Researchers develop 3D printable material that mimics biological tissues

At the University of Colorado Denver, researchers have developed a method to create 3D printed liquid crystal elastomers with complex structures. The aim of this research is to build structures that match the physical properties of complex biological tissues, such as cartilage. Over the years, researchers around the world have been exploring the potential of 3D printing technologies for patient treatments and therapies. One of the main benefits of additive manufacturing is the level of complexity that can be achieved for a given structure. In this case, the researchers hope that the technique will help with creating patient-specific implants to replace tissues that have been lost because of injury or disease.
Given that tissues have unique properties, such as flexibility and strength, they are difficult to emulate when using synthetic substances. Tissues such as cartilage are extremely hard wearing, yet still soft and flexible enough to allow for movement and cushioning. For example, the spine’s components are strong and flexible enough to protect delicate neural tissue. Chris Yakacki, researcher involved in the study commented: “The spine is full of challenges and it’s a hard problem to solve. People have tried making synthetic spinal tissue discs and they haven’t done a good job of it.”
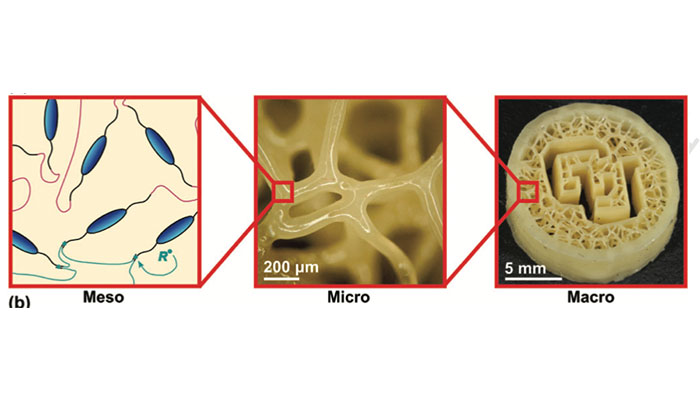
The structure at different scales | Image via CU Denver News
3D printed liquid crystal elastomers
In the study published in Advanced Materials, the team of researchers explain that they used liquid crystal elastomers to create complex structures that imitate biological tissue. More precisely, they used DLP 3D printing technology. DLP is similar to SLA in the sense that it also relies on photopolymerization to create an object layer by layer using ultraviolet light. The technology enables a high degree of precision, which is key for structures that will enter the body such as this one. During printing, the researchers used a photocurable (thus DLP printable) main-chain liquid crystal elastomer (LCE) resin. They explain that this resin showed “12 times greater rate-dependence and up to 27 times greater strain-energy dissipation compared to those printed from a commercially available photocurable elastomer resin,” after carrying out some mechanical tests.
Therefore, the material seems to have significant shock-absorbing qualities, which makes it highly suited for dynamic joints or protective structures in the body. Chris Yakacki added: “Everyone’s heard of liquid crystals because you stare at them in your phone display. And you’ve likely heard of liquid crystal polymers because that’s exactly what Kevlar is. Our challenge was to get them into soft polymers, like elastomers, to use them as shock absorbers.” A higher degree of complexity also means that the structure can be personalized and completely adapted to a patient’s body – a key difference between conventional methods that do not offer this level of customization. Therefore, the final product that mimics the natural structure of cartilage will also be able to match a person’s anatomy perfectly.
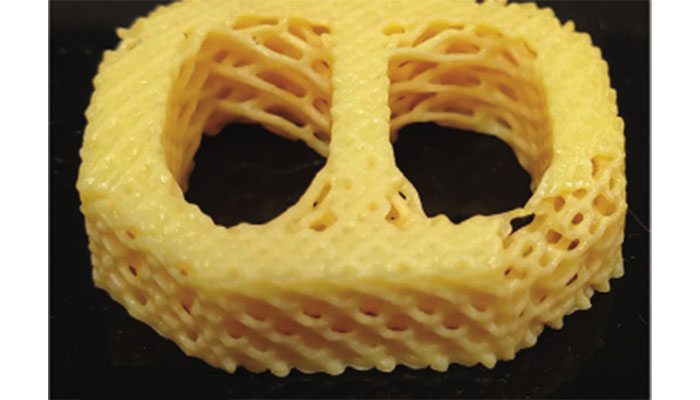
Image via CU Denver News
You can find more information about the study HERE. What do you think of using 3D printing technologies to replace cartilage? Let us know in a comment below or on our Facebook and Twitter pages! Sign up for our free weekly Newsletter, all the latest news in 3D printing straight to your inbox!