10 Reasons Why DfAM Matters in 3D Printing
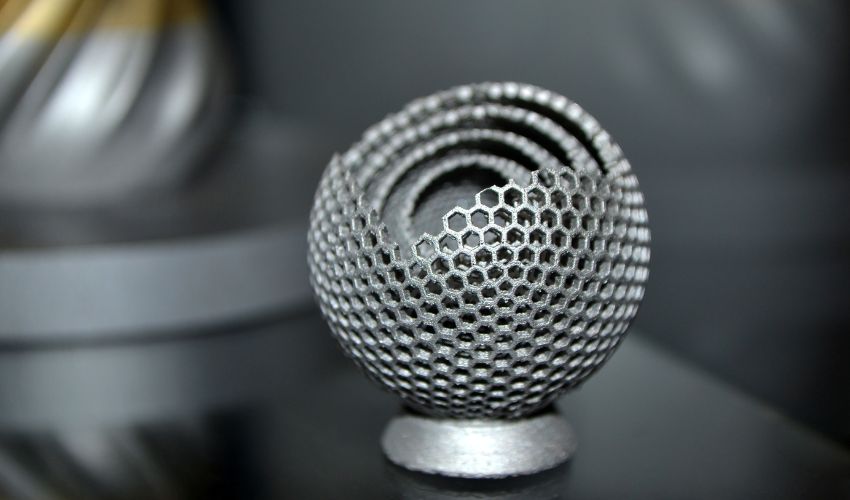
At this point, if you are involved with additive manufacturing, you know just how important design is for the creation of a part, with modeling being the first step in any 3D printing process. Enter Design for Additive Manufacturing, or DfAM as it is more commonly known. Defined as “design for manufacturability” for additive manufacturing, or more simply as the design methods and tools that can optimize parts that are created using additive manufacturing, DfAM allows users to take advantage of the benefits of the design freedom that is present in 3D printing and is key to creating functional, high-performing parts. But, even with that knowledge, DfAM is sometimes ignored in the industry. But why is it important? What benefits can it bring to parts? We explore these questions in our new editorial format where we list 10 reasons why DfAM matters in 3D printing.
#1. Reduced 3D Printing Mistakes
Printing failures are the bane of any user of additive manufacturing technologies. Especially when it comes to highly industrial processes, such as LPBF or SLS which use lasers, or expensive materials like PEEK and PEKK, small mistakes that ruin the part can really set users back in terms of cost and time. This is where the value of DfAM becomes quickly obvious. Through design, it is possible not just to properly orient and support the model (both of which go a long way in ensuring properties such as isotropy and in ensuring there will be no warping), but also to allow users to choose the right infill and layer settings for a part. This in turn significantly reduces print failures.
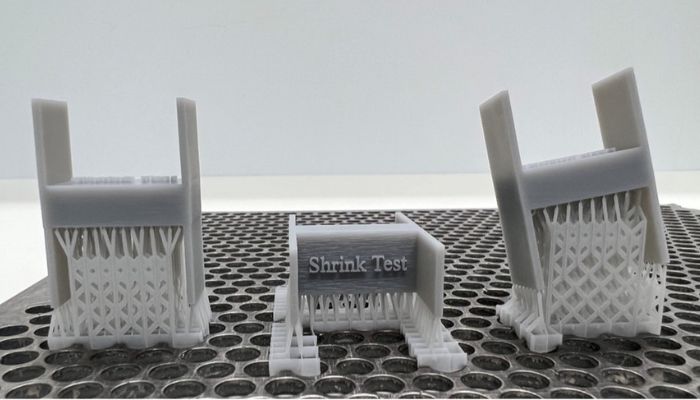
Correction orientation is one of the considerations in DfAM (photo credits: Protolabs)
#2. Faster Printing
Speed is a core benefit of additive manufacturing as the technologies enable users to create parts at a fraction of the time that would be used with conventional manufacturing methods. However, that speed is not a given. By using DfAM, it is possible to optimize the design using tricks like lattice structures to keep the strength while minimizing the amount of material that needs to be used. It also will allow users to minimize support structures which, as will be discussed below, also cuts down on print time.
#3. More Complex Designs
In 3D printing, there is no additional difficulty involved when a design is more complex. DfAM therefore allows for users to create significantly more complex geometries than those that would be made using more traditional design rules. Through software, parts that significantly more complex geometrically, especially for metal, can be designed and then printed. This complexity is where we really see the freedom that 3D printing brings to users.
#4. Optimize Weight-Performance Ratio
Connecting to the previous example, DfAM also allows users to take advantage of different design software to fully optimize a part. We’ve heard about it time and time again, one of the reason why 3D printing is so coveted in sectors like aerospace and automotive is because it allows you to create a part that is substantially lighter while still keeping its strength and other properties, meaning a superior weight-performance ratio. This can be done notably through DfAM, for example by integrating lattice structures or using topological optimization and generative design for a part. These are specifically designed to optimize and generate parts to have less material while still meeting specific constraints like strength. And while in traditional manufacturing, the resulting parts can be too complicated to make, this is not a problem in 3D printing, as mentioned above.
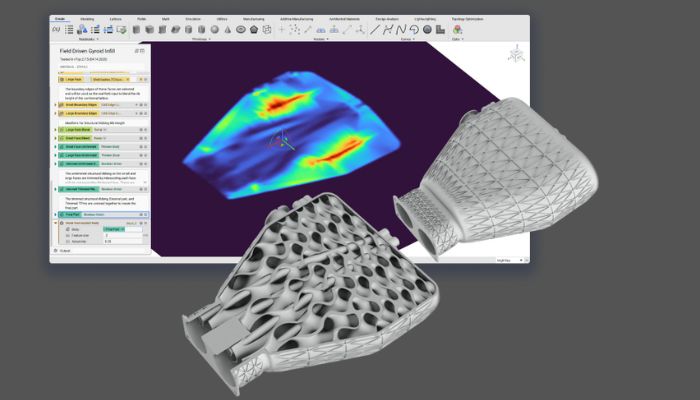
One of the ways that DfAM can be used is with topological optimization (photo credits: nTop)
#5. Fewer Support Structures
It can be easy to see support structures as a “necessary evil” in 3D printing. While supports are absolutely critical for ensuring that a part will not deform or warp during the 3D printing process, they also mean more material use (affecting both cost and time), which in turn can make post-processing longer as well as affect the look of the part. This is where DfAM can play a role. Through careful design of parts, such as reducing overhangs, improving orientation or correctly choosing infill settings, users can have fewer supports when making parts.
#6. Reducing Post-Processing
Continuing from the previous point, another significant reason that DfAM matters is that it will allow users to reduce overall post-processing. Of course, one of the main reasons that this can be done is through optimization of support structures, meaning less time will be used on removing them, but there are also other considerations. For example, by orienting the part correctly or reducing layer height (both important considerations in DfAM), issues such as surface smoothness can be addressed already before printing even starts. If these things are not considered, often post-processing will take significantly longer, hence the benefit of turning to DfAM.
#7. Part Consolidation
Another reason why DfAM matters is for part consolidation. An increasingly popular reason for using additive manufacturing, especially in sectors like aerospace and automotive, is the ability to consolidate multiple parts into one through more complex geometries. One example of this is with the Czinger 21C hypercar where the manufacturer, Divergent 3D, claims that it were able to consolidate thousands of parts into just a few hundred, significantly lowering the weight and increasing performance. This type of consolidation is only possible through 3D printing and can be done by learning and adopting the rule of DfAM.
#8. Increased Scalability and Mass Production
Admittedly, this next point does not necessarily apply to each 3D printing technology equally. Not all of them are well-suited to mass production or scalability for various reasons. However, for technologies like SLS, DMLS, resin 3D printing and binder jetting, DfAM can play a critical role in scaling up production. Through DfAM, the maximum number of parts can be placed on the build volume through stacking. Taking DfAM into account can help users overcome one of the major criticisms of 3D printing, that it is not well-suited to mass production.
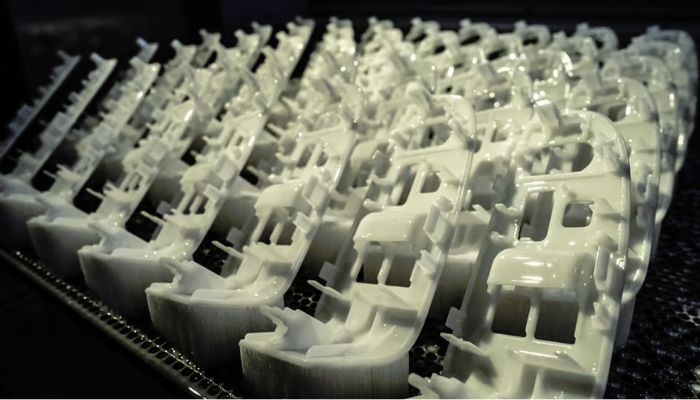
Stacked 3D printed parts made using resin 3D printing (photo credits: 3D Systems)
#9. Cost Optimization
Complex geometries and lighter parts are key reasons that DfAM matters, but what are the benefits of being able to create them if the cost is too great? Luckily, DfAM has actually been shown to also reduce cost when making parts. In 2020, The Barnes Group argued that 86% of the cost of the part in AM was driven by design, and that has been proven over and over again. Only through design can you reduce the amount of material used while continuing to keep strength and other properties, ultimately affecting the cost of the part. Also, it’s important to consider that more complex does not mean more expensive, in fact depending on the design, it could be the opposite!
#10. Optimization based on 3D technology
Last, but certainly not least, DfAM matters because it allows users to optimize the part based on the specific 3D printing technology used. There are seven families of 3D technologies with even more processes falling under them and it should go without saying that there are significant differences in them. One example is powder-based technologies, where designs should probably integrate escape holes to ensure that the parts are printed hollow (which would not be a concern in FDM or resin 3D printing). Meanwhile, in FDM 3D printing, anisotropy is common, thus DfAM can help improve isotropy on parts if necessary.
What do you think of these 10 reasons why DfAM matters? Do you already use DfAM when designing parts for 3D printing? Let us know in a comment below or on our LinkedIn, Facebook, and Twitter pages! Don’t forget to sign up for our free weekly newsletter here, the latest 3D printing news straight to your inbox! You can also find all our videos on our YouTube channel.