#3DStartup: One Click Metal Wants to Make Metal Additive Manufacturing Accessible to All
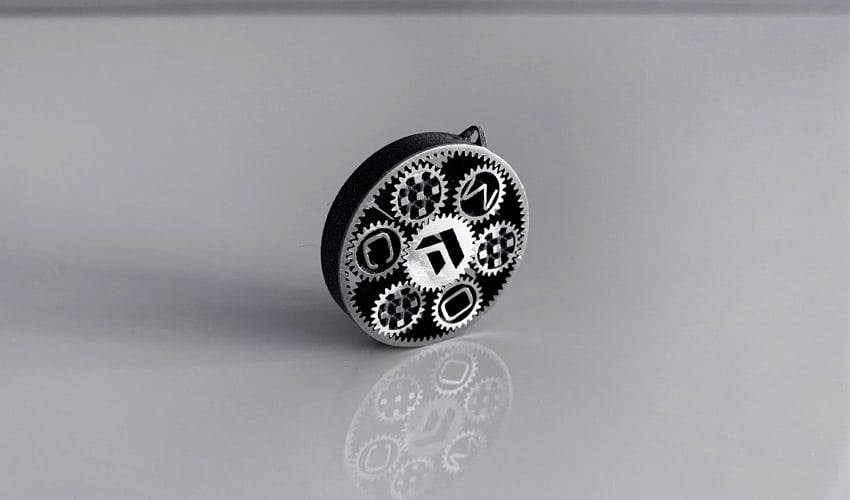
We first met German startup One Click Metal at Formnext 2019. Its goal is clear: it wants to democratize access to metal additive manufacturing by offering a printing solution that is easier to use, a powder system that is less complex to handle, all at a more affordable price. Its 3D printer is based on the laser powder fusion process, available at today at just over a hundred thousand dollars, which is an affordable cost relative to other offerings on the market. One Click Metal hopes that more companies will be able to access this technology full of possibilities and wishes to participate in the worldwide development of metal additive manufacturing. We met with the team of this Stuttgart-based startup to understand how its products can help with the adoption of 3D metal technologies.
3DN : Can you present yourself and your link with AM?
Our team belongs to the generation that already had their first experience with 3D plastic printers at university. To create a design with the computer, manufacture it with the 3D printer and hold the finished product in your hands the next day without having to rely on external manufacturing is a feeling of great autonomy and independence. This speed and freedom, along with the relatively easy access to FDM and SLS printers, opens up a whole new world of possibilities for businesses, designers and engineers, the potential of which is far from exhausted. And now imagine that all this could also be possible with metals. What ideas could be realised… We really don’t want to miss that and this is why we created One Click Metal.
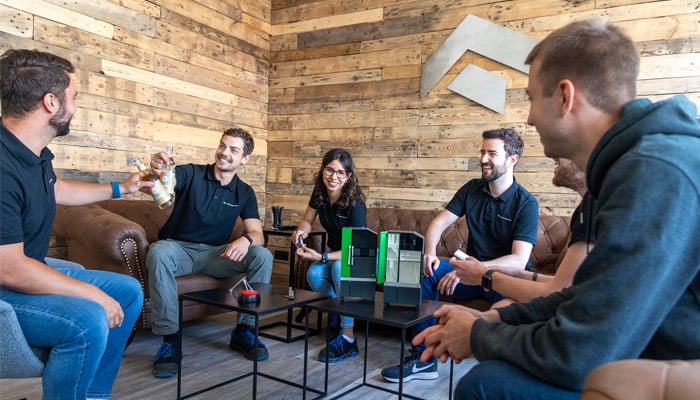
The One Click Metal team
3DN : How did the idea of creating One Click Metal come up?
Through our previous work, we have often seen that metal 3D printing technologies are potentially interesting for many companies, but that most AM systems are very expensive and complex. Especially newcomers or SMEs then say: I lack the knowledge in the application, I cannot make such a large investment for a technology that is unknown to me and my employees. And that is completely understandable. So, we said to ourselves, that should be easier. We want to bring a metal 3D printing system onto the market that makes it easier to overcome these initial hurdles. That means, above all, improving accessibility to these technologies and thus lowering the barriers. This is how One Click Metal was born. Making. technologies available with one click.
3DN : Can you tell us more about your technology and products? How are they different from your competitors?
The process we use is not invented by us. The laser powder bed fusion process has been known since the 1990s. Compared to other technologies, it has the greatest industrial and technical maturity and therefore also has the largest market share. We use this process because it achieves high densities, high productivity, and high resolution in terms of layer thickness and dimensional accuracy. For our product solutions, this means that we can take advantage of this technology and at the same time, with our customer-centric approach, lower the biggest entry barriers into metal 3D printing: lack of knowledge and applications, very expensive and complex systems, and no clean and simple powder handling, all of which severely limit accessibility to AM technologies for a wide range of companies. Our solutions to this are the powder and cartridge system for uncomplicated powder handling, the co-thinking-philosophy and the step-by-step HMI instructions that guide the user through the preparation and printing process, and of course our relatively low system price. In product development, our strongest focus is on the customer: What problems do they currently have in implementing and successfully using metal 3D printing? What are the pain points? How can we solve these problems for him with our products? And these pain relievers are developed and integrated into our products. We think this point is often still not given enough importance in the industry: that in the end, what matters is what the customer needs and what brings him added value. And not that the machine has many features that the customer doesn’t need or can’t use, but which make a machine expensive.
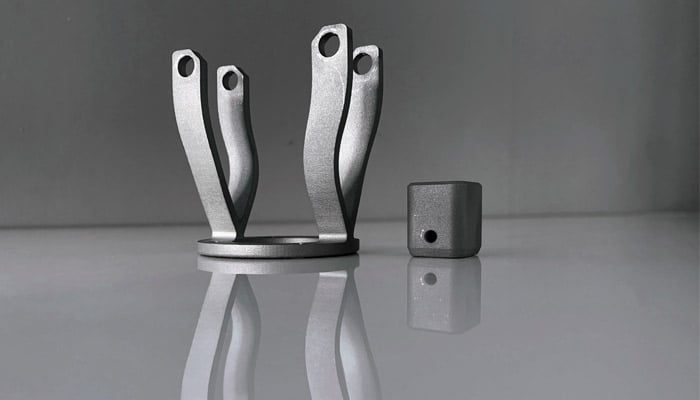
Example of parts printed in 3D on the MPRINT + solution (photo credits: One Click Metal)
3DN : Who are you targeting with this affordable 3D printing system?
Our system is of course suitable for all groups of people and companies, regardless of size, industry, or previous experience with additive manufacturing. We have found that our system is particularly attractive for beginners who want to start with prototyping or their first miniseries due to its very simple and uncomplicated operation and the powder cartridge system: no specially trained personnel are required, as the user is only exposed to minimal direct powder contact. Educational institutions or training departments thus also benefit from our system. Due to our low system price, we are also very interesting especially for SMEs, for whom most AM systems on the market have so far simply been too expensive and too complex.
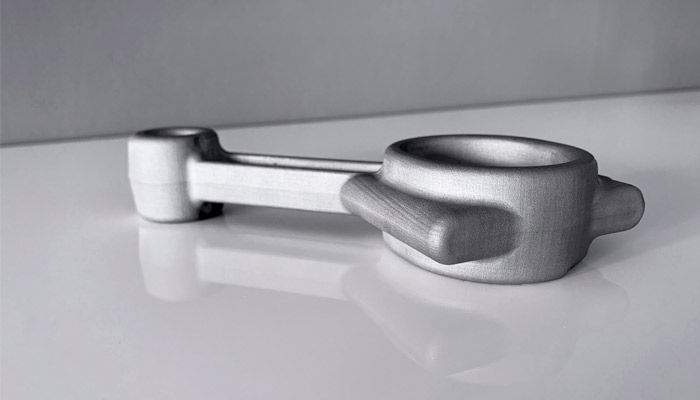
Photo credits: One Click Metal
3DN: What are your future projects?
In the future, we will focus more on entering new industries and adapting our product solutions to the requirements without losing sight of our development guideline. We will also continue to align our products and features with customer needs and constantly optimise them to get closer to our vision: Making technology understandable for everyone and available with one click.
3DN: In your opinion, what is the future of metal AM compared to other AM technologies?
Metal AM has been strongly pushed in recent years by the aerospace, energy and automotive industries and dominated by machine manufacturers who have been doing classical mechanical engineering. Similar to what we are seeing with AM plastics processes, the metal AM sector will continue to change and reach a larger and broader audience. Complex machines will become devices whose application is much simpler, more digital, and more connected. The entry barrier in the metal AM sector currently tends to be higher for young, innovative companies. As SMEs enter AM technologies through low-cost and uncomplicated solutions, this entry barrier will continue to fall for all, enabling a much wider use of metal AM technologies than we are currently familiar with.
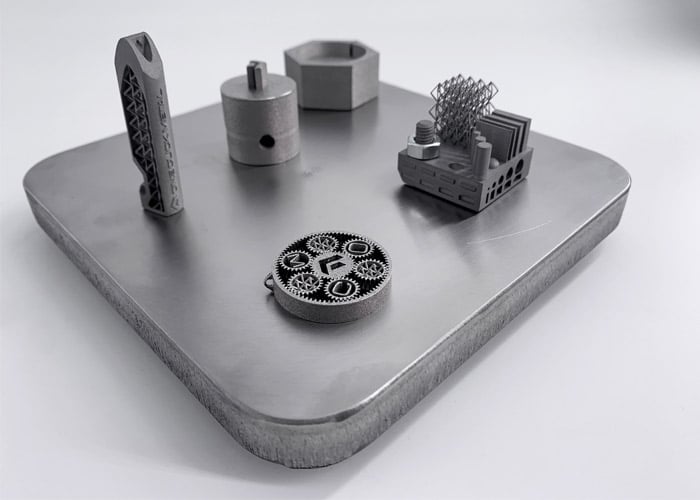
Photo credits: One Click Metal
3DN: Any last words for our readers?
Go to our website, we provide a lot of information about metal 3D printing, including topics like powder disposal or heat management that are often left out but are hugely important. Have a look around and if you have any questions or comments, please contact us.
What do you think of One Click Metal? Let us know in a comment below or on our Facebook, Twitter and LinkedIn pages! Sign up for our free weekly Newsletter here, the latest 3D printing news straight to your inbox!
How does this process get past the prototype fence in the manufacturing sector? How do you cost an item relative to volume? It seems great for one or two items. Is multi cavity an option? How do you overcome heat transfer in thicker sections? Very interesting. Who manufactures the basic raw material in a given color and how do you know what polymer to use. Is there enough history and hands on experience to maximize this process when mated with a given material.
Thank you,
William Foushee