Researchers 3D Print Headlight Lenses, Overcoming Manufacturing Challenges
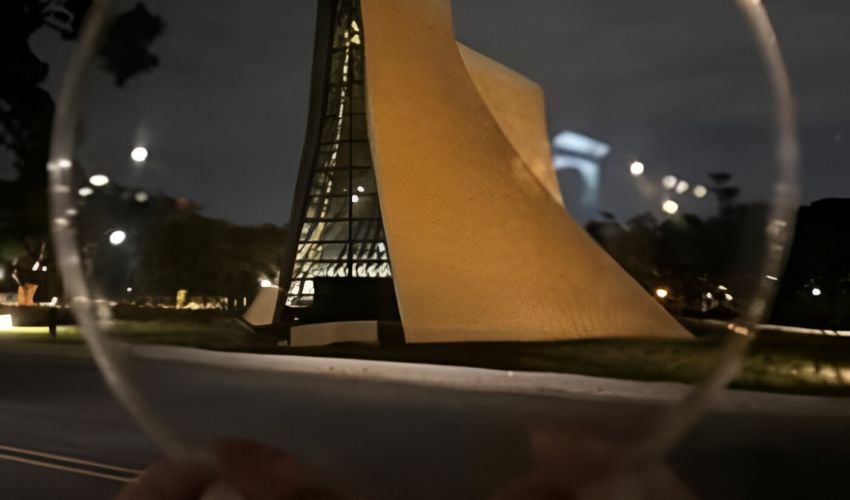
One of the best ways to understand 3D printing’s value is by explicitly comparing its effectiveness versus CNC machining and reverse engineering. Such is the case in a study conducted by Taiwan’s Tunghai University, where researchers discovered that, for headlight lenses, 3D printing allowed for more flexibility and greater performance than the latter traditional technologies. The automotive sector often employs additive manufacturing (AM) because the technology is valued for producing topology- and weight-optimized parts, custom components, prototypes and small series productions. 3D printed headlight lenses, however, are not common in the industry.
Why turn to AM for headlight lenses? First, it is necessary to understand what headlight lenses achieve. Headlight lenses are critical to a car’s lighting system because they ensure light is evenly transmitted across the road, promoting safe driving in the dark. The lenses also protect the bulbs from environmental elements like dust, debris, snow and rain. The parts offer an opportunity for customization too, because a unique lens can add an aesthetic component to a vehicle.
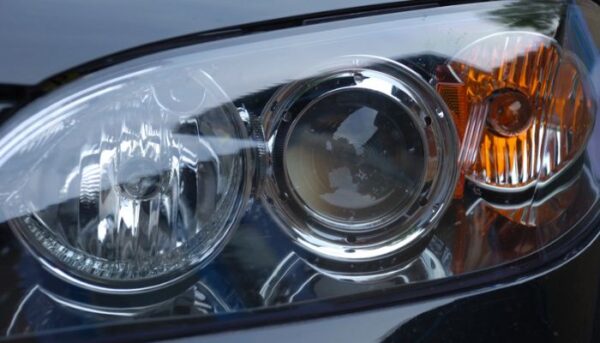
Traditional headlight lens
Traditionally, headlights have been mass-produced with a focus on consistent quality, but as the automotive industry evolves, the market is desiring more diverse products that meet unique needs. But, this shift towards more personalized solutions is difficult for mass production to adapt to, because the expense of traditional lens molds requires careful evaluation of the financial risks and benefits before committing to production, creating a longer decision-making process.
Research team leader Chia-Hung Yeh explained, “Moreover, as product designs become more complex, mold design and manufacturing processes are also becoming more intricate, which slows production speeds. To stay competitive in a rapidly changing market, manufacturing design capabilities must meet these demands quickly.”
Comparing the Processes
The test involved producing 14 headlight lenses in one eight-hour print cycle, along with CNC-machined lenses and reverse-engineered lenses. The researchers then measured key properties of the lenses, including light transmittance, surface profile, radius of curvature, diameter, height and surface roughness. The results? The 3D printed lens had a minimal curvature radius error, exceptional surface roughness and a transmittance of 93 percent. These results were on par with the CNC-machined sample, which had a 94 percent transmittance, and the two types of reverse-engineered lenses (91 and 94 perfect), exceeding the 90 percent transmittance of a commercially available polycarbonate lens.
Not only could the 3D printed version stand up against the traditionally manufactured versions, but the resin used cost about $30, demonstrating cost-effectiveness. According to the report, the research showed that 3D printing was suitable for making prototypes, improving operational efficiency and shortening production times. The study’s language regarding 3D printing was overwhelmingly positive, with the last line of its abstract reading: “In cases where customization is required, 3D printing unquestionably outperforms conventional manufacturing methods.”
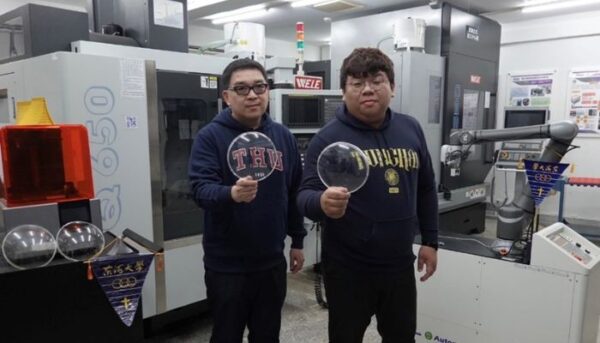
The research, led by PI Chia-Hung Yeh (left) and doctoral candidate Wei-Min Chen (right), was conducted at the Digital Design Engineering Laboratory, Department of Industrial Engineering and Enterprise Information, Tunghai University. (Photo Credit: Chia-Hung Yeh, Tunghai University)
Wei-Min Chen, a doctoral candidate who helped lead the research with Yeh, explained: “3D-printing technology holds significant promise for producing optical components by allowing rapid prototyping of product designs, enabling designers and engineers to quickly validate the aesthetic, structural and functional aspects of their creations. Additionally, it makes it possible to bring intricate and innovative designs to life, shortening the development cycle for new vehicle models and boosting overall market competitiveness.”
Going forward, the researchers plan to investigate specific headlamp module configurations and assess internal factors, like fixture temperature, operating environment and structural design. Through this evaluation, they aim to ensure that the findings can applied effectively to practical applications. To learn more, read the press release HERE.
What do you think of 3D printing headlight lenses? Let us know in a comment below or on our LinkedIn, Facebook, and Twitter pages! Don’t forget to sign up for our free weekly newsletter here, the latest 3D printing news straight to your inbox! You can also find all our videos on our YouTube channel. For more on additive manufacturing in the automotive sector, click here.
*Cover image: The Luce Memorial Chapel in Taichung, Taiwan viewed through one of the 3D printed headlight lenses. Photo credit: Chia-Hung Yeh, Tunghai University