3D printed porous scaffold structures can promote bone growth in patients
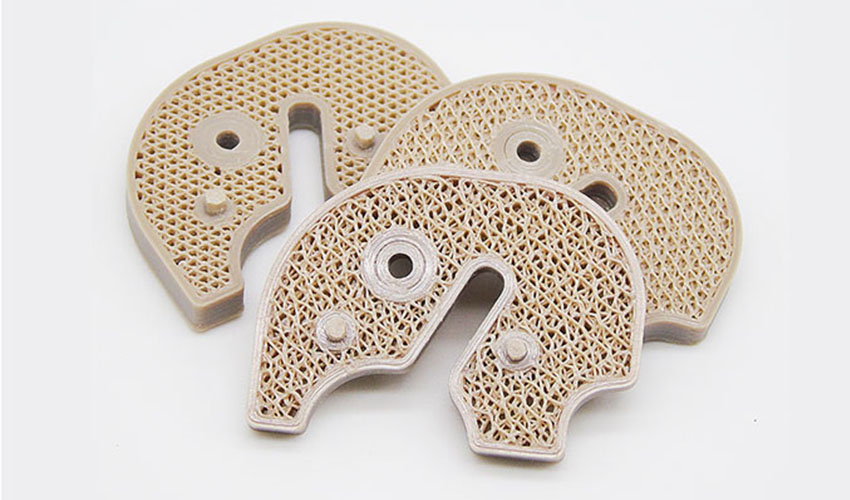
The startup FossiLabs, based in the U.S., develops FDM 3D printers capable of producing medical implants made from PEEK. These high-performance implants resemble bone-like structures and can promote bone growth in patients with musculoskeletal disorders. Combining the properties of PEEK with a 3D printing solution that can engineer porous structures is the innovative idea behind FossiLabs. In order to learn more about the company and how it is aiming to offer new solutions for the medical sector, we met Todd Reith, the Founder of the company. So, can 3D printed porous scaffold be a viable solution for musculoskeletal disorders?
3DN: Can you tell us more about yourself and your relationship with 3D printing?
I am a true entrepreneur who, over time, has become an expert in multiple disciplines. I started out in software development, creating some of the first online web banking applications, pharmaceutical database applications, and early artificial intelligence (AI) logic for target marketing applications. I then focused on designing headless guitars with high-tech carbon fiber components and custom electronics, including piezo sensors. The guitar business evolved to designing and manufacturing custom mother of peal inlay designs for other guitar manufactures and their respective artist instruments. My manufacturing path lead me to developing metal components and eventually machining fuel and shock components for Team Penske’s Indy Car Racing Team. Eventually I became involved with medical device implants.
I initially had no interest with 3D printing. It was just a toy that made useless plastic trinkets. By random chance, a co-worker asked me to help him troubleshoot and fix his 3D printer. Frustrated with the poorly made piece of equipment and software interface, I stated to my co-worker, I could make a better machine. I was sucked into the craze of additive machining. I obsessively researched and absorbed all the information I could find. Three months later, I built my first high-temperature 3D printer. After 3 distinctly different businesses, FossiLabs, ties in all my past acquired skills. It is very exciting to be able to use all the disciplines I have perfected over the past 20+ years.
3DN: What is FossiLabs’ mission? And how did the company come about?
FossiLabs’ mission is to engineer bone-like structures to improve the lives of patients with musculoskeletal disorders. The goal is to speed recovery by encouraging cell growth where traditional methods may have prolonged the healing process. FossiLabs drives to innovate, contribute, and advance forward with novel ideas.
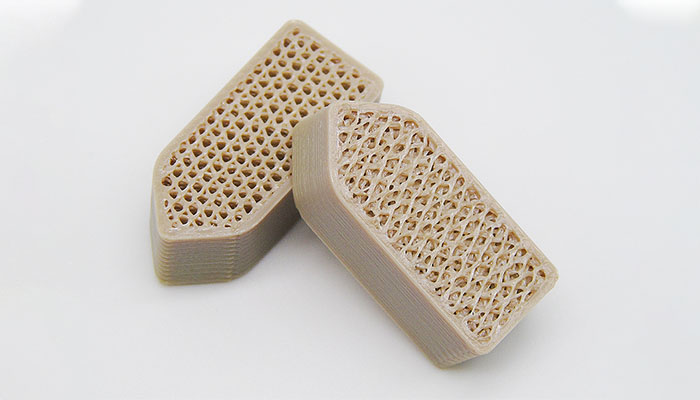
Bone-Foam and Bone-Mesh porous scaffold structures is FossiLabs’ vision | Credits: FossiLabs
FossiLabs initially started with the lofty desire to 3D print PEEK traditional static implants. After successfully engineering and building a working machine that could print PEEK filament, we printed our first static cervical spacer. We showed it off proudly during a sales pitch. Everyone was excited in the meeting. After the excitement settled down, the potential client stated “Why would we buy a 3D printed spacer, when we can machine the same thing from solid rod material?” Reality sunk in that we needed a game changer. We needed to disrupt the market and engineer something that could not be machined. We had to bring value to market. The concept of Bone-Foam and Bone-Mesh porous scaffold structures became our vision.
3DN: What are the main benefits of PEEK for the medical sector?
PEEK (polyether ether ketone) is an amazing polymer. PEEK is an advanced biomaterial, which has excellent mechanical and chemical properties that can be maintained at very high temperatures. Although within the body, the temperature limits would never be tested, PEEK is near transparent with advanced imaging and its natural elasticity corresponds very closely with natural bone. PEEK is also stable in the body for long periods of time, has low thermal conductivity, lightweight, and easy to sterilize. We currently use Evonik’s VESTAKEEP i4G FDA approved FFF filament.
3DN: Can you tell us more about your technology?
FossiLabs has developed a set of proprietary processes that allow us to manipulate a 3D model of a medical implant device to identify areas where bone in-growth and on-growth is desired. We can define solids, bone-mesh and bone-foam regions. The controlled macroporosity scaffolding structures within the implantable device, and hydroxyapatite (HA) nanocoating, provide unparalleled hydrophilicity and faster osseointegration. The combination of the PEEK scaffolding and HA nanocoating potentially would eliminate the need for biologics pressed in a traditional graft window during surgery. The implant could be taken directly out of sterile packaging and immediately into the patient’s body, thus simplifying the procedure and reducing the chances of infection.
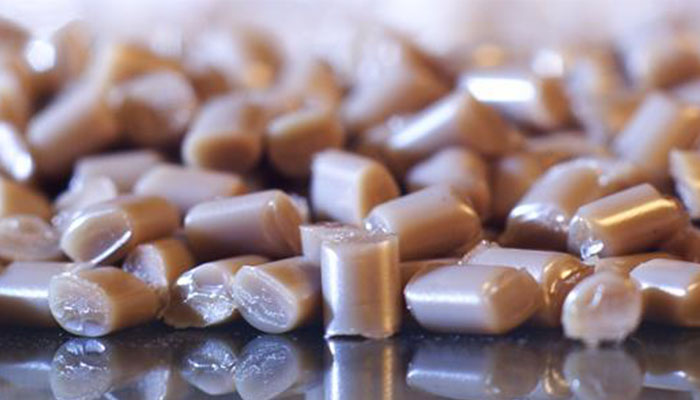
FossiLabs uses PEEK filaments manufactured by Evonik. Before being turned into filament, PEEK is in the form of pellets | Credits: Evonik
3DN: How do you see the future of 3D printed implants?
This is just the beginning. There are many different 3D printing technologies that are gaining momentum. It is a very exciting time to see all of these technologies move at hyper speed. Some interesting advances include bioceramic Sr-HT-Gahnite applications, patient specific implants, and 3D printed tissues and organs.
3DN: Any last words for our readers?
Stay tuned, more to come!
What do you think of FossiLabs’ use of additive manufacturing to offer medical implants that promote bone growth? Let us know in a comment below or on our Facebook and Twitter pages! Sign up for our free weekly Newsletter, all the latest news in 3D printing straight to your inbox!