University of Maine creates the world’s largest 3D printed boat
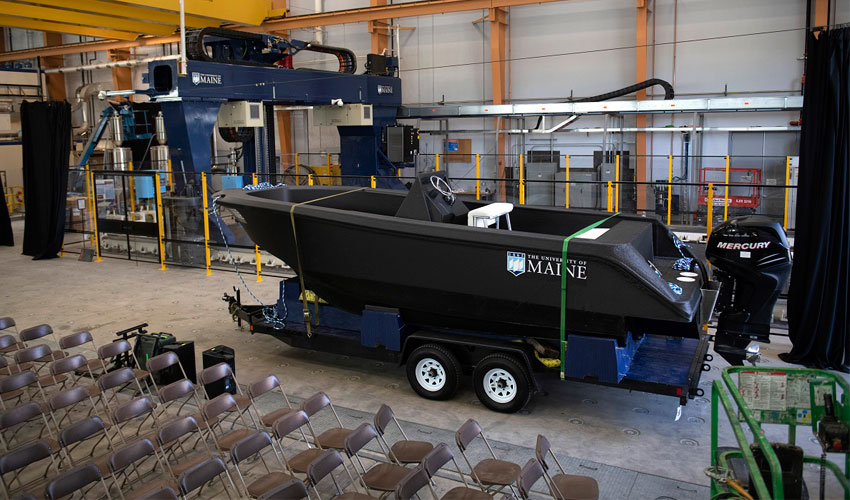
A team of researchers from the University of Maine revealed the largest 3D printed part in the world. It is a boat, the 3Dirigo, designed on a large-format polymer 3D printer developed by the UMaine Advanced Structures and Composites Center. The piece is 7.62 meters long and weighs 2.2 tons! The project teams were awarded 3 World Records: the largest 3D printed solid part, the largest 3D printed boat and finally the largest 3D printer. This is a promising initiative for the maritime sector, which take advantage of the benefits of additive manufacturing.
More and more additive manufacturers are turning to large-format 3D printing, hoping to create large structures in one go and avoid assembly or post-processing steps that are expensive and time-consuming. The University of Maine is therefore joining this trend, with an emphasis on the use of composite materials. Last May, its partner the Oak Ridge National Laboratory (ORNL) received $20 million to develop a large-format additive manufacturing program based on 3D printing materials that contained wood fiber. The 3D printing of the boat is therefore a significant step forward in this government-supported project.
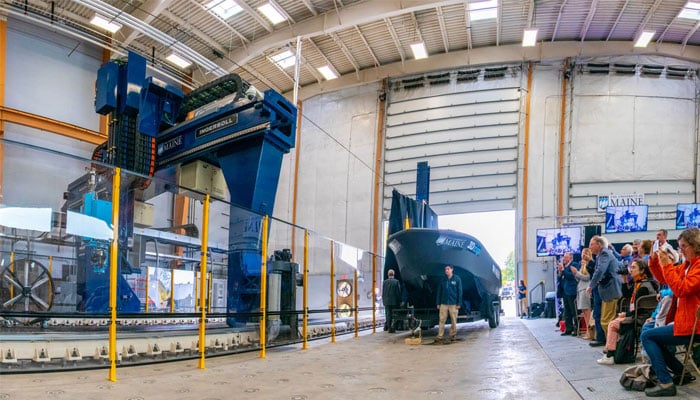
The large-format 3D printer, next to the 3D printed boat | Image via UMaine
3D Printed Boat: The Manufacturing Process
The UMaine teams worked with Ingersoll Machine Tools to develop their 3D printer, it presents a printing volume of 30 x 6.70 x 3 meters (length, width and height) and a speed of 227 kilos per hour. The print head is fixed on a gantry mounted on rails, making it easier to move along the length. As of today, the manufacturer is not offering a wide-range of compatible materials, however the machine was designed to use raw materials of biological origin, in particular cellulose from wood. Apparently, the 3D printer was designed for rapid prototyping applications for civil, defence and infrastructure applications.
In order to demonstrate the capabilities of their large format 3D printer, the teams created the 3D printed boat 3Dirigo. It was manufactured in just 72 hours from a mixture of plastic and wood cellulose. The part is 7.62 meters long and weighs 2.2 tons, making it the largest solid structure ever 3D printed.
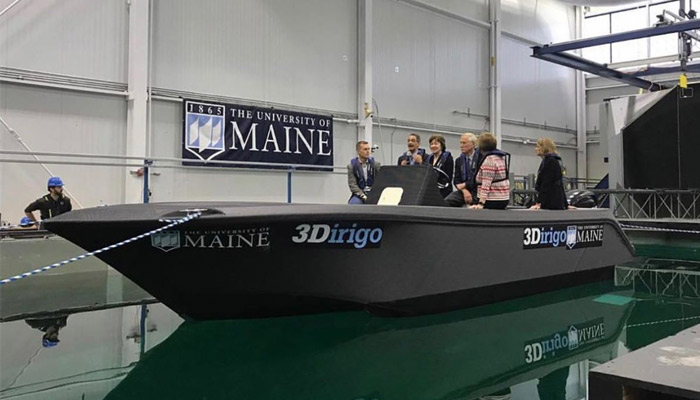
The boat has been tested by the Alfond W2 Ocean Engineering Laboratory test site
Other Projects
The University of Maine took the opportunity to present a second project, a 3.6-metre long 3D printed communication shelter for the US military. The university worked in collaboration with the Combat Capabilities Development Command (CCDC), a branch of the army that consists of rapidly deploying shelter systems for soldiers. Col. Frank Moore, Military Assistant at CCDC Soldier Center, explains: “The innovation that we have witnessed here at the University of Maine will revolutionize how the Army prototypes and manufactures shelters, vehicles and other large systems. The lighter yet stronger 3D printed systems will advance the state of the art in additive manufacturing, forging the future of expeditionary equipment IAW with the Army’s new policy on advanced manufacturing.”
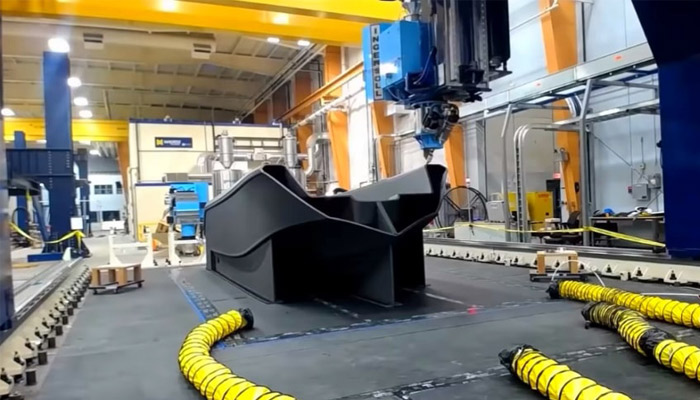
The boat took 72 hours to be 3D printed
The machine is also expected to meet the needs of rapidly deployable and logistically weak infrastructure systems. With this in mind, the teams printed a 2.2-ton, 6.4-metre-long 3D mold to make a 23-metre-long bridge girder. The bridge is expected to be built in Hampden, Maine, in the summer of 2020. Habib Dagher, Executive Director of the UMaine Advanced Structures and Composites Center concludes: “We are truly honored to be working with leaders from the Maine boatbuilding industry, Maine Forest Products Industry, the national construction industry, Maine Technology Institute, Oak Ridge National Laboratory, the U.S. Dept of Energy Advanced Manufacturing Office, the U.S. Office of Naval Research, the U.S. Army, and the U.S. Army Corps of Engineers. With this large printer, we will be able to accelerate innovation and prototype development in both the civilian and military sectors.” Find more information HERE.
What do you think of these achievements coming from the University of Maine? Let us know in a comment below or on our Facebook and Twitter pages! Sign up for our free weekly Newsletter, all the latest news in 3D printing straight to your inbox!
Very nice job! 6 Craftsmanship at its finest and I am looking forward to seeing more of your workmanship
I know this article was from a while ago but just came across it. I wonder what has happened since. Also a bit vague on the plastic used, a lot of plastics don’t do that well in the environment UV degradation, water absorption and the alike.