TitanIEM: 3D-Druck für nachhaltige und günstige In-Ear-Monitore mit bester Audioqualität
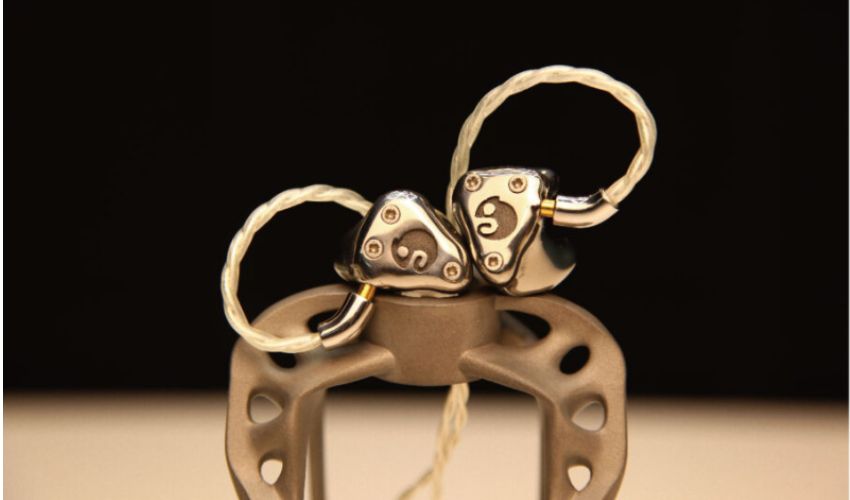
In der U-Bahn, im Flugzeug, beim Sport oder auf der Arbeit – überall tragen Menschen kabellose Ohrhörer oder Kopfhörer, um Geräusche zu dämpfen oder Musik und Podcasts in bester Qualität zu hören. Der Otto Normalverbraucher strebt nach einem optimalen Klangerlebnis und den feinsten Tönen, wie sie in der Audiobranche üblich sind. Neben dieser Professionalisierung der Unterhaltungselektronik spielt aber auch die Nachhaltigkeit eine immer bedeutendere Rolle in dieser Sparte. Aus diesem Grund haben BLT (Bright Laser Technologies), Earfit und Addpark ihre Kompetenzen gebündelt und TitanIEM entwickelt, einen 3D-gedruckten professionellen In-Ear-Monitor, der sowohl anpassbar als auch akustisch präzise und langlebig ist.
Üblicherweise werden IEMs durch herkömmliche Produktionstechnologien gefertigt. Dabei kommt es allerdings zu zahlreichen Herausforderungen: das komplexe Design ist schwierig umzusetzen, die Produktion dauert sehr lange und es fällt viel Abfall an. Darüber hinaus sind die Geräte aus Plastik und daher anfällig für Feuchtigkeit und Stöße. Deshalb entschieden sich BLT, Earfit und Addpark, die In-Ear-Monitore per 3D-Druck und aus Titan zu fertigen, denn die additive Fertigung ermöglicht die Umsetzung von individualisierten Designs und eine Produktion mit geringem Abfall, wobei die Möglichkeit der Serienproduktion besteht. Die Entscheidung für Titan rührt daher, dass es eine stabile Oberfläche aufweist und reine Audiosignale garantiert. Dies sorgt für einen sauberen Klang ohne unerwünschte Resonanzen.
Die Entwicklung von nachhaltigen In-Ear-Monitoren aus Titan
Ziel der Unternehmen war es, ein akustisch optimiertes Produkt zu erstellen, das einerseits langlebig und anpassbar ist, andererseits ressourcenschonend produziert wird. Die Ohrhörer sollten optimal auf die Anforderungen von Musikern, Tontechnikern und Akustikern eingehen und personalisierbar sein. Earfit entwickelte das Design, um die Optimierung der akustischen Eigenschaften zu erreichen. Dazu wurden spezielle interne Schallkanäle integriert, so können Klangnuancen um bis zu 30 % klarer wiedergegeben werden, als das bei Kunststoffgehäusen der Fall ist. Das Unternehmen zielte beim Design auch darauf ab, eine hohe individuelle Anpassung zu ermöglichen und das Gewicht der Ohrhörer zu reduzieren.
Im nächsten Schritt kommt der 3D-Druck ins Spiel. Die TitanIEMs wurden aus einer proprietären Titanlegierung von BLT gedruckt und von Addpark mit den Lösungen und der LB/M-Technologie (Laser Beam on Metal, PBF) von BLT gefertigt. Die Schichtdicke betrug unter 40 Mikrometer, um eine hohe akustische Präzision und Haltbarkeit zu gewährleisten. Außerdem wurden poröse Strukturen integriert, um die Resonanzfähigkeit zu erhöhen.
Das akustische Finetuning war nur ein Teil des Gesamtziels, der zweite Aspekt betraf die nachhaltige Produktion. Die Unternehmen verkündeten diesbezüglich interessante Ergebnisse. Verglichen mit herkömmlichen Ohrhörern konnte das Gewicht der TitanIEMs um 20 % gesenkt werden. Die Produktionszeit konnte auf die Hälfte reduziert werden und es konnten 20 % der Kosten eingespart werden. Auch fiel 50 % weniger Abfall an, indem der 3D-Metalldruck für die Herstellung herangezogen wurde. Mit diesen Resultaten wollen die drei Verbündeten neue Standards in der Unterhaltungselektronik setzen, bei denen leistungsstarke Produkte und ressourcenschonende Fertigung Hand in Hand gehen. Mehr zu den TitanIEMs finden Sie HIER.
Was halten Sie von den nachhaltigen TitanIEMs? Wir hoffen auf den weitere Erfolg des Projektes für 3D-gedruckte Haut! Lassen Sie uns dazu einen Kommentar da, oder teilen Sie es uns auf Facebook oder LinkedIN mit. Möchten Sie außerdem eine Zusammenfassung der wichtigsten Neuigkeiten im 3D-Druck und der additiven Fertigung direkt und bequem in Ihr Postfach erhalten? Dann registrieren Sie sich jetzt für unseren wöchentlichen Newsletter.