Ford and EOS develop high security 3D printed locking wheel nuts
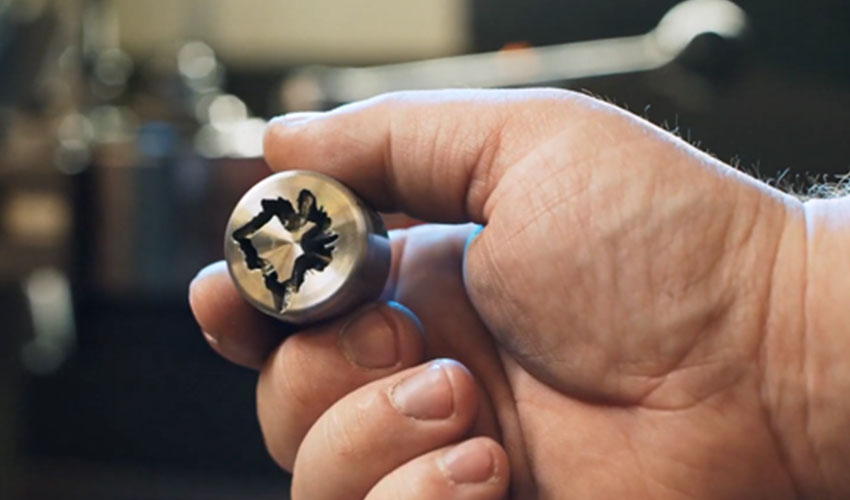
About a year ago, Ford had produced what they claim to be the largest automotive 3D printed part in history. Their additively manufactured aluminium intake manifold was installed in the Hoonitruck, a 1977 Ford F-150 with a twin-turbo 3.5-litre V6 EcoBoost engine owned by Ken Block, star of popular YouTube series, Gymkhana. More recently, the car manufacturer partnered with leading 3D printing manufacturer EOS to create unique 3D printed locking wheel nuts that will prevent wheel and tire thefts.
These are not any locking wheel nuts. In fact, they are made using a unique biometric signature based on the car owner’s recorded voice. Just like some systems will use biometric identification based on fingerprints or iris scan, recording the voice of the driver can be used to create a completely unique design. Engineers record the voice of the driver and then use software to convert the soundwaves into a pattern that can be 3D printed on the locking nut. The nut and key are designed as a single piece and 3D printed using acid and corrosion-resistant stainless steel. Later, they are separated and ready for use after a small amount of finishing.
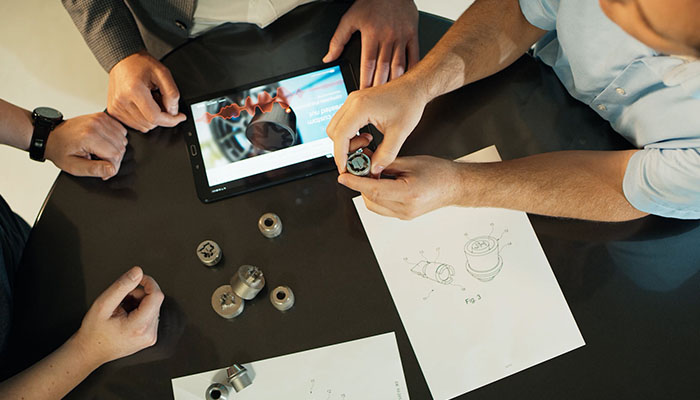
The nut and key are 3D printed as a single piece using stainless steel | Credits: Ford Motor Co.
“Some alloy wheels can cost thousands to replace, but these unique rim nuts will stop thieves in their tracks. Making wheels more secure and offering more product personalization are further proof that 3D printing is a game-changer for car production,” commented Raphael Koch, Research Engineer for Advanced Materials and Processes at Ford.
According to specialists, locking wheel nut removal tools have become more accessible, which has resulted in alloy wheels becoming a target for thieves. Standard equipment cannot work on this new type of locking wheel nut design. In addition to being completely unique to each driver, Ford has put in place another security system to avoid a thief from making a wax imprint of the pattern. This is why components feature unevenly spaced ribs inside the nut as well as widening indentations.
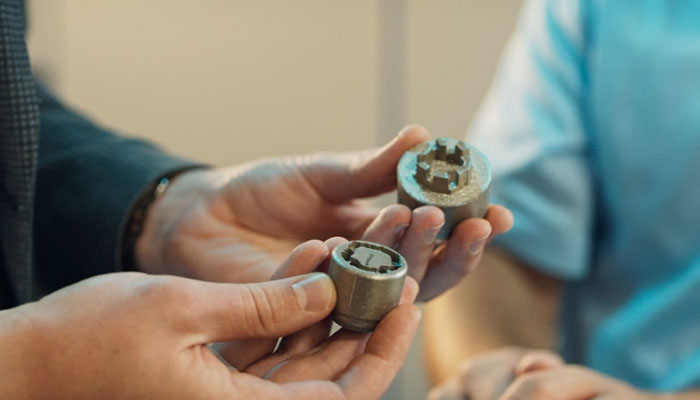
The 3D printed locking wheel nuts | Credits: Ford Motor Co.
Ford worked with EOS, using their M 290 3D printer, based on Direct Metal Laser Sintering. These 3D printed components can be made in five days, a significant reduction from the previous eight-week turn-around. Additive manufacturing can truly offer a new level of customization for parts, increasing safety at a reasonable cost. It would be very expensive, if not impossible, to introduce such a system using traditional manufacturing methods.
This concept is somewhat similar to Stealth Key, manufactured by UrbanAlps. These 3D printed keys have internal structures that are impossible to copy, offering more security. Will additive manufacturing become the norm for producing more secure components? Let us know what you think in a comment below or on our Facebook and Twitter pages! Sign up for our free weekly Newsletter, all the latest news in 3D printing straight to your inbox!