Employing 3D printing for the restoration of a church
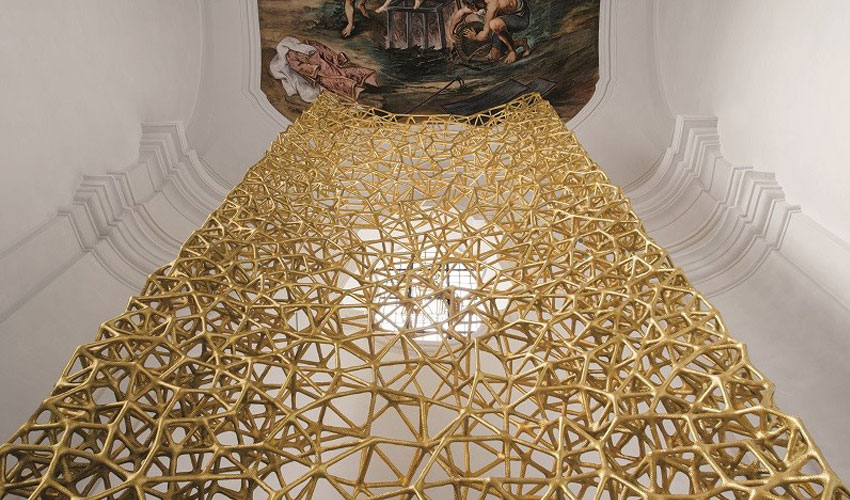
Additive manufacturing is everywhere, even where you don’t really expect it. In Germany, if you walk around Altmühldorf in Bavaria, you will have the opportunity to see a 3D printed altarpiece in the village church. Designed by Oliver Tessin and the artists Corbinian Böhm and Michael Gruberen, in partnership with the German 3D printing service FIT AG, the golden structure is 8 metres high, 2.5 metres wide, and is a fine example of topological optimization. It is reminiscent of a honeycomb where all the branches are meticulously interlocked.
The entire 3D modeling phase that precedes the printing stage allows the user to play with the shapes, material and to check whether the design is optimized for additive manufacturing. Often, the 3D model is designed with as little material as possible to avoid increasing costs and post-processing steps. Topological optimization removes material where it is not needed: the final weight of the part is therefore reduced, as is its cost. This is a key advantage in the design of a part such as an altarpiece. Yet additive manufacturing is not a production method that comes to mind when it comes to restoring a church. In fact, the teams behind the project had to prove to the city that 3D printing technologies were a viable method.
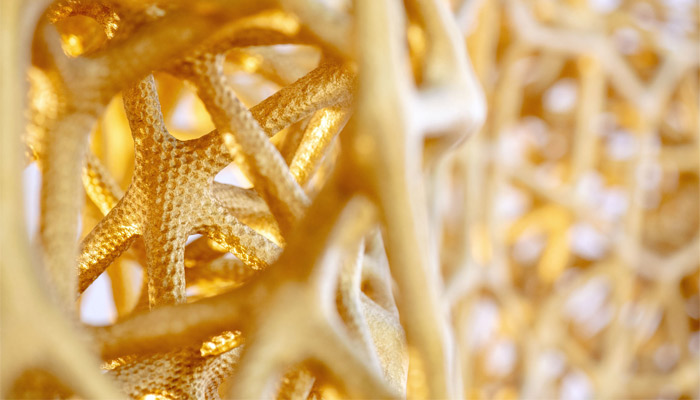
The structure of the altarpiece resembles honeycomb
The manufacturing process of the 3D printed altarpiece
Originally, the architects in charge of the project wanted to use WAAM technology, attracted by its unique appearance, properties and above all the possibility of using metal. However, when they approached FIT AG’s 3D printing department, they realised that other processes and materials could be more attractive in terms of cost, geometric restrictions and durability of the parts. SLS proved to be the most relevant, offering high mechanical performance, low weight and design freedom.
FIT AG explains that it 3D printed the 60 parts that form the structure on an EOS P770 machine from PA12, each part measuring 680 x 550 x 380 mm. They explain it took 120 machine days, to produce everything. Once printed, they were coated with a bronze-aluminium structural alloy via thermal spraying and a metallic varnish to create the final gloss. This coating was applied to guarantee the durability of the polyamide over time, have a certain resistance to oxidation and to the environment (dust, soot, etc.).
According to the teams, the assembly process was the most complicated stage: the entire structure weighing 350 kilos, it was necessary to imagine an efficient way to assemble the altarpiece on site. 2,000 individual connectors were glued together by hand. The project took a total of 6 months, with the 3D printing part being the fastest. The result is quite impressive! Bruno Knychalla, Project Engineer at FIT AG, concludes: “New technologies and spiritual objects are not so often combined. I think that our wide range of technological knowledge and our interdisciplinary team convinced people that we could do something bold and new that leaves an impression of quality craftsmanship with timeless elegance. I think people were really amazed.” You can find more information HERE.
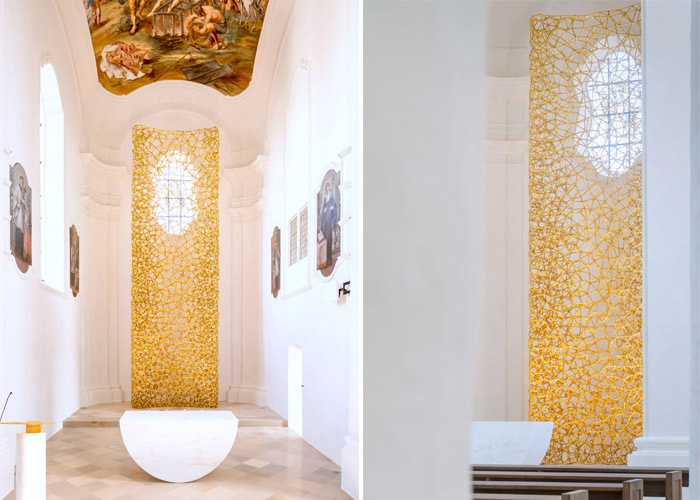
The 3D printed altarpiece | Credits: Studio Ticino
What do you think of this 3D printed altarpiece? Let us know in a comment below or on our Facebook and Twitter pages! Sign up for our free weekly Newsletter, all the latest news in 3D printing straight to your inbox!