3D Printed Tungsten Paves Way for More Efficient Fusion Energy
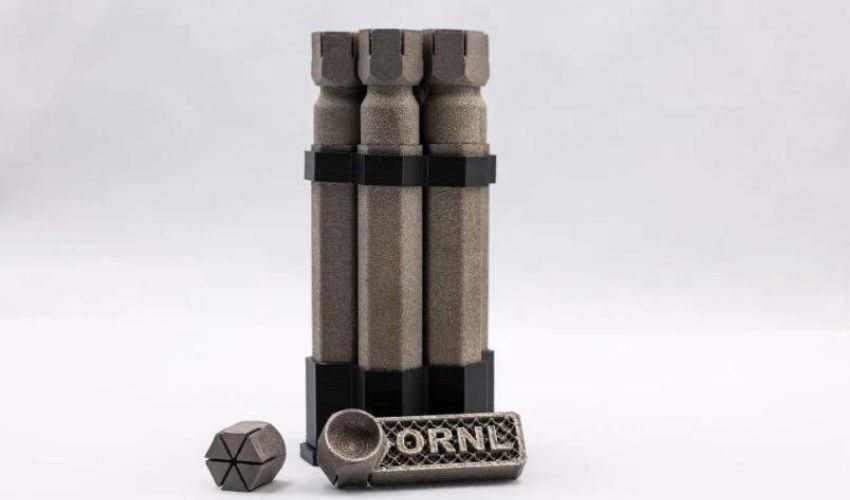
Fusion energy holds promise as a potential solution to humanity’s energy demands. However, unlike nuclear fission, the development of economically viable fusion reactors faces significant challenges. One such obstacle is the intense neutron irradiation that subjects reactor materials to extreme stress, increasing the risk of embrittlement. To address this, researchers at Oak Ridge National Laboratory have turned to 3D printing to create flawless tungsten components capable of withstanding the extreme temperatures and conditions within fusion reactors. Leveraging additive electron beam manufacturing, they have successfully produced complex tungsten parts with intricate geometries, paving the way for advancements in fusion energy technology.
The challenges inherent in fusion technology primarily stem from the rigorous demands placed on the materials utilized, necessitating resilience against extreme temperatures and intense energy levels. Tungsten emerges as a promising candidate due to its remarkably high melting point, rendering it well-suited for fusion reactors where plasma temperatures soar beyond 180 million degrees Fahrenheit. However, despite its favorable properties, tungsten presents a paradox: while highly durable under extreme conditions, it becomes brittle and prone to fracture at room temperature and in its pure state. The slightest impurities can induce alterations in its structure, exacerbating its fragility.
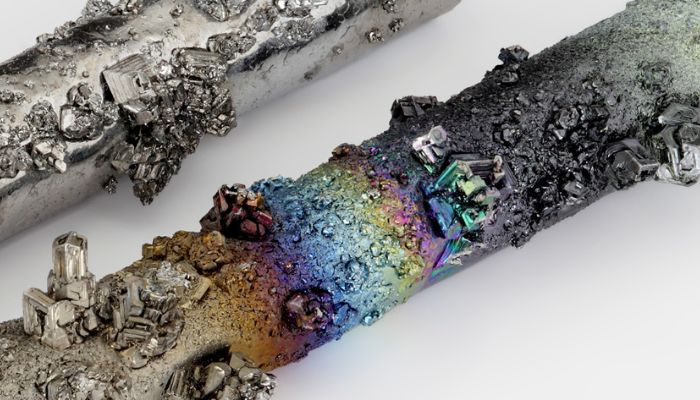
Tungsten is a shiny white heavy metal with a high density and has the highest melting point of all metals at 3422°C. (Photo Credits: Heinrich Pniok via Wikimedia Commons)
The solution to embrittlement is an electron beam 3D printer that applies tungsten layer by layer into precise shapes. To melt the metal powder and bond it into a solid metal object, the technology uses a magnetically directed stream of particles in a high-vacuum housing. The vacuum reduces contamination from foreign material and the formation of residual stresses.
The breakthrough achieved by researchers at ORNL’s Manufacturing Demonstration Facility, with support from the DOE’s Advanced Materials and Manufacturing Technologies Office, holds the potential to enhance both the safety and efficiency of fusion reactors moving forward. This advancement not only offers a promising alternative to traditional nuclear reactors but also represents a significant stride toward sustainable energy production. By mitigating carbon emissions, fusion technology aligns with global efforts to combat climate change.
Moreover, the development of 3D-manufactured tungsten components could extend beyond fusion applications, finding utility in various high-temperature scenarios across industries. When speaking on the benefits of this material, Michael Kirka, Senior Research staff member at ORNL, stated:
Electron-beam additive manufacturing is promising for the processing of complex tungsten geometries. This is an important step for expanding the use of temperature-resistant metals in energy resources that will support a sustainable, carbon-free future.”
What do you think of these 3D printed tungsten components? Let us know in a comment below or on our LinkedIn, Facebook, and Twitter pages! Don’t forget to sign up for our free weekly newsletter here for the latest 3D printing news straight to your inbox! You can also find all our videos on our YouTube channel.
*Cover Photo Credits: Oak Ridge National Laboratory