Using 3D Scanning to Repair and Customize the Famous Ford GT40
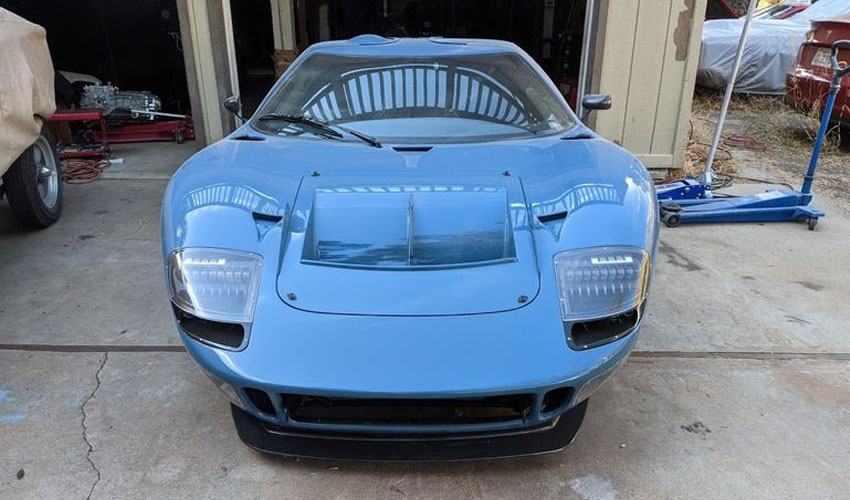
The Ford GT40 is a sports car designed in only 126 examples in the 1960s, with a history well known to car enthusiasts but also amateurs, the rivalry between Henry Ford II and Enzo Ferrari has inspired more than one movie. In any case, the vehicle is the focus of today’s topic: In the United States, vintage car enthusiast Chris Ashton used 3D technology to modify and customize his Ford GT40, using Artec Space Spider and Artec Eva 3D scanners. The collector was able to reproduce complex shapes very quickly, as close to the real thing as possible, and hopes to get back on the road as soon as possible.
3D scanners are often used to digitize objects and parts from the past, allowing users to obtain a digital copy. This copy can then be modified, customized and then 3D printed to become a physical model. This is particularly interesting in the automotive sector for designing spare parts: on vintage cars, most spare parts are no longer produced, complicating maintenance and repair tasks and increasing costs considerably. However, thanks to a 3D scanner, the user can easily digitize his original part and recreate a model first digitally and then physically thanks to additive manufacturing.
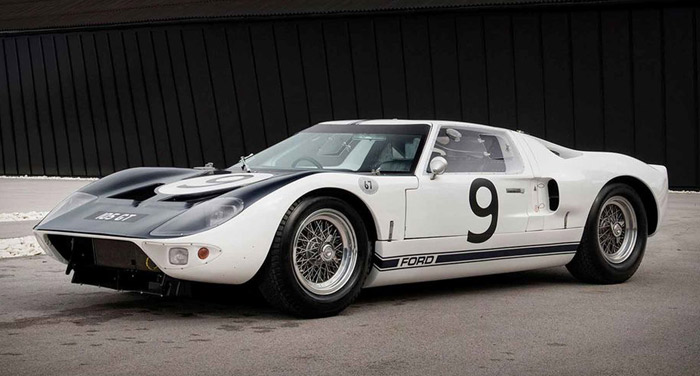
Photo Credits: Ford
Artec’s solutions for customizing the Ford GT40
Chris Ashton has a passion for cars and was able to combine this passion with his business: Ruffian Cars is a California-based company that builds and modifies sports cars. They’ve been using additive manufacturing to reproduce parts for a few years now, but the process required many iterations before getting a model as close to the original as possible. That’s why the company invested in Artec Space Spider and Artec Eva scanners, aiming especially to reproduce the car’s wideners.
Chris Ashton explains, “Previously I would have needed to sculpt the flares out of foam or clay, right on top of the car, and take the whole car to a shop for them to pull the molds (or do it myself, which is messy and involves a lot of chemicals.) And I would have had to do the job twice because you can’t mirror a part in the real world. The big advantage here is that the fender flares were built digitally on a scale scan of the actual car so we know they’ll fit properly, and the left and right sides will be exact mirrors of each other.”
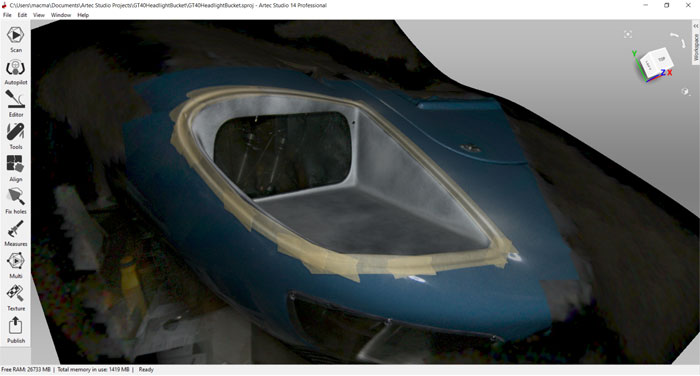
The internal angles and curves of the headlight housing were 3D scanned (photo credits: Artec 3D)
Chris says the Artec Eva scanner was used to scan the entire vehicle, while the Space Spider was used to scan smaller parts and zoom in on the components to be integrated. It is a scanner that is particularly well suited to applications that require fine detail and accuracy, ideal for capturing the reality of small objects. The company can then retrieve all the data from the vehicle on 3D software, see in real time the nesting of parts, etc. Chris continues: “Since the scans come into the computer at real-world scale, I can model my new parts around them and print them without any scale issues, which is a huge improvement over what I was doing before, which was taking measurements, building on those, and hoping they were correct.” This makes the 3D printing process easier and more accurate.
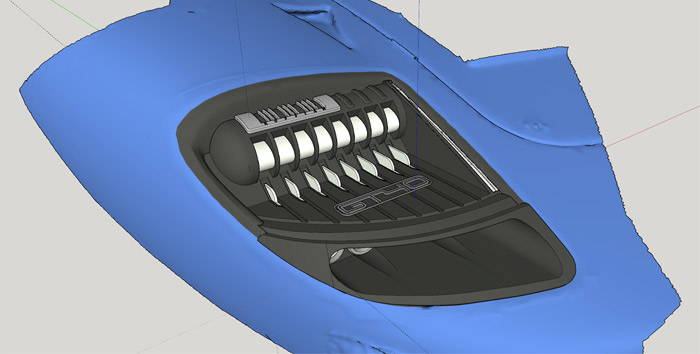
The assembled headlight model (photo credits: Artec 3D)
Chris Ashton’s work doesn’t stop at reproducing the Ford GT40’s wideners: the customization work goes as far as the seatbelt buckles, but also on the fenders and side skirts. In November, he will present his Ford GT40 at SEMA 2021, a trade show where car manufacturers exhibit their products. More information on Artec 3D scanners can be found HERE.
*Thumbnail Photo Credits: Artec 3D
What do you think about the use of scanning solutions to repair classic cars?Let us know in a comment below or on our Facebook and Twitter pages. Don’t forget to sign up for our free weekly newsletter, with all the latest news in 3D printing delivered straight to your inbox!