Recent 3D Printing Applications in the Aeronautics Sector
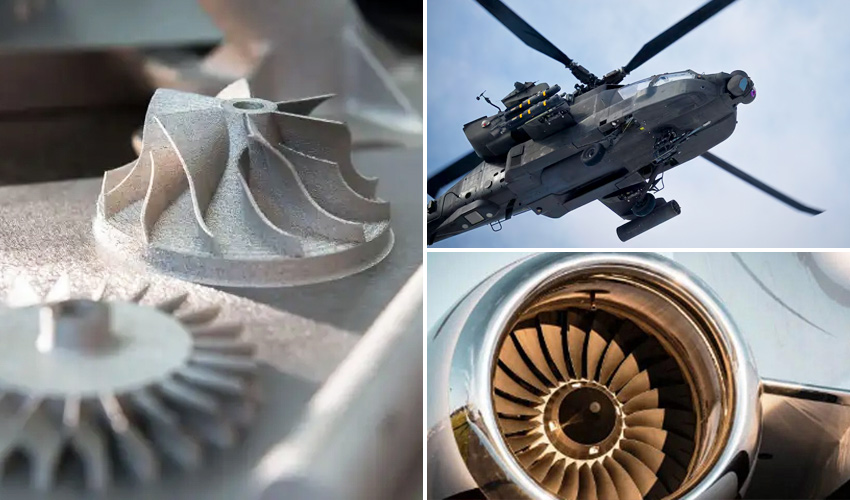
Additive manufacturing is amazing for producing lightweight, strong and geometrically complex parts—so the technology is particularly valuable in the aeronautics sector, where strength and weight optimization are critical. Aeronautics is the science and practice of designing, building, and flying all aircraft, except those that go into space. The sector was one of the earliest adopters of AM, initially using it for rapid prototyping. Today, however, its applications have expanded to include end-use parts in airplanes, helicopters, drones and more. To showcase the versatility and impact of 3D printing in this field, we have compiled a list of some of the most recent and remarkable applications of AM in aeronautics.
Norsk Titanium Supplies Parts for Boeing 787, Launches Supplier Partnership
Norsk Titanium US Inc., a leader in titanium additive manufacturing and active in the aerospace industry, already supplied parts for the Boeing 787 Dreamliner in 2021. The company is best known for its patented Rapid Plasma Deposition® technology, which improves the strength and durability of the finished part and works similarly to directed energy deposition (DED). Norsk’s technology is different because it uses an electron beam to heat powder in several places simultaneously. Among the parts they created were 3D printed titanium components certified by the FAA (Federal Aviation Administration). Now the company has agreed to supply volume production parts directly to The Boeing Company, marking the beginning of a direct supplier relationship. Norsk Titanium expects to provide hundreds of structural parts by 2025. ““Our RPD® technology and established material specifications position Norsk Titanium to react quickly to the demands of our customers,” explains Nick Mayer, VP of Commercial.
ITP Aero Obtains EASA Certification for 3D Components
Based in Vizcaya, ITP Aero has successfully obtained certifications from the European Aviation Safety Agency (EASA) and the Spanish Aviation Safety Agency (AESA) for 3D-printed structural components. The company thus becomes the first in the aero engine industry to receive these approvals for parts manufactured using selective laser sintering (SLS), applied to the rear blades of the TP400 engine. This industrial additive manufacturing process allows the creation of complex components using less material and energy, which contributes to the sector’s sustainability. In addition, ITP Aero has developed its own additive manufacturing standards and specifications for high-temperature aero-engine components. The company has a dedicated manufacturing cell and is building the “ADMIRE” research center to further advance digital and sustainable manufacturing technologies.
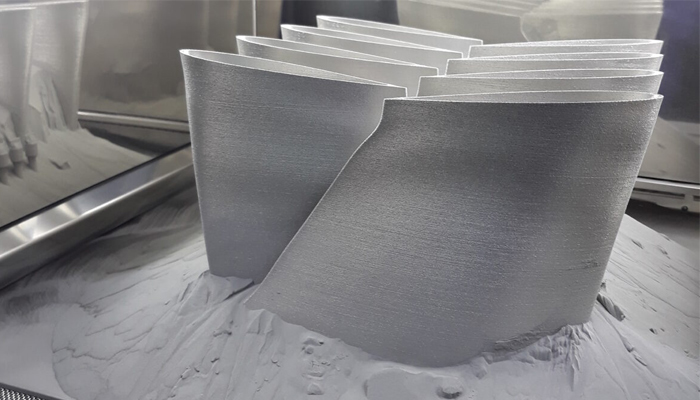
Photo Credits: ITP Aero
Safran Invests €80M for 3D Printing Campus
Safran is an international high-tech group operating in the aerospace, space and defense sectors. It invested 80 million euros to open a campus dedicated to additive manufacturing in Le Haillan, near Bordeaux. The goal was to create a large center of excellence for additive manufacturing. The campus, which houses about 200 employees specializing in 3D printing, is about 12,500 meters. Inside are at least eight 3D printers with powder bed fusion technologies, finishing equipment, two heat treatment furnaces, a scanning electric microscope, a metallurgical lab and a powder lab. Safran aims to integrate additive manufacturing within its engine components from 1 percent to 25 percent. The company has produced more than 1,000 3D-printed parts so far. This investment by Safran is another step toward strengthening collaboration between European companies, research institutes, and defense, bringing them closer to the massive investments of the United States, which, to date, continues to dominate in this sector.
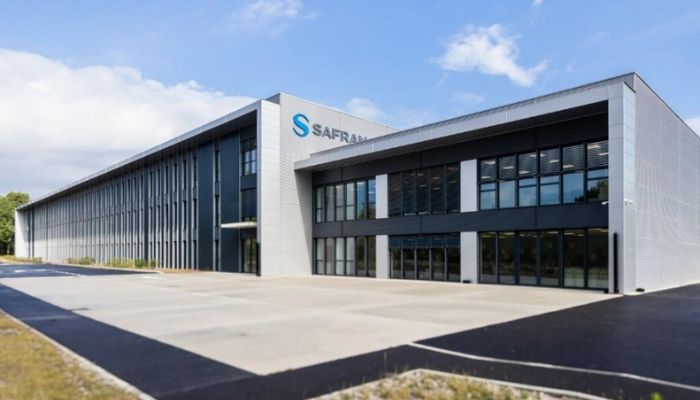
Photo Credits: Safran
Materialise Develops 3D Printed Cabin Solutions
Materialise has expanded its role in the aerospace maintenance, repair and overhaul (MRO) sector and is now working with Proponent, the world’s largest aerospace distributor, and Stirling Dynamics, a leading EASA 21. J-certified design organization, to develop 3D printed cabin solutions. Materialise has previously partnered with Airbus and EOS to successfully produce 3D-printed parts for the A350 aircraft, including around 100 flame-retardant parts. The aim of the new partnership is now to provide certified 3D-printed spare parts for the aviation industry. Stirling Dynamics will focus on improving designs for cabin interior parts, while Materialise will utilize its certified production capabilities. “By combining our respective expertise, we are creating a powerful alliance with the skills needed to lower AM adoption barriers in the aeronautics industry,” explains Jurgen Laudus, Vice President of Materialise Manufacturing. The collaboration has already resulted in several cabin repair solutions that target specific problems in aircraft cabins. Proponent in particular has played a key role by working with OEMs to offer these solutions worldwide.
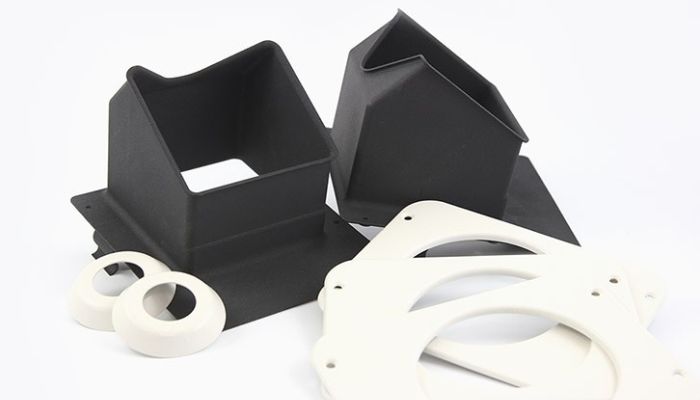
Airworthy parts made of flame-retardant PA 2241 FR material, which is offered by Materialise in Airbus-certified quality (Photo Credits: Materialise)
Lufthansa Uses 3D Printing to Create Cabin Parts for Planes
Lufthansa Technik is a leading provider of civil aircraft maintenance, repair, overhaul and modification services. The company uses polymer additive manufacturing to redesign cabin parts and to reproduce conventional aircraft parts, as well as customize VIP passenger cabins. The AM technology is being used to make conventional airliner cabin components stronger and lighter. They have already improved the function of ventilation grilles, clips and covers for their aircraft. Lufthansa plans to increasingly use additive manufacturing, especially for bionic design, which is the application of biological methods to 3D printing technologies. According to the company, adjustments to cabin design and weight reduction made with AM can contribute significantly to the aviation industry’s efforts for greater sustainability and reduced carbon footprint.
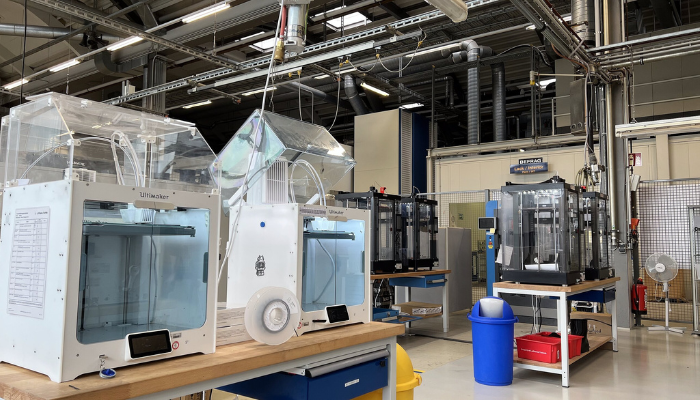
Photo Credits: Lufthansa Group
Airbus Helicopters’ 3D Printing Center
Airbus is no stranger to 3D printing, as the company has been integrating 3D-printed parts into its aircraft for years. Often, they have outsourced additive manufacturing services, but in late 2023 Airbus Helicopters opened its own 3D printing center at its Donauwörth, Germany site, expanding its in-house AM capabilities. The center has three machines for titanium parts, four for plastic and one for aluminum. Airbus Helicopters uses the technology to create serial production parts, in addition to parts for prototypes like CityAirbus NextGen eVTOL and the high-speed Racer experimental compound helicopter. Stefan Thomé, Airbus Helicopters managing director for Germany, explained the benefits of using AM. “Among other advantages, 3D printing can reduce the weight of aircraft components, which leads to less fuel consumption,” Thomé said. “Such potential can bring financial benefits and contribute to reducing CO2 emissions during operations.”
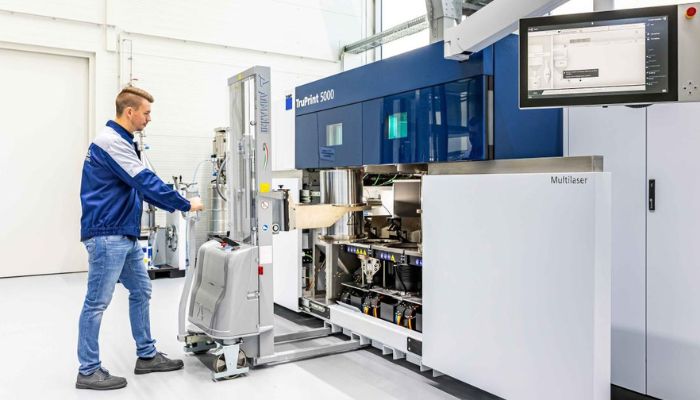
Photo Credits: Airbus Helicopters
3D Rotors for Boeing’s Apache Helicopters
Boeing has begun testing a complete 3D-printed main rotor system for the AH-64 Apache attack helicopter. This project aims to reduce lead times and improve supply chains for normally forged parts. At the Association of the U.S. Army’s annual conference, Boeing and ASTRO America unveiled their first 3D-printed component. It is a main rotor linkage, fabricated on a large-format metal 3D printer. Government-funded ASTRO has been working on a $95 million contract to develop additive manufacturing capabilities for large parts, such as tank hulls. A 3D-printed component of the main rotor was made in eight hours, compared with the year it would normally take to forge it. Boeing wants to perform large-scale fatigue testing on these, which could speed up aircraft repair and optimize parts manufacturing.
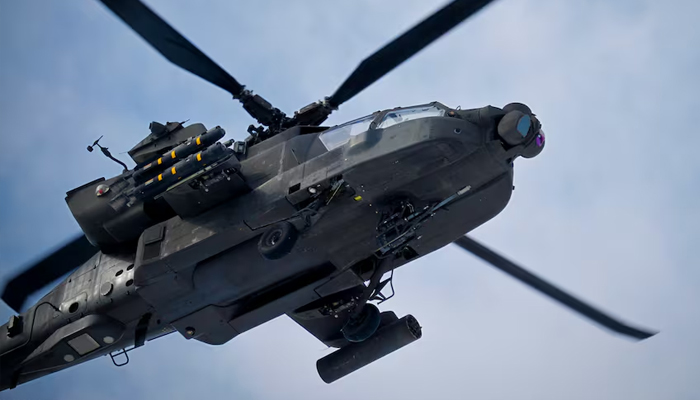
Photo Credits: Boeing
Finnair Uses 3D Printed Parts in A320 Planes
Remember the video panels that some airplanes have overhead seats? Many airlines, including the Finnish airline Finnair, are phasing them out. The company recently replaced them with 3D-printed blanking panels (panels used to cover “gaps” of unused space) in its Airbus A320 cabins, to offer a lightweight alternative to the heavy video players. The additive manufacturing company AM Craft created over 300 blanking panels to upgrade 17 of Finnair’s A320 planes. According to Finnair, 3D printing the panels helped to minimize excess inventory and reduce costs associated with the traditional supply chain. And, Aviation Week reported that the panels were designed to work with the existing mounting rails for easy installation. What’s more, any airline with A320 planes could benefit from this 3D printing project because the blanking panels are available in AM Craft’s digital catalog.
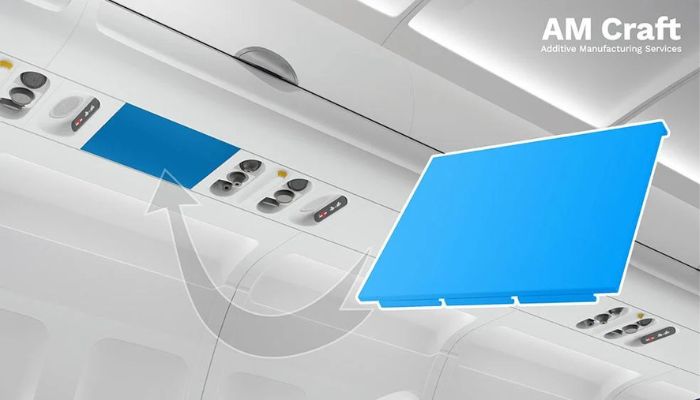
Photo Credits: AM Craft
Liebherr-Aerospace Lindenberg GmbH Produces 3D-printed Flexible Shaft
Liebherr-Aerospace Lindenberg GmbH, a company that manufactures integrated systems for the aviation industry, has now developed a flexible flex shaft for aviation applications using additive layer manufacturing (ALM). Traditionally, this consists of seven components that are joined using complex processes. 3D printing simplifies this process, reducing the need for maintenance and making production less complex. The flex shaft 3D-printed from titanium powder, which has been approved for series production by Airbus and EASA, is to be integrated into the differential gear of the flap system of the Airbus A350. It transmits rotational movements to a position sensor and helps to compensate for angular and axial errors between the gearbox and the sensor. The approval of the 3D-printed flex shaft underlines that additive manufacturing is a reliable technology for improving sustainability in aviation. “The flex shaft demonstrates how different functions can be efficiently integrated into one component. Extensive tests showed the reliability of this novel design approach, which opens the door for more complex and critical applications of AM in the future,” explains Svenja Pestotnik, Head of Additive Manufacturing at Liebherr-Aerospace Lindenberg GmbH.
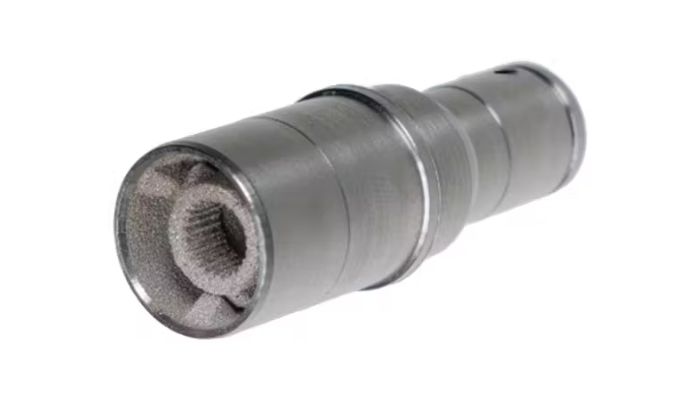
The flexible shaft from Liebherr-Aerospace has a more complex design and is produced from titanium powder using additive manufacturing technology. (Photo Credits: Liebherr-Aerospace Lindenberg GmbH)
LEAP and Additive Manufacturing
It’s hard to miss LEAP when it comes to aeronautics and 3D printing. Designed by CFM International, a joint venture between GE Aerospace and Safran Aircraft Engines, it is a propulsion system for commercial aircraft (such as the Airbus A320neo or Boeing 737 MAX) that was launched in 2016. Its primary objectives were to reduce fuel efficiency, CO2 emissions and noise. On the eve of its 10th anniversary, LEAP has lived up to its promises, according to CFM. But what really interests us is the 3D printing part. The propulsion system was partially designed using additive manufacturing, in particular the turbine fairings, nozzle tips and fuel injectors. A laser fusion process on a powder bed was chosen.
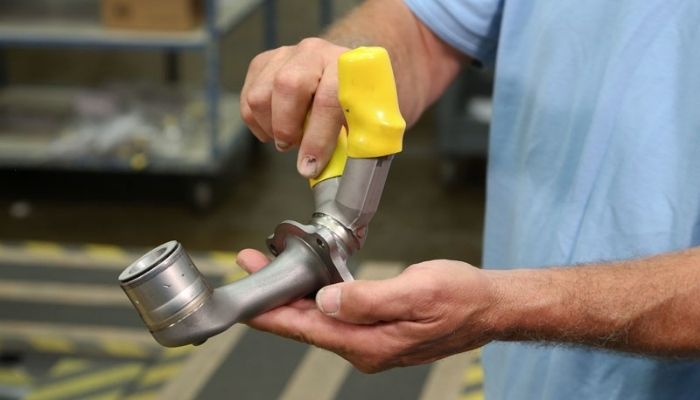
Photo Credits: GE
Marines Make Reamer Maintenance of F-35B Lightning II More Efficient
The goal of Marine Aviation Logistics Squadron 13 is to provide logistical support to the Marine Aircraft Group, like personnel and spare parts. However, in July 2024, MALS-13 faced a critical shortage of reamers for the F-35B Lightning II squadrons. These are essential precision-cutting tools for aviation maintenance. Conventional reamers were indeed expensive, and MALS-13 had insufficient quantities of them due to long procurement times. Using additive manufacturing, they created an on-demand solution by developing high-performance reamers. In this way, they reduced not only maintenance costs by more than 50 percent but also procurement time. The parts went from being available in three months to being produced within the same day. To recreate the missing reamers, two Markforged X7 industrial 3D printers were purchased, enabling MALS-13 to produce the aerospace-grade parts in-house, eliminating dependence on outside suppliers.
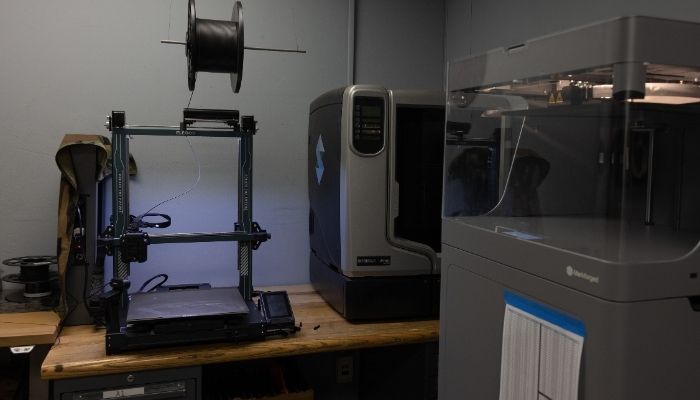
Photo Credits: Lance Cpl. Elizabeth Gallagher
The Titan Falcon Drone
When it comes to aeronautics, we can’t overlook unmanned aerial vehicles, more commonly known as drones. Whatever their use – exploration, military, research, etc. – they are increasingly numerous, and can incorporate 3D-printed parts. Such is the case of the Titan Falcon developed by Titan Dynamics. It has an autonomy of 6 hours and a range of 400 kilometers, enabling it to cover a wide area. Equipped with a camera, it is an ideal solution for battlefield surveillance – it was in fact used during the conflict between Ukraine and Russia. As far as additive manufacturing is concerned, the company remains mysterious as to the materials and technology employed, but what is certain is that it has reduced lead times and facilitated iterations.
Conflux Manufactures Heat Cxchangers Using Metal 3D Printing
Conflux contributes to modern aviation with the help of 3D printing by ensuring greater performance and reliability. The company manufactures heat exchangers for aircraft using metal 3D printing in order to realize more complex geometries and thus optimize the performance of the heat exchangers. This contributes to the overall performance of the aircraft. On the one hand, the overall weight can be reduced thanks to lightweight components, while on the other, efficient heat management has a direct impact on the performance and range of an aircraft.
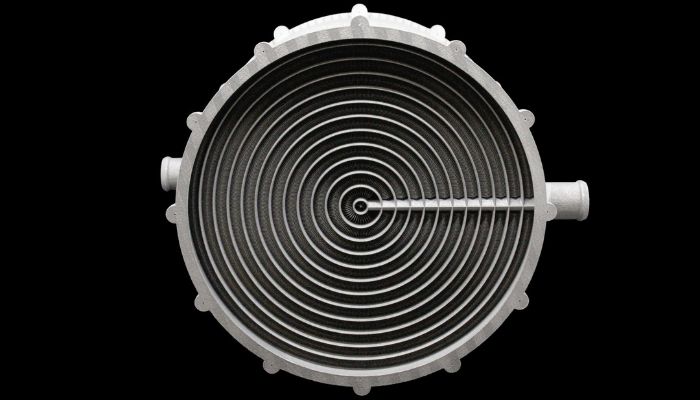
Photo Credits: Conflux
3D Printed Helicopter Cockpit For a Full-Flight Simulator
In 2024, Murtfeldt Additive Solutions printed a modular helicopter cockpit on behalf of Reiser Simulation and Training GmbH. Murtfeldt used several units of the large-format Queen 1 3D printer from Q.BIG 3D. Using the VFGF (variable fused granulate fabrication) process, the individual components could each be 3D printed and then quickly assembled. The longest printing time for a single component was 100 hours, while the total production time was just over a month. With dimensions of 2,260 mm x 1,780 mm x 17.05 mm, the cockpit weighs only 200 kilograms. 3D printing with plastic pellets proved valuable in this project in order to achieve lightweight construction goals and produce more economically. As many tools are required for such a project in traditional production, 3D printing has reduced costs. In addition, the price of pellets for large-format prints is much more attractive than that of filament.
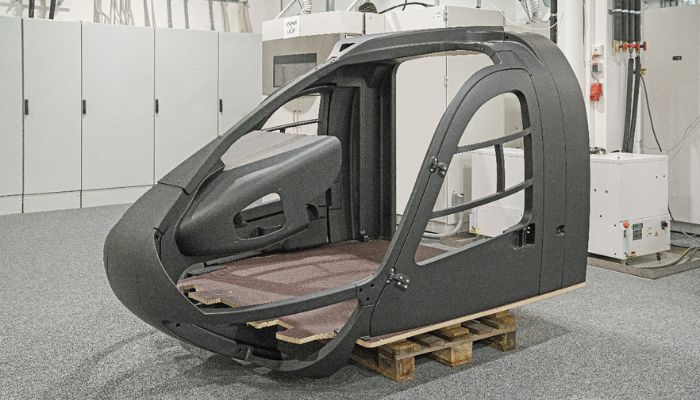
Photo Credits: Q.BIG 3D
BEAMIT and Leonardo Aircraft Partner for Additive Manufacturing Mass Production
The Italian Leonardo Group is one of the leading international players in building technological capabilities in aerospace, defense & security. The company is a technology partner of governments, defense administrations, institutions and companies. The use of additive manufacturing in Leonardo’s activities has long been well known. In recent years, in particular, as far as the Aircraft division is concerned, Leonardo has renewed a partnership with the BEAMIT service for mass production of various components with Additive Manufacturing technology in metal, which will be active until at least 2028. To date, Leonardo Aircraft now has more than 100 qualified parts with BEAMIT that are currently installed on key aircraft such as the M345, M346, and C27J.
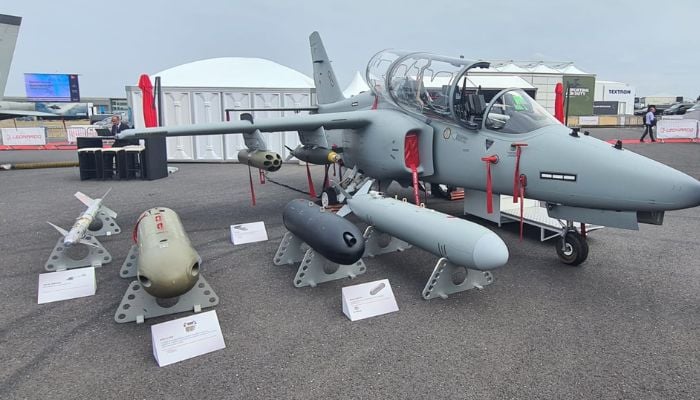
Leonardo M-345. (Photo Credit: Italia Vola)
MIMOSA Project Optimizes Aircraft with 3D Printing
The European MIMOSA project, with the participation of various European institutional and corporate partners, was launched in 2022 and aims to transform aircraft construction through the joint use of 3D printed composite materials and metals. The project aims to support the next generations of aircraft, which will necessarily have to follow production criteria with reduced environmental impact and lower need for raw materials.
The study is based on the realization of multi-material structures composed of metal alloys and composite materials without intermediate elements, through the integration of metal additive manufacturing, plasma surface treatments and carbon fibers. At the end of service, structures made with MIMOSA technology can be regenerated through an “atomization” process, reducing waste and becoming “secondary” raw material for the same additive manufacturing processes.
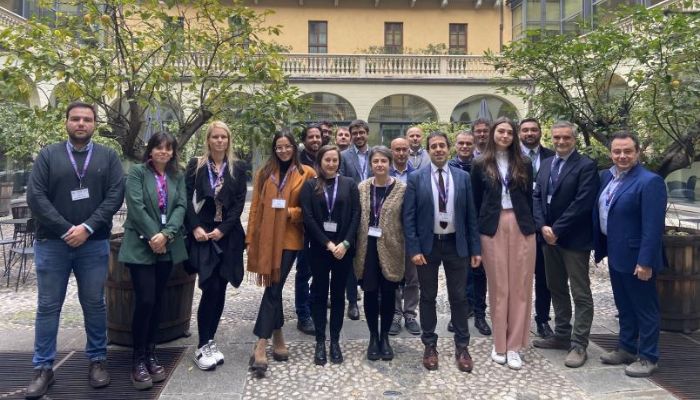
The MIMOSA project team (Photo Credits: Polytechnic University of Turin)
What do you think about the future of 3D printing aeronautics? Let us know in a comment below or on our Facebook and Twitter pages! And, for more on additive manufacturing in aerospace, check out our dedicated page HERE. Don’t forget to sign up for our free weekly Newsletter, with all the latest news in 3D printing delivered straight to your inbox!
3D printing technology was good for aeronautical equipment’s and Military equipment’s and other area also developed..
3D printing technology was good for aeronautical equipment’s and Military equipment’s and other area also developed.
It’s fascinating to see companies leveraging 3D printing to create lighter components.