MIT 3D printing system reproduces realistic variations in glossiness
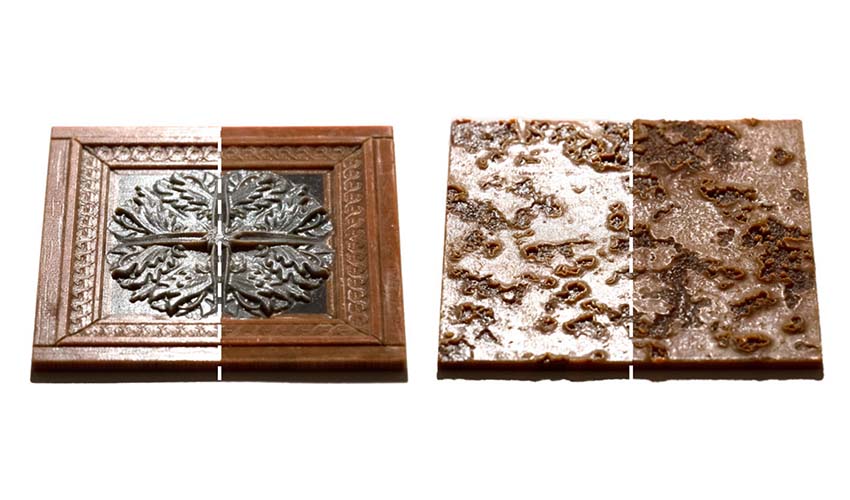
Recently, MIT researchers developed a 3D printing system able of giving an object more salient features by reproducing its glossiness. Gloss remains a challenge to 3D print because hardware isn’t designed to deal with the different viscosities of the varnishes that lend surfaces a glossy or matte look. Therefore, researcher Michael Foshey and his colleagues have been working on a solution which could enable realistic variations in glossiness across a 3D printed surface. The advance could aid fine art reproduction and the design of prosthetics.
Indeed, this technology could be used to faithfully reproduce fine art, allowing near-flawless replicas to be distributed to museums that don’t have access to originals. It might also help create more realistic-looking prosthetics. Michael Foshey adds that the advance represents a step toward visually perfect 3D printing, “where you could almost not tell the difference between the object and the reproduction.”
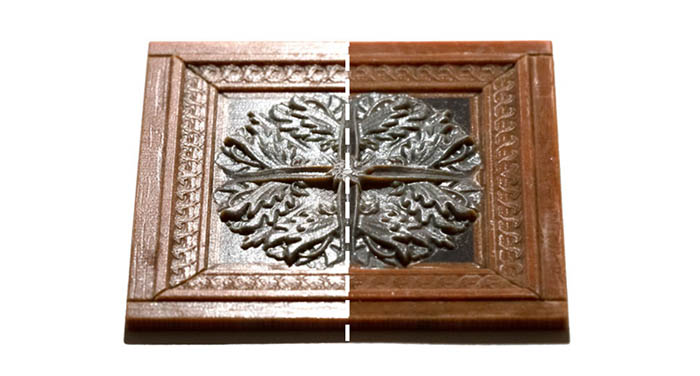
To the right, the part was 3D printed using MIT’s system to reproduce glossy and matte finishes | Image via MIT News
Reproducing variations in glossiness
As a matter of fact, glossiness is simply a measure of how much light is reflected from a surface. Varnishes that lend a glossy finish tend to be less viscous and to dry into a smooth surface. Varnishes that lend a matte finish are more viscous. Usual 3D printing hardware is not made to reproduce this varying reflectivity. The more viscous varnish (for the matte effect) contains large polymers that, when dried, protrude randomly from the surface and absorb light. Those polymers pose a dilemma for 3D printers, whose skinny fluid channels and nozzles aren’t built for this texture. “They’re very small, and they can get clogged easily,” explains Michael Foshey.
Therefore, the researchers developed a printer with large nozzles and the ability to deposit varnish droplets of varying sizes, given that size also affects precision. The varnish is stored in the printer’s pressurized reservoir, and a needle valve opens and closes to release varnish droplets onto the printing surface. A variety of droplet sizes is achieved by controlling factors like the reservoir pressure and the speed of the needle valve’s movements. The more varnish released, the larger the droplet deposited. The same goes for the speed of the droplet’s release. “The faster it goes, the more it spreads out once it impacts the surfac. So we essentially vary all these parameters to get the droplet size we want.”
The researchers tested the technology on a variety of objects, mostly flat printouts with textures that varied by half a centimeter in height. Michael Foshey is happy with them: “They definitely have more of a feel of what you’re actually trying to reproduce.” You can find more information HERE.
What do you think of this new system developed by MIT? Let us know in a comment below or on our Facebook and Twitter pages! Sign up for our free weekly Newsletter, all the latest news in 3D printing straight to your inbox!