Die besten 3D-Druck Anwendungen in der Luftfahrt
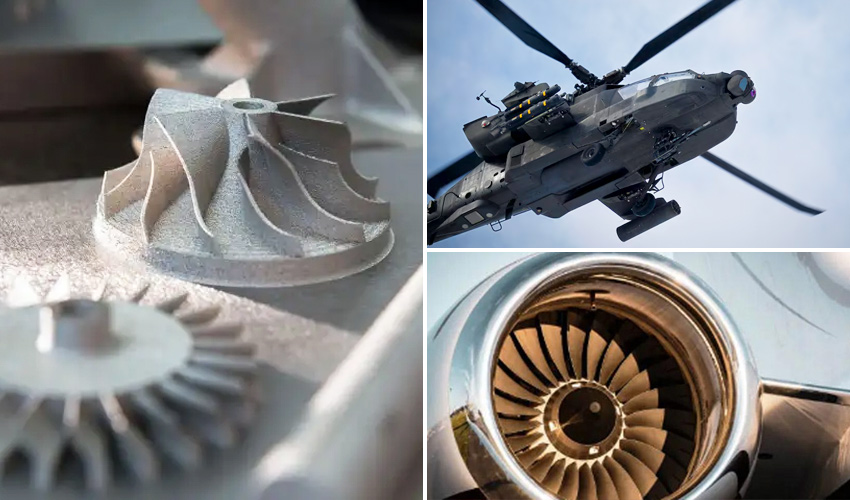
Die additive Fertigung eignet sich hervorragend für die Herstellung leichter, stabiler und geometrisch komplexer Teile – daher ist diese Technologie besonders wertvoll für den Luftfahrtsektor, wo Festigkeits- und Gewichtsoptimierung entscheidend sind. Die Luftfahrt ist die Wissenschaft und Praxis der Entwicklung, des Baus und des Fliegens aller Flugzeuge, mit Ausnahme derer, die ins All fliegen. Dieser Sektor gehörte zu den ersten Anwendern von AM und nutzte es zunächst für das Rapid Prototyping. Heute haben sich die Anwendungen jedoch auf Endverbrauchsteile in Flugzeugen, Hubschraubern, Drohnen und mehr ausgeweitet. Um die Vielseitigkeit und den Einfluss des 3D-Drucks in diesem Bereich zu verdeutlichen, haben wir eine Liste einiger der jüngsten und bemerkenswertesten Anwendungen von AM in der Luftfahrt zusammengestellt.
Norsk Titanium liefert Teile für die Boeing 787 und startet neue Lieferantenpartnerschaft
Norsk Titanium US Inc., ein führendes Unternehmen im Bereich der additiven Fertigung mit Titan und in der Luft- und Raumfahrtindustrie tätig, lieferte bereits 2021 Teile für die Boeing 787 Dreamliner. Bekannt ist Norsk vor allem für seine patentierte Rapid Plasma Deposition®-Technologie, die die Festigkeit und Haltbarkeit des fertigen Teils verbessert und ähnlich wie Directed Energy Deposition (DED) funktioniert. Im Gegensatz dazu nutzt Norsk jedoch einen Elektronenstrahl, der es ermöglicht, das Pulver an mehreren Stellen gleichzeitig zu erhitzen. Zu den hergestellten Teilen gehörten 3D-gedruckte Titankomponenten, die von der FAA (Federal Aviation Administration) zertifiziert wurden. Nun hat das Unternehmen eine Vereinbarung zur direkten Lieferung von Serienproduktionsteilen an The Boeing Company getroffen, was den Beginn einer direkten Lieferantenbeziehung markiert. Norsk Titanium rechnet damit, bis 2025 Hunderte von Strukturteilen bereitzustellen. „Unsere RPD®-Technologie und etablierten Materialspezifikationen versetzen Norsk Titanium in die Lage, schnell auf die Anforderungen unserer Kunden zu reagieren“, erklärt Nick Mayer, VP Commercial.
ITP Aero erhält EASA-Zertifizierung für 3D-Komponenten
Das in Vizcaya ansässige Unternehmen ITP Aero hat von der Europäischen Agentur für Flugsicherheit (EASA) und der staatlichen spanischen Agentur für Flugsicherheit (AESA) die Zertifizierung für 3D-gedruckte Strukturbauteile erhalten. Das Unternehmen ist das erste in der Triebwerksbranche, das diese Zulassungen für Teile erhalten hat, die mit selektivem Lasersintern (SLS) hergestellt wurden und für die hinteren Schaufeln des TP400-Triebwerks verwendet werden. Dieses industrielle additive Fertigungsverfahren ermöglicht die Herstellung komplexer Komponenten mit geringerem Material- und Energieverbrauch und trägt so zur Nachhaltigkeit des Sektors bei. Darüber hinaus hat ITP Aero eigene Standards und Spezifikationen für die additive Fertigung von Komponenten für Hochtemperatur-Flugzeugtriebwerke entwickelt. Das Unternehmen verfügt über eine eigene Fertigungszelle und baut das Forschungszentrum „ADMIRE“ auf, um digitale und nachhaltige Fertigungstechnologien weiter voranzutreiben.
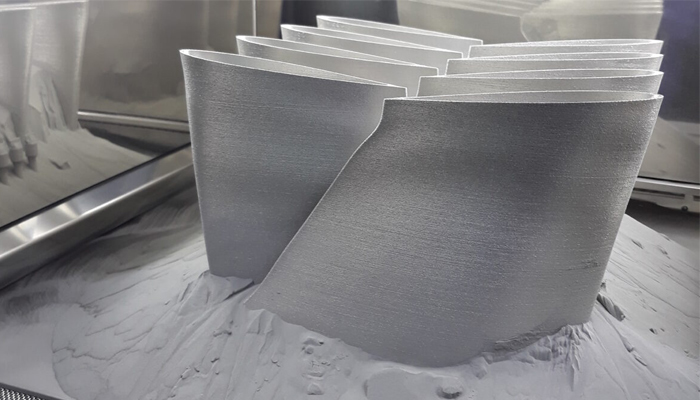
Bild: ITP Aero
Safran investiert 80 Millionen Euro in seinen 3D-Druck-Campus
Safran ist ein internationaler Hightech-Konzern, der in den Bereichen Luft- und Raumfahrt sowie Verteidigung tätig ist. Er hat 80 Millionen Euro investiert, um in Le Haillan in der Nähe von Bordeaux einen Campus für die additive Fertigung zu eröffnen. Ziel war es, ein großes Kompetenzzentrum für additive Fertigung zu schaffen. Der Campus, in dem rund 200 auf 3D-Druck spezialisierte Mitarbeiter beschäftigt sind, ist etwa 12.500 Meter groß. Er beherbergt mindestens acht 3D-Drucker mit Pulverbettfusionstechnologie, Endbearbeitungsgeräte, zwei Wärmebehandlungsöfen, ein Rasterelektronenmikroskop, ein metallurgisches Labor und ein Pulverlabor. Safran hat sich zum Ziel gesetzt, die additive Fertigung um 1 bis 25 % in seine Triebwerkskomponenten zu integrieren. Das Unternehmen hat bisher mehr als 1.000 3D-gedruckte Teile hergestellt und plant, im Jahr 2022 mehr als 4.000 Teile und im Jahr 2023 mehr als 8.000 Teile mit dieser Technologie zu produzieren. Diese Investition von Safran ist ein weiterer Schritt zur Stärkung der Zusammenarbeit zwischen europäischen Unternehmen, Forschungsinstituten und dem Verteidigungssektor und bringt sie näher an die massiven Investitionen der Vereinigten Staaten heran, die in diesem Sektor bisher noch dominieren.
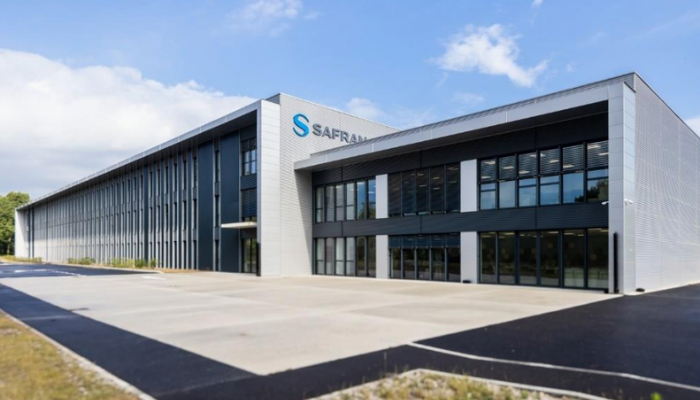
Bild: Safran.
Materialise entwickelt gemeinsam mit Partnern 3D-gedruckte Kabinenlösungen
Materialise hat seine Rolle im Bereich Wartung, Reparatur und Überholung (MRO) der Luft- und Raumfahrtbranche erweitert und arbeitet nun mit Proponent, dem weltweit größten Luft- und Raumfahrthändler, sowie Stirling Dynamics, einer führenden EASA 21.J-zertifizierten Designorganisation, zusammen, um 3D-gedruckte Kabinenlösungen zu entwickeln. Bereits zuvor hat Materialise in einer Partnerschaft mit Airbus und EOS erfolgreich 3D-gedruckte Teile für das A350-Flugzeug hergestellt, darunter rund 100 flammgeschützte Teile. Ziel der neuen Partnerschaft ist nun die Bereitstellung zertifizierter 3D-gedruckter Ersatzteile für die Luftfahrtindustrie. Stirling Dynamics konzentriert sich hierbei auf die Verbesserung von Designs für Kabineninnenteile, während Materialise seine zertifizierten Produktionskapazitäten nutzt. „Mit unserer gebündelten Expertise senken wir die Hürden für die Einführung von AM in der Luftfahrt und bieten zertifizierte Lösungen für den Ersatzteilmarkt“, erklärt Jurgen Laudus, Vice President von Materialise Manufacturing. Die Zusammenarbeit hat bereits mehrere Lösungen zur Kabinenreparatur hervorgebracht, die auf spezifische Probleme in Flugzeugkabinen abzielen. Insbesondere Proponent spielte hierbei eine Schlüsselrolle, indem es mit OEMs zusammenarbeitet, um diese Lösungen weltweit anzubieten.
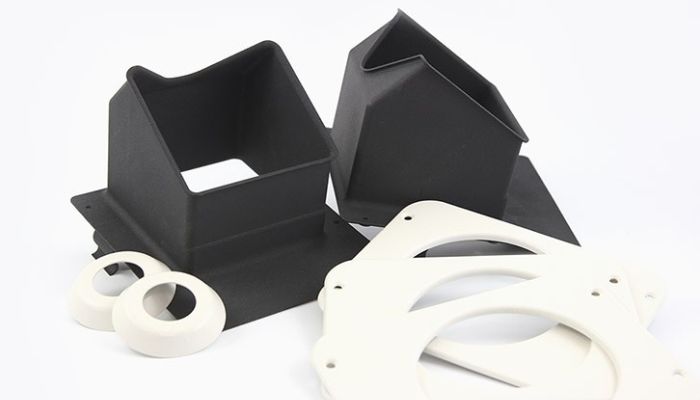
Flugtaugliche Teile aus dem flammgeschützten PA 2241 FR-Material, welches von Materialise in Airbus-zertifizierter Qualität angeboten wird. (Bild: Materialise)
Lufthansa nutzt 3D-Druck zur Herstellung von Kabinenteilen für ihre Flugzeuge
Lufthansa Technik, ein führender Anbieter von Wartungs-, Reparatur-, Überholungs- und Modifizierungsdienstleistungen für zivile Flugzeuge, nutzt nach eigenen Angaben die additive Fertigung von Polymeren sowohl für die Neugestaltung spezieller Kabinenteile als auch für die Reproduktion herkömmlicher Flugzeugteile. Lufthansa nutzt den 3D-Druck sogar für die individuelle Gestaltung von VIP-Kabinen. Die additive Fertigung wird aber auch eingesetzt, um herkömmliche Flugzeugkabinenteile stärker oder leichter zu machen. So hat sie bereits die Funktion von Lüftungsgittern, Clips und Abdeckungen für ihre Flugzeuge verbessert. Lufthansa plant, die additive Fertigung verstärkt zu nutzen, insbesondere im Hinblick auf den Einsatz von bionischem Design. Dabei handelt es sich um die Anwendung von biologischen Methoden auf 3D-Drucktechnologien. Nach Angaben des Unternehmens können Anpassungen des Kabinendesigns und Gewichtsreduzierungen durch AM einen wichtigen Beitrag zu den Bemühungen der Luftfahrtindustrie um mehr Nachhaltigkeit und eine geringere CO2-Bilanz leisten.
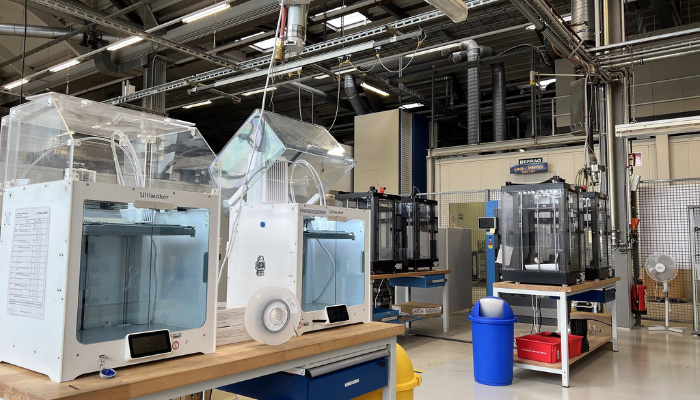
Bild: Lufthansa Group
Das 3D-Druckzentrum von Airbus Helicopters
Der 3D-Druck ist für Airbus kein Fremdwort, denn das Unternehmen baut schon seit Jahren 3D-gedruckte Teile in seine Flugzeuge ein. Oft hat das Unternehmen die additive Fertigung ausgelagert, aber Ende 2023 eröffnete Airbus Helicopters sein eigenes 3D-Druckzentrum am Standort Donauwörth, Deutschland, und erweiterte damit seine internen AM-Fähigkeiten. Das Zentrum verfügt über drei Maschinen für Titanteile, vier für Kunststoffteile und eine für Aluminiumteile. Airbus Helicopters nutzt die Technologie zur Herstellung von Serienteilen sowie von Teilen für Prototypen wie den CityAirbus NextGen eVTOL und den experimentellen Hochgeschwindigkeits-Verbundhubschrauber Racer. Stefan Thomé, Geschäftsführer von Airbus Helicopters in Deutschland, erläuterte die Vorteile des Einsatzes von AM. „Neben anderen Vorteilen kann der 3D-Druck das Gewicht von Flugzeugkomponenten reduzieren, was zu einem geringeren Treibstoffverbrauch führt“, sagte Thomé. „Ein solches Potenzial kann finanzielle Vorteile bringen und dazu beitragen, die CO2-Emissionen im Betrieb zu reduzieren.“
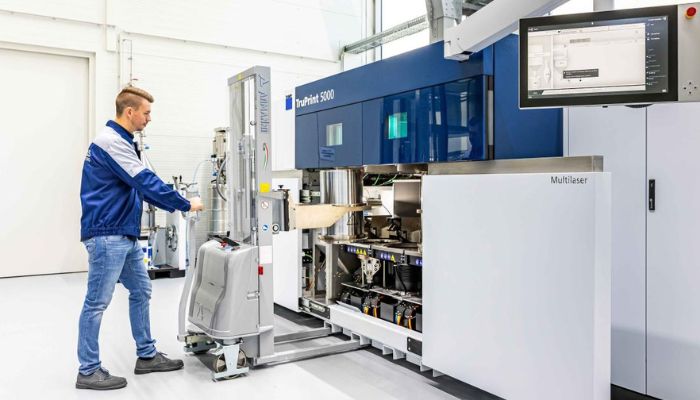
Bild: Airbus
3D-Rotoren für Apache-Hubschrauber von Boeing
Boeing hat mit dem Test eines kompletten 3D-gedruckten Hauptrotorsystems für den Kampfhubschrauber AH-64 Apache begonnen. Ziel dieses Projekts ist es, die Vorlaufzeiten zu verkürzen und die Lieferketten für normalerweise geschmiedete Teile zu verbessern. Auf der Jahreskonferenz der Association of the US Army stellten Boeing und ASTRO America ihr erstes 3D-gedrucktes Bauteil vor. Es handelt sich um ein Hauptrotorgestänge, das mit einem großformatigen 3D-Metalldrucker hergestellt wurde. Das von der Regierung finanzierte Unternehmen ASTRO arbeitet im Rahmen eines 95-Millionen-Dollar-Vertrags an der Entwicklung von additiven Fertigungsverfahren für große Teile wie Panzerhüllen. Eine 3D-gedruckte Hauptrotorkomponente wurde in acht Stunden hergestellt, verglichen mit einem Jahr, das es normalerweise dauern würde, sie zu schmieden. Boeing will damit groß angelegte Ermüdungstests durchführen, was die Reparatur von Flugzeugen beschleunigen und die Herstellung von Teilen optimieren könnte.
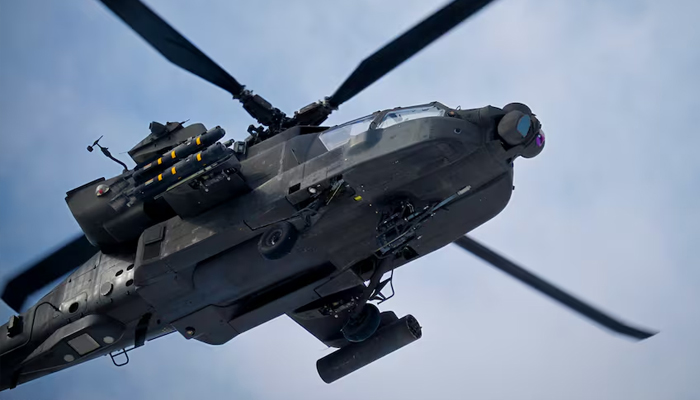
Bild: Boeing
Finnair verwendet 3D-gedruckte Teile in A320-Flugzeugen
Erinnern Sie sich an die Videotafeln, die in einigen Flugzeugen über den Sitzen angebracht sind? Viele Fluggesellschaften, darunter auch die finnische Fluggesellschaft Finnair, schaffen sie schrittweise ab. Das Unternehmen hat sie vor kurzem durch 3D-gedruckte Blanking-Paneele (Paneele, die ungenutzten Raum abdecken) in seinen Airbus A320-Kabinen ersetzt, um eine leichte Alternative zu den schweren Videoplayern zu bieten. Das Additive-Manufacturing-Unternehmen AM Craft fertigte über 300 Blanking Panels, um 17 der A320-Flugzeuge von Finnair aufzurüsten. Laut Finnair hat der 3D-Druck der Paneele dazu beigetragen, überschüssige Lagerbestände zu minimieren und die mit der herkömmlichen Lieferkette verbundenen Kosten zu senken. Wie Aviation Week berichtet, wurden die Verkleidungen so konzipiert, dass sie mit den vorhandenen Montageschienen zusammenarbeiten und somit leicht zu installieren sind. Darüber hinaus kann jede Fluggesellschaft mit A320-Flugzeugen von diesem 3D-Druckprojekt profitieren, da die Verkleidungsplatten im digitalen Katalog von AM Craft erhältlich sind.
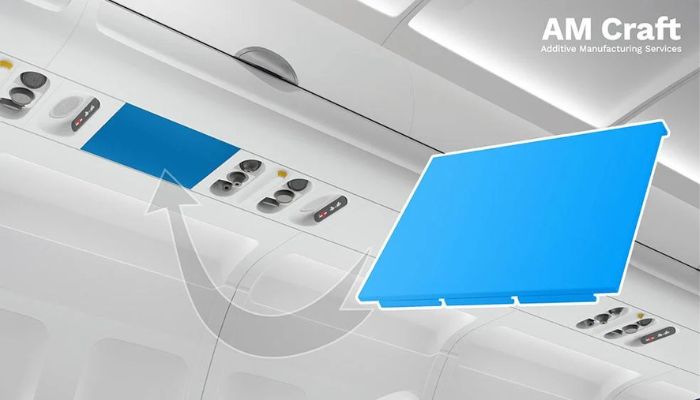
Bild: AM Craft
Liebherr-Aerospace Lindenberg GmbH produziert 3D-gedruckte Flexwelle
Liebherr-Aerospace Lindenberg GmbH, ein Unternehmen, welches integrierte Systeme für die Luftfahrtindustrie fertigt, hat nun eine flexible Flexwelle für Luftfahrtanwendungen im additiven Schichtbauverfahren (ALM) entwickelt. Traditionell besteht diese aus sieben Bauteilen, die mittels aufwendigen Prozessen miteinander verbunden werden müssen. Durch den Einsatz von 3D-Druck wird dieser Prozess vereinfacht, wodurch der Wartungsbedarf sinkt und die Produktion weniger komplex wird. Die aus Titanpulver 3D-gedruckte Flexwelle, die von Airbus und EASA für die Serienproduktion freigegeben wurde, soll im Differentialgetriebe des Klappensystems des Airbus A350 integriert werden. Sie überträgt hier Drehbewegungen auf einen Positionssensor und hilft, Winkel- und Achsenfehler zwischen Getriebe und Sensor auszugleichen. Die Zulassung der 3D-gedruckten Flexwelle unterstreicht, dass additive Fertigung eine zuverlässige Technologie für die Verbesserung der Nachhaltigkeit in der Luftfahrt darstellt. „Die Flexwelle zeigt, wie verschiedene Funktionen effizient in ein Bauteil integriert werden können, was den Weg für komplexere AM-Anwendungen in der Zukunft ebnet“, erklärt Svenja Pestotnik, Leiterin der additiven Fertigung bei Liebherr-Aerospace Lindenberg GmbH.
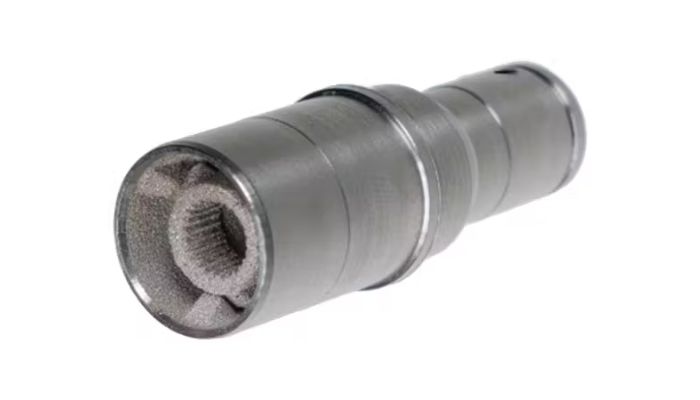
Die flexible Welle von Liebherr-Aerospace weist eine komplexere Bauweise auf und wird aus Titanpulver unter Verwendung der additiven Fertigungstechnik produziert. (Bild: Liebherr-Aerospace Lindenberg GmbH)
LEAP und die additive Fertigung
Es ist schwer, an LEAP vorbeizukommen, wenn man über Luft- und Raumfahrt und 3D-Druck spricht. Er wurde von CFM International, einem Gemeinschaftsunternehmen von GE Aerospace und Safran Aircraft Engines, entwickelt und ist ein Antriebssystem für Verkehrsflugzeuge (wie den Airbus A320neo oder die Boeing 737 MAX), das 2016 auf den Markt gebracht wurde. Seine ursprünglichen Ziele waren die Senkung der Treibstoffeffizienz, der CO2-Emissionen sowie der Lärmbelastung. Kurz vor seinem zehnten Geburtstag hat der LEAP laut CFM seine Versprechen gehalten. Aber was uns interessiert, ist natürlich der 3D-Druck. Das Antriebssystem wurde zum Teil mithilfe additiver Fertigungsverfahren entwickelt, insbesondere die Turbinengehäuse, die Düsenspitzen und die Kraftstoffeinspritzdüsen. Dabei wurde ein Laserschmelzverfahren auf einem Pulverbett bevorzugt.
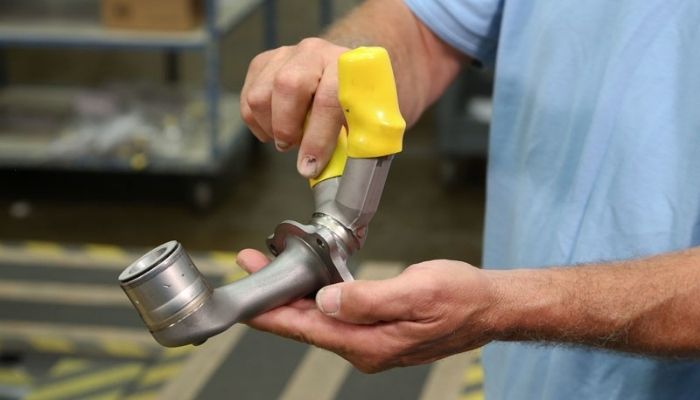
Bild: GE
Marines machen die Wartung der F-35B Lightning II-Reibahle effizienter
Die Marine Aviation Logistics Squadron 13 hat die Aufgabe, die Marinefliegergruppe logistisch zu unterstützen, z. B. durch die Bereitstellung von Personal und Ersatzteilen. Im Juli 2024 sah sich MALS-13 jedoch mit einem kritischen Mangel an Reibahlen für die F-35B Lightning II Geschwader konfrontiert. Dabei handelt es sich um wichtige Präzisionsschneidewerkzeuge für die Instandhaltung der Luftfahrt. Herkömmliche Reibahlen waren teuer und MALS-13 verfügte aufgrund langer Beschaffungsfristen nicht über ausreichende Mengen. Dank der additiven Fertigung konnten sie durch die Entwicklung von Hochleistungsreibahlen eine Lösung auf Abruf schaffen. Dadurch konnten sie nicht nur die Wartungskosten um mehr als 50 Prozent senken, sondern auch die Beschaffungszeiten verkürzen. Die Teile waren nicht mehr drei Monate lang verfügbar, sondern konnten noch am selben Tag produziert werden. Um die fehlenden Reibahlen nachzubilden, wurden zwei Markforged X7 Industrie-3D-Drucker angeschafft, die es MALS-13 ermöglichten, die für die Luft- und Raumfahrt geeigneten Komponenten im eigenen Haus zu produzieren und damit die Abhängigkeit von externen Lieferanten zu beseitigen.
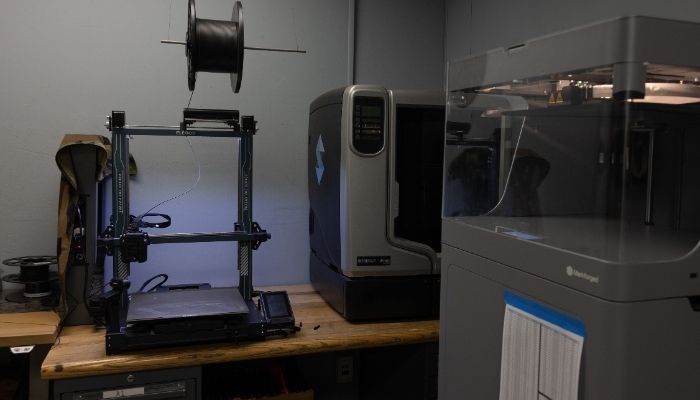
Bild: Lance Cpl. Elizabeth Gallagher
Die Drohne Titan Falcon
Wenn man über Luft- und Raumfahrt spricht, kommt man nicht an unbemannten Luftfahrzeugen vorbei, die allgemein als Drohnen bezeichnet werden. Unabhängig davon, ob sie für Forschungszwecke, militärische Zwecke oder für die Forschung eingesetzt werden. – Es gibt immer mehr von ihnen und sie können 3D-gedruckte Teile integrieren. Dies ist auch bei der Titan Falcon der Fall, die von Titan Dynamics entwickelt wurde. Er hat eine Flugdauer von 6 Stunden und eine Reichweite von 400 Kilometern, wodurch er ein großes Gebiet abdecken kann. Mit einer Kamera ausgestattet, ist er eine ideale Lösung zur Überwachung von Schlachtfeldern – er wurde sogar im Konflikt zwischen der Ukraine und Russland eingesetzt. Was die additive Fertigung angeht, bleibt das Unternehmen hinsichtlich der verwendeten Materialien und Technologien geheimnisvoll, aber sicher ist, dass sie die Zeit verkürzt und Iterationen erleichtert hat.
Conflux fertigt Wärmeaustauscher per 3D-Metalldruck
Conflux hat es sich zur Aufgabe gemacht, mithilfe des 3D-Drucks einen Beitrag zur modernen Luftfahrt zu leisten. Diese sieht sich mit der Aufgabe konfrontiert, für mehr Leistung und Zuverlässigkeit zu sorgen. Conflux fertigt Wärmeaustauscher für Flugzeuge per 3D-Metalldruck, um komplexere Geometrien zu realisieren und so die Leistung der Wärmeaustauscher zu optimieren. Dies trägt zur Gesamtperformance des Flugzeugs bei. Einerseits kann das Gesamtgewicht durch Leichtbaukomponenten reduziert werden, andererseits schlägt sich ein effizientes Wärmemanagement direkt in der Leistung und Reichweite eines Flugzeuges nieder.
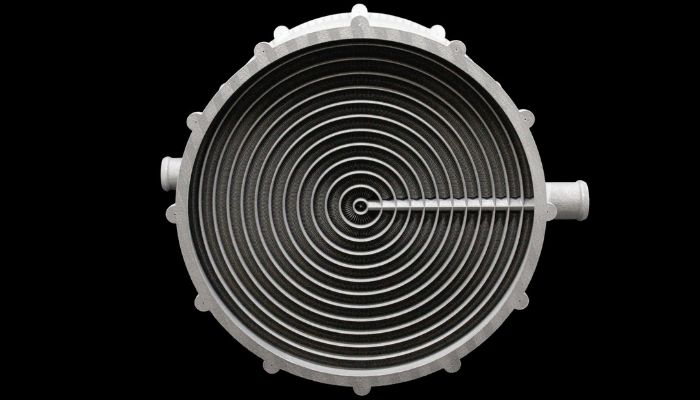
Bild: Conflux
3D-gedrucktes Hubschrauber-Cockpit für einen Full-Flight-Simulator
Murtfeldt Additive Solutions druckte 2024 im Auftrag von der Reiser Simulation and Training GmbH ein modular aufgebautes Helicopter-Cockpit. Dafür verwendete Murtfeldt mehrere Anlagen des großformatigen 3D-Druckers Queen 1 von Q.BIG 3D. Mithilfe des VFGF-Verfahrens (variable fused granulate fabrication) konnten die einzelnen Bauteile je 3D gedruckt werden und dann zügig zusammengebaut werden. Die längste Druckzeit eines einzelnen Bauteils betrug 100 Stunden, die Gesamtfertigung etwas mehr als einen Monat. Das Cockpit wiegt bei seinen Abmessungen von 2.260 mm x 1.780 mm x 17.05 mm „nur“ 200 Kilogramm. Der 3D-Druck mit Kunststoffpellets hat sich bei diesem Projekt als wertvoll erwiesen, um Leichtbauziele zu erreichen und wirtschaftlicher zu produzieren. Da in der traditionellen Fertigung für ein solches Projekt viele Werkzeuge anfallen, konnten die Kosten durch den 3D-Druck gedrosselt werden. Außerdem sind die Preise von Pellets für großformatige Drucke wesentlich interessanter als jene von Filament.
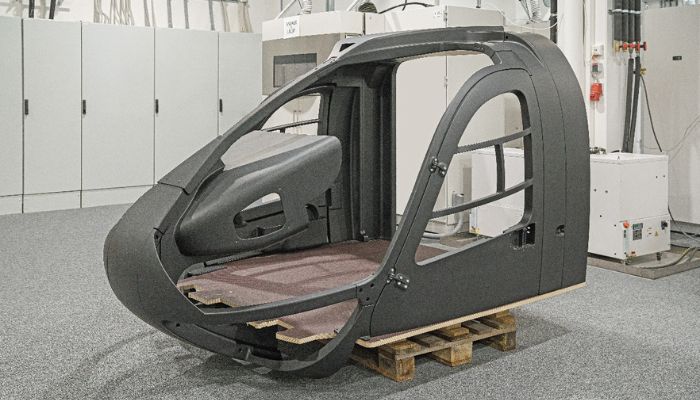
Bild: Q.BIG 3D
Partnerschaft zwischen BEAMIT und Leonardo Aircraft für Massenproduktion mit additiver Fertigung
Die italienische Leonardo-Gruppe ist einer der führenden internationalen Akteure bei der Realisierung von technologischen Fähigkeiten in den Bereichen Luft- und Raumfahrt, Verteidigung und Sicherheit. Das Unternehmen ist ein Technologiepartner von Regierungen, Verteidigungsbehörden, Institutionen und Unternehmen. Der Einsatz der additiven Fertigung in den Aktivitäten von Leonardo ist seit langem bekannt. In den letzten Jahren hat Leonardo, insbesondere im Bereich Aircraft, eine Partnerschaft mit dem BEAMIT-Service für die Massenproduktion verschiedener Komponenten mit der Additive Manufacturing Technologie in Metall erneuert, die bis mindestens 2028 aktiv sein wird. Bis heute verfügt Leonardo Aircraft über mehr als 100 qualifizierte Teile mit BEAMIT, die derzeit in wichtigen Flugzeugen wie der M345, M346 und C27J eingebaut sind.
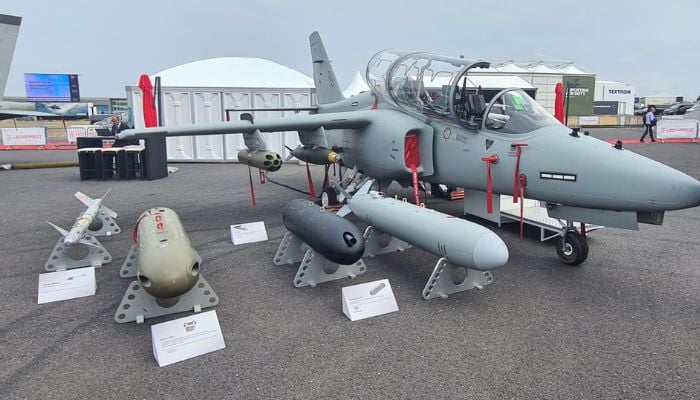
Leonardo M-345 (Bild: Italia Vola)
MIMOSA-Projekt zur Optimierung von Flugzeugen durch 3D-Druck
Das europäische Projekt MIMOSA, an dem verschiedene europäische institutionelle und unternehmerische Partner beteiligt sind, wurde 2022 ins Leben gerufen und soll den Flugzeugbau durch den gemeinsamen Einsatz von 3D-gedruckten Verbundwerkstoffen und Metallen verändern. Das Projekt zielt darauf ab, die nächsten Flugzeuggenerationen zu unterstützen, die zwangsläufig Produktionskriterien mit geringeren Umweltauswirkungen und einem geringeren Bedarf an Rohstoffen folgen müssen. Die Studie basiert auf der Realisierung von Multi-Material-Strukturen, die aus Metalllegierungen und Verbundwerkstoffen ohne Zwischenelemente bestehen, durch die Integration von additiver Metallfertigung, Plasma-Oberflächenbehandlung und Kohlenstofffasern. Am Ende des Dienstes können die mit der MIMOSA-Technologie hergestellten Strukturen durch einen „Zerstäubungs“-Prozess regeneriert werden, wodurch der Abfall reduziert wird und sie zu einem „sekundären“ Rohstoff für die additiven Herstellungsverfahren selbst werden.
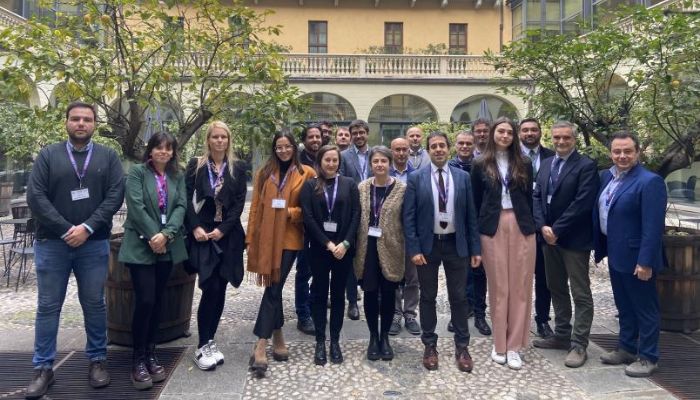
Das MIMOSA-Projektteam (Bild: Politecnico di Torino)
Was halten Sie von diesen Anwendungen des 3D-Drucks in der Luftfahrt? Lassen Sie uns dazu einen Kommentar da, oder teilen Sie es uns auf Facebook oder LinkedIN mit. Wenn Sie mehr zum 3D-Druck in der Luft- und Raumfahrt lesen möchten, schauen Sie auf unserer Landing Page vorbei. Möchten Sie außerdem eine Zusammenfassung der wichtigsten Neuigkeiten im 3D-Druck und der additiven Fertigung direkt und bequem in Ihr Postfach erhalten? Dann registrieren Sie sich jetzt für unseren wöchentlichen Newsletter.