Researchers create 3D printed sweating robot muscle
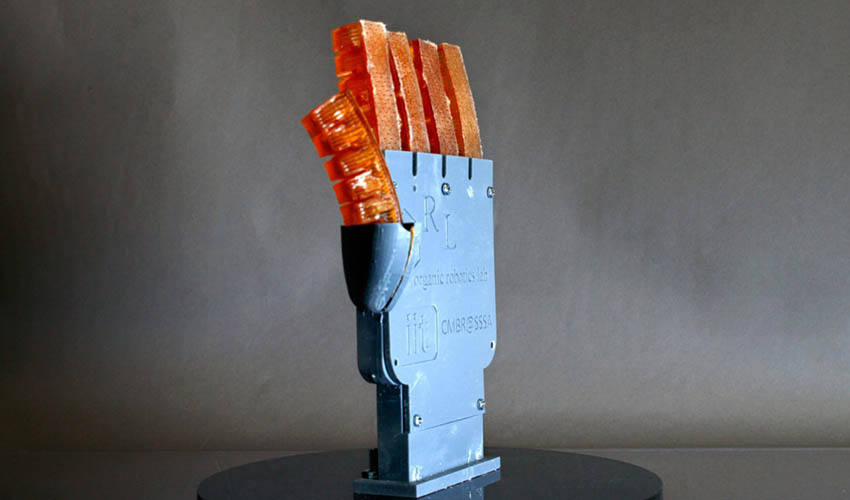
At Cornell University, a group of researchers have created a 3D printed sweating robot muscle. By enabling the robot hand to sweat, the muscle can regulate its temperature in the same way that mammals do. The researchers explained that thermal management is essential to allow robots to work over a long period of time without overheating. According to the lead researcher on this project, Rob Shepherd, this form of thermal management is a viable solution thanks to additive manufacturing.
The team’s research, Automatic Perspiration in 3D Printed Hydrogel Actuators, was published in Science Robotics and details the method that enables the robot muscle to sweat. In fact, if the high-torque density motors and exothermic engines that power a robot overheat, the robot will cease to operate. This is even more of an issue with soft robots that are made of synthetic materials. So why not take inspiration from mammals and allow the robot hand to sweat?
One of the research scientists explains: “The ability to perspire is one of the most remarkable features of humans. Sweating takes advantage of evaporated water loss to rapidly dissipate heat and can cool below the ambient environmental temperature. So as is often the case, biology provided an excellent guide for us as engineers.”
3D printed sweating robot muscle
The team of scientists used multimaterial stereolithography, using light to cure the shape of the robot layer by layer. For this, the team had to develop the necessary nanopolymer materials. In fact, they fabricated fingerlike actuators composed of two hydrogel materials that can retain water and respond to temperature. More precisely, the base layer reacts to temperatures over 30°C by shrinking. When this happens, the water is squeezed up into another layer that is perforated with tiny pores. These pores are also sensitive to the same temperature range, therefore they dilate and let the water escape. They close when the temperature falls below 30°C.
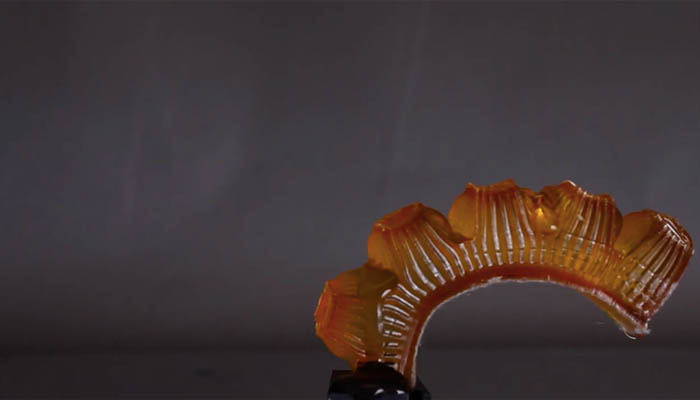
Cornell researchers used 3D printing to create fingerlike actuators that can regulate their temperature through sweating | Credits: Cornell University
The team found that this process was actually three times more efficient than in humans. Co-lead author on the paper, T.J. Wallin explains: “The best part of this synthetic strategy is that the thermal regulatory performance is based on the material itself. We did not need to have sensors or other components to control the sweating rate. When the local temperature rose above the transition, the pores would simply open and close on their own.”
These fingerlike actuators were added to a robot hand that could grab and lift objects. One thing to keep in mind is that these fingers could hinder the robot’s mobility. While the water can make the robot’s hand slippery, modifications to the hydrogel texture could compensate. Another thing to consider is that the robot will need to be supplied in water if it loses it, in the same way as we do. Rob Shepherd added: “I think that the future of making these more biologically analogous materials and robots is going to rely on the material composition.”
The layer by layer process of additive manufacturing was essential to creating these finger actuators. Shepherd concluded: “This brings up a point multidisciplinary research in this area, where really no one group has all the answers.” You can find more information HERE. What do you think of this 3D printed robot hand? Let us know in a comment below or on our Facebook and Twitter pages! Don’t forget to sign up for our free weekly Newsletter, with all the latest news in 3D printing delivered straight to your inbox!