#3DExpress: 3D Printed Headrests in the New Sports Car FromAlpine
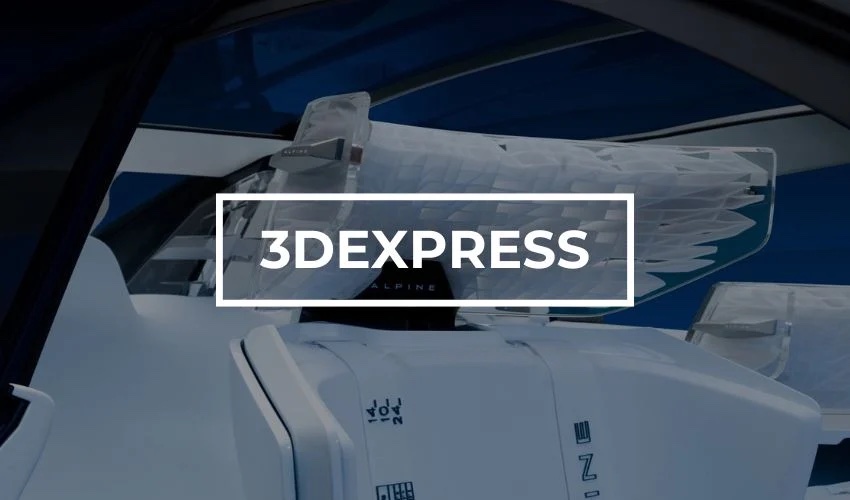
This week in our new 3DExpress, we bring you the new 3D-printed headrests produced by ERPRO for carmaker Alpine. They are made from a bio-elastomer. We’ll also take a look at the MASSIF project announced by AddUp and its partners: the aim is to enable a larger, more environmentally-friendly metal 3D printing process. Last but not least, we’ll be presenting a new de-soldering solution for large-format metal parts, to be found at Formnext 2024.
ERPRO 3D Prints New Parts for Alpine
Having already designed some accessories for the Peugeot 308, French 3D printing service ERPRO has now announced a collaboration with Alpine. Its first 100% electric sports car, the A390_β, features 3D-printed headrests. They were produced using the SLS process, with the bio-sourced Pebax® Rnew® elastomer developed by Arkema. The headrests are encased in a transparent material reminiscent of blocks of ice – the car manufacturer is said to have drawn inspiration from nature, and the Alps in particular, to develop its new show car.
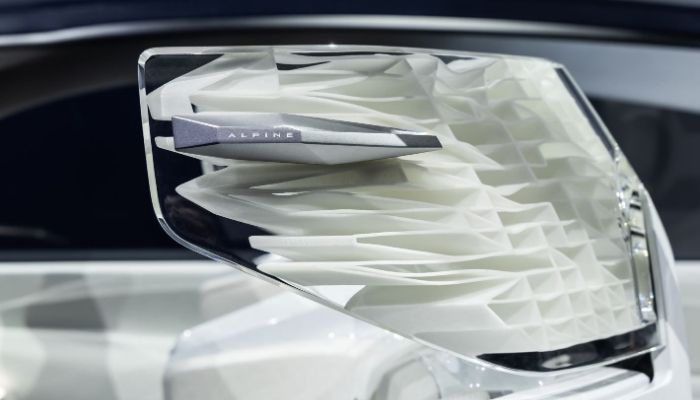
Photo Credits: Alpine
AddUp and XXL Metal 3D Printing
Metal 3D printing solution manufacturer AddUp recently announced a new development project. Called MASSIF (for Metal Additive System, Sustainable, Industrial, Eco-Friendly), it aims to design a large-format machine to increase industrial productivity and printing capacity. Clear objectives have been announced: +300% in terms of productivity, a volume 12 times greater than current AddUp 3D printers, and 10% less metal waste generated. This metal machine will be developed in partnership with Cailabs, CETIM, Dassault Systèmes, ISP Systems and Vistory. Julien Marcilly, CEO of AddUp, explains: “It was the association of the best experts, each in their field, that allowed us to launch the MASSIF project. This technological leadership in large-scale metal 3D printing will enable us to meet the challenges of energy transition and productivity for aeronautics, defense and space players, always in a co-design approach by AddUp with its clients.”
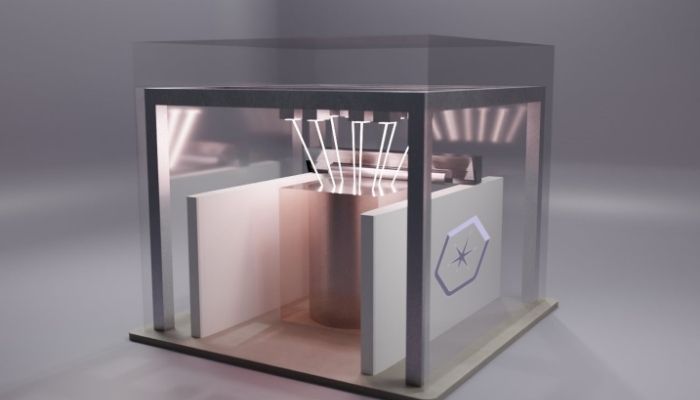
Illustration of the MASSIF concept (photo credits: AddUp)
A New Depowdering System for Large Parts
Solukon is a German manufacturer of post-processing solutions. It has just unveiled its new SFM-AT1500-S system for fast, efficient depowdering of metal parts. But what’s particularly interesting about this machine is that it can handle parts weighing over 2 tons! This is the manufacturer’s largest machine, capable of handling components measuring 600 x 600 x 1,500 mm or 820 x 820 x 1,300 mm, for a total weight of 2,100 kilos, including plates. The solution is currently being tested by two 3D printer manufacturers. It is due to be presented for the first time at the Formnext trade show from November 19 to 22.
PROTEC3D and Its Line of Ballistic Protection Solutions
German company Mehler Protection has introduced PROTEC3D, an innovative line of ballistic protection solutions using 3D printing. Specifically, it has used this technology to offer greater design flexibility and reduce component weight. Using an SLM (Selective Laser Melting) printer, they were able to create complex structures impossible to achieve using traditional methods, guaranteeing consistent, customized ballistic resistance. Thanks to 3D printing, they were able to incorporate additional features, such as cooling channels and mounting points, in a single process, improving the structural integrity and durability of the products. The company is applying this technology to develop STANAG 4569-compliant solutions, extending its product range and application to military vehicles, ships and other critical environments.
Nikon Adds Powder Feed System to LM102A Machine
Nikon, known for its optical and photographic products, recently announced the addition of a powder feed system to its Lasermeister 102A metal 3D printing system. The LM102A works with DED technology, and the new Additional Powder Feeder (APF) system enables multiple metal powders to be printed simultaneously. This makes it possible to manufacture parts with different material properties, and to develop new alloys with small quantities of powder. The APF is also available as an option for existing systems. This innovation is particularly interesting for R&D, aerospace, defense and energy. Dr Akira Tanaka, Head of Materials Research at Nikon, adds: “With APF, we can precisely control the alloy composition during printing. This opens up entirely new possibilities in lightweight construction and the optimization of thermal properties.”
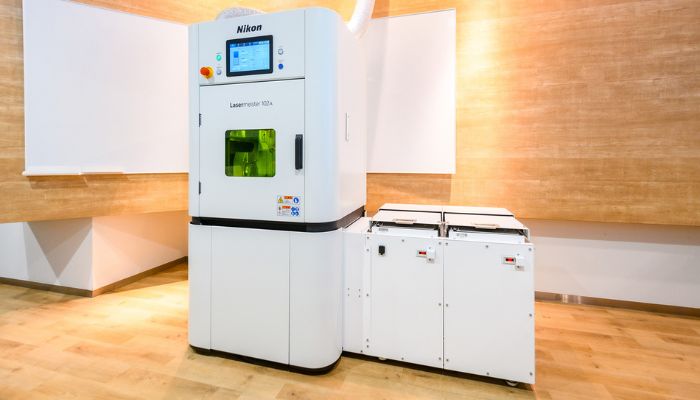
Photo credits: Nikon
What do you think of these 3D printed headrests that were made for Alpine? Let us know in a comment below or on our LinkedIn, Facebook, and Twitter pages! Don’t forget to sign up for our free weekly newsletter here for the latest 3D printing news straight to your inbox! You can also find all our videos on our YouTube channel.