3D Printing To Lead Prototype Development for McLaren F1 Racing
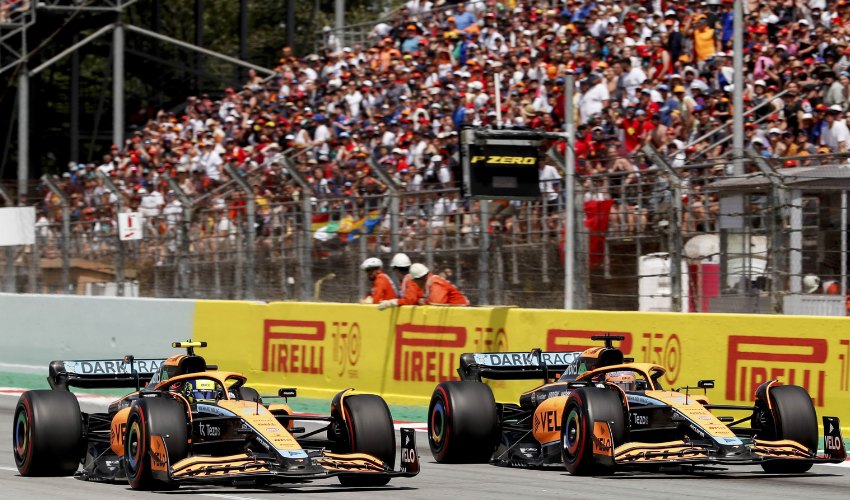
Shifting further towards sustainable engineering and manufacturing, McLaren Racing, F1’s first carbon-neutral team, has fully embraced 3D printing as the cornerstone of its prototype development process. The company reports that it is 3D printing more prototypes than engineering them, surpassing conventional engineering methods. This strategic transition has further highlighted McLaren’s commitment to driving innovation and reducing its environmental footprint within the competitive landscape of Formula 1 racing.
McLaren’s commitment to innovation and sustainability is evident in its dedicated 3D printing lab, a unique space at its Southwest London headquarters. This buzzing hub houses over 20 Stratasys printers, capable of producing more than 9,000 parts annually. These components range from intricate wind tunnel models to critical aerodynamic elements like front and rear wings, side bodywork, and upper body components. Led by McLaren’s Chief Operating Officer Piers Thynne, this approach heralds a new era of sustainable rapid prototyping, where each part is crafted with precision, yet with minimal waste.
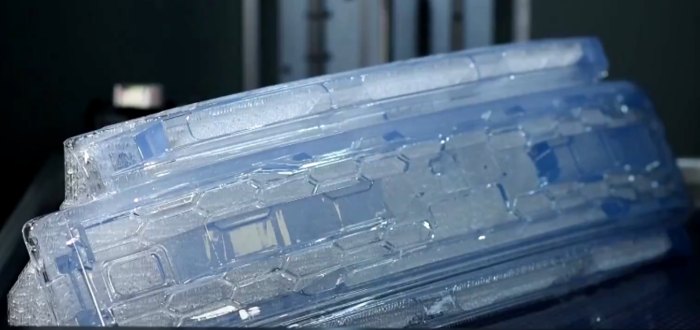
A 3D printed McLaren F1 prototype part.
The sheer complexity of designing and manufacturing an F1 car’s front wing assembly demands thousands of parts, many of which are single-use. McLaren’s strategic partnership with leading 3D printing firm Stratasys, renowned for its expertise in additive manufacturing, has empowered the team to harness a diverse range of filaments, including cutting-edge carbon fiber and recycled materials. This not only enhances performance but also aligns seamlessly with McLaren’s vision for a greener future.
Yann Regeul, Senior Vice President at Stratasys, echoed the sentiment, emphasizing the industry’s shift towards recycled filament and reduced waste. “The ability to print 100% recycled filament with our new OpenAM software is really a change for the industry, enabling McLaren to significantly reduce their waste—a top preoccupation for most customers today,” Regeul explained.
By leveraging 3D printing technology, McLaren has streamlined production processes, significantly reducing long delivery times and environmental impact. This not only applies to automotive parts but extends to fixtures, jigs, and small molds, which previously required lengthy, laborious production from metal blocks.
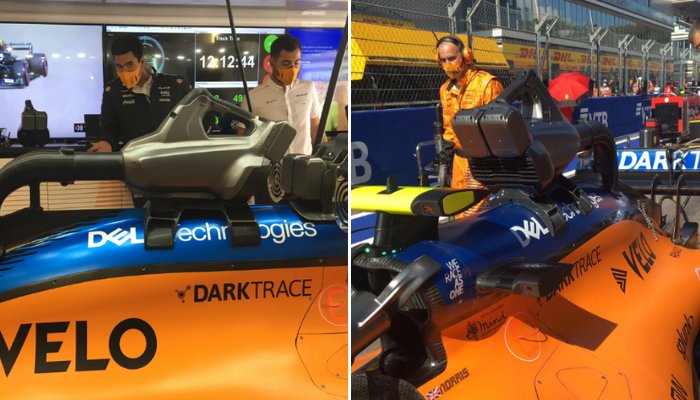
A 3D printed engine cooling duct fitted on a McLaren F1 racecar.
Speaking on these benefits, Jeremy Hart, a veteran F1 commentator, stated, “Formula 1 is the most advanced sport on the planet, and therefore it’s great to find ways to cut down waste and to be more efficient in terms of how it produces its cars.” Amid Formula 1’s trajectory toward achieving net-zero emissions by 2030, with mandatory sustainability enhancements for all cars by 2026, McLaren’s heightened integration of 3D printing cements its role as a leader in advancing eco-friendly racing practices.
What do you think of McLaren’s switch to 3D printing for prototyping? Let us know in a comment below or on our LinkedIn, Facebook, and Twitter pages! Don’t forget to sign up for our free weekly newsletter here for the latest 3D printing news straight to your inbox! You can also find all our videos on our YouTube channel.
*All Photo Credits: Stratasys