New Metal 3D Printed Abutment Solution to Fight Oral Infectious Diseases
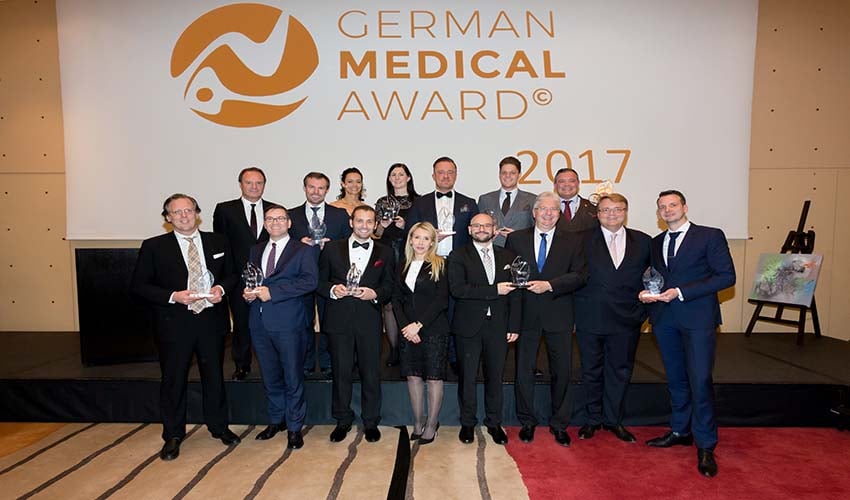
Oral implantologist, researcher and inventor Dr. Mario Kern has developed the Extended Anatomic Platform (EAP), a patented process for creating metal 3D printed dental abutments. An abutment is used as a connecting element for bridges, dentures and implants. The platform has been designed in such a way that it should counter the growing presence of peri-implantitus, an infectious disease that causes the soft tissue around the implant to recede, making the metal abutment visible. This is just one more application which demonstrates that the dental additive manufacturing sector is growing rapidly.
Revolutionising dental implant prosthetics
To counter the issue of metal abutments showing, dental technicians typically use ceramic abutments to cover the exposed metal. However, this is not a permanent solution as the ceramic is not sturdy enough and can become loose over time. Therefore, the EAP process was created with these issues in mind and produces more biocompatible abutments with a natural aesthetic.
The geometry of the EAP abutments is different and also incorporates ceramic behind the metal. When the surrounding tissue recedes it is possible to remove some of the metal to reveal the ceramic again as you can see in the following video.
The surface of abutments is made for optimal cell attachment. Dr. Mario Kern further explains, “A smooth surface makes cell attachment difficult, and a rough surface facilitates bacterial growth. A roughness of 0.2µm of the EAP surface is ideal as it allows a positive impact on cell growth.”
A winning technology
As Dr. Mario Kern explains, “Our hybrid abutment EAP® Extended Anatomic Platform was nominated and won by an international panel of experts. This represents another milestone in the history of our product, which we have been developing since 2012. This prestigious award once again demonstrates our responsibility for our great product, which will facilitate and improve many aspects of implant prosthetics.”
The EAP process integrates GE Additive’s Dental Hybrid Solution which combines metal 3D printing and CNC milling. The solution uses Follow-Me open software for data preparation and control of both the Concept Laser Mlab cusing 200R 3D printer and the Datron C5/D5 5-axis milling and post-processing machine. The Mlab cusing 200R 3D printer produces the structures that connect a crown, bridge or removable denture to the dental implant fixture before being milled.
“The Dental Hybrid process enables economical production of my abutment with the highest accuracy. With its dental expertise and technical solutions, GE Additive is the perfect partner for my business. This solution combines the advantages of additive manufacturing with subtractive technology, to get the best out of both manufacturing worlds, which means a time and cost-efficient production process”, said Dr. Mario Kern. In fact, the EAP process has been said to reduce production costs and time by an estimated 40%.
Find out more HERE.
Let us know what you think in a comment below or on our Facebook and Twitter pages! Sign up for our free weekly Newsletter, all the latest news in 3D printing straight to your inbox!