as well as small series production. The machine is compact and can be ordered from $59,000, which is relatively affordable compared with competing solutions. Whether the results are comparable remains to be seen.
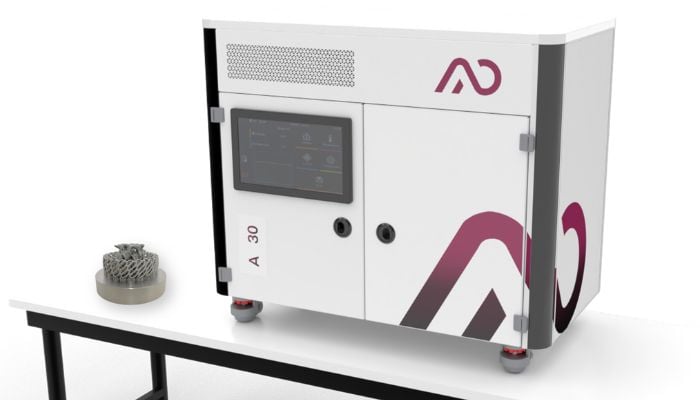
The A30 3D printer is the smallest model (photo credits: Additive Plus)
A 3D Printed Bridge Made Out of a Wind Turbine Blade
It’s a propeller! It’s a wind turbine blade! No, it’s a bridge! Ok, it is maybe not as exciting as Superman, but a Dutch company has done something fairly remarkable by repurposing a decommissioned wind turbine blade to make a 3D printed modular bridge. Done by Poly Products, known for its composite processing expertise, the final structure was made as a part of the Circular Viaduct Project, an initiative that is led by the Dutch Ministry of Infrastructure and Water Management. The goal? Well, to create an innovative bridge while also reusing blades from a nearby wind farm that was shutting down. The resulting structure spans 39 feet (12 meters) and measures 10 feet (3 meters) wide and is able to support loads of up to 5 tons. The best part? The project was able to fully harness the potential of the wind turbine blades which are strong, lightweight and highly weather-resistant, exactly what is needed for a bridge, helping to minimize the use of new raw materials. Now that is what we call reduce, reuse, recycle!
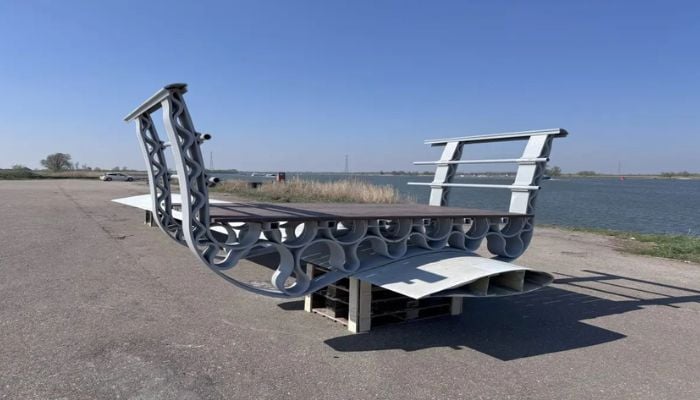
Photo Credits: Poly Products
Vertico and Zaha Hadid Architects Print a Concrete Arch
The Dutch company Vertico presented its new 3D printing project this week: In collaboration with Zaha Hadid Architects, it designed an arch called Aevum for the INTERNI exhibition ‘Cre-Action’ at the University of Milan La Statale. It is a 6 x 6 meter structure that combines two arches: one is made of marble and was made in the traditional way, while the other was 3D printed from concrete. According to Vertico, it took just two weeks from receipt of the CAD model to delivery of all the components, i.e. 21 pieces. The printing itself is said to have taken just 48 hours. This structure is intended to show that it is possible to combine craftsmanship with state-of-the-art technology in architecture. Volker Ruitinga, CEO of Vertico, added, “This project is a real milestone because it establishes the legitimacy of 3D-printed concrete by placing it alongside the craftsmanship of marble. The speed, low cost, freedom of form and short delivery times that additive manufacturing promises are clearly demonstrated here.”
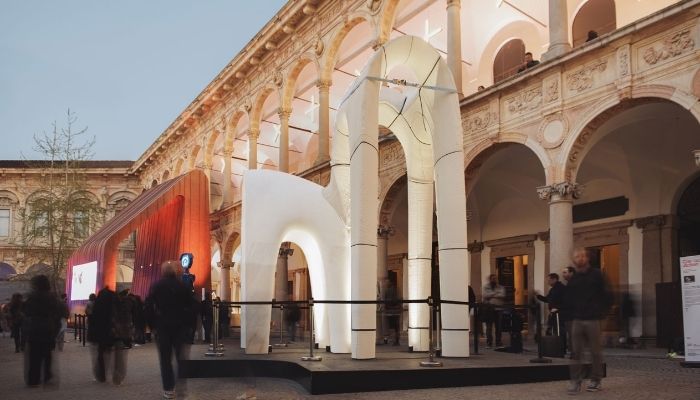
Photo Credits: Vertico
What do you think of the use of 3D printing for facial implants? Let us know in a comment below or on our LinkedIn, Facebook, and Twitter pages! Don’t forget to sign up for our free weekly Newsletter here, the latest 3D printing news straight to your inbox! You can also find all our videos on our YouTube channel. If you are interested in finding more 3D printing news in the medical and dental sector, visit our dedicated section HERE.
*Cover Photo Credits: 3D Systems