Why Combine 3D Printing and Industrial Automation Applications?
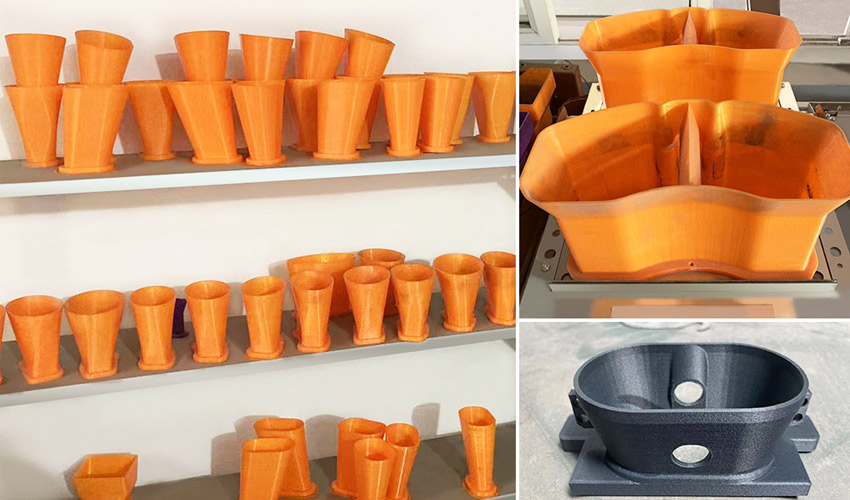
3D printing is widely used in the field of automation such as in compression molding. It’s a formative manufacturing method, currently popular in industry, that involves compressing the desired amount of molding material between two heated presses to give it its final shape. It is cost-effective compared to other production processes, allowing both small parts and large components to be designed. In addition, the base mold can be 3D printed, giving manufacturers more flexibility and geometric freedom. That’s why one electrical manufacturer has invested in several 3D printers from Flashforge, including 11 Creator 4 models. With this investment, the company was able to reduce its labor costs by 80% and cut delivery times by 50%.
Flashforge is a Chinese manufacturer that entered the 3D printing market in 2012. Since then, it has offered a wide range of solutions worldwide and caters to applications in education, healthcare, jewelry, and more. Among its wide range of 3D printers is the Creator 4, an industrial FDM machine with two independent extruders and different extrusion options to expand the range of compatible materials. It’s a ideal solution for multiples industries such as automotive, medical or consumer goods. It boasts a printing volume of 400mm*350mm*500mm, a heating plate capable of reaching 130°C and a closed chamber that can rise to 65°C. It is a solution that offers optimal temperature control combined with production flexibility, allowing it to be combined with automation processes, such as compression molding.
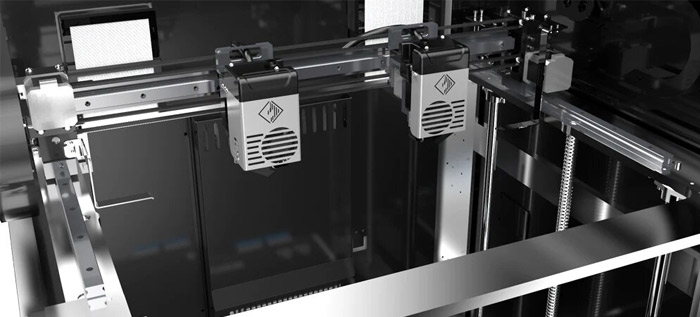
The Creator 4 offers two independent extruders
Integrating 3D Printing into the Compression Molding Process
One of the challenges of compression molding is the design of the hoppers and mold: each hopper must match the mold cavity exactly so that the material can flow properly. However, the molds used are not all the same shape, with different or irregular cavities, which multiplies the number of hoppers needed. Flashforge’s customer, which specializes in the manufacture of electrical equipment, explained: “Each project involves dozens, if not hundreds, of different shaped molds. Each size requires over a hundred hoppers. So, a completed project represents tens of thousands of hoppers. In the past, we have had to hire trade experts or even outsource the order. However, whichever solution we chose, it was costly in time and money, as was post-project maintenance.”
That’s where 3D printing comes in: the company relied on Flashforge’s Creator 4 machines to design the hoppers, freeing itself from the various shape, labor, time, and maintenance constraints of the past. As a result, the company invested in 11 machines and is now able to complete the design and production of 40 hoppers in a single day, about 10 more than before, all with only one employee on the job.

Photo credits: Flashforge
The 3D printer is capable of creating the hoppers with an accuracy of 0.2 mm to meet the necessary requirements. In addition, the Creator 4 is compatible with a wide range of materials, allowing the company to produce stronger, more abrasion-resistant molds and hoppers. The company uses ABS, nylon, polycarbonate and other technical materials to increase the durability of parts.
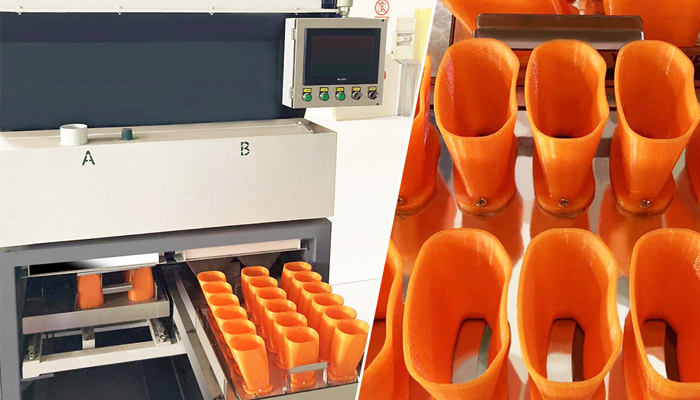
Photo credits: Flashforge
Benefits of Flashforge’s 3D Printing Solutions
In addition to this material compatibility, Flashforge 3D printers also allow teams to better control the manufacturing process and ensure that parts meet compression molding requirements. The resulting hoppers are lighter and easier to replace in the event of a defect.
Finally, the company estimates that it saved 10% of its labor costs in the first year and increased its output by 35%. A representative concluded: “Our customer orders are increasing and we will have to increase our production rate. Thanks to 3D printing, we can organize ourselves quickly and meet these growing needs. This is a real plus for us because we are able to meet demand in a flexible way.” If you have any 3D printing needs in terms of automation processes, feel free to contact Flashforge’s team HERE.
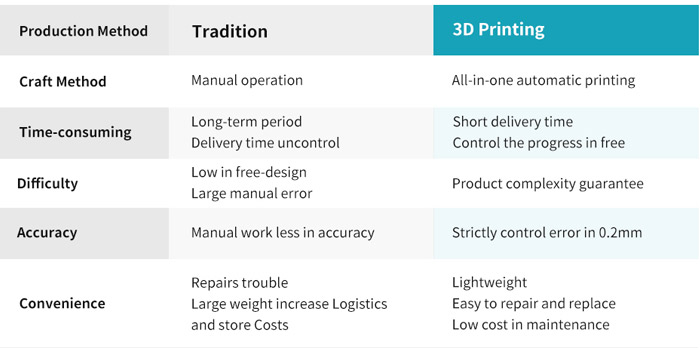
Comparison between traditional manufacturing process and 3D printing
What do you think of the combination of 3D printing and compression molding? Let us know in a comment below or on our LinkedIn, Facebook, and Twitter pages! Don’t forget to sign up for our free weekly Newsletter here, the latest 3D printing news straight to your inbox! You can also find all our videos on our YouTube channel.