The Top 3D Printing Applications in Water Sports
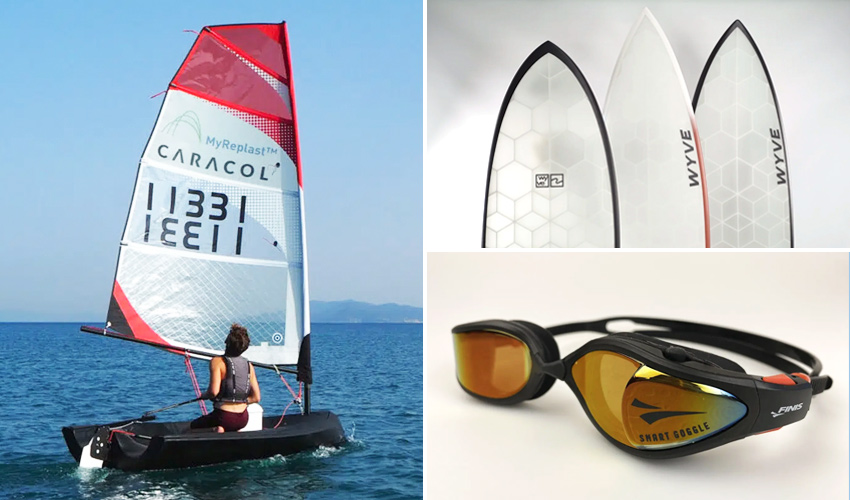
Summer has been here for a few weeks now, and it seems that everyone is leaving on vacation as we all have our minds set on sea, sandy beaches and well-deserved rest. What’s more, the 2024 Olympic Games are about to get underway, heralding some intense sporting days ahead. It’s for these two reasons that today we bring you this article dedicated to the use of 3D printing in water sports. Whether it’s surfing, windsurfing, swimming or kayaking, 3D technologies offer considerable advantages in the sector: reduced manufacturing time, customization of accessories, improved performance, etc. It also helps reduce the environmental impact of these sports, a particularly important point these days. We’d like to take a look back at a few projects that combine 3D printing and water sports – although of course this list is by no means exhaustive. Have a great summer!
Innovating One of the Most Popular Water Sports With 3D Printing: Surfing
WYVE
Founded in 2019 by two engineer, surfer friends, WYVE is a French start-up that relies on additive manufacturing to design surfboards. It uses material extrusion to produce the core of surfboards. The core incorporates a lattice structure to enable the mechanical parameters to be changed from one board to another. Depending on the level of surfing and use of the board, WYVE will play with the thickness and density of the print to produce a tailor-made product, whether in terms of vibration, weight, torsion and so on. This is where additive manufacturing truly shows its value. Today, the French company offers several board models that it can deliver to around ten countries.
YUYO
YUYO, an innovative company based in the south of France, has developed what it claims to be the first sustainable 3D-printed surfboards. They seek to solve the surfer’s paradox by offering boards that respect the environment and the oceans. Leveraging large-format 3D printing and advances in bio-composite materials, YUYO manufactures boards from natural or recycled materials. Their 3D printing filament is made entirely from plastic waste. YUYO also uses natural basalt fiber and a linseed oil-based biosourced resin. Additive manufacturing makes it possible to create customized boards on demand, in a responsible manner, thus contributing to the preservation of aquatic ecosystems.
Paradoxal Surfboards and its Algae-Based Surfboards
Paradoxal Surfboards is another innovative French company that designs, manufactures and markets 3D-printed surfboards using ocean waste as an alternative to traditional petroleum-based materials. Paradoxal Surfboards is dedicated to eco-design and the use of new bio-sourced materials to reduce environmental impact. The company specializes in three key areas: materials sourcing, the design and development of 3D-printed surfboards, and the creation of water sports equipment from marine waste. Thanks to 3D printing, Paradoxal Surfboards offers unique, translucent surfboards with a honeycomb structure.
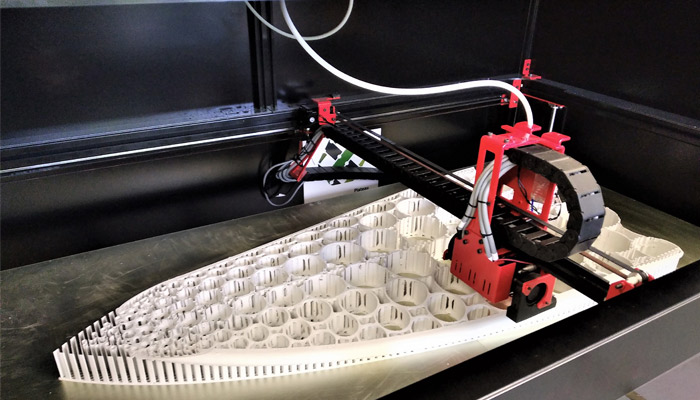
Paradoxal Surfboards rely on green algae waste.
3D Printed Surfboard Fins
At the University of Wollongong in Australia, a multidisciplinary team is working to improve the surfing experience for athletes. With the Surf Flex Lab project, a team of surfers and engineers bring together their expertise in both fields to develop technology for the water sport. The project employs rigorous scientific methods and uses advanced technology to improve surfing equipment. The main focus of their research is on optimizing the design of fins and boards. An example of their work is the 3D printed fins they developed as an alternative to the costly injection molding manufacturing process. For their design, they were inspired by the fins of humpback whales. This design demonstrated more performance and could be adapted to the individual needs of the surfer as well as the swell. If you are also passionate about surfing and the science behind it, the team’s latest scientific publications is freely accessible.
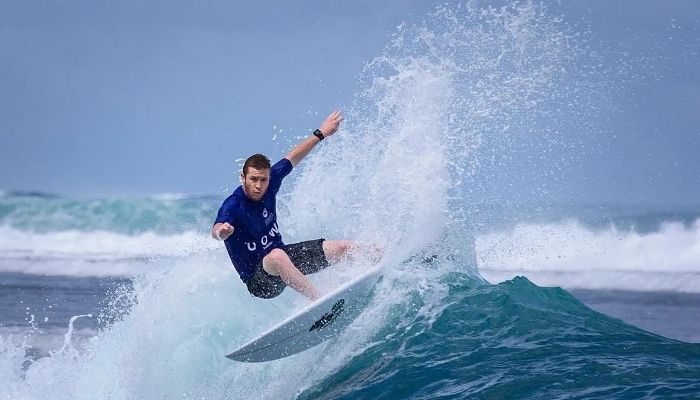
Photo Credits: Surf Flex Lab
Blueprint Surf
Given the many ecological issues currently facing the ocean, it should come as no surprise that those that love it are trying to protect it, including surfers as should be clear from this list. For an example from the US, take the founders of Portland, Maine-based Blueprint Surf who are turning to 3D printing to make more eco-friendly boards that they can use guilt free. The company uses large-scale polymer manufacturing and PETG to create a 3D printed frame that then is wrapped in soft composite skin make it suitable for surfing. The company hopes to makes the industry greener by prevening the export of large amounts of surfboard foam from Southeast Asia and rather moving to have 3D printers in each surf area to allow customers to get their boards locally.
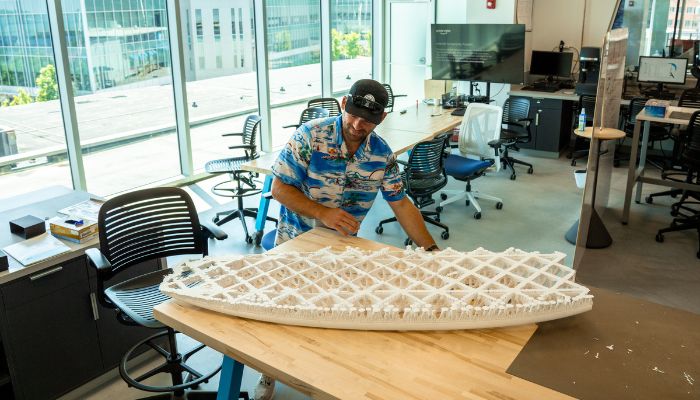
The 3D printed frame of the surfboard and co-founder Luke Diehl (photo credits: Blueprint Surf)
Swellcycle’s Sustainable Surfboards
Based in Santa Cruz, California, Swellcycle is a company that specializes in producing sustainable surfboards using 3D printing and recycled materials. Their mission is to provide surfers with high-performance boards while reducing pollution. To do this, Swellcycle uses recycled plastics, such as PETG from hospital equipment, remnants of old surfboards, end-of-life or unrepairable products, and bio-based resins. From the collected materials, filaments used in the FDM 3D printing of Swellcycle surfboards are then created. A perfect example of environmental friendliness and circular economy.
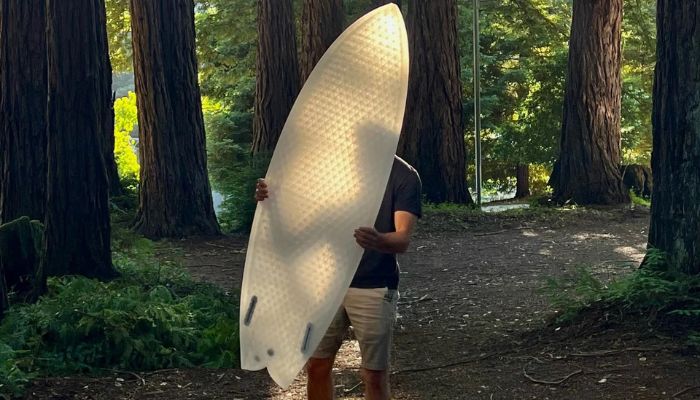
Photo Credits: Swellcycle
Kayaks, Paddleboards, and Jet Skis
A Kayak Created by 3D Printing and Machining
The so-called Värmdö is a 3D printed kayak that is part of a project led by RISE Research Institutes of Sweden, in collaboration with ADAXIS. The goal of this initiative was to combine machining with large-format additive manufacturing to create a life-size kayak from recycled materials. To carry out the project, ADAXIS AdaOne software was used to generate tool paths for both 3D printing and subsequent machining. In addition, the research team used a high-performance pellet extruder attached to the end of an ABB IRB6700 robotic arm to create the final kayak design. Finally, they turned to machining to open all the hatches, drill holes and mill the bottom of the hull. This interesting project opened up many fields of study, especially in the field of water sports, such as the use of recycled materials or 3D printing on non-flat surfaces.
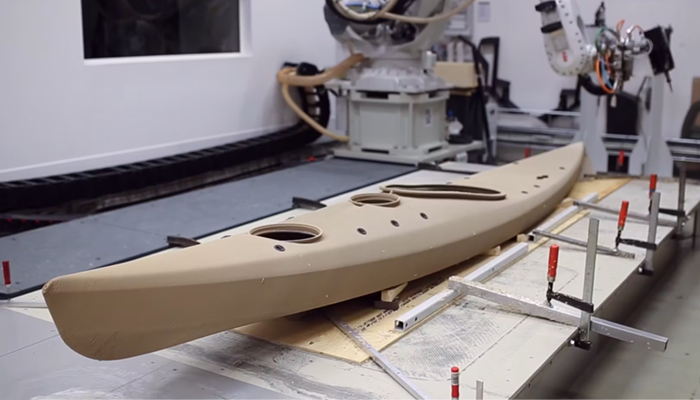
Photo Credits: Adaxis
3D Printed Water Scooter
Offering an adventure both above and below water, AMAZEA scooters by the German company JAMADE were designed using a BigRep large-format 3D printer. Pro HT, a material developed by BigRep, was used to make the scooters due to the material’s temperature resistance and low shrinkage features. With 75% of the scooter made using additive manufacturing, AMAZEA is perfectly waterproof — manufacturing the scooter in one shot gave the company freedom from the restrictive nature of assembly that also comes with the risk of leakage.
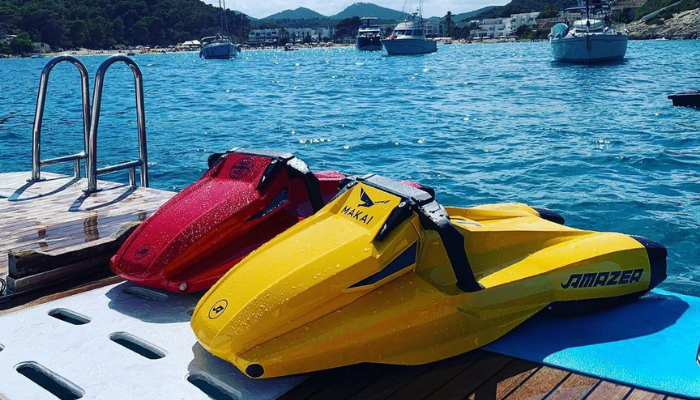
Water scooter manufactured as one part on a large-format 3D printer. (Photo Credit: AMAZEA)
A 3D Printed Sailboat
In collaboration with NextChem, Caracol has produced a sail boat using 3D printing. The special thing about the Beluga sailboat is that it could be produced in just 40 hours in one go. The Caracol robot system and its proprietary LFAM technology were used for this. The algorithms developed by Caracol make it possible to align the extrusion head of the robot system at different angles, allowing overhangs, hollow and geometrically complex designs to be printed. The material used was polypropylene with 30% glass fiber. This made it possible to produce a very lightweight sailboat that is also environmentally friendly, as the MyReplastTM material used is recycled. With its 3D-printed sailboat, Caracol is also actively supporting the circular economy.
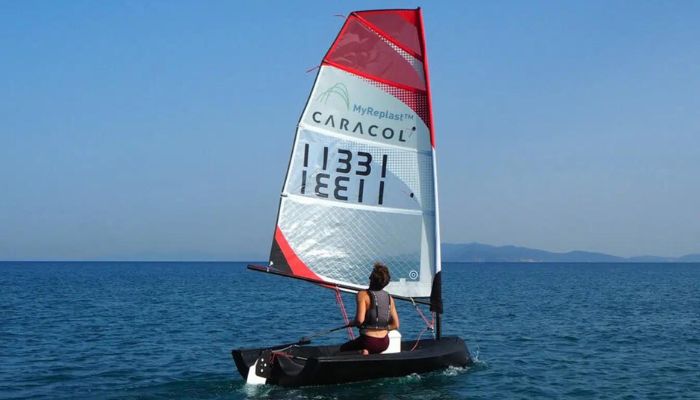
Photo Credits: Caracol
Creaform Supports the American Magic Team
The New York Yacht Club’s American Magic team is competing in the 36th America’s Cup this year and is working with Creaform, a leader in 3D metrology, to improve their boat. Throughout the project, the team will be equipped with state-of-the-art metrology technology, including metrology-grade 3D scanners, optical coordinate systems for photogrammetry, scan-to-CAD and inspection software. These technologies will accelerate the development of key components for the foiling monohull yachts. The ability to scan surfaces with Creaform scanners saved the boat builders many hours of work, which in turn enabled adjustments to other parts of the boat and had a positive impact on boat speed. In general, the technology allows shapes designed by humans to be transferred to the computer, modified and passed on to other tools. The team and the boat were thus optimally prepared for the competition and can increase their chances of winning the America’s Cup.
FINIS 3D Prints Diving Goggle Prototypes
FINIS, Inc. is a California-based company that develops advanced products for swimmers, including with additive manufacturing. The team started with FDM 3D printing and soon realized that more isotropic parts were needed, which is why they then turned to SLA printing. Here they use the Form 3+ printer from Formlabs, which is particularly impressive due to its wide range of available materials. Silicone 40A resin was used for printing, a 100% silicone resin that can produce flexible and soft parts that can be printed within a day and are also durable. A major advantage for the company is the ability to directly implement new ideas for parts. Designs can be quickly changed, printed and then tested in the pool. By using the resin, the prototypes improved significantly and the 3D-printed goggles were also convincing in the pool tests, as they are soft and seal well at the same time. The team integrated 3D printing into their development cycle to improve designs and carry out tests, which helps to produce better products.
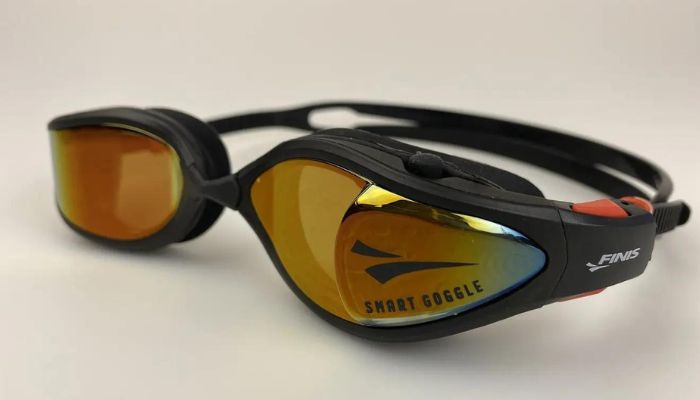
Photo Credits: FINIS
The ‘Made in Spain’ Electric Propeller
The company Pantur has collaborated with the startup Electric Sea (eSea) in the development of a portable electric propeller adaptable to various boats and aquatic equipment. It can be easily integrated into surfboards, paddle surfboards and kayaks. This innovative product stands out for its lightness, autonomy and ease of use, providing technical assistance and safety in adverse conditions at sea. A crucial aspect of the project has been the use of 3D printing to design and manufacture the motor housing for use in water sports. This process has enabled the rapid creation of prototypes and molds, reducing costs and production times. In addition, the quality, strength and lightness that the product needs in sea conditions has been guaranteed. 3D printing as a manufacturing process has proven to be a valuable tool in the optimization of the propeller, positioning it as an ideal option for both sportsmen and rescue teams.
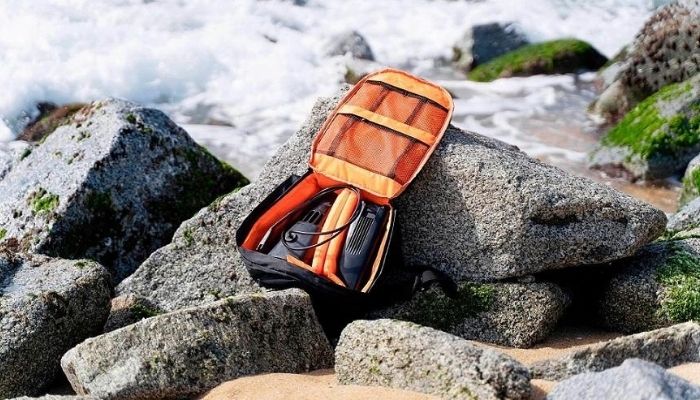
Photo Credits: Interempresas
What do you think of these 3D printing applications in watersports? Let us know in a comment below or on our Facebook and Twitter pages. Don’t forget to sign up for our free weekly newsletter, with all the latest news in 3D printing delivered straight to your inbox!