3D Printed Runners for Hydropower Dams to be Developed by ORNL
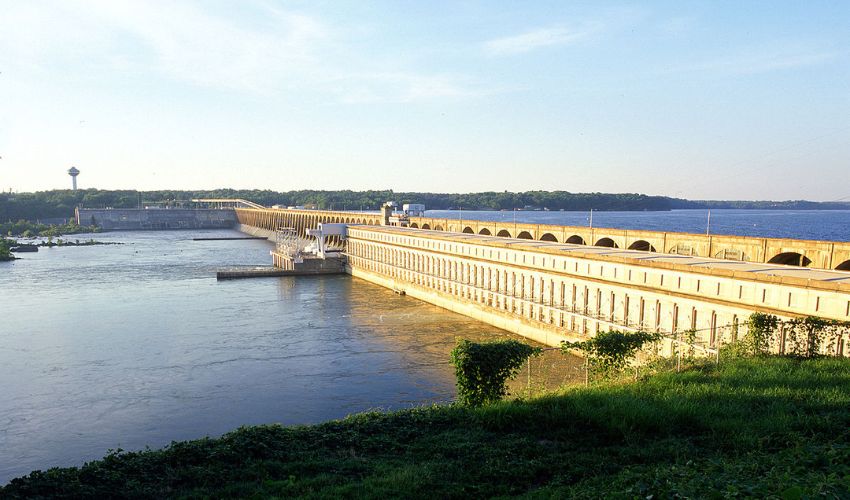
According to the Department of Energy (DOE), hydropower accounts for nearly 27% of utility-scale renewable electricity generation in the United States. A runner, the rotating part of a turbine that turns the energy of falling water into electricity, is key to this technology. However, runners are almost entirely produced overseas; when they fail, it can take years to create and receive replacements. To address this problem, the DOE allocated $15 million to their Oak Ridge National Laboratory so they could develop a system to produce runners themselves. Their project, the Rapid Research on Universal Near Net Shape Fabrication Strategies for Expedited Runner Systems (Rapid RUNNERS), will develop a program combining additive manufacturing and conventional tools to produce runners domestically.
Throughout the three-year project, the Rapid RUNNERS team at ORNL will create the software, hardware, robotics, and manufacturing strategies necessary to produce these large components. The program relies on software that allows six or more robots to work simultaneously, completing tasks like wire arc welding, grinding, metrology, and other functions traditionally done by workers.
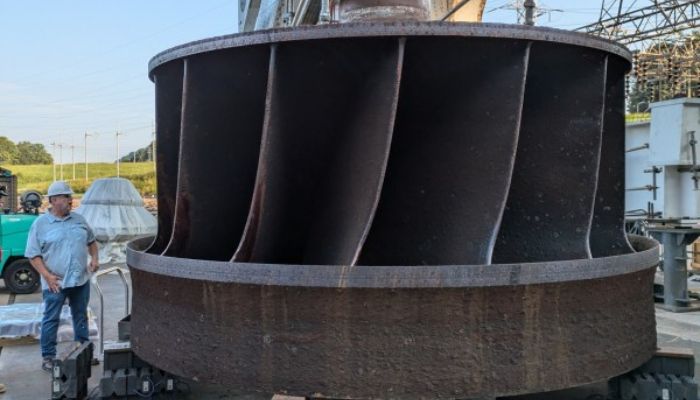
ORNL’s Jay Tiley inspects a hydroelectric runner from TVA’s Cherokee Dam (photo credits: Jim Tobin/ORNL, U.S. Dept. of Energy)
At ORNL, Rapid RUNNERS will produce three runners for hydropower dams, demonstrating their system’s capability. They’ll fabricate the runners using a robotic welder that will deposit metal layer by layer. While the solution used isn’t explicitly noted, the technology clearly falls under Directed Energy Deposition, DED. This AM strategy will quickly create metal parts that are close to the desired final dimensions, known as near-net-shape. Traditional machining techniques will then be used for post-processing in a way that is more time and materially-efficient than existing procedures.
Adam Stevens, an R&D staff member at ORNL and technical lead for the project, said that “right now, it takes around 18 months to produce one of these. If you can’t operate a hydropower turbine because you’re waiting for a part, that’s 18 months of clean energy you’re not generating. This approach can fill the gap in the domestic industrial base.”
The three runners that ORNL is producing will be Francis-style turbines, a particular style of large stainless-steel runner. The first will be a prototype and the second will potentially be installed in the Tennessee Valley Authority’s (TVA) Ocoee Dam in Parksville, Tennessee. The Ocoee Dam has five generating units that produce 24 megawatts of electricity, and the runner for this dam will be five feet in diameter.
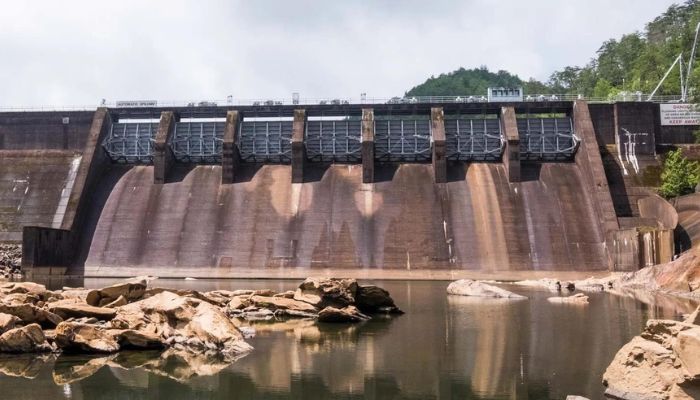
The Rapid RUNNERS team is manufacturing a runner for the Ocoee Dam in Tennessee, pictured here (photo credits: Ocoee Adventure Center)
By contrast, the third runner produced by ORNL will be for the TVA’s Wilson Dam which has 21 generating units producing 653 megawatts of electricity. This runner will be 15 feet in diameter, 8 feet high, and weigh more than 46 tons. Additive manufacturing is ideal for creating such a large-scale piece because it can work faster across large shapes than any individual system. According to scientists at the ORNL, the approach could greatly reduce waiting times for critical components and enable economic growth in the manufacturing sector for energy.
Additive manufacturing has been employed for hydropower projects before, but the Rapid RUNNERS program could revolutionize the industry in the United States. ORNL’s Stevens said that “this has the potential to transform forging and casting of large-scale metal components.” The platform developed by Rapid RUNNERS, Stevens added, “will allow for domestic production of infrastructure-scale net-shape components for energy, defense, shipbuilding, hydropower, and municipal water supply – any industry that requires a large piece of metal could benefit from this.” To learn more about Rapid RUNNERS, click here.
What do you think about incorporating additive manufacturing into hydropower? Let us know in a comment below or on our LinkedIn, Facebook, and Twitter pages! Don’t forget to sign up for our free weekly newsletter here for the latest 3D printing news straight to your inbox! You can also find all our videos on our YouTube channel.