10 Reasons Why 3D Printing Is Considered Sustainable
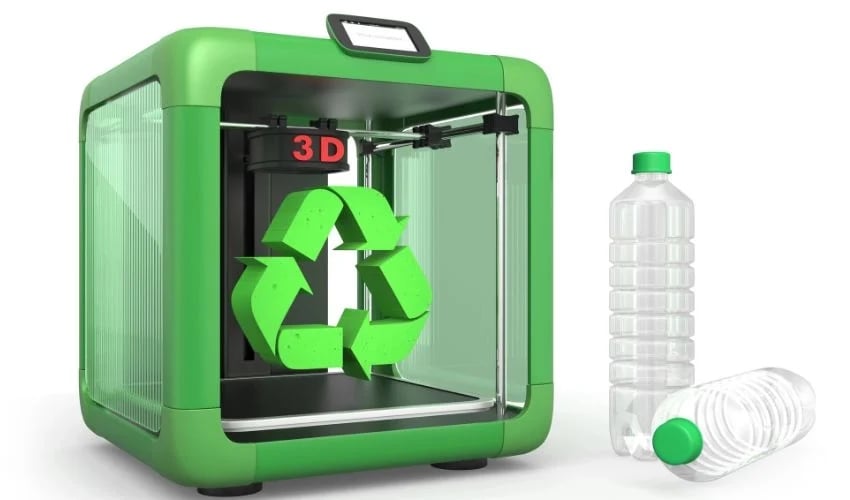
Additive manufacturing is often seen as a greener alternative to traditional manufacturing methods and mass production, which generates high emissions. One reason for this is that 3D printing only adds materials where they are actually needed, thus reducing waste. Although the sustainability benefits of 3D printing depend on the process, materials and components used, it offers many opportunities to make industry more sustainable and respectful of our resources. The UN’s Sustainable Development Goals are also encouraging industry to pursue greener strategies, such as climate protection measures or more sustainable consumption and production patterns. In this article, we present ten reasons why 3D printing is considered more sustainable, and the potential of this manufacturing technology for a more environmentally friendly future.
#1: Reduction of Waste and Material
Compared to traditional manufacturing methods, 3D printing offers advantages in terms of waste reduction. In general, subtractive processes such as turning, drilling or sawing generate more material waste, for example in the form of chips. This problem does not arise with 3D printing, as the material is used directly for the layer-by-layer construction of the object. However, it must be stated that the generation of waste varies depending on the technology, as powder and resin printing processes generate more waste than other 3D printing technologies due to the need for support structures or excess powder that cannot be fully reused. Still, by precisely planning the required material, software functions can optimize the 3D model to minimize material usage. This ensures a more efficient use of resources and reduces energy consumption and machine emissions.
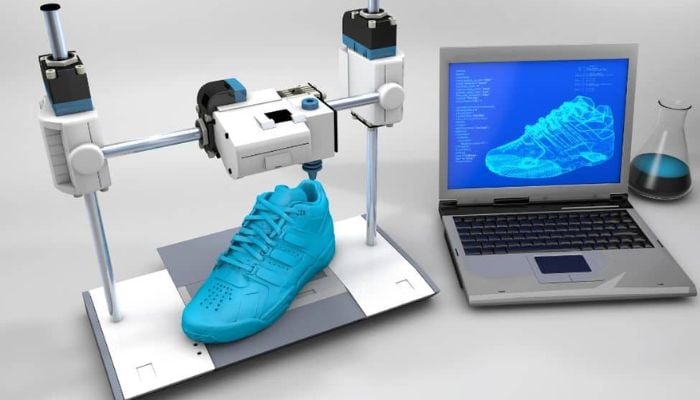
3D printing involves printing directly onto the building platform, which minimizes material waste (photo credits: Devrimb)
#2: Local Production
Traditionally, many products are sourced from distant locations, leading to global dependency and supply chains that impact our local economy and environment. However, thanks to local 3D printing, companies are able to produce their products directly within the community without relying on external supplies, thereby reducing CO2 emissions. It also avoids the use of packaging normally associated with the transportation of parts.
#3: On-Demand Production
On-demand production is also linked to local production. Companies can manufacture products flexibly and in line with demand, which significantly minimizes overproduction and the need for inventories. Spare parts do not have to be kept in stock, but can be produced as needed. The flexibility of additive manufacturing makes it possible to offer customized products that meet the individual needs of customers and thus ensure demand-oriented production, which could lead to a reduction in industrial processes in the future.
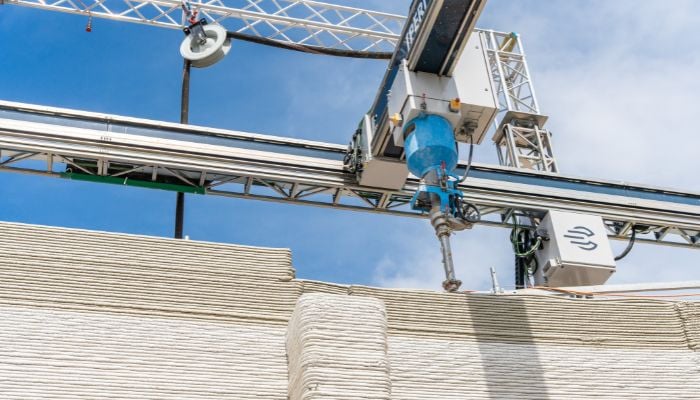
On construction sites in particular, 3D printing, especially concrete 3D printing, is used on site, making construction more sustainable (photo credits: Heidelberg Materials)
#4: Service Life Extension Through Repair
The reusability of components through 3D printing also promotes the circular economy. In industry, the DED (Direct Energy Deposition) process is often used to repair damaged components by applying material layer by layer to the existing components instead of manufacturing them from scratch. The process reduces the need for new raw materials and extends the service life of components. Almost all weldable metals can be used for this purpose, which increases the flexibility and efficiency of the repair process.
#5: Recycling and Upcycling
Misprints, defective or no longer required print projects can potentially be melted down and reused for the manufacture of new products. Thermoplastic materials such as ABS, PETG or PLA in particular offer these recycling options. However, this still rarely happens. The technology is useful for upcycling used products by combining waste products with 3D-printed workpieces and creating innovative one-offs. Despite the advantages mentioned, recycling materials also poses a challenge, as the quality of the material must be high enough to be reused in a printing process. Multi Jet Fusion enables a sustainable approach here with its reusability rate of up to 80% of used material and powder bed fusion technologies may also offer the possibility of reusing up to 98% of the powder, but due to the lack of studies surrounding this, this is in doubt.
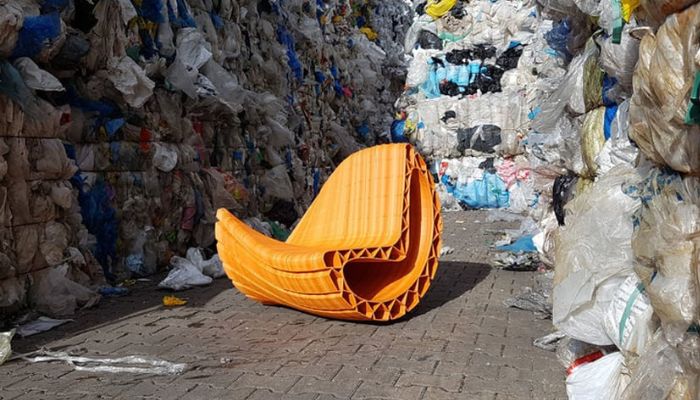
The Print your City project transforms plastic waste into furniture using 3D printing (photo credits: Print your City)
#6: Eco-Friendly Materials
Many sustainable materials are now available for 3D printing, which are either recyclable or bio-based. In addition to traditional metals and plastics, new materials that can reduce the ecological footprint are increasingly being used. Examples include biodegradable materials such as filaments made from corn starch, coffee grounds, sugar cane or wheat waste, which can be disposed of in a more environmentally friendly way. PLA, which is made from natural raw materials such as corn, is particularly well known. By adding by-products, the filament can be almost 100% bio-based. PLA is also biodegradable in industrial composting plants (even if its sustainability has been questioned). Non-fossil plastics such as PET or PHA made from renewable raw materials and recycled filaments made from ABS and PET also support the circular economy. However, the sustainability of all these materials depends on various factors, including the raw material source, compatibility with ecosystems, transportation routes and recyclability. Continuous research, experimentation and improvement of existing materials could reduce environmental impacts in the future.
#7: Energy-Saving Production
By combining several functions in one production run, 3D printing offers opportunities to save energy. A significant advantage lies in the energy efficiency of the end product. In the aerospace sector, weight reduction through 3D printed parts leads to lower fuel consumption and a reduction in emissions compared to traditionally manufactured parts. By using less filler material and more efficient material utilization, 3D printing enables faster production with lower energy consumption. Additionally, special filaments can be used that have a lower melting point or a print bed insulated with aerogel that can maintain temperatures up to 60°C with almost no additional power consumption. Other measures that can be taken include insulating the print head with silicone or rock wool, which reduces heat loss, or building an enclosure around the printer to prevent temperature loss.
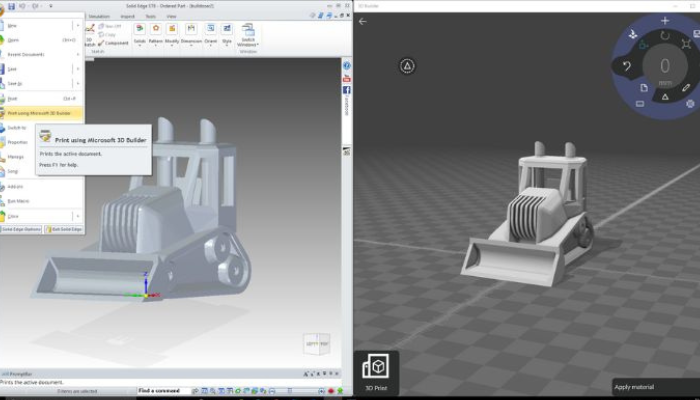
Using software, you can optimize your design to save material (photo credits: Solid Edge)
#8: Optimized Design Through Software
The use of 3D modelling software enables effective design optimization, reducing material consumption and printing time and promoting environmentally friendly production processes. Virtual simulations help to remove unnecessary details and support structures and some software provides tools for early error detection and defect analysis during 3D CAD design. The software solutions make it possible to test models digitally, saving material and energy through unnecessary test prints. The digital transfer of CAD designs also reduces the need for production facilities and lowers transportation costs and emissions. In addition, the lightweight design enables material savings through reduced filling and increased wall thickness. Manufacturing complex assemblies as one-piece components reduces material and energy consumption. Work is currently underway on new processes that use artificial intelligence to detect and correct printing errors in real time.
#9: Environmental Protection Projects
3D printing not only offers the potential for more environmentally friendly production, but also makes an effective contribution to the preservation of species and our environment. For example, the technology is used to replicate nature in order to print coral, nests, reefs or beehives and to provide animals that have lost their shelter due to climate change with an artificial dwelling that is identical to their natural habitat. The company is also involved in ocean conservation projects and the production of meat alternatives. This not only protects animals, but also reduces CO2 emissions, as the consumption of one piece of beef generates up to 12 kg of CO2. Various companies use additive manufacturing to produce plant-based meat, which promises a 95% lower environmental impact compared to conventional meat production.
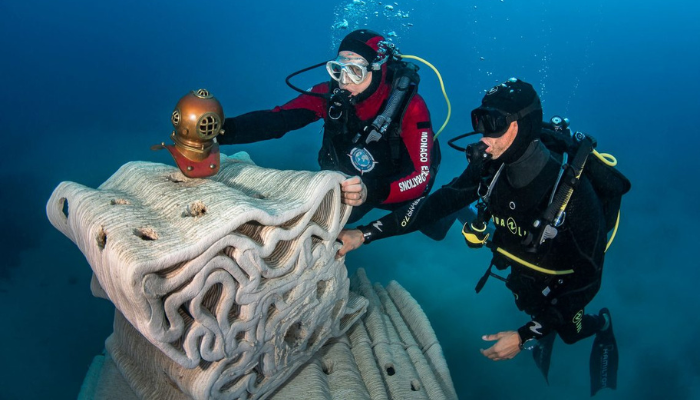
Divers bring a 3D-printed reef to the seabed (photo credits: xtreee.com / Greg Lecoeur)
#10: Research and Innovation
Last but not least, the threshold for prototype development and experimentation in 3D printing is very low. This allows companies and innovators to implement new ideas quickly and develop sustainable solutions. This flexibility results in constant product and technology improvements, especially with regard to environmental protection. Many companies and start-ups are actively dedicated to the further development of additive manufacturing in order to make it more efficient and even more environmentally friendly. This innovative strength opens up new possibilities for creative applications and industrial processes and ensures that 3D printing is continuously optimized in terms of its sustainability.
Do you think that 3D printing is more sustainable? Are there any major reasons we left out? Let us know in a comment below or on our LinkedIn, Facebook, and Twitter pages! Don’t forget to sign up for our free weekly newsletter here for the latest 3D printing news straight to your inbox! You can also find all our videos on our YouTube channel.