Isotropy in 3D Printing: What Is It and How Does It Affect the Final Parts?
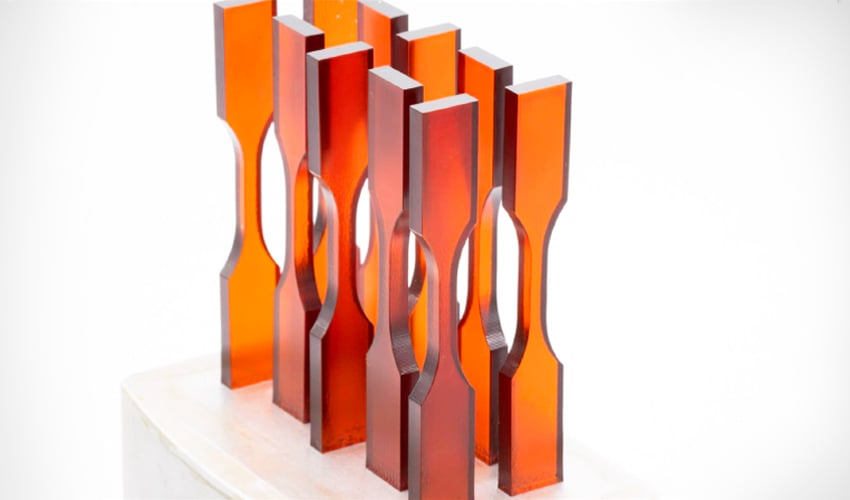
If you are part of the 3D printing industry or at least somewhat familiar with the technology, you will have heard of the concept of isotropy, which is defined as uniformity in all orientations. Thus, if we apply it to additive manufacturing, it refers specifically to uniformity in 3D printed parts. We can interpret this term from many different angles, whether it is the color, surface finish, shape of the model, etc. However, the property that most often interests experts, and to which the concept of isotropy is generally associated, is strength. In other words, an isotropic part is one that has the same strength in all the physical parts that make it up. But why is it so important to understand the meaning of this concept, and how does it affect the final 3D printed parts?
As 3D printing is an increasingly democratized manufacturing method, many companies are implementing it for the creation of final parts. It is therefore essential to understand the different technologies available and the performance of the material to be used. In general, most thermoplastic polymers are considered isotropic. This is mainly due to their nature and the fact that the cohesion between their component polymer chains is uniform in all directions. However, this does not mean that parts made from these materials maintain this quality level.
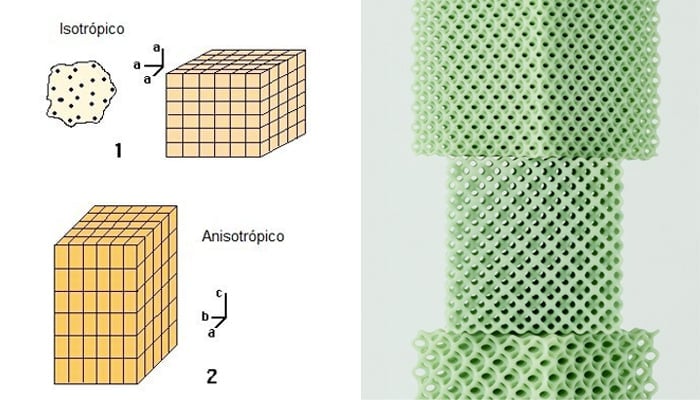
The difference between an isotropic and anisotropic model (Photo credits: IMA / Carbon)
In fact, sometimes the manufacturing method can cause anisotropy in the parts even though their raw material has isotropy. When this happens and anisotropic parts are obtained, it means that they have physical properties that are different depending on the direction in which they are measured. Let us now look at some techniques to maintain this degree of isotropy in 3D printing, focusing only on methods that work with polymers.
How To Achieve Isotropy in 3D Printing
The great advantage of obtaining 3D printed parts that are isotropic is that they offer greater mechanical resistance, which is necessary in many specific industrial applications. For this, multiple aspects must be taken into account to maintain this inert quality in the materials and to obtain final parts with the right properties for the desired industrial applications. In the following, we will analyze three specific points: design/slicing, printing and post-processing.
The Importance of Design and Slicing
The critical design and modeling stage is done at the beginning of any additive manufacturing process. Therefore, it is also an important step to take into account when it comes to achieving isotropic final parts. As we can see in the image above, the simpler and more symmetrical the parts are, the easier it will be for their strength to be the same everywhere. And we are not only talking about the general shape but also about the inside of the parts. The design of the geometry itself can also have an influence since lattice-type structures defined according to requirements can replace solid volumes. Therefore, although this decision is not strictly decisive, it must be taken into account for the subsequent manufacture of parts.
Finally, it is not only the geometrical conditions, the technology and the printing material that must be taken into account in this initial prefabrication phase. It is also important to understand the slicing process carried out on the slicer. Thus, the on-machine manufacturing position is essential to have control over the anisotropy induced by the process and to achieve maximum optimization. These parameters can be adjusted in the slicer program and can guarantee a correct manufacturing process for the final parts.
Choosing a Manufacturing Process
A key point to take into account if we want to obtain isotropic parts is to choose the right additive manufacturing technology. If we look at FDM 3D printing, one of the most widely used techniques today, we find a multitude of problems related to isotropy. During the thermoplastic extrusion process, an intertwining of the molten polymer chains is generated between each of the adjacent layers in order to hold the part together. As a result, microporous structures may be generated, where the real cross-section of the part varies in each direction with respect to the apparent cross-section. Since these polymer chain bonds are not very strong, the models obtained will be weaker in relation to the lines of the layers.
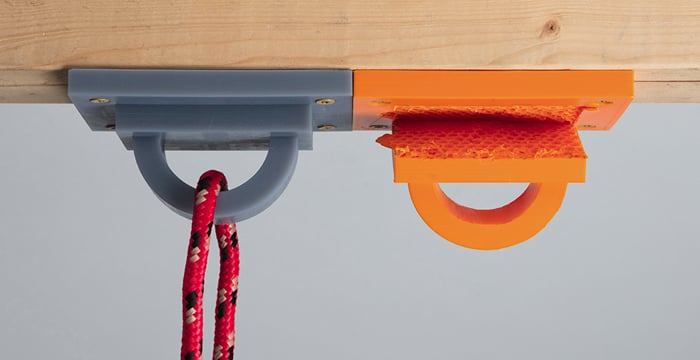
The orange part is anisotropic, and was created with FDM 3D printing (Photo credits: Formlabs)
In resin 3D printing (SLA or DLP), individual monomers are covalently bonded by the application of a light source, resulting in the formation of a solid cured polymer layer. Typically, the exposed layer is not completely cured and still contains unbound monomer groups. When the next layer is exposed, it is possible to establish additional covalent bonds between the current layer and the previous one. These bonds contribute to the formation of a much stronger network structure and a closer approximation of isotropy compared to FDM technology.
Finally, another additive technology that works with polymers is selective laser sintering (SLS). In fact, we can say that this is the technique that guarantees the best results for technical applications with 3D printing. As its name suggests, it consists of sintering polymeric microparticles layer by layer in powder form. In this case, users can resort to more widespread technical polymers in the industry such as PA11 and PA12, or even thermoplastic elastomers such as TPE and TPU.
With SLS 3D printing, parts with ideal characteristics for engineering applications can be more easily obtained, since they have high isotropy, high dimensional accuracy and allow the creation of models with complex geometries. It should be noted that the models manufactured via SLS 3D printing may still have porosity in their structure. However, unlike those created using FDM, this porosity is uniform and is not influenced by the orientation of the part during the printing process. This gives the parts a remarkable isotropy, since, although their real cross-sections do not match their apparent cross-sections, the latter remain uniform in all directions.
Post-Processing Techniques
Post-processing is the final necessary step in any additive manufacturing process. In this context, it can play a key role in increasing the bond between layers and reinforcing the isotropy of the parts. In the case of resin 3D printing, post-treatment techniques where heat is applied, such as thermal post-curing, promote further curing of the layers throughout the part. In turn, this provides a higher degree of mechanical isotropy in the part, almost as if they had been injection molded.
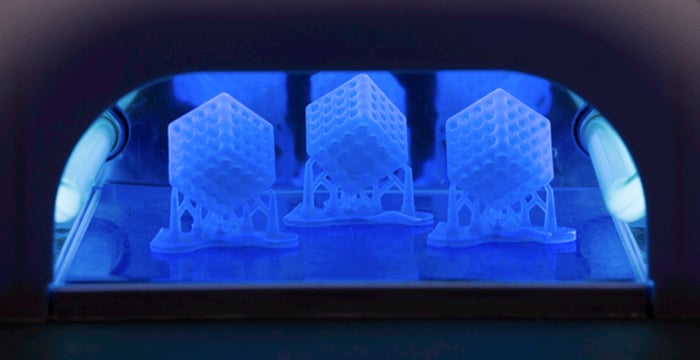
UV curing is a post-processing technique for resin-printed parts (Photo credits: Formlabs)
In addition, in cases where print support structures have been used, the removal of these may leave some defects on the surface of the parts. That is why some post-processing methods, such as polishing and sanding, can help to smooth these imperfections and avoid deformation of the parts for better isotropy.
What do you think about the importance of isotropy in 3D printing? Let us know in a comment below or on our LinkedIn, Facebook, and Twitter pages! Don’t forget to sign up for our free weekly newsletter here, the latest 3D printing news straight to your inbox! You can also find all our videos on our YouTube channel.
*Cover Photo Credits: polySpectra