3D Solar Discusses Using Additive Manufacturing in the Energy Sector
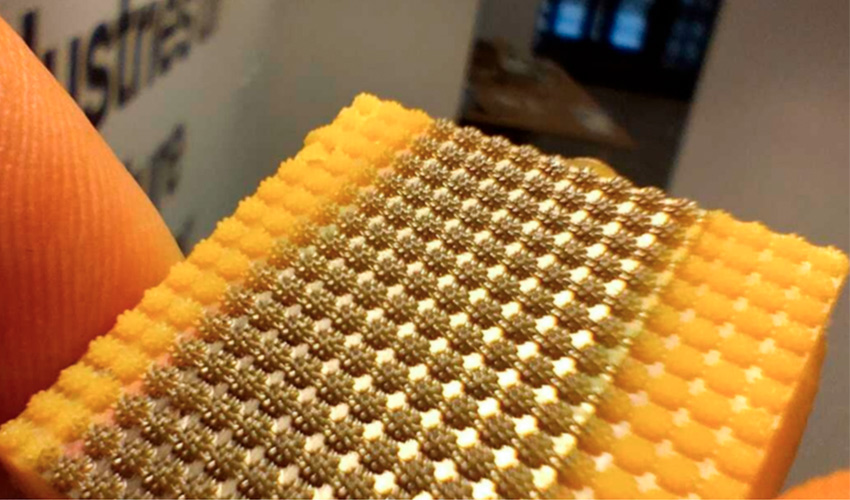
When we talk about the sectors that have implemented additive manufacturing, the list is long. More and more companies are betting on its adoption in the production chain. We have already seen its use in industries such as automotive, consumer goods, aerospace and even oil and gas. One of the sectors that can also benefit from 3D printing is the energy sector. In this context, the U.S. company 3D Solar has developed its own process to take advantage of this technology. We spoke to its team to learn more about its vision for the technology and its application in this field.
3DN: Could you introduce yourself and tell us about your connection with 3D printing?
My name is Daniel Clark, and I’m 41 years old. I was introduced to photopolymers when I was 12 years old through my great-uncle Dennis Gustafson. My first real experience with 3D printing at shows was in 2014 at RAPID + TCT, when Kevin Ayers had me come to Detroit and introduced me to Simon Scott, Graham Tromans and Todd Grimm, where we made a plan to run silicon through a Renishaw Metals 3D printer.
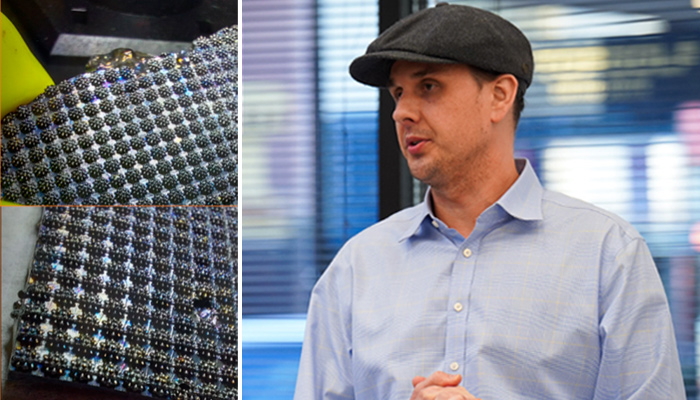
On the right is Daniel Clark of 3D Solar.
3DN: What is 3D Solar? How did the idea of creating the company come about?
The goal of 3D Solar is to revolutionize the solar energy sector with a highly efficient method for harnessing solar power. I crafted a novel three-dimensional solar cell/panel that maximizes energy production within a minimal footprint. Drawing inspiration from biomimicry and sacred geometric shapes, I have engineered an innovative solar cell that captures up to two to three times more power at almost half the cost of conventional silicon-based cells.
My innovation journey began in 2010 with “vertical gardening,” a technique that involves cultivating plants in vertically stacked layers. By integrating vertical 3D hydroponics, I was able to distribute water and the plants evenly, resulting in a 300% increase in plant yield. It was this concept of maximizing utility in a constrained space that led me to wonder about its potential applications in 3D solar energy.
3D Solar is redefining the way we harness solar energy by increasing the surface area of 3D glass micro substrates by 300% compared to a flat substrate through its hybrid 3D printing IP. We have chemically modified the Tethon Genesis Development high-loading resin for casting and molding. Thus, we can make eco-friendly parts every 15-30 seconds with this material. 3D Solar has a cutting-edge vision with an electrochemical manufacturing approach in the coating of 3D solar micro solar cells for solar energy harvesting.
3DN: What additive manufacturing technologies and materials do you work with?
Tethon 3D provides the base resin, which we then chemically modify using two formulations. One is designed for volumetric printing, casting and molding of metals, semiconductors and ceramics. It uses a special photo initiator that operates with infrared light. This resin overcomes Beer-Lambert’s law, enabling printing at depths of up to 2-3 inches inside the volume of the resin, even within dark, metal and metal oxide-filled resin.
The second Tethon custom resin formulation is for volumetric printing, casting and molding of glass in large volumes without cracking or overheating. There is a third ingredient we are using to inhibit light in our dual-color continuous volumetric 3D printer, which we are developing with the help of Marijn van Antwerpen, whose uncle is the brains behind Admatech.
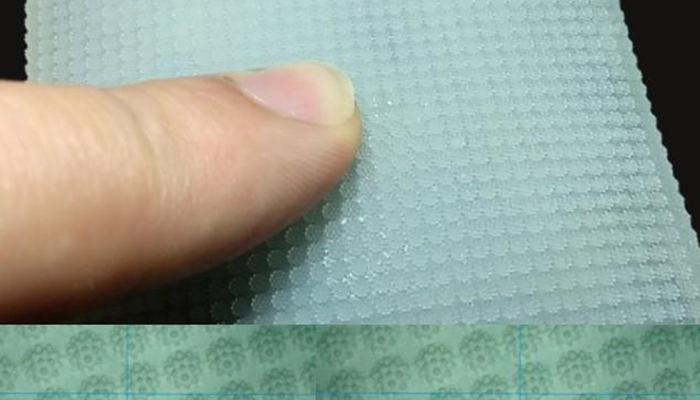
Piece developed with the company’s technology (Photo Credits: 3D Solar)
3DN: What are the limitations of using 3D printing in this sector?
Solar, micro-optics, and the semiconductor industries need very smooth glass substrates without layer lines. So, you are limited to photo-polymer printers like those from Nanoscribe, Boston Micro Fabrication, Axtra 3D and niche LCD printers.
3DN: How do you see the future of 3D printing in this industry in 10 years?
Most of the low-volume printing players will disappear, and a new era of high-volume manufacturers will emerge. I’m talking about printers like Mold Jet but for high-volume production, where our hybrid casting/molding is combined with a 3D printer in one machine, achieving faster production than injection molding.
3DN: Any last words for our readers?
Shapeways is an example of not embracing evolution. Our IP could have helped them make that quantum leap I am talking about from low volume to high volume!
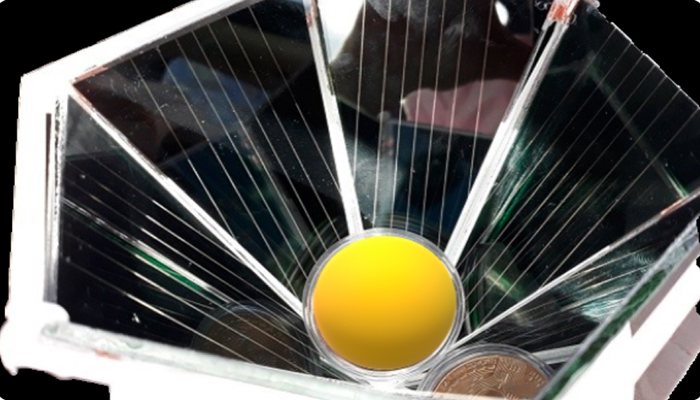
Photo Credits: 3D Solar
What do you think of 3D Solar’s use of additive manufacturing? Let us know in a comment below or on our LinkedIn or Facebook pages! Plus, don’t forget to sign up for our free weekly Newsletter to get the latest 3D printing news straight to your inbox. You can also find all our videos on our YouTube channel.
*Cover Photo Credits: 3D Solar