Geschaffen, um zu bleiben: Wie URWAHN durch disruptives Design und 3D-Druck nachhaltige E-Bikes herstellt
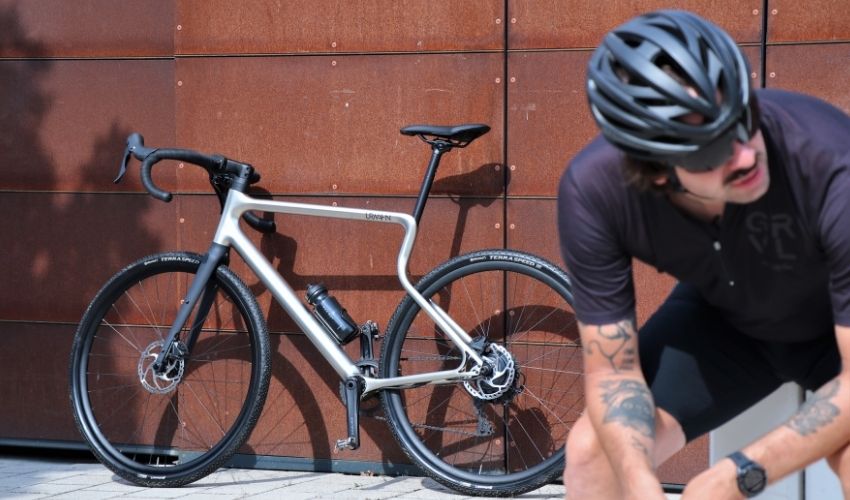
Seit 2013 steht URWAHN für faire und funktionale Mobilität. Der deutsche Fahrrad-Hersteller führt derzeit drei Hauptmodelle im Sortiment, die im Design und ihrer Funktionalität die jeweiligen Namensgebungen widerspiegeln: STADTFUCHS, WALDWIESEL und STRAßENFALKE. Alle diese Hightech-E-Bikes sind leicht, smart und maßgeschneidert. Außerdem kommen einige der Komponenten aus dem 3D-Drucker. Design, Funktion, Performance und Komfort sind bei URWAHN eng miteinander verkettet. Die ganze Produktentwicklung steht im Zeichen der Humanzentrierung, des Integrated Design Engineering und bricht mit Konventionen. So kam es auch zum einzigartigen Softride-Rahmen, dem typischen „Rahmen mit dem Knick“, bei dessen Produktion URWAHN auf additive Fertigung setzt. Er ist robust, komfortabel, facettenreich und durch sein modulares Design an unterschiedliche Bedürfnisse anpassbar, was die Produktlebensdauer erhöht. URWAHN holt das Beste aus den modernen Technologien und Materialien heraus und verfolgt eine nachhaltige Strategie. Zusammen mit dem Design sollen Langlebigkeit und Leistung der Produkte erzielt werden. Die Bikes sind geschaffen, um zu bleiben. Im Interview gibt Gründer Sebastian Meinecke preis, wie es zu URWAHN kam, warum er stets mit einer disruptiven Denkweise an Dinge herangeht und wie der 3D-Druck bei den URWAHN-E-Bikes und in der Fahrradbranche mitmischt.
3DN: Könntest du dich und URWAHN kurz vorstellen und erzählen, wie du zum 3D-Druck gekommen bist?
Hallo, ich heiße Sebastian Meinecke und bin Mitgründer von URWAHN. Die Idee für URWAHN entstand schon während meines Bachelorstudiums, im Sport- und Technikstudium mit Schwerpunkt Produktentwicklung und Integrated Design Engineering. Ich habe mir während dieser Zeit schon Gedanken gemacht, wie moderne urbane Fortbewegung funktionieren könnte, was praktisch ist im Sportkontext und wie die Mobilität der Zukunft aussieht. Damals lagen puristische Bikes ganz im Trend, also Fahrräder für den urbanen Gebrauch, die mit wenigen Komponenten auskommen, inspiriert von der New Yorker Kurier-Szene und dem Bahnradsport. Dieser Trend schwappte nach Deutschland über und bei einem lokalen Fahrradhersteller, der in dieser Richtung unterwegs war, konnte ich meine Bachelorarbeit verfassen und viel über diesen puristischen Ansatz in der Fahrradherstellung lernen.
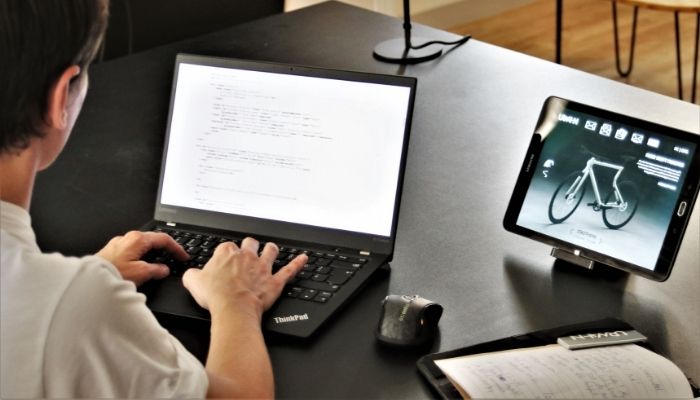
Wie sieht die moderne Mobilität der Zukunft aus? Diese Frage stellte sich Meinecke schon während des Studiums und begleitete ihn bei der Entwicklung von smarten, maßgeschneiderten E-Bikes.
Im Masterstudiengang habe ich das intensiviert und leidenschaftlich fortgesetzt, eigene Fahrräder individualisiert und in einer One-Man-Show dann eine Firma gegründet, SME Bicycles. Das hat im Keller meiner damaligen Zweiraumwohnung angefangen und dort habe ich dann die Bikes meiner Kunden nach individuellen Wünschen refurbished. Mein Ziel war und ist immer, Dinge anders zu denken und eine disruptive Denkweise hineinzubringen. Ich habe mir Fragen gestellt, wie man ein Fahrrad bedürfnisorientiert denken kann und Technologie, Design, Wertschöpfung und Nachhaltigkeit unter einen Hut bringt. An der Uni hatte ich Zugang zum Fabrication Laboratory und kam so mit FDM und SLA in Berührung. Beeindruckt von der disruptiven DNA dieser Technologien, habe ich mir gesagt, es wäre doch cool, den 3D-Druck unter ökonomischen, ökologischen Gesichtspunkten in die Fahrradproduktion mit reinzubringen, um dem Fahrrad noch mehr Freiheit und Flexibilität zu geben. Dies auch durch die Konstruktion des Rahmens, so wurden wir der typische „Rahmen mit dem Knick“. In meiner Masterarbeit habe ich den ganzen Produktzyklus durchlaufen, sodass ich einen konkreten Businessplan hatte. Damit bin ich direkt in die Vorgründerphase gestartet, um das Ganze zur Serienreife zu bringen. Durch den EU-Gründungstransfer kam auch ein Förderbetrag hinzu und nach zwei Jahren kam es dann Ende 2017 zur erfolgreichen Gründung von URWAHN, zusammen mit meinem heutigen Geschäftspartner Ramon Thomas.
3DN: Wie setzt ihr bei URWAHN den 3D-Druck für die Bikes ein? Auf welche Technologien und Materialien setzt ihr dabei?
Wir sind sehr stark inspiriert worden von den Stahlelementen im klassischen Fahrradbau, wo die Rohrelemente mit Muffen versehen waren und es keine Verbindungselemente gibt. Den Ansatz der Gliederung fanden wir sehr interessant, gleichzeitig war 3D-Druck so teuer, dass wir den Rahmen nicht als Ganzes in AM denken konnten. Der 3D-Druck war uns allerdings von Anfang an ein Anliegen, aber auch eine Herausforderung, wo wir immer wieder ein bisschen zurückgeworfen wurden. Zu Beginn haben wir mit Prototypen und Funktionstypen durch LPBF und SLM experimentiert. Allerdings kam es durch die unerwartet hohen Kosten schnell zur ersten Ernüchterung. Durch Abstecher beim Feinguss und einige Umwege sind wir schlussendlich wieder Richtung LPBF gegangen.
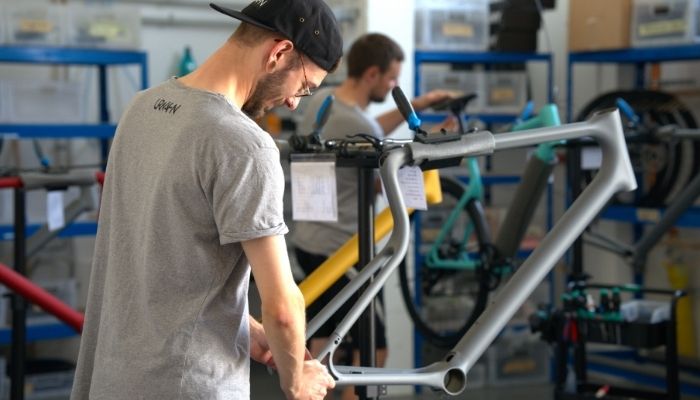
Das Rahmendesign orientiert sich am puristischen, klassischen Fahrradbau. Bei der Herstellung setzt URWAHN auf 3D-Druck.
Wir haben insgesamt schon mit diversen Technologien gearbeitet. Klassischerweise mit FDM-Techniken, SLA, SLS – aber unser Schwerpunkt liegt heut klar auf LBPF und High-Speed-Sintering mit Voxeljet, womit wir Stahl 1.2709 im LPBF und GA12 sowie TPU im HSS für den Rahmen verarbeiten. Heute besteht unser Rahmen aus sieben Bauteilen, kommt aber ästhetisch gegliedert und formgeschlossen daher. Alle Freiformen kommen aus dem 3D-Druck.
Mit Kunststoffen haben wir ebenfalls experimentiert. Wir suchen immer nach zusätzlichen Möglichkeiten, den 3D-Druck zu forcieren und zum Beispiel Sattel und Griffeinheiten zu drucken. Das testen wir auch schon und werden die Showcase-Elemente zusammen mit Voxeljet auf der formnext 2023 präsentieren.
3DN: Welche Vorteile bietet der 3D-Druck für euer Unternehmen und allgemein für die Fahrradbranche?
Der 3D-Druck hat uns erstmal mehr Freiheiten geboten, um das Produkt in der Gestaltung anders zu konzipieren und Leichtbau zu betreiben. Unser Rahmen ist heute gerade mal so schwer wie ein moderner Aluminium-Rahmen, ist elastisch und weist eine Optik auf, die mit einer Monocoque-Bauweise in Carbon vergleichbar ist. Durch den 3D-Druck ist es uns auch möglich, local sourcing, sprich local manufacturing zu betreiben. Wir produzieren hier am Standort und sind dadurch sehr nachhaltig und reaktionsschnell. Dank 3D-Druck können wir Bedürfnisanforderungen schnell und unkompliziert umsetzen und auf Trends reagieren. Auf der Liquiditätsseite haben wir viel mehr Handlungsspielräume und können uns nahe am Markt, am Kunden bewegen. Das haben wir deshalb geschafft, weil wir auf additive Fertigung setzen. Unser Rahmen ist, was die Wertschöpfung und die Materialien betrifft, zu 100% Made in Germany, darauf sind wir besonders stolz.
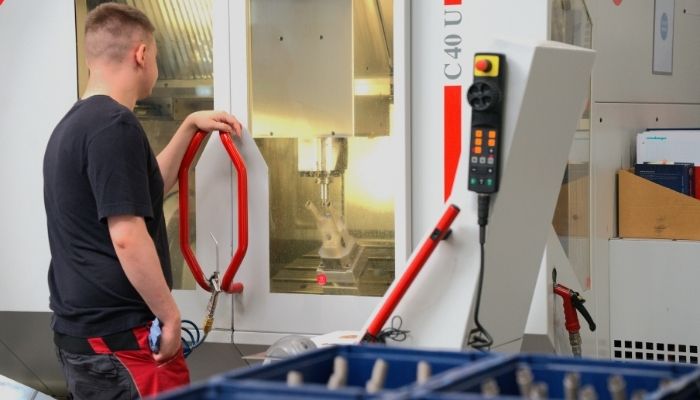
Der 3D-Druck eröffnet Design-Freiheiten und die Verarbeitung von leichten Materialien.
3DN: Das Thema Nachhaltigkeit spielt bei URWAHN ja eine große Rolle. Was haben 3D-Druck und Nachhaltigkeit für dich miteinander zu tun? Kannst du auf Projekte eingehen, die ihr dazu umgesetzt habt?
Wir verfolgen da eher einen globalen Ansatz und denken weniger in Projekten. URWAHN wurde mit der Prämisse gegründet, Wertschöpfung wieder nach Deutschland zu bringen. Das haben wir dadurch geschafft, dass wir auf kurze Transport- und Kommunikationswege setzen, indem wir in einem geringen Aktionsradius agieren, derzeit zirka 200 km. Unsere Lager sind im Vergleich zu anderen auch sehr klein und überschaubar, was uns eine bedarfsgerechte Produktion in nachhaltiger Ausrichtung garantiert. Wir produzieren nach Auftragslage, also on demand.
Um Verpackungen – und letztendlich Müll – zu vermeiden, haben wir für den Versand spezielle Boxing Systeme entwickelt, die ausgefüttert sind und mit denen wir in Zyklen fahren. Wir arbeiten also im Kreislaufsystem und wenn wir eine Auslieferung tätigen, können wir gleichzeitig fertige Erzeugnisse bei einem anderen Partner abholen. Unsere gesamte Logistik ist zyklisch, im Kreislauf, konzipiert.
Diesen zyklischen Gedanken haben wir auch im Produktdesign selbst mit eingebracht, begründet durch den 3D-Druck. Unser Rahmen ist etwa modular gedacht. Wenn beispielsweise jemand heute in der Stadt wohnt und den STADTFUCHS als Urban E-Bike fährt, aber in einem Jahr aufs Land zieht, haben sich seine Bedürfnisse an ein Fahrrad geändert. Wir können das Fahrrad dann so upgraden, dass es den gleichen Rahmen hat und den neuen Bedürfnissen entspricht. Wenn der Rahmen beschädigt ist, nehmen wir ihn zurück, behandeln ihn je nach Problemstellung und bringen ihn wieder in den Produktkreislauf.
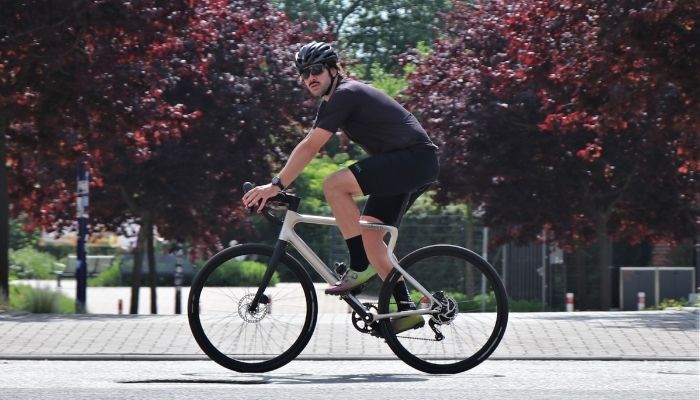
Der modulare Rahmen kann je nach Bedürfnissen angepasst werden. Der STADTFUCHS kann so in ein Gravel umfunktioniert werden.
Natürlich betreiben wir auch Recycling auf allen Ebenen, so auch in der Produktion. Ausschussteile gehen bei uns in die Sekundärverwertung. Wir versuchen, überall eine Verwertungsstrategie zu verfolgen. Wenn zum Beispiel Anbauteile eine Beschädigung erlitten haben, montieren wir diese auf Vorführer-Modellen oder auf Refurbish-Bikes. Nachhaltigkeit und 3D-Druck gehen bei uns Hand in Hand.
3DN: Wie wird die additive Fertigung deiner Meinung nach die Fahrradherstellung in den nächsten 10 Jahren beeinflussen?
Ich merke schon jetzt, dass sich immer mehr Fahrradhersteller dem 3D-Druck zuwenden. In erster Linie, um Prototypen zu erstellen und Entwicklungsprozesse zu beschleunigen. Aber natürlich setzen sich auch viele damit auseinander, unter welchen Bedingungen 3D-Druck und Serienfertigung vereinbar sind. Aus ökonomischen Gründen wagen sich viele Hersteller noch nicht daran, den 3D-Druck zu integrieren, weil man den 3D-Druck sehr konstruktiv mit eindenken muss, damit man bessere Effekte hat. Wir haben das zum Glück schon sehr früh gemacht. Hinzu kommt, dass die Maschinen und 3D-Druck-Prozesse noch sehr teuer sind. Der 3D-Druck wird als höchstflexibel und freiheitsgeben aufgezeigt, letztendlich, ist es aber so, dass auch der 3D-Druck standardisiert mit höchstmöglicher Auslastung laufen muss, um ökonomisch gute Preise zu erzielen.
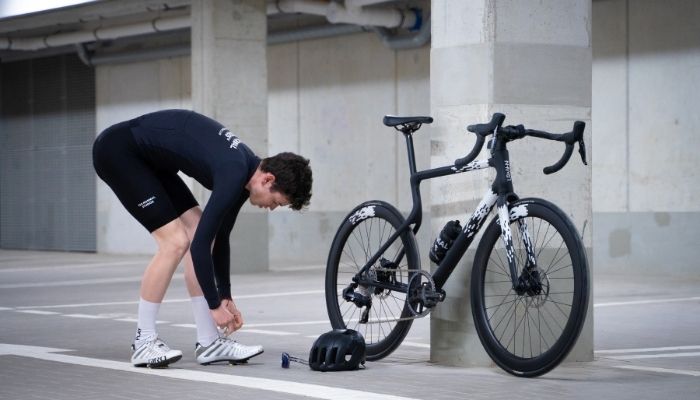
3D-Druck und Fahrradherstellung werden in Zukunft immer mehr verkettet sein. Die additive Fertigung bietet Vorteile für Design und Funktion.
Das Fahrrad ist eines der ältesten Fortbewegungsmittel, die es gibt und dementsprechend altbewährt ist auch die Herstellungsweise. Es ist notwendig, dass es da zum Umdenken kommt, was sich glücklicherweise bereits abzeichnet. Ich glaube, in den nächsten fünf bis zehn Jahren wird da Bewegung reinkommen. Der Trend geht stark in Richtung local manufacturing und das könnte den 3D-Druck zusätzlich befeuern. Additive Manufacturing ist definitiv ein Zukunftsthema in der Fahrradbranche. Ich denke aber trotzdem, dass der 3D-Druck dem mittleren und hohen Preisebenen an Herstellern vorbehalten sein wird, weil sich die Technologie dann doch nicht so schnell entwickelt.
3DN: Hast du noch ein abschließendes Wort an unsere Leserschaft?
„Think outside the frame“ ist mein Leitmotiv und das kann ich jedem empfehlen. Es ist wichtig, ständig über den Tellerrand hinauszuschauen und Türen, die sich schließen, als Chancen wahrzunehmen. Man muss den Blick einfach stets nach vorne richten und auch auf diejenigen, die das Produkt letztendlich konsumieren. Bei URWAHN schauen wir zuerst immer auf die Nutzer, dann auf die Stakeholder und auf die Wertschöpfung mitsamt der Entwicklung, um unsere Prozesse effektiv im nachhaltigen Kontext ausführen können. Mehr zu URWAHN finden Sie HIER.
Was halten Sie vom disruptiven Ansatz von URWAHN? Hatten Sie bereits Gelegenheit ein E-Bike des deutschen Herstellers zu testen? Lassen Sie uns gerne einen Kommentar da, oder teilen Sie es uns auf Facebook oder LinkedIN mit. Möchten Sie außerdem eine Zusammenfassung der wichtigsten Neuigkeiten im 3D-Druck und der additiven Fertigung direkt und bequem in Ihr Postfach erhalten? Dann registrieren Sie sich jetzt für unseren wöchentlichen Newsletter.
*Bildnachweise: URWAHN