3D printed bone implants thanks to plasma injection

Researchers at the German Fraunhofer Institute has announced a new technique for the development of 3D printed bone implants. It involves injecting plasma into the implant, thereby promoting cell growth inside and outside the implant which should allow the natural recovery of the bone.
The link between additive manufacturing and medicine has for some time been quite solid, with many applications developing and particularly around bio-printing. Research at the University of Arizona are working on 3D printing to better treat fractures. Through stem cells and 3D technologies scientists involved want to find a more effective way to treat these injuries. This time, German researchers are interested in plasma and additive manufacturing, also with the aim of healing a defective bone.
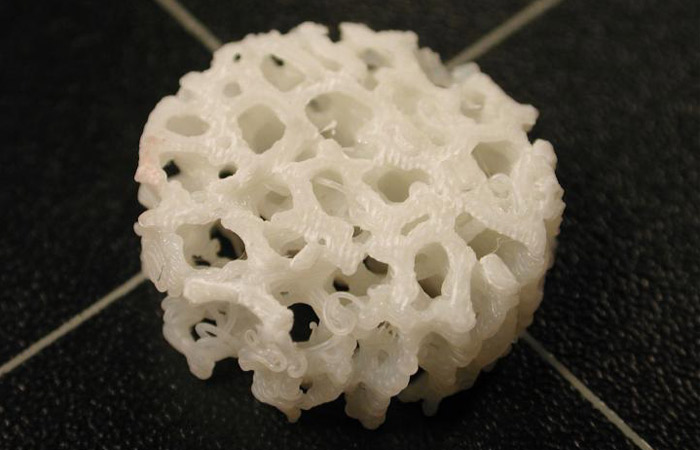
Scaffolding printed in 3D by the University of Arizona
How to develop 3D printed bone implants?
To create these 3D printed bone implants, a cold plasma jet is injected between each layer of copolymer. Thus forming the structure of the implant which is actually a scaffold that will dissolve over time. This plasma jet makes it possible to place aminopenicillins which are antibiotics with bone diffusion. These then come to mix with the 3D printed structure, forcing the bone cells to find a suitable substrate for their adhesion.
The researchers say that the implant is molded directly into the patient’s bone and does not require any chemical treatment, thus respecting its stability. The design of each implant is personalized and allows a perfect fit for every need. “Our goal is for the bone cells to grow into the synthetic structure as quickly as possible and finally replacing the implant which is broken down gradually by the body’s own enzymes,” said Dr. Jochen Borris, Head of the Life Science and Ecology business unit at Fraunhofer IST.
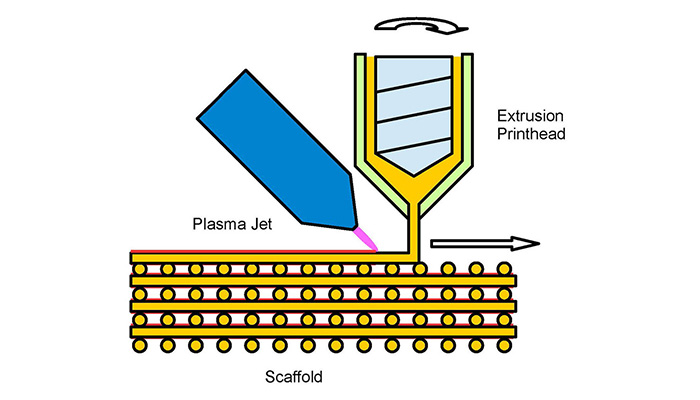
Bone implant manufacturing technique
After placing 3D bone implants, doctors can control the density of 3D printed media and the filling of each. Those that are sealed give greater stability to each of the implants. Dr Thomas Neubert, Project Manager for the EU at Fraunhofer IST concludes: “Like natural bones, implants can now have areas with different strengths,“
What are the next steps ?
According to the Institute, the project is still in the development phase. Since it is still in the laboratory test phase, the next step is to evolve the technique and its application uses. “The innovative technique offers a lot of potential for adapting bone implants very precisely to the individual needs of patients. With our method, we’re able to control the shape, porosity, mechanical stability and biomechanical characteristics well and vary them within the implants. This means that we can produce areas with different strengths or porosities, which can also be coated with various functional groups.” said Dr. Borris.
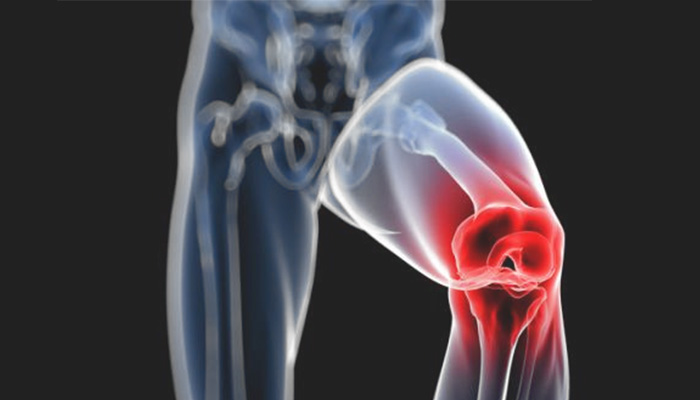
This method could be very useful for treating serious fractures
The doctors behind this development said that the technique was particularly interesting for patients with cancer or serious fractures. The goal is for doctors to develop 3D printed bone implants for every patient who needs them. The project is currently seeking industrial partners, suggesting that there are still a few years left before seeing these implants in hospitals. You can find more information in the press release HERE .
What do you think of this method of manufacturing bone implants printed in 3D? Let us know what you think in a comment below or on our Facebook and Twitter pages! Don’t forget to sign up for our free weekly Newsletter, with all the latest news in 3D printing delivered straight to your inbox!