3D startup of the month: MarkForged, making waves in additive metal manufacturing
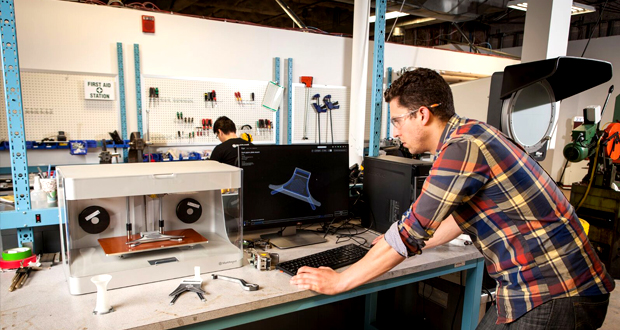
Each month we present the 3D startup of the month, choosing startups that are revolutionizing the 3D printing industry in their own way. For this month’s startup of the month, we met with MarkForged’s CEO Greg Mark to learn more about their newest 3D metal printer. After introducing us to a 3D printer that is capable of producing parts from carbon, MarkForged has now launched the Metal X, a machine that is helping change the industry on additive metal manufacturing, at a price below market standards.
3DN : Can you introduce us to MarkForged and explain to us how MarkForged began?
At MarkForged, we have designed the first and only 3D printer today that integrates both fiber and plastic together into a product that can be printed; giving a final composite part that is made of solid metal. What makes our 3D printer so unique is its patented Continuous Fiber Filament (CFF) technology that works with the MarkForged Eiger software. It automatically creates a fiberglass model (i.e. carbon, fiber, nylon, glass, Kevlar..) to guarantee an optimal solidity of the final piece. This allows you to print solid tools and custom made parts that have a complex design, which would be very difficult to manufacture otherwise.
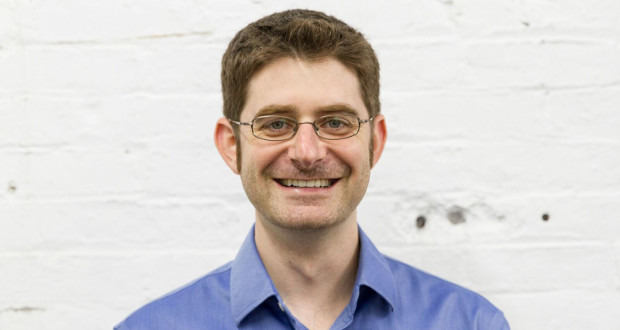
Greg Mark, CEO of MarkForge
Before founding MarkForged, I was an aerospace engineer who specialized in racing technologies. I was therefore able to work very closely with the prototyping, the parts creation process, and especially on the components that are take time to fabricate.
I created MarkForged with the desire to encourage other engineers to print solid, high quality 3D parts using 3D technologies. This would thus enable them to go directly from design to the desired result. Before the creation of MarkForged, 3D printing technologies were mainly made for prototyping, modeling and toys. Our mission has always been to revolutionize manufacturing: we replace long and expensive machining and manual manufacturing by 3D printing the solid parts.
3DN : Why move from carbon to metal?
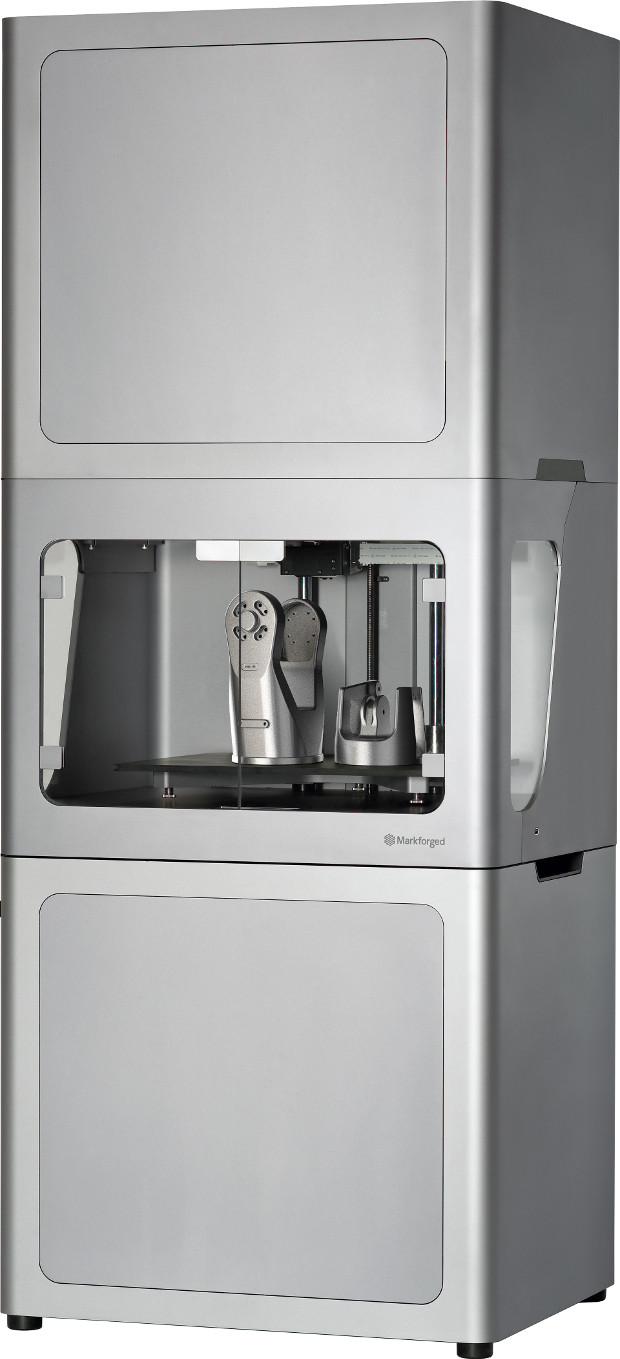
The Metal X by MarkForge
Carbon fiber is the lightest and strongest material that can create a variety of complex geometry pieces. But, if you need high temperatures, for example an engine component or wear parts, then you will need a metal.
The Metal X is the first 3D metal printer that is priced reasonably, in comparison to other CNC machines. At $99,500 USD (about £79,400), it is 1/5 or even 1/10 of the price of traditional metal printers. The Metal X is the first high-grade stainless steel (at 17-4 and 303) with tool steel and other metals currently being developed.
3DN : How is the technology that was developed for the Metal X new?
Metal X is the first 3D printer to operate with a technology called Atomic Diffusion Additive Manufacturing (ADAM). The ADAM process uses the same metal powders that are seen in 3D laser sintered metal printers; the only change is that they are embedded in plastic. This plastic eliminates the toxicity and flammability that is inherent in these powders. The material is then printed layer by layer, followed by a sintering process to obtain the final part. By sintering the entire piece at one time, the layers are more solid, which is not the case with other 3D printing processes.
3DN : What sector(s) are you focusing on? Who are your customers?
We have clients in a variety of industries such as aerospace, automotive, industrial, commercial machinery, medicine, dentistry, sports, as well as in oil and gas industries. Our printers are used today to manufacture tools and equipment in mechanical workshops and on production lines. Our customers also make a lot of prototypes, and some of them manufacture parts for mass production.
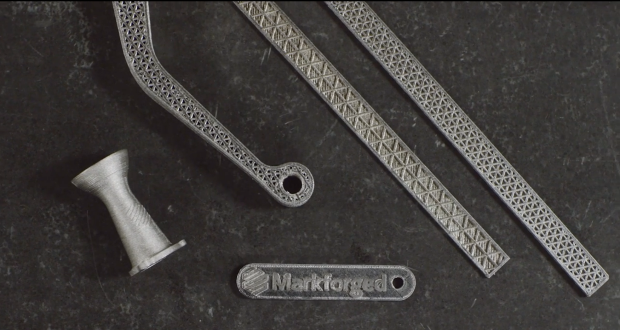
Examples of metal pieces printed by MarkForge
3DN : In the years to come, what do you envision for the future of additive metal fabrication?
I see metal additive manufacturing becoming more accessible, with a price level that will be lower than before. As a result, this will cause an upset in production, inventory management practices, and the speed of product development, all in a very positive way.
Whether you are a big manufacturer or a small retailer, the fact that you will now be able to print real molds in one night instead of in weeks or months at an even more attractive price will be nothing by positive when it comes to the development of your products. Being able to print metal spare parts overnight has considerable economic benefits. In addition, smaller series of metal parts can be printed, machined or made with complex tools. This brings us back to greater profitability and better competitiveness for our customers.
Watch the video below for an introduction to the Metal X:
3DN : Anything you would like to add for our readers?
3D printing has made significant progress over the past four years. The machines are now easier to use and are powerful. When you buy your first printer, you will make a few parts. Once you get in the habit of integrating 3D printing into your design process, you’ll see that more and more parts are being made to be printed in 3D. It’s nice to be able to produce a piece that same day as its design.
For more information on MarkForged, visit their site here.
Can MarkForged become a leader in the metal additive manufacturing market? Share your opinion in the comments below and don’t forget to add us on Facebook and Twitter!