Zukunft der Wärmekontrollsysteme: 3D-gedrucktes Rohrsegment kombiniert Heizung und Sensor
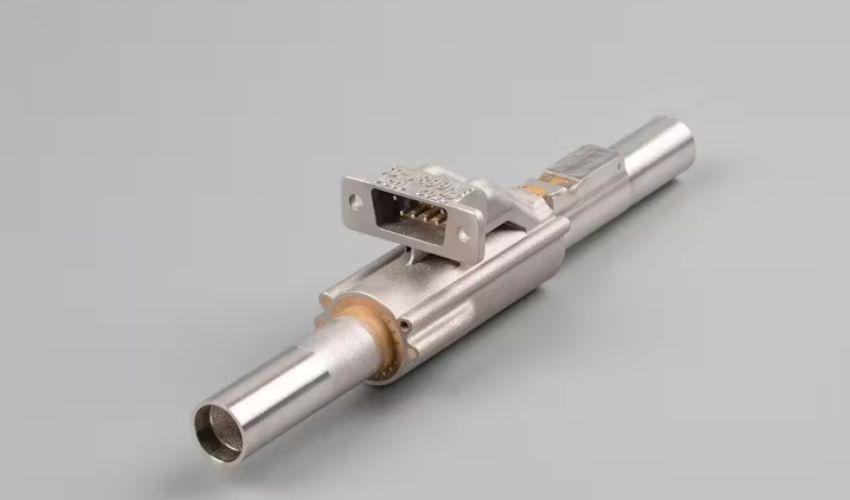
Die meisten der heute verwendeten Wärmekontrollsysteme sind schwer, sperrig und erfordern darüber hinaus viele Verbindungskabel. Das EU-Projekt AHEAD (Advanced Heat Exchange Devices) zielt darauf ab, diese Systeme zu optimieren, und nun wurde ein vielversprechendes Ergebnis vorgestellt: ein 3D-gedrucktes Rohrsegment, das die Flüssigkeit in Mechanically Pumped Loops (MPL) erhitzen und ihre Temperatur messen kann.
Entwickelt wurde das Rohrsegment vom Schweizer Technologie-Innovationszentrum CSEM in Zusammenarbeit mit LISI Aerospace Additive Manufacturing und Thales Alenia Space France. Das Besondere an dem 3D-gedruckten Rohrsegment ist, dass es Heizelemente und Temperatursensoren kombiniert. Außerdem könnte es zukünftig in thermischen Kontrollsystemen von Satelliten verwendet werden. Aber auch außerhalb der Satellitentechnologie könnte das Segment in IoT-Anwendungen oder der Industrie 4.0, wo Heiz- und Überwachungslösungen die Zuverlässigkeit von Wärmemanagementprozessen verbessern, eine wichtige Rolle spielen.
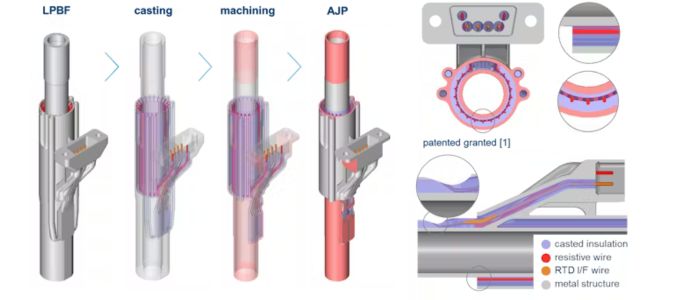
Das Segment wiegt 115 Gramm, ist 150 Millimeter lang und kann bei Temperaturbereich von – 65 °C bis +85 °C sowie bei einem Druck von bis zu 48 bar arbeiten. (Bild: CSEM)
Doch wie wurde das 3D-gedruckte Rohrsegment hergestellt, und wie kommt es in MPLs zum Einsatz? Mechanically Pumped Loops lassen Flüssigkeiten wie Ammoniak zirkulieren, damit Wärme von heißen zu kalten Bereichen transportiert wird. Das 3D-gedruckte Rohrsegment soll hier das Kühlmittel beheizen und die Temperatur messen, um die thermische Regulation zu steuern. Hierfür wurde das Segment aus Edelstahl 316L und mittels Laser-Pulverbett-Schmelzen produziert. Der 3D-Druck verringerte die Notwendigkeit, separate Komponenten zu verkleben oder zu verdrahten, was die MPL-Installation vereinfacht, da ohne den Verdrahtungsprozess Risiken reduziert werden. Auch Hervé Saudan, Projektleiter bei CSEM, betont, dass das Design für eine gleichmäßige Wärmeübertragung sorgt, da die Heizdrähte optimal um das Rohr angeordnet sind, wobei Fehler wie Delamination oder Kabeltrennung wegfallen.
Dennoch brachte die Herstellung auch erhebliche Herausforderungen mit sich, wie beispielsweise den 3D-Druck langer elektrischer Leitungen, die elektrisch von der Rohrstruktur isoliert bleiben sollen. Hierfür wurden Opferbrücken, also Stützstrukturen, entwickelt – eine Designlösung, die die elektrische Isolation zwischen Drähten und der Rohrstruktur gewährleistet und der Aushärtung ganz einfach entfernt werden kann. Darüber hinaus musste das Laser-Pulverbett-Schmelzen aufgrund der kleinen Lücken zwischen Struktur und Drähten hochpräzise sein. Das bedeutet, die Lücken durften nicht zu eng sein, da dies zu großer Materialverschmelzung führt, und gleichzeitig durften sie nicht zu groß sein, da dies die Wärmeübertragung von Drähten auf die Innenseite des Rohrs beeinträchtigt. Die Design- und Herstellungsprozesse wurden nun durch ein Patent geschützt.
Für zukünftige Weltraumanwendungen könnte die Struktur solcher Rohrsegmente auch aus Aluminium bestehen, um das Gewicht weiter zu reduzieren, aber auch andere Materialien wie Glaskeramik als Isoliermaterial oder Harze könnten verwendet werden. Mit dem Vorteil integrierter Kabel ebnen die 3D-gedruckten Rohrsegmente den Weg für weitere Anwendungen im Bereich der Heizung. Hervé Saudan bestätigt: „Wir haben mehrere laufende Projekte, aber ich fürchte, sie bleiben derzeit vertraulich.“ Mehr über das Rohrsegment erfahren Sie HIER.
Was halten Sie von der Produktion des 3D-gedruckten Rohrsegments? Lassen Sie uns dazu einen Kommentar da, oder teilen Sie es uns auf Facebook oder LinkedIN mit. Wenn Sie mehr zum 3D-Druck in der Luft- und Raumfahrt lesen möchten, schauen Sie auf unserer Landing Page vorbei. Möchten Sie außerdem eine Zusammenfassung der wichtigsten Neuigkeiten im 3D-Druck und der additiven Fertigung direkt und bequem in Ihr Postfach erhalten? Dann registrieren Sie sich jetzt für unseren wöchentlichen Newsletter.
*Titelbildnachweis: CSEM