Heraeus stellt größtes aus amorphen Metallen 3D-gedrucktes Zahnrad her
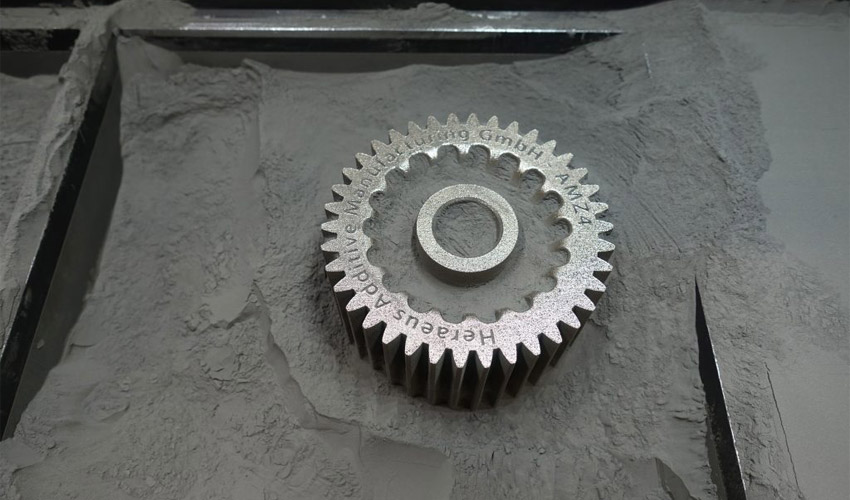
Heraeus ist ein deutscher Technologiekonzern, das sich unter anderem auf Edel- und Sondermetalle und Quarzglas spezialisierte und, wie viele Materialhersteller, in die additive Fertigung investiert hat. Mit der Erstellung des größten additiv gefertigten Zahnrades aus amorphen Metallen – auch bekannt als metallisches Glas – brachen sie kürzlich einen Rekord bei den 3D-Druckteilen. Gedruckt auf einer der Maschinen des Herstellers EOS eröffnet Heraeus das Feld der Möglichkeiten für eine Vielzahl von Branchen.
Die Vorteile des Metall-3D-Drucks haben sich bewährt; die Technologie hat viele Branchenteilnehmer angezogen, die von dieser neuen Fertigungsmethode profitiert haben und in der Lage waren, das Gewicht ihrer Teile zu reduzieren, während sie ihre Komplexität erhöhten und die Produktionszeiten verkürzten. Heraeus hat sich in seinem additiven Herstellungsverfahren für amorphe Metalle entschieden. Diese amorphe Metalllegierung hat, wie ihr Name schon sagt, eine amorphe und nicht kristalline Struktur und kann durch sehr schnelles Abkühlen aus dem geschmolzenen Zustand der Legierung erhalten werden. Es handelt sich um eine Materialart, die sehr interessante mechanische Eigenschaften wie hohe Festigkeit, ausgezeichnete Korrosions- und Verschleißfestigkeit, hohe Streckgrenze und leichte Magnetisierung und Entmagnetisierung bietet. Sie kann daher als interessantere Metalle angesehen werden als Stahl oder Titan.
Ein leichteres Zahnrad
Es ist also diese amorphe Metalllegierung, die für den 3D-Druck des Zahnrades von Heraeus verwendet worden wurde. Ein Herstellungsverfahren, das das Endgewicht des Zahnrads um die Hälfte reduziert habe. Nach Angaben des Unternehmens wog es nur noch 2 Kilogramm. Dank topologischer Optimierungsverfahren ist es gelungen, die Geometrie des Zahnrades zu optimieren und Bereiche zu entfernen, die für seine einwandfreie Funktion nicht notwendig sind. Dies ist ein Rekord für die Gruppe, denn aufgrund der hohen erforderlichen Abkühlraten, vor allem über 1000 Kelvin / Sekunde, konnten bisher nur Kleinteile aus amorphen Metallen hergestellt werden.
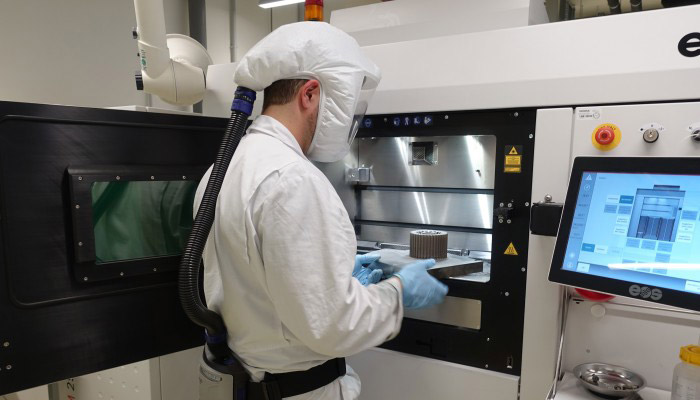
Heraeus verwendete Metall-3D-Drucklösungen von EOS
Das Team sagt: „Komplexe Bauteile benötigen mit konventionellen Methoden zahlreiche Arbeits- und Fertigungsschritte. Mehrere Einzelteile müssen produziert und anschließend zusammengefügt werden. 3D-Drucker erledigen dies in einem einzigen Vorgang. Nach dem Aufbau im Drucker sind auch bewegliche Teile sofort einsatzbereit und voll funktionsfähig.„
Weitere Informationen finden Sie in der offiziellen Pressemitteilung HIER.
Teilen Sie uns Ihre Meinung mit und kontaktieren Sie uns. Möchten Sie eine Zusammenfassung der wichtigsten Neuigkeiten im 3D-Druck und der additiven Fertigung direkt und bequem in Ihr Postfach? Registrieren Sie sich jetzt für unseren wöchentlichen Newsletter und folgen Sie uns auf Facebook, Twitter und Google+, um stets auf dem Laufenden zu bleiben! Außerdem sind wir auch auf XING und LinkedIN zu finden.