3D Printed Infant Masks Are a Success Story for Silicone in the Medical Sector
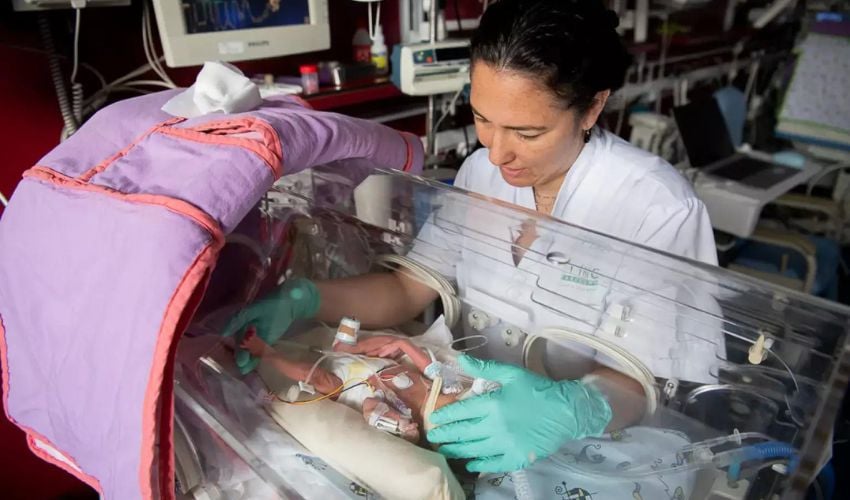
The use of additive manufacturing for the production of medical devices has increased rapidly in recent years. While the global market for 3D printing in healthcare reached a volume of $2 billion in 2021, it will double by 2026 to around $4 billion, according to forecasts by Global Data. Along with this rapid growth, the possibilities of the applications are increasing, as well as the demands on the materials used. Due to the diversity of applications of medical 3D printing in the various fields of orthopedics, dentistry, surgery, etc., a wide variety of materials are used, which must meet medical requirements while also having the ability to be processed for 3D printing. One material that is increasing in medical use is silicone.
Silicone in particular has a number of properties that are valuable in the medical field. The rising silicone AM market underscores the trend of increased demand across the industries. In 2021, the total market value was estimated at $1.5 billion and is expected to register a compound annual growth rate of 19.9% through 2028. As mentioned earlier, this advance can also be seen in its increased use in medical applications. Silicone is biocompatible, UV-resistant, thermally stable, it can be sterilized, and it is easily customizable to different individuals through 3D printing. For example, the company Elkem Silicones and the Hospital Clínic of the University of Barcelona are working on a proof-of-concept project, using 3D-printed silicone medical respiratory masks to treat premature infants.
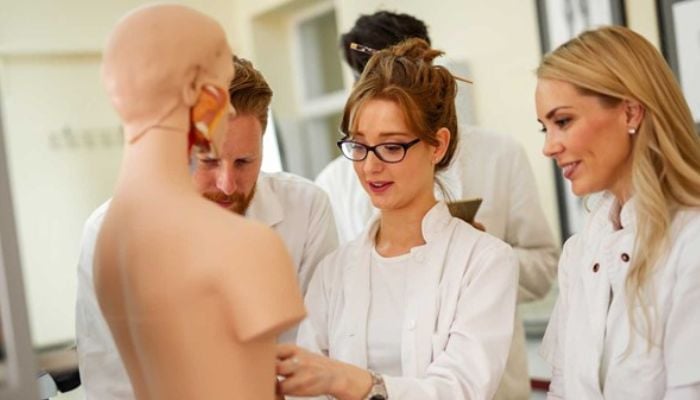
Silicone 3D printing is taking on an increasingly important role in medicine. (Image: Elkem)
Around 70% of premature babies require respiratory support. Non-invasive ventilation techniques such as a CPAP (Continuous Positive Airway Pressure) device, which delivers air pressure to a connected mask through a tube, are often used. These masks, however, are not ideal for babies because their faces are smaller and shaped differently than those of adults. What’s more, due to the rapid growth of infants, they also need new masks on a regular basis. 3D printing offers the advantage here that the masks can be customized and also regularly reprinted. 3D printing makes it possible to print cavities, unconventional geometries, and the ability to change designs iteratively. One crucial point why Elkem Silicones and Hospital Clínic Barcelona are turning to 3D-printed silicone masks is that despite their wide range of manufacturers, sizes and shapes, traditionally manufactured generic medical products cannot fit everyone.
A second point is that these ill-fitting medical devices can sometimes cause injuries such as pressure sores, scarring and hair loss. The sores can even become infected if the medical device – in this case, the mask – is not properly cleaned. Custom-made medical devices, on the other hand, fit more comfortably and better suit a patient in both the short- and long-term. Karsten Schlichter, global business development manager at Elkem Silicones, comments, “It isn’t just the mask. It’s also the way you put the mask on the baby,” further explaining, “Allowing the mask to remain on the baby without the straps pushing it down and putting pressure on the skin and on the head.”
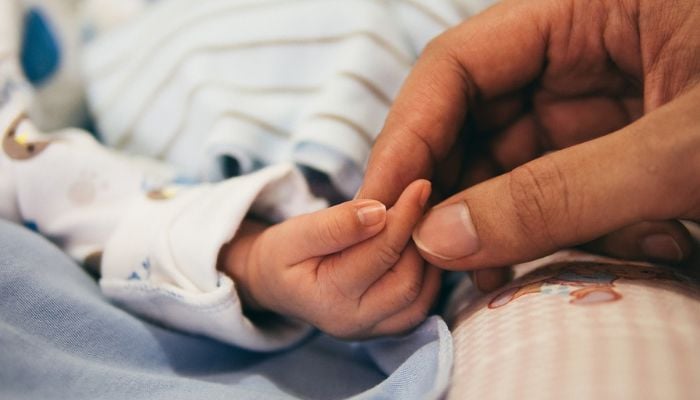
Around 70% of premature babies need a mask. Standard masks are not tailored to their needs. Medical-grade silicone masks from 3D printers could help. (Image: Pixabay)
In addition to customization through 3D printing, the printed material also plays a crucial role. The main element in baby masks is the material, namely hypoallergenic silicone. Silicone allows for comfort on the face and unlike a hard, stiff material, it does not leave scars on babies’ skin. “With silicone, you can have many formulations,” Schlichter says. “You can adjust to the final use and comfort level for the patient. The mask is on the face of the patient, but at the same time, the mask must be connected to oxygen. The mask also has to have some mechanical properties to allow the tube to go into the mask correctly with no leakage.” The mask therefore combines soft material for the face with harder, stiffer material for the ports. Both can be printed in one process using 3D printing. In addition, silicone holds a number of properties that are desirable in medical products, Schlichter elaborates: “Silicones have now become maybe the best material for elastomer parts in medical applications. That’s due to the properties of silicone, such as biocompatibility and chemical inertness.”
Although the proof-of-concept project on silicone masks for premature infants which started in August 2022 has not yet been fully completed, some results have already been achieved. Mannequin tests showed a 14% reduction in leakage. In addition, the mask led to greater comfort, which prevented scarring, ulcers and infections. Schlichter interprets these results extremely positively and is optimistic about the development of additive manufacturing and the role silicone will play in it, “We see silicones as a real, novel material for 3D printing, with all the applications that silicones have in their variety, from medical to industrial applications. Going forward, we are working on several technologies that will allow us to open up the space even wider for silicones in 3D printing.” To learn more about how this technology is helping the medical field, click HERE.
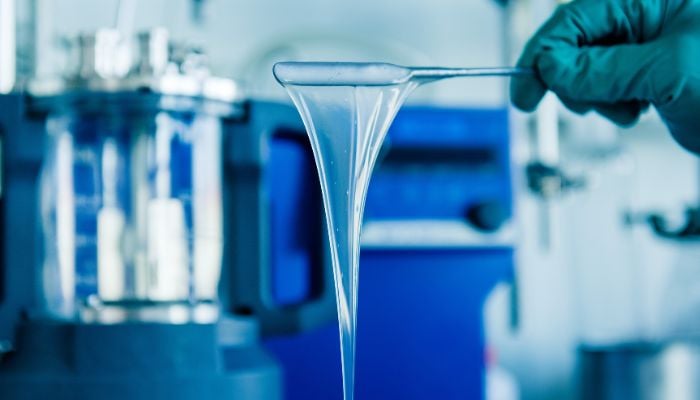
Elkem is focusing on the production of silicones for additive manufacturing. (Image: Elkem)
What do you think about 3D printed silicone technology helping newborns? Let us know in a comment below or on our LinkedIn, Facebook, and Twitter pages! Don’t forget to sign up for our free weekly Newsletter here, the latest 3D printing news straight to your inbox! You can also find all our videos on our YouTube channel.
*Cover photo credits: Hospital Clínic Barcelona