What Are the Most Innovative 3D Printing Applications in the Automotive Sector?
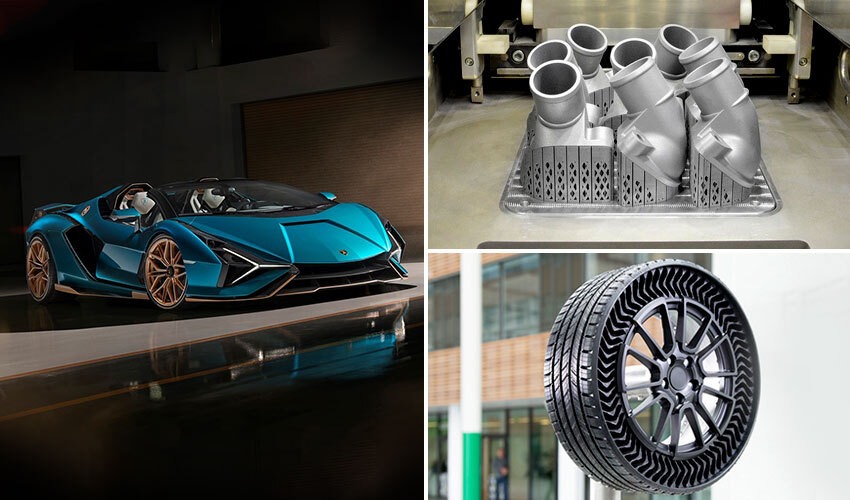
Among the application sectors in which we find additive manufacturing technologies, the automotive industry is one that is most taking advantage of them. AM allows large automotive companies to reduce costs, time and weight when producing complex parts. In addition, it also allows greater customisation at the design level. Given the significant growth that 3D printing is experiencing in the automotive industry, it is expected that by 2028 the figure will reach $12.4 billion. To better understand the impact that the integration of this technology is having on the industry, we have compiled a list of the major companies that use 3D printing in the automotive sector, as well as their various applications. The companies have been listed in alphabetical order.
Audi accelerates automotive design
Audi is a German multinational dedicated to the manufacture of top-of-the-range sports cars, and has been part of the Volkswagen group since 1965. A few years ago, the company decided to use Stratasys solutions with the aim of accelerating automotive design. PolyJet technology allowed Audi to develop and evaluate different prototypes before producing the parts of a vehicle. By incorporating the J750 3D printer into its line, the manufacturer was able to extend the production of models such as wheel covers, grilles, door handles or even rear light cabs, which are usually made of transparent plastic. With 3D printing, they were able to speed up automotive design and creation of final parts, meeting the demands of their customers.
Bentley Created More than 15,000 3D Printed Parts in 2021
The British car manufacturer Bentley is not only known for its renowned car bodies, but also for its ambitions to expand 3D printing applications for automobiles. Thanks to an investment of more than 3 million euros, the company was able to manufacture more than 15,000 components in 3D in 2021, saving time in design and manufacturing and minimizing waste. In addition to the process and economic advantages that Bentley derives from the use of additive manufacturing, its customers also experienced significant addded value. For example, thanks to 3D printing, they can have components produced in a completely individual and personalized manner.
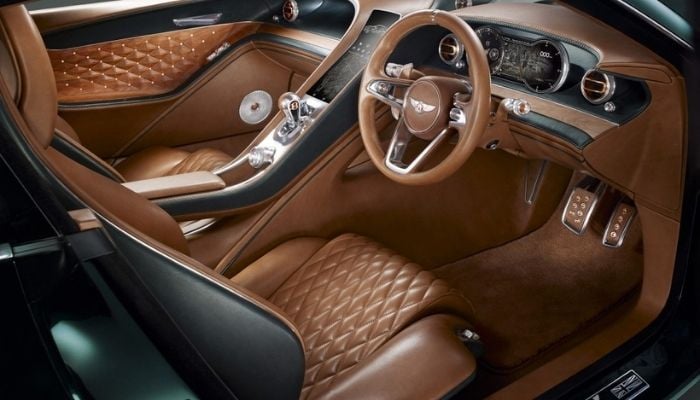
Photo Credits: Bentley
BMW opts for additive manufacturing
Next in our list of companies implementing 3D printing in the automotive sector is the German giant BMW. Based in Munich, it has been using additive manufacturing for more than 25 years and was one of the first automakers to integrate this technology. In June 2020 they finally opened their own additive manufacturing centre with the aim of pooling their production skills. This campus has over 80 employees and more than 50 industrial manufacturing solutions. In addition to the centre, BMW has demonstrated its capabilities on numerous occasions, for example with the i8 Roadster sports car. This model integrates parts that are much lighter than if they had been created using traditional methods. Parts such as the bonnet support are now stronger as well as lighter. An advanced method of optimising car production.
The Bugatti Bolide is Lighter and Faster Thanks to 3D printing
In order to create its by far lightest, fastest and most aggressive vehicle to date, French car manufacturer Bugatti turned to AM. The Bolide, as this sportscar with an assortment of new technologies is called, has 3D printed certain parts that reduce the weight of its components significantly. The manufacturers integrated many of their earlier revealed individual AM manufactured parts, with a titanium printed brake caliper and a processed spoiler support and engine mount from SLM Solutions being only a few examples of the numerous 3D printed parts in the innovative vehicle. The integration of 3D printing was especially important for the complex shaped parts as well as to help to make the Bugatti Bolide a lightweight and therefore much faster sportscar.
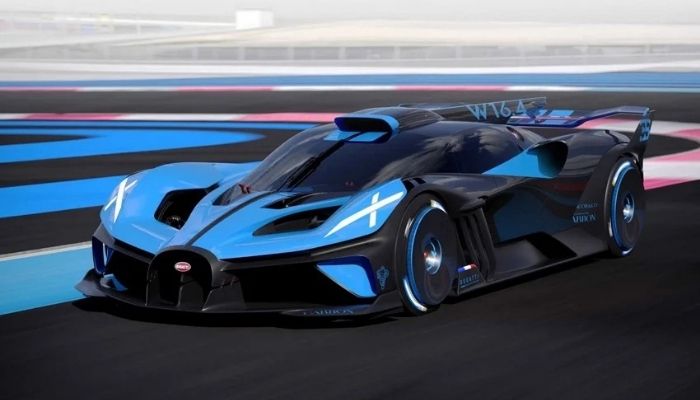
Photo Credits: Bugatti
Dallara and its 3D Printed Heat Exchangers
Italian automaker Dallara has turned to Conflux Technology to manufacture the heat exchangers for its Formula 3 cars. The company relies on additive manufacturing to produce parts that are more efficient and more resistant to heat. More specifically, it uses laser fusion machines on a powder bed from EOS. The particularity of this project lies in the size of the exchangers: Dallara needed small components that could meet the requirements of motorsport. Conflux Technology therefore came up with several CAD and CFD designs and printed several iterations to validate the geometry and study the characteristics of the part such as surface roughness.
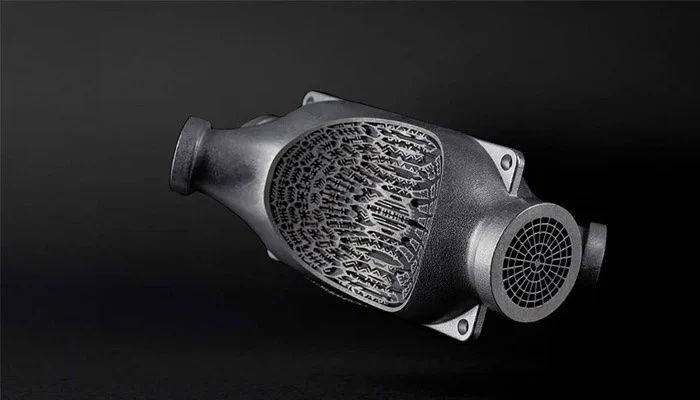
Photo Credits: Conflux Technology
Ferrari and Metal Additive Manufacturing
Additive manufacturing has a key role in motor sport, enabling the design of lighter, stronger and more efficient parts in a much shorter time frame. The manufacturer Ferrari has therefore relied on this technology – in particular metal 3D printing – to design the pistons of one of its engines. Ferrari explains that it used an EOS machine and titanium powder and that additive manufacturing enabled it to imagine a much more complex, resistant and lighter part thanks in particular to topological optimisation. This method also increases the number of possible iterations: the company can imagine as many designs as necessary and accelerate its prototyping phase. The manufacturer has also designed 3D printed brake pedals with a hollow structure – a result that would not have been possible using other manufacturing methods.
Ford’s 3D printing projects
In 1988, the car manufacturer Ford had already invested in three 3D printers; in 2015, it estimated its production of 3D printed parts at 500,000, proof that the technology has a place of importance for the American company. And for good reason, the company has forged strong partnerships with certain manufacturers such as Desktop Metal and Carbon. If we look at the parts made by Ford, we have to tell you about its aluminium air intake manifold, one of the largest 3D printed metal parts for the automobile. It weighs 6 kilos and was made in just 5 days. More recently, the American has come up with customised wheel nuts to protect the rims. Printed on EOS machines, these lug nuts were modelled from the driver’s voice: this is converted into a 3D model and printed inside the nut. This is an effective method of combating theft, since only the driver’s voice can be used to remove the nuts.
Lamborghini uses AM to personalize Sian Roadster
Lamborghini is associated with everything except affordability – the brand is the definition of high-end expensive sports cars. Nevertheless, the company still actively uses additive manufacturing because AM offers more than just saved costs and rapid production, for Lamborghini 3D printing represents endless opportunities of customization. Unveiled this summer, Lamborghini’s Sian Roadster can be highly personalized according to the client’s preferences. The newly designed air vents were manufactured using additive manufacturing technology allowing perfect customization: among other things, customers will be able to have their initials integrated in the design of this car element.
McLaren’s New Artura Hybrid Supercar
Like many other car brands, luxury carmaker McLaren is no stranger to the benefits of AM. For its high-performance hybrid supercar, the Artura, which McLaren engineered to combine technology, design and unmatched performance, the company chose to rely on 3D metal printing. The British automobile manufacturer enabled the innovative method to design the engine block and cylinder head cores to allow better cooling of the engine, and therefore better performance. The general focus of the company when creating the concept of the supercar was on making its weight lighter compared to other similar vehicles. In order to make that possible, the designing team used carbon fiber to design a lighter frame. In addition to that, they incorporated 3D printed cores in the engine block and aluminum cylinder heads, which, without the use of AM, would have been impossible to create in such precise detail.
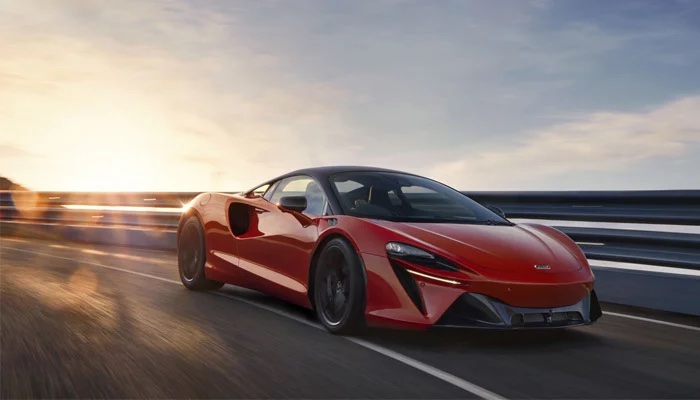
Photo Credits: McLaren
Mercedes’ Various Uses for Additive Manufacturing
The automotive industry is not limited to vehicles for transporting people but also includes vehicles for transporting goods, so we felt it was important to talk about Mercedes’ trucks. After initially focusing successfully on 3D printing plastic parts, Mercedes is now manufacturing truck parts in metal. By using metal additive manufacturing, replacement parts become stronger and more flexible. Another advantage is that Mercedes has the ability to produce these parts in small quantities and at low cost. Mercedes is the first company to focus on the production of truck parts. While Mercedes is the first company to focus on truck parts production, it also uses technology to optimize some of its cars. For one of its latest vehicles, the EQXX, the German brand used 3D technologies to reduce the weight of components and to limit manufacturing costs and time.
3D Printed Tires from Michelin
French tire manufacturer Michelin has introduced its first prototype tire using additive manufacturing technologies in 2019. Called Uptis (Unique Puncture-proof Tire System), the tires were designed to be airless to reduce the risk of punctures. The company worked with U.S.-based General Motors to develop the 3D printed prototype. In addition, the company says that additive manufacturing could be used to repair the puncture-resistant rubber strip if needed. As a testament to success, the Uptis tires drove their first few miles in 2021. And following this success, the company hopes to move to commercialization by 2024. To date, 3D printing has only been used to develop the prototype, using renewable and bio-based materials, but should production reach higher volumes, the technology could be employed on a larger scale. Reducing waste and promoting sustainable mobility, Uptis tires incorporate a flexible fiberglass and rubber-reinforced structure on an aluminum wheel.
The Mini Strip, a Sustainable Vehicle Thanks to 3D Printing
By opting for 3D printing, the British car manufacturer MINI affirms its desire to offer more sustainable cars to its customers. The MINI Strip, designed by Paul Smith, is intended to be environmentally friendly. To achieve this, the teams behind the project have 3D printed various parts from recycled materials. These include floor mats made from recycled rubber, under-door panels and hubcaps. In addition to making the car more sustainable, these multiple 3D printed parts give the MINI Strip a simplified geometry and a sleek design.
Porsche and the first 3D printed engine pistons
You have almost certainly heard of famed luxury carmaker Porsche. But what you might not know is that the manufacturer has been using additive manufacturing since the early 1990s. In fact, in 2020 the company made tracks on several major projects using 3D printing including 3D printed engine pistons for the high-performance engine of the Porsche 911 GT2 and a 3D printed, 40% lighter electric drive housing. Though recently there have not been any major news in regards to 3D printed parts from the company, at the end of 2021 they did announce that they were investing in 3D printing specialist INTAMSYS, which is especially known for its high-performance materials, suggesting that 3D printing will continue to play a major role in their cars.
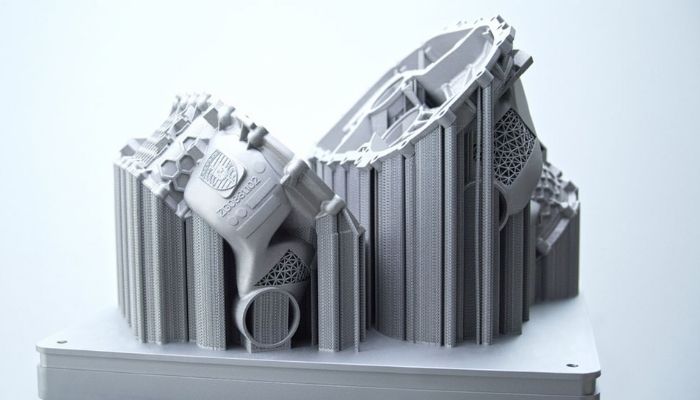
Photo Credits: Porsche
SEAT and 3D Printing in the Automotive Sector
The Spanish manufacturer SEAT is advancing the use of 3D printing in automotive as well. The company has recently completed a new 3,000 m2 building that will unify all processes and activities prior to mass production of a new model. A large space in the new center will be dedicated to additive manufacturing projects. SEAT’s AM center houses multiple 3D printers, nine, to be precise. The machines include: an HP Multi Jet Fusion, an SLS machine, 6 FDM 3D printers and a PolyJet solution. Thanks to the diversity of these technologies, SEAT is able to produce parts with greater or lesser detail, with important mechanical properties and advanced functionalities. The machines operate 24 hours a day and produce an average of 50 parts per day. According to the manufacturer, 80% of the parts are prototypes used to develop vehicles more quickly, the rest being mainly tooling and customization components.
Vital Auto and the Cars of the Future
Founded in 2015, British industrial design studio Vital Auto specializes in automotive design. The company’s illustrious clients include many global car manufacturers, such as Volvo, Nissan and McLaren. And in order to provide them with high-quality prototypes quickly and at a reduced cost, Vital Auto uses Formlabs’ Form 3L and Fuse 1 3D printers. From design to production, the company has integrated additive manufacturing into its entire production process. Anthony Barnicott, Design Engineer in charge of additive manufacturing at Vital Autos, explained, “We’ve used 3D printing from day one. We wanted to introduce it to our manufacturing processes, not only to reduce costs, but to give the customer more diversity with their designs and their ideas. What interests me most about the Form 3L machines is their versatility, the ability to do a material change in less than five minutes and the variability of those materials going from a soft, flexible material to a hard and rigid material for us is priceless.”
YOYO, the 3D Printed Electric Vehicle
As global warming becomes an increasing concern worldwide, more and more people are turning to more eco-friendly alternatives to traditional products, including electric cars. And 3D printing is no exception in that regard. Take for example, YOYO, the fully-electric city car from XEV. The car was made mostly with 3D printing, large-format additive manufacturing to be exact. According to the company, YOYO is the more sustainable solution to urban mobility thanks to a 100% electric motor and 3D printing of course was chosen due to its more sustainable nature as compared to traditional manufacturing methods.
What do you think about these 3D printing applications in the automotive sector? Let us know in a comment down below or on our Facebook and Twitter pages! Don’t forget to sign up for our free weekly Newsletter, with all the latest news in 3D printing delivered straight to your inbox!
Great technology which, along with the process of sintering, will create some of the lightest, most durable, as well as uniquely functional devices and wearables. This would ensure faster production of materials, quite possibly at prices which are more equitable in one’s understanding of the buyer’s mantra, “you get what you pay for.”