How Recycling MJF & SLS Powder into FDM Filament Promotes Sustainability in Additive Manufacturing
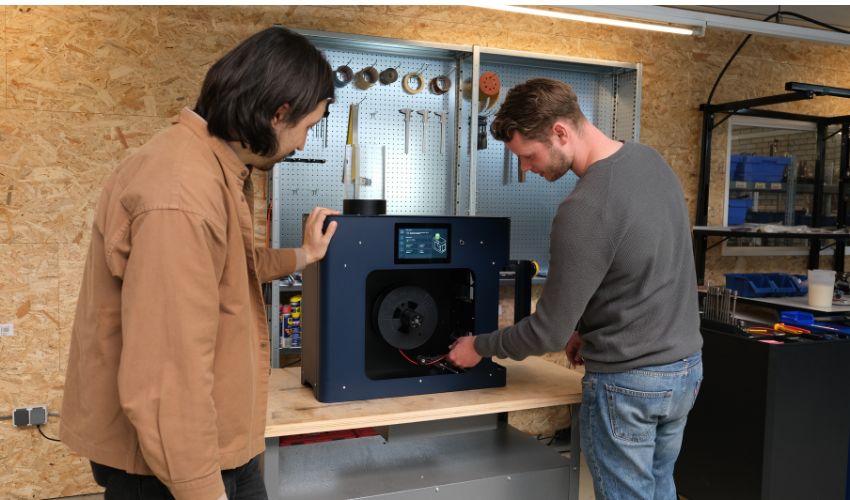
Never has there been so much discussion of environmental damage and awareness of our impact on the planet. Whatever the sector, environmental protection is at the heart of many concerns. And the 3D printing market is no exception. With the rise of additive manufacturing also comes the need to adopt sustainable practices that reduce waste and promote a circular economy. One of the ways to achieve this is by transforming and reusing waste materials.
3devo, a Dutch company specializing in the development and recycling of 3D printing materials, is asking just such questions and has recently developed a solution for recycling MJF/SLS powder waste into high-quality 3D printing filament. MJF and SLS are both powder-based 3D printing technologies but differ in key aspects. For example, MJF produces parts with more uniform mechanical properties and better surface finishes, while SLS offers a broader range of materials and finer resolution for intricate details. Both MJF and SLS powders can be processed efficiently by 3devo’s recycling system. In so doing, the company is promoting and encouraging a circular economy.
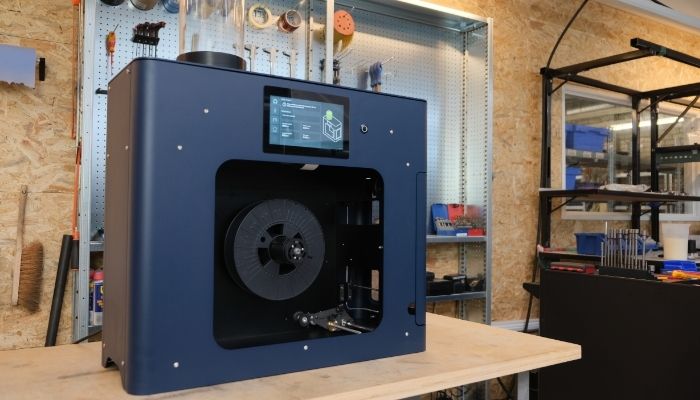
3devo developed a solution for recycling MJF/SLS powder into 3D printing filament
Quantifying the Environmental Impact
The additive manufacturing industry, while innovative, generates a significant amount of waste, particularly in the form of unused or discarded microplastics, such as SLS and MJF powder. The powder is typically made of PA12 Nylon and other thermoplastics, although in the case of SLS printing, the powder can also include other materials such as polyamides, thermoplastic elastomers or composite powders mixed with glass or aluminum.
A MJF (Multi Jet Fusion) 3D printer can leave a high percentage of unused powder after a print typically equating to 2-3kg of non-reusable powder. If a MJF printer is used on a very regular basis, users can easily accumulate over 1,000kg of waste in a year. By converting this waste into filament, companies can reduce their material waste by half, effectively cutting down the need for virgin plastic production. This not only conserves resources but also significantly reduces the carbon emissions associated with the production and transportation of new materials.
Traditional MJF/SLS Powder Disposal Methods
Currently, disposing of MJF powder presents a significant environmental challenge. When this powder cannot be recycled, it is typically sent to landfills, incinerated, or subjected to specialized waste treatment. Landfill disposal, the most common method, contributes to the growing issue of plastic pollution, with the powder potentially taking hundreds of years to decompose. Furthermore, harmful components in the powder may leach into the soil and groundwater, posing long-term environmental risks. Incineration, while reducing waste volume, can release toxic gases and pollutants unless stringent emission controls are in place, raising further concerns about air quality. Even with specialized chemical treatments, the disposal process can be costly and still carries the potential for environmental harm.
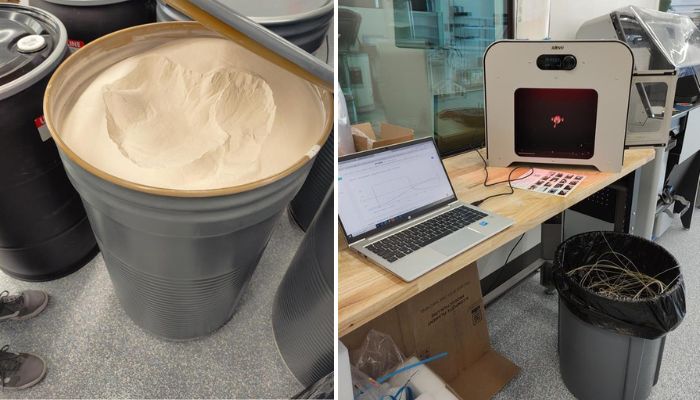
Recycling MJF powder is easier thanks to 3devo’s solution
Given these challenges, recycling MJF and SLS powder makes both environmental and economic sense. Unlike many other recycling projects that require sorting materials, the nylon powder is already relatively uniform, making it an ideal candidate for recycling. During the MJF process, the powder becomes contaminated by the detailing agent used in the process, making it unsuitable to reuse with MJF – but this does not cause an issue when it is turned into FDM filament.
How to Turn Waste Powder into FDM Filament With 3devo
The process of converting waste MJF powder into FDM filament is straightforward with the right equipment, such as a 3devo Filament Maker. This compact, all-in-one solution holds a significant advantage over traditional filament extrusion systems, which often involve multiple in-line components (such as the extruder, air-cooling path, and spooler), resulting in a much larger footprint.
The 3devo Filament Maker streamlines the entire process, allowing users to produce almost 3kg of reusable filament per day, equating to around four full spools. By providing a compact and efficient system, 3devo enables companies to integrate filament recycling directly into their operations, saving space and reducing complexity.
During extrusion, there are several data points which can be monitored to ensure high quality filament. These include the screw speed (used to maintain even distribution and uniform melting of the powder), cooling (to prevent the filament from becoming too brittle or retaining excess heat), and extrusion speed (a slower speed allows more time for cooling, helping maintain a consistent filament diameter). Users can make necessary adjustments to the extrusion speed and cooling settings to keep the filament within the desired range.
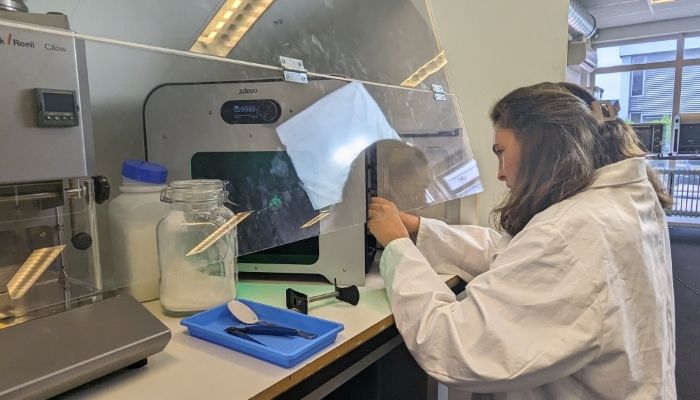
Converting waste MJF powder into FDM filament is straightforward with the right equipment
Benefits of the 3devo Filament Maker
A prime example of the benefits of this process comes from Arizona-based AZ3D prototyping company, which has equipped itself with the 3devo Filament Maker machine and reaped the benefits.
Specializing in MJF and SLA additive manufacturing, AZ3D faced a significant challenge in managing and ethically disposing of its used nylon powder. The company had accumulated seven 55-gallon drums of this waste, each weighing approximately 130kg, and traditional plastic pelletization companies were unwilling to handle the MJF material, leaving AZ3D without a viable recycling solution.
After three years of searching for a sustainable solution, AZ3D discovered 3devo who embraced the challenge of recycling MJF material. AZ3D sent a sample of their waste to 3devo’s facility in the Netherlands for testing. Through several phases of optimization, 3devo successfully produced filament from the MJF material, demonstrating that this waste could be transformed into a valuable resource.
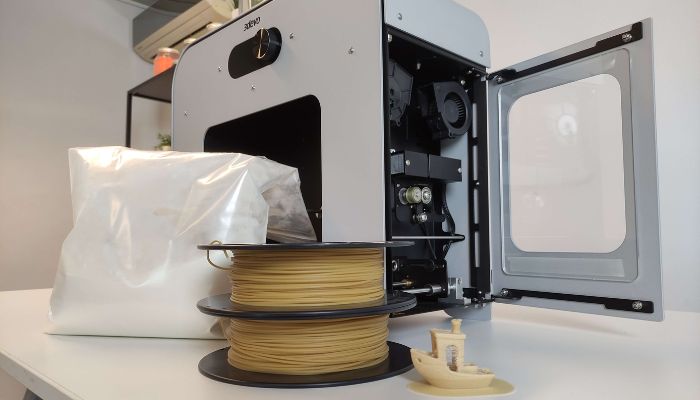
3devo’s machine can be integrated easily into the workflow
These conclusive tests prompted AZ3D to acquire their own machine. After receiving comprehensive training from 3devo to understand how to integrate it into their workflow, they were able to start producing their own filament in-house.
With an in-house filament extrusion system, AZ3D can now manage MJF powder waste ethically, significantly reducing the company’s environmental footprint and preventing microplastic pollution.
AZ3D’s founder, Rocky Parkerton, reflected on the success of this partnership: “The hard part was finding 3devo and a machine that wouldn’t seize up or break down. We may end up having to invest in more Filament Makers. But that seems like a good problem to have.”
Long Term Benefits for Manufacturers
The long-term benefits of adopting plastic recycling practices like those offered by 3devo are vast. Companies that incorporate recycled SLS/MJF powder into their production processes can expect to see significant cost savings over time. By reducing the need for expensive disposal methods, these companies can lower their expenditure while simultaneously decreasing their environmental impact.
Beyond this, as sustainability becomes an increasingly important factor in consumer choices and regulatory requirements, companies that adopt such practices will be better positioned to meet these demands. Using recycled materials can help companies achieve environmental certifications, such as ISO 14001, which can be a significant advantage in a competitive market.
On an industry-wide scale, if more companies adopt the practice of recycling SLS/MJF powder, the cumulative reduction in plastic waste could be substantial. This widespread adoption could lead to a significant decrease in the amount of plastic waste generated by the 3D printing industry, contributing to global sustainability goals and setting a new standard for environmentally responsible manufacturing.
One thing is certain, the solution developed by 3devo can help manufacturers adopt this approach and promote better recycling of plastic powder, all while contributing to a circular economy. To learn more about 3devo’s recycling process, take a look at their Filament Makers.
What do you think of 3devo’s solutions? Can they contribute to the recycling of additive manufacturing waste? Let us know in a comment below or on our LinkedIn, Facebook, and Twitter pages! Don’t forget to sign up for our free weekly newsletter here for the latest 3D printing news straight to your inbox! You can also find all our videos on our YouTube channel.
*All Photo Credits: 3devo
I love the photo of the 3Devo extruder above a bin full of waste filament……just about sums up my experience with the machine….