Velettrica nutzt 3D-Druck für eine nachhaltigere Schifffahrt
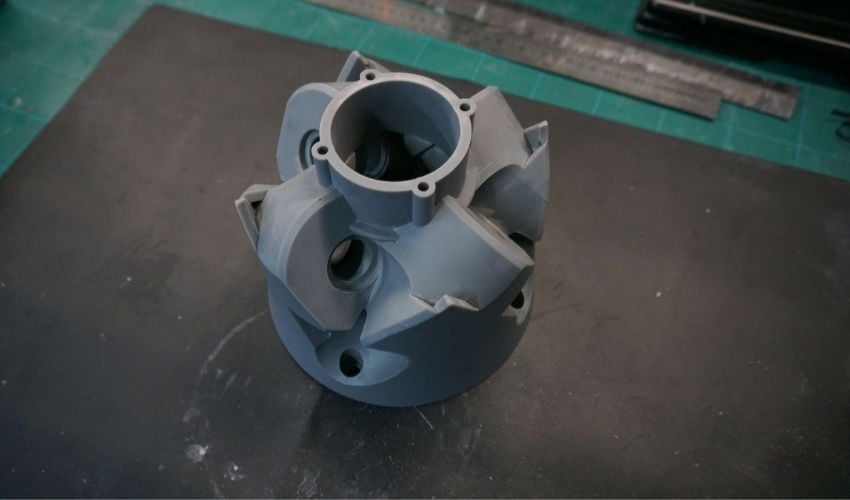
Die additive Fertigung ist inzwischen so ausgereift, dass fortschrittliche Materialien hergestellt werden können, die selbst in den extremsten Umgebungen – vom Himmel über den Weltraum bis hin zu den Tiefen des Meeres – effiziente und kostengünstige Lösungen garantieren. Ein hervorragendes Beispiel für diese technologische Revolution ist Velettrica, ein italienisches Startup, das den 3D-Druck zur Entwicklung von Schlüsselkomponenten für den funktionierenden Prototyp des Segelbootmotors SAIL-POD 25 eingesetzt hat. Um mehr darüber zu erfahren und zu verstehen, wie der Einsatz von Spitzentechnologien wie 3D-Druck und biomimetischem Design neue Grenzen im nachhaltigen Segeln eröffnet, haben wir den Gründer von Velettrica, Roberto Baffigo, interviewt.
3DN: Könnten Sie sich kurz vorstellen und erzählen, wie Sie zum 3D-Druck gekommen sind?
Ich bin Roberto Baffigo, wurde 1972 in Rom geboren und habe in meinem Leben immer Sport getrieben: Rudern, Segeln, Mountainbiking, Skifahren und jetzt Flossenschwimmen. Ich habe Physik studiert und das hat meine Neugier und Experimentierfreudigkeit geweckt. Meine Verbindung zum 3D-Druck stammt aus der Welt des Schmucks: Der Übergang vom manuellen zum digitalen Prototyping war eine echte Revolution, die mit der Verfügbarkeit von immer zuverlässigeren und kostengünstigeren Drucktechniken explodierte. Der 3D-Druck ermöglichte es mir, alle Erfindungen, die in der speziellen Spirale von Velettrica enthalten sind, schnell zu testen.
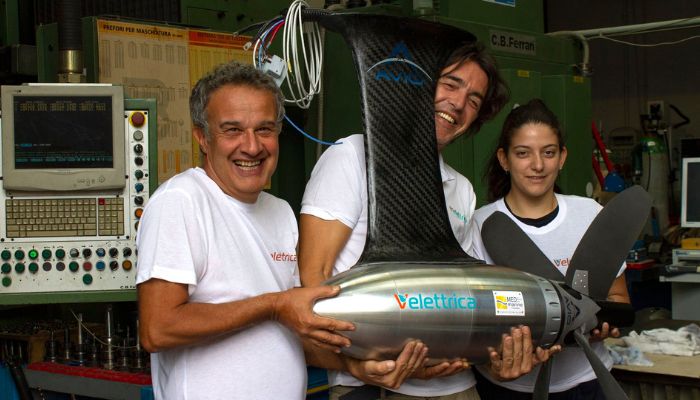
Roberto Baffigo und das Velettrica-Team mit dem SAIL-POD 25-Motor.
3DN: Wie kam es dann zur Gründung von Velettrica und was ist Ihr Ziel?
Velettrica entstand 2021 aus dem Traum, das umweltfreundliche Segeln zu erforschen, eine Idee, die bei Segelurlauben mit meiner Frau Chiara und unseren Kindern Stella und Pietro Noè reifte. Ich habe immer davon geträumt, mit ihnen im Gleichgewicht mit der Natur reisen zu können. Ich wollte das Segelboot noch umweltfreundlicher machen, indem ich einen Elektromotor einsetzte, der nicht nur für den Antrieb sorgt, sondern auch Energie erzeugt, wenn er vom Wind angetrieben wird. Der Motor, der im Rahmen des Velettrica-Projekts entwickelt wurde, heißt SAIL-POD 25.
Velettrica hat sich zum Ziel gesetzt, energieeffiziente Antriebssysteme zu entwickeln, die hauptsächlich aus erneuerbaren Quellen gespeist werden, um die Verschmutzung der Meere zu verringern. Das Herzstück der Innovation von Velettrica ist ein Multifunktionspropeller mit elektronischem Steuersystem, der nach einem biomimetischen Ansatz entwickelt wurde. Er ist nämlich von den Flossen des Walhais inspiriert. Wenn er nicht in Betrieb ist, schließt sich dieser Propeller in einer blumenartigen Form, wodurch der Wasserwiderstand minimiert und die Energieeffizienz des Antriebssystems optimiert wird.
3DN: Können Sie uns mehr über den SAIL-POD 25 Motor erzählen? Wie wurde die additive Fertigung bei seiner Herstellung eingesetzt?
Wir haben den 3D-Druck für mehrere Komponenten des SAIL-POD 25 verwendet, in einigen Fällen wurden die endgültigen Teile direkt hergestellt, in anderen Fällen wurde Rapid Prototyping verwendet, um die Formen oder Kerne für den Verbundstoff herzustellen. Es handelt sich um ein hocheffizientes elektrisches Antriebs- und Aufladesystem für Segelboote mit einem Faltpropeller mit verstellbarer Steigung. Es ist einfach zu installieren, nimmt keinen Platz im Boot ein und ist umweltfreundlich und wartungsfrei. Außerdem verursacht es weder Lärm noch Vibrationen oder Hitze.
Das von Velettrica in Italien entwickelte Unternehmen 3DiTALY hat einige Komponenten für einen funktionierenden Prototyp des Triebwerks 3D-gedruckt und dabei verschiedene Materialien und Drucktechnologien kombiniert. Der SLS Fuse 1-Drucker von Formlabs und das Material Nylon 12 Powder wurden verwendet, um den Kern der Propellerblätter herzustellen: ein thermoplastischer Kunststoff, der aufgrund seiner hohen Zugfestigkeit und Umweltstabilität für die Herstellung komplexer Baugruppen und langlebiger Komponenten mit minimaler Wasseraufnahme geeignet ist. Der erste Prototyp der Propellernabe für den Trockentest wurde dagegen aufgrund seiner komplexen Form mit dem Formlabs Form 3L SLA-Drucker und Grey Resin hergestellt, um einen hohen Detailgrad, eine glatte, matte Oberfläche und optimale mechanische Eigenschaften zu erzielen. Die „speziellen“ mechanischen Teile schließlich werden mit der DMLS-Technologie aus Inconel oder Aluminium hergestellt und die Flossenform wird mit der SLS-Technologie aus einem HDT-Photopolymer gefertigt.
3DN: Warum haben Sie sich für den 3D-Druck entschieden und welche Vorteile bietet dieser für Sie?
Bei vielen Bauteilen war es eine zwingende Entscheidung, da die patentierte Mechanik so „beispiellos“ und komplex ist, dass es unmöglich oder übermäßig teuer gewesen wäre, sie mit herkömmlichen Technologien herzustellen.
Im Einzelnen bietet der 3D-Druck zahlreiche Vorteile, wie z. B. die Möglichkeit der schnellen Herstellung von Prototypen in weniger als 24 Stunden, Kostensenkungen von bis zu 90 % im Vergleich zur maschinellen Bearbeitung, die Herstellung von komplexen Teilen wie Propellern, Laufrädern und Turbinenschaufeln für Unterwassergeräte; die Möglichkeit, fortschrittliche Werkstoffe mit attraktiven Eigenschaften wie Feuerbeständigkeit, Verringerung der Schadstoffemissionen und Korrosionsbeständigkeit zu verwenden; und schließlich die Produktion auf Abruf, die es den Konstrukteuren ermöglicht, Teile genau dann und dort zu erhalten, wo sie benötigt werden, wodurch die Lagerkosten, das Risiko der Überproduktion und die Umweltauswirkungen verringert und Effizienz und Nachhaltigkeit gefördert werden.
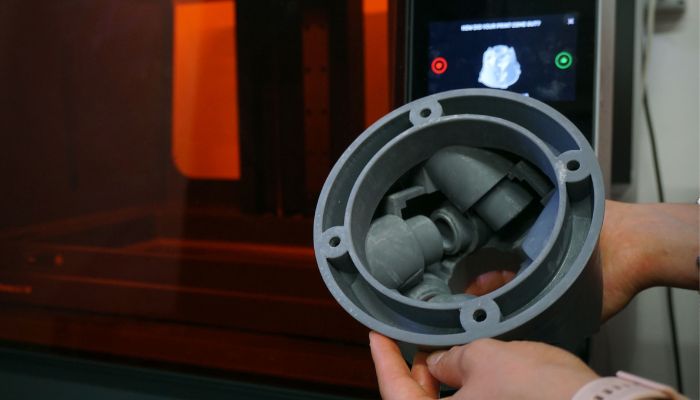
Ein Teil des Propellers wurde im 3D-Druckverfahren aus Harz hergestellt.
3DN: Wie sehen Sie die Rolle der additiven Fertigung im Marinesektor?
Der Marinesektor, insbesondere im Bereich der elektrischen Antriebe, ist häufig durch eine individuelle oder halbindividuelle Fertigung gekennzeichnet bzw. profitiert davon. Die additive Fertigung bietet, wie bereits erwähnt, große Freiheiten, da sie die Kosten für maßgeschneiderte Komponenten senkt. Darüber hinaus liegen die Vorteile im Hinblick auf die Nachhaltigkeit sowohl in der Einsparung von Rohstoffen und Energie bei der Produktion im Vergleich zu anderen Techniken als auch in der einfachen Wiederverwertung der verwendeten Materialien am Ende der Lebensdauer des Bauteils, vor allem bei Thermoplasten. Schließlich sind polymere Werkstoffe dem Bewuchsschutz wesentlich ähnlicher als Metalle, was z. B. bei Propellern eine geringere Dispersion von Chemikalien in die Umwelt und eine Aufrechterhaltung der Effizienz mit entsprechenden Energieeinsparungen ermöglicht.
3DN: Haben Sie noch abschließende Worte an unsere Leserschaft?
Wir haben viele Zukunftspläne und Träume. In der Zukunft wollen wir mit demselben Geist wie die Segelelektrizität fliegen, um den Himmel auf die nachhaltigste Weise zu durchqueren. Eine Botschaft an alle, die uns lesen: Nutzen Sie den 3D-Druck, um Ihre Ideen zu verwirklichen, er ist das Werkzeug, das Träume wahr werden lässt.
Was halten Sie von Velettrica? Lassen Sie uns dazu einen Kommentar da, oder teilen Sie es uns auf Facebook oder LinkedIN mit. Wenn Sie mehr zum 3D-Druck in der Automobilbranche lesen möchten, schauen Sie auf unserer Landing Page vorbei. Möchten Sie außerdem eine Zusammenfassung der wichtigsten Neuigkeiten im 3D-Druck und der additiven Fertigung direkt und bequem in Ihr Postfach erhalten? Dann registrieren Sie sich jetzt für unseren wöchentlichen Newsletter.
*Bildnachweise: Velettrica