Harvard scientists develop 3D printed shape shift material
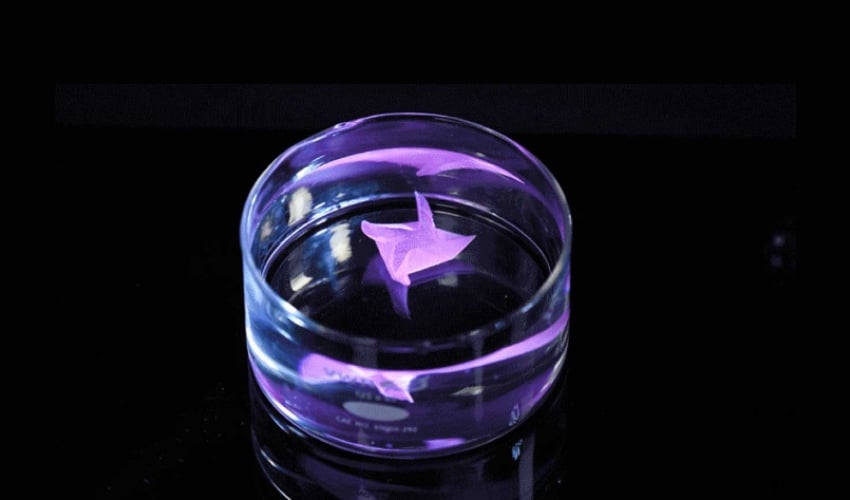
A team of researchers at the Harvard John A. Paulson School of Engineering and Applied Sciences (SEAS) has developed a material that can be 3D printed into any shape and pre-programmed with reversible shape memory. In other words, once a certain stimulus is applied, the fabric will change form back to its original shape. Harvard researchers used keratin from wool to develop the innovative material, which can potentially not only transform the textile industry, but also have an impact on the medical sector, since this 3D printed shape shift material is biocompatible.
The shape shift technology was achieved largely due to the unique properties of keratin, a fibrous protein found in hair, but also in nails, shells, and wool. For their project the researchers extracted keratin from Agora wool, which is commonly used in textile production. But how exactly does it work? When a fiber is stretched – or exposed to a specific stimulus – its spring-like structures uncoil, and the bonds realign to form stable beta-sheets. The fiber remains in that position until it is triggered to coil back into its original shape.
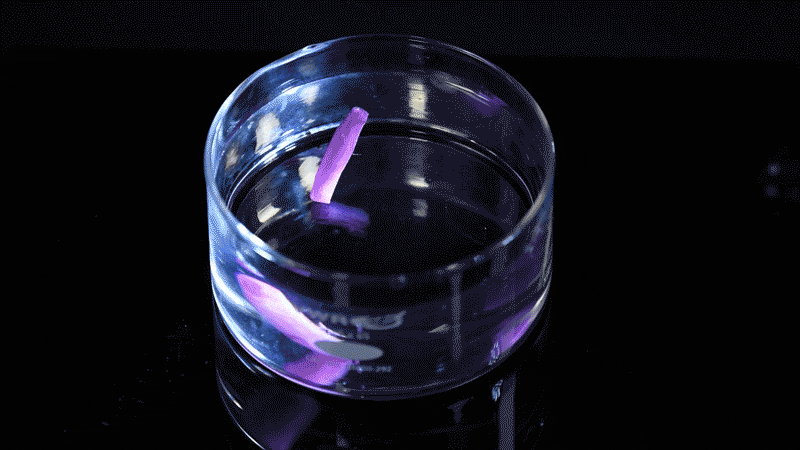
Credits: SEAS
For the demonstration purposes, the Harvard team 3D printed keratin sheets in several different shapes. For instance, one of the 3D printed sheets had a form of an origami star as its permanent shape (the one to which it will return when triggered). Once the material was pre-programmed, the researchers immersed the origami in water, where it unfolded and became ductile. Then, the team rolled the flexible sheet into a tight tube and once it was dry, the sheet was locked in firmly in that position. To reverse the process, they put the tube back into water – can you guess what happened next? The 3D printed fabric unrolled and folded back into an origami star, on its own. That’s how Harvard researchers proved that their 3D printable shape shift technology works.
Kit Parker, Professor of Bioengineering and Applied Physics at SEAS, and senior author of the paper explains, “We have shown that not only can we recycle wool but we can build things out of the recycled wool that have never been imagined before. With recycled keratin protein, we can do just as much, or more, than what has been done by shearing animals and, in doing so, reduce the environmental impact of the textile and fashion industry.”
Parker further added, “Whether you are using fibers like this to make brassieres whose cup size and shape can be customized every day, or you are trying to make actuating textiles for medical therapeutics, the possibilities of our work are broad and exciting. We are continuing to reimagine textiles by using biological molecules as engineering substrates like they have never been used before.”
What do you think about the 3D printable shape shift material developed by Harvard researchers? Let us know in a comment below or on our Facebook and Twitter pages! Sign up for our free weekly Newsletter, all the latest news in 3D printing straight to your inbox!