10 Reasons to Use Pellets in 3D Printing
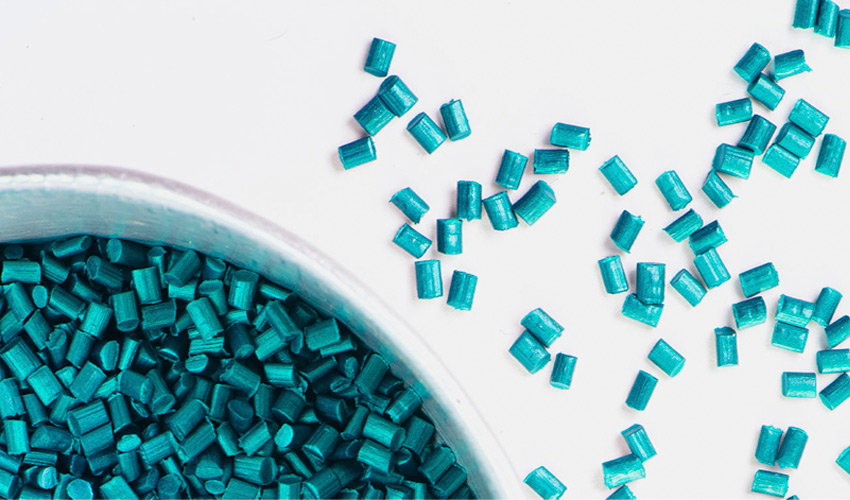
The term pellets, in the context of plastics, refers to small granules of various shapes (small cylinders or discs) made of polymer or a polymer blend. These are used as a raw material for the manufacture of finished plastic products through various technologies, among which is additive manufacturing. The 3D printing technology used with pellets is material extrusion, which often involves a comparison with the use of filaments. Today we will look at why using pellets in 3D printing can be advantageous, analyzing the top 10 reasons why manufacturers and users are turning to this technology. The choice is not just about the shape of the material used, as much as the type of material, the machines used, the end applications, the size of the parts, the flexibility and speed of printing, and the sustainability aspect of the pellets. We delve into all these points and more below.
1. Wide Material Choice
One of the prime motivations for adopting pellet 3D printing is the ability to have access to a wide range of materials. In FFF 3D printing, the materials available in filament form, while numerous today, pale in comparison to those available as pellets. This is because the pelletizing process allows a plastic material to be transformed into pellets without significantly compromising the starting polymer, as is the case when creating filaments.
Thus, pellets allow the use of raw polymers, thermoplastics and even composite materials with additives such as glass or carbon fibers. This allows experimentation with new formulations, adapting the mechanical, thermal or aesthetic properties of the finished product and obtaining customized formulations. Finally, pellets are also used in other manufacturing technologies, such as injection molding, which expands the choice of materials available.
2. Increased Printing Flexibility
Another reason to consider using pellets in 3D printing is the possibility of using different machines, from desktop 3D printers to robotic arms that create large parts. Robotic 3D printing in particular allows for a high degree of printing flexibility by being able to work on 5 axes and on very large surfaces, enabling the creation of medium and large parts for a wide variety of industries: from construction, to design, to transportation and beyond.
As a result, pellets are particularly suitable for large-format 3D printing (LFAM) since using large quantities of material in the form of filaments would be economically disadvantageous. In addition, the use of pellets allows the use of extruders with a larger diameter than 0.8 mm (limit for 3D printing with filaments), which is ideal for larger and faster prints.
3. Cost Reduction
Among the main reasons for adopting 3D printing with pellets is undoubtedly the cost savings. Considering that filaments are manufactured from pellets, one can imagine that the cost of pellets compared to filaments is much lower (an estimated 65-90% reduction in printing costs per kilo). In addition, since pellets are also used in other technologies such as injection molding, this makes the market much larger and drives down costs.
The economic advantage becomes even more obvious when printing large quantities of material and large parts, in generally shorter times than when printing with filaments. In addition, the choice of pellets also allows cheaper or recycled materials to be used, further lowering costs and promoting the circular economy. It should be noted that the cost of infrastructure still remains high, as these are often large machines. However, 3D pellet printing allows flexibility in this respect, and small and medium-sized companies are now able to build their own machines at a lower cost.
4. Circular Economy
The use of pellets in 3D printing promotes the circular economy in several ways. First, pellets can be produced from recycled materials, allowing plastic waste to be reduced and fed back into the production cycle. Pellet printers allow the use of reclaimed or industrial waste plastics, limiting the need for new raw materials.
In addition, users have the option to directly recycle printed products or failed prints, making the entire printing process more sustainable and reducing environmental impact. This approach aligns perfectly with the principles of the circular economy, where reuse of materials is essential to reduce waste and energy consumption.
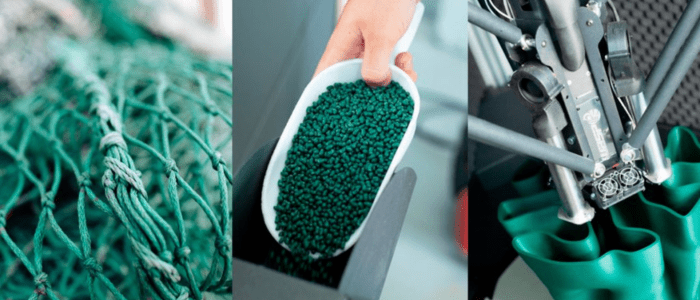
In partnership with WASP, Reflow has produced rPPGF material obtained from fishing nets, recycled and pelletized for use in 3D printing (photo credits: WASP)
5. Increased Production Speed
3D printing with pellets is fast mainly because of the ability to use machines with larger diameter nozzles than those used for FFF 3D printing. This therefore increases printing and production speed and contributes to cost reduction. However, there is also a less positive aspect to this point: by increasing the nozzle size and printing speed, the final parts will lose detail and complexity.
6. Lower Risk of Printing Interruptions
3D printing with pellets reduces the risk of interruptions and printing problems compared to traditional filaments due to the nature of the direct extrusion process. The pellets are consistently melted, eliminating the need to replace material, as with filament spools, during the process. In addition, the pellets, being in granular form, do not experience twisting or deformation typical of filament, thus reducing the possibility of blockages or jams in the extruder.
The configuration of pellet extrusion systems is designed to handle larger volumes and continuous flows of material, making the printing process smoother and more reliable. That said, the shape of the pellets is crucial in 3D printing: before starting printing, it is important to ensure that the pellets are compatible with the 3D printer being used.
7. Multi-Material and Multicolor 3D Printing
Connecting to the point about materials, we can add among the advantages of 3D pellet printing the fact that it is possible to mix multiple materials directly in the print head of the machine. Although obviously, you will need to evaluate the printing temperatures and specific characteristics of each material and choose the most appropriate printer. In addition, it is possible to introduce color additives to the pellets and create multicolored or differently colored parts within a single print. This makes it possible to obtain parts with unique and highly customized properties.
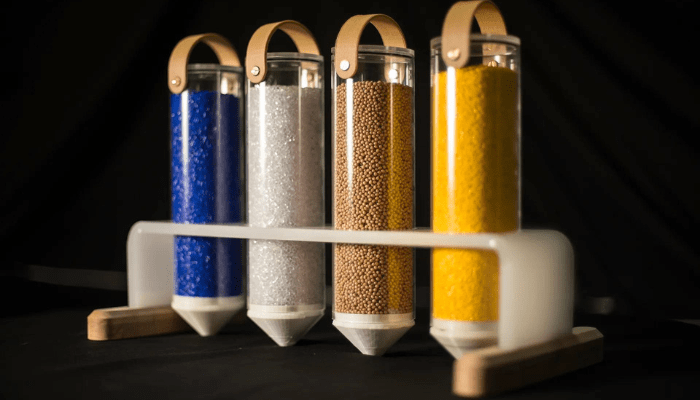
The use of pellets in 3D printing allows for a wide choice of materials, colors and greater printing flexibility (photo credits: Pollen)
8. Properties of Final Parts
When working with granules, the final properties that can be obtained are high, because they preserve the characteristics of the raw material. You cannot achieve the same results with filaments, whose manufacturing process, added to the printing process, make the properties of the final product different from those of the starting material. Using pellets in 3D printing makes it possible to obtain parts with the same chemical and physical properties obtained with injection molding.
9. Simplified Production
As mentioned earlier, pellets are also used in other manufacturing technologies. The use of pellets thus simplifies production because it allows the same material to be used for both additive manufacturing and other processes, such as injection molding. This is particularly beneficial for companies that work with multiple technologies and can thus optimize raw material management, reducing logistics costs and simplifying the entire supply chain.
For example, the use of pellets allows for a rapid transition from prototyping to mass production. During the prototyping process, using pellets makes it possible to test the properties of a material through 3D printing, and then quickly move to mass production with injection molding.
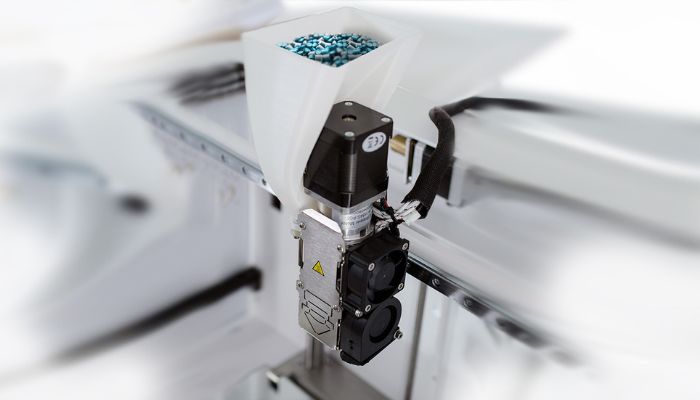
Pellet 3D printing solutions on the market are on the rise, with LFAM solutions as well as smaller format ones (photo credits: Tumaker)
10. An Expanding Market
All the previously stated reasons are driving more and more users to adopt pellet 3D printing for cost, time, flexibility and sustainability benefits. Undoubtedly, the technology is less widely adopted than filament extrusion 3D printing, but there is an increasingly diverse choice of pellet 3D printing solutions on the market. However, current limitation to the adoption of the technology include mainly the high cost of the machines, which are generally more complex and large in size, or the low accuracy of the prints.
Companies and startups are therefore trying to bring more affordable solutions to the market, pellets created specifically for 3D printing or extruders optimized and adaptable to machines already owned by companies. Finally, the possibility of using recycled materials in pellets and fostering a circular economy offers an important motivation nowadays to further develop the technology for more sustainable future production.
Do you use pellets for 3D printing? Let us know in a comment below or on our LinkedIn, Facebook, and Twitter pages! Don’t forget to sign up for our free weekly newsletter here for the latest 3D printing news straight to your inbox! You can also find all our videos on our YouTube channel.