Titan vs Aluminium: Welches Metall eignet sich für den 3D-Druck?
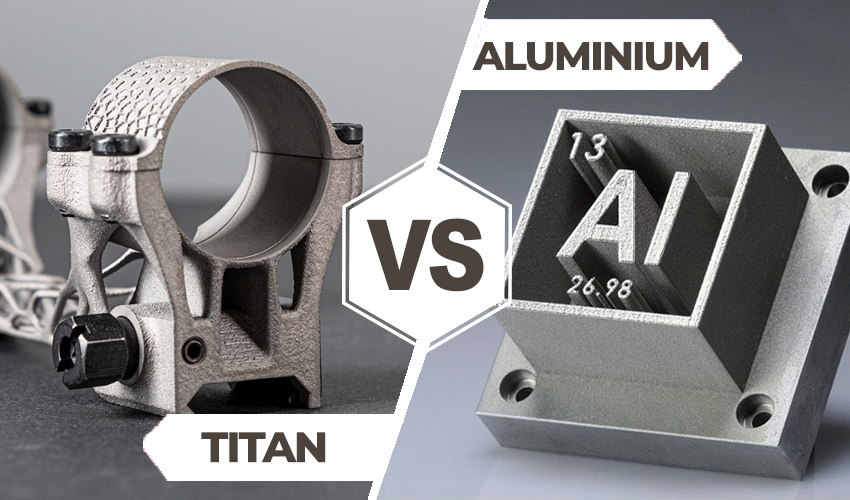
Metall ist derzeit neben Kunststoff einer der gefragtesten Werkstoffe für additive Fertigungsverfahren. Es überrascht nicht, dass seine hervorragenden Eigenschaften es zur idealen Wahl für die anspruchsvollsten Anwendungen in Bezug auf Leistung und Festigkeit machen. In diesem Artikel werden wir uns auf zwei der wichtigsten Metalle für den 3D-Druck konzentrieren: Titan und Aluminium. Diese werden hauptsächlich für Verfahren wie das Laserschmelzen (L-PBF) oder die direkte Energieabscheidung (DED) verwendet. Sie sind hauptsächlich in Pulverform erhältlich, wobei der Schwerpunkt auf dem industriellen Umfeld liegt. Wir werden ihre Gemeinsamkeiten und Unterschiede vergleichen, um einen tieferen Einblick in ihre Eigenschaften und Anwendungen zu gewinnen und die Vorteile zu verstehen, die sie in diesem Herstellungsverfahren bieten.
Herstellung und Eigenschaften
Titan
Titan ist ein metallischer Werkstoff, der in der Natur nicht als Element vorkommt und aus Erzen gewonnen werden muss, die entweder aus Rutil (TiO2) oder Ilmenit (FeTiO3) gewonnen werden können. Die Gewinnung von Reintitan ist ein komplexer Prozess, der mehrere Schritte umfasst. Die am weitesten verbreitete Methode zur Gewinnung von Reintitan ist die Kroll-Methode, die 1940 von dem amerikanischen Chemiker William J. Kroll entwickelt wurde. Bei dieser Methode wird Titandioxid (TiO2) mit Chlorgas (Cl2) reduziert, um Titantetrachlorid (TiCl4) zu erzeugen, das dann mit Magnesium (Mg) reduziert wird, um Titanmetall herzustellen. Die Kroll-Methode eignet sich zwar zur Herstellung von Reintitan, ist aber ein kostspieliger Prozess, der viel Energie erfordert. Außerdem ist es aufgrund der hohen Reaktivität von Titan schwierig, es als reines Metall zu erhalten, sodass eine Probe mit einem Reinheitsgrad von 99,9 % als handelsübliches Reintitan eingestuft wird. Aus diesem Grund wird es normalerweise in Kombination mit anderen Elementen verwendet, um eine Legierung zu bilden.
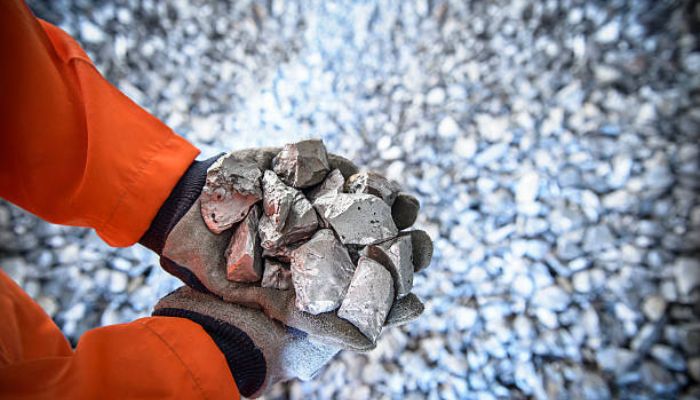
Bild: Getty Images
Titan hat zahlreiche Eigenschaften, die es äußerst vielseitig und in vielen Bereichen nützlich machen. Es wird häufig in Kombination mit anderen Elementen verwendet, um eine Legierung zu bilden, da es aufgrund seiner hohen Reaktivität nur schwer als reines Metall zu erhalten ist. Reines, extrahiertes Titan wird jedoch aufgrund seiner hohen Biokompatibilität in einigen Anwendungen geschätzt, z. B. in der medizinischen Industrie. Zu seinen wichtigsten Eigenschaften gehören eine hohe mechanische Festigkeit, eine geringe Dichte, eine ausgezeichnete Korrosionsbeständigkeit und Steifigkeit.
Die wichtigsten Titanlegierungen, die im 3D-Druck verwendet werden, sind die folgenden:
- Titan 6Al-4V, Grad 5: Es ist das wichtigste und gängigste Material. Es wird im 3D-Druck aufgrund seiner hohen Festigkeit und Haltbarkeit verwendet. Die Legierung besteht aus Titan, Aluminium und Vanadium und kann hohen Temperaturen und korrosiven Umgebungen standhalten.
- Titan 6Al-4V, Grad 23: Es ist biokompatibel und wird daher häufig für medizinische Implantate und Prothesen verwendet.
- Titan Beta 21S: Es hat eine höhere Festigkeit als herkömmliche Titanlegierungen und ist außerdem widerstandsfähiger gegen Oxidation und Verformung. Es eignet sich hervorragend für orthopädische Implantate und Anwendungen in der Luft- und Raumfahrttechnik. Beta-Titan wird häufig in der Kieferorthopädie verwendet.
- Cp-Ti (Reintitan), Grad 1, 2: Es wird aufgrund der Biokompatibilität des Titans mit dem menschlichen Körper in der Medizinindustrie für eine Vielzahl von Anwendungen eingesetzt.
- TA15: Es besteht fast vollständig aus Titan, dem jedoch etwas Aluminium und Zirkonium zugesetzt ist. Bauteile aus dieser Legierung sind sehr stabil und widerstandsfähig gegen hohe Temperaturen, was sie ideal für den Bau starker Teile in Flugzeugen und Motoren macht. Im Vergleich zu ihrer Festigkeit sind sie auch recht leicht.
Aluminium
Aluminium ist ein Metall, das sowohl Leichtigkeit als auch Festigkeit bietet. Es ist nicht nur korrosionsbeständig, sondern kann auch geschweißt werden. In seiner reinen Form ist es recht selten zu finden. Häufiger findet man es als Legierung mit anderen Metallen, die seine physikalischen und mechanischen Eigenschaften verbessern, wie Silizium und Magnesium. Wie bei Titan gibt es zwei aufeinander folgende industrielle Verfahren, um das Material in reiner Form zu gewinnen. Beim ersten Verfahren, dem so genannten Bayer-Verfahren, wird Aluminiumoxid aus Bauxiterz gewonnen. Das Erz wird gewaschen und zerkleinert, in Natronlauge aufgelöst und gefiltert, um reines Aluminiumhydroxid zu erhalten. Anschließend wird es erhitzt, um Aluminiumoxidpulver zu erhalten. Beim zweiten Verfahren, dem sogenannten Hall-Héroult-Verfahren, wird durch elektrolytische Reduktion von Aluminiumoxid reines Aluminium gewonnen. Die meisten Verarbeitungsanlagen werden in der Nähe der Minen gebaut, um die Kosten für den Transport des Erzes zu senken.
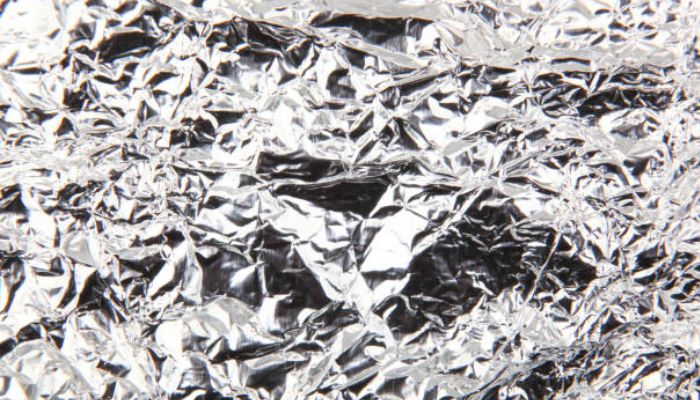
Bild: Getty Images
Wie bereits erwähnt, sind Aluminiumlegierungen weiter verbreitet als die reine Form und werden in vielen industriellen Anwendungen eingesetzt. Darüber hinaus haben sie ein sehr gutes Verhältnis von Festigkeit und Gewicht. Ebenfalls weisen sie eine sehr gute Beständigkeit gegen Metallermüdung und Korrosion auf. Zu ihren Eigenschaften gehört auch, dass sie gut recycelbar, thermisch und elektrisch leitfähig und wenig toxisch sind.
Die wichtigsten Legierungen, die beim 3D-Druck von Aluminium verwendet werden, sind:
- AISi10Mg: Es ist die gebräuchlichste Legierung, die aus Silizium und Magnesium besteht. Sie ermöglicht die Herstellung massiver und komplexer Teile und wird zur Herstellung einer Vielzahl von Gegenständen wie Gehäusen, Motorteilen und Produktionswerkzeugen verwendet.
- Al2139: Das ist die stabilste Aluminiumlegierung, die von der deutschen Firma EOS entwickelt wurde. Sie eignet sich aufgrund ihrer Leichtigkeit, Festigkeit und chemischen Beständigkeit ideal für Sektoren wie den Automobilbau und wurde bereits von Organisationen wie der US Air Force, Mercedes-Benz und Airbus verwendet. Das Interessante an diesem Werkstoff ist, dass er speziell für die additive Fertigung entwickelt wurde und viele andere auf dem Markt erhältliche Legierungen übertrifft.
- Al 7000-Serie: Es ist eine bekannte Serie von Pulverlegierungen mit hoher Zugfestigkeit und niedriger Temperaturbeständigkeit.
- Al 6061 & Al 7075: In letzter Zeit erzielen 3D-Hersteller sehr gute Ergebnisse mit diesen beiden Legierungen. 6061 hat eine geringere Zugfestigkeit und Härte als 7075. Andererseits ist 7075 stoßfester und verformt sich weniger als 6061er Aluminium.
- A201.1: gehört zur 200er-Reihe von Kupfer-Aluminium-Legierungen, die als sehr fest gelten. Allerdings sind sie schwer zu gießen. Diese Legierungen werden für Anwendungen empfohlen, bei denen das Verhältnis von Festigkeit zu Gewicht von entscheidender Bedeutung ist, z. B. im Transportwesen und in der Luft- und Raumfahrt.
Titan und Aluminium im direktem Vergleich Metalle
Aluminium und Titan sind zwei sehr unterschiedliche Metalle, die in einer Vielzahl von Anwendungen zum Einsatz kommen. Bei der Entscheidung zwischen den beiden Metallen müssen die unterschiedlichen Eigenschaften berücksichtigt werden.
In Bezug auf das Verhältnis von Festigkeit zu Gewicht ist Titan die ideale Wahl, wenn eine hohe Festigkeit und Robustheit erforderlich ist, weshalb es in medizinischen Komponenten oder sogar in Satellitenkomponenten verwendet wird. Andererseits ist Aluminium zwar weniger fest als Titan, dafür aber viel leichter und preiswerter. Was die thermischen Eigenschaften betrifft, so ist Aluminium perfekt für Anwendungen geeignet, die eine hohe Wärmeleitfähigkeit erfordern. Titan hingegen ist aufgrund seines hohen Schmelzpunktes ideal für Anwendungen in Hochtemperaturumgebungen, wie z. B. Triebwerkskomponenten in der Luft- und Raumfahrt. Sowohl Aluminium als auch Titan weisen eine ausgezeichnete Korrosionsbeständigkeit auf. Titan ist jedoch biokompatibler als Aluminium, weshalb es vor allem im medizinischen Bereich eingesetzt wird.
Form der verwendeten Materialien und 3D-Technologien
Form
In den meisten Fällen liegen Titan und Aluminium in Pulverform vor, obwohl sie auch in Form von Drähten oder Fäden erhältlich sind, wie z. B. das Titan- oder Aluminiumfilament von Virtual Foundry oder Nanoe mit seinem Zetamix-Angebot.
Um Teile mit diesen Metallen in 3D zu drucken, muss das Legierungspulver zunächst gewonnen werden, was mit zwei Haupttechniken geschieht: Plasmazerstäubung oder Gaszerstäubung. Die Plasmazerstäubung (ionisiertes Gas) ist ein Verfahren, bei dem hohe Temperaturen, eine Energie- und Wärmequelle, ein inertes Medium wie Argon und hohe Geschwindigkeiten eingesetzt werden, um das Metall zu zerstäuben. Mit diesem Verfahren werden hochwertige, verschleißfeste Pulver hergestellt. Bei der Gaszerstäubung hingegen wird Luft, Argon oder Helium als Gas verwendet, um einen geschmolzenen Materialstrom zu zerstückeln. Es ist ein sehr effizientes Verfahren und wird häufig zur Herstellung feiner, kugelförmiger Metallpulver eingesetzt. Die für die Herstellung des Metallpulvers verwendete Technik ist wichtig, da sie die endgültigen Eigenschaften des Teils eindeutig beeinflusst.
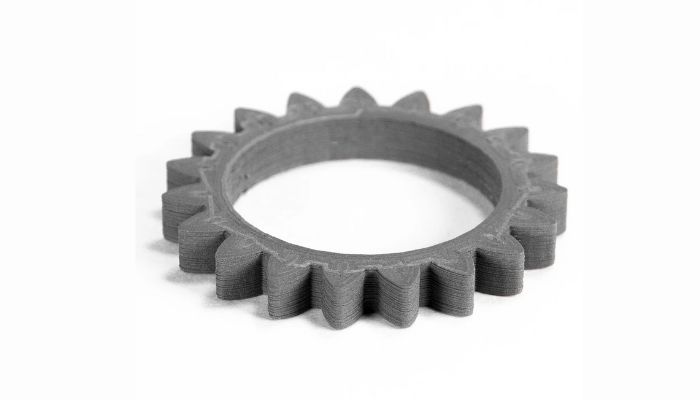
Getriebe aus Titan 64-5 ungesintert (Bild: SAPPHIRE3D)
3D-Drucktechnologien
Für die Verarbeitung von Titan im 3D-Druck kann eine Vielzahl von Metalltechnologien eingesetzt werden, wie z. B. das Laserschmelzen (L-PBF), Direct Energy Deposition (DED) oder Binder Jetting. Für Aluminium gibt es zusätzlich zu den bereits erwähnten Verfahren noch ein weiteres, wie das Kaltgasspritzen, auch Cold Spray genannt.
Beim Laserschmelzen wird ein Laserstrahl verwendet, um das pulverförmige Metall Schicht für Schicht bis zu seinem Schmelzpunkt zu erhitzen und das Objekt aufzubauen. Titan schmilzt bei sehr hohen Temperaturen (1600 °C), sodass die thermischen und mechanischen Auswirkungen des Materials vor dem 3D-Druck analysiert werden müssen. Die Schmelztemperatur von Aluminium ist mit etwa 630 °C viel niedriger, aber Aluminium hat ein hohes Reflexionsvermögen und eine hohe Wärmeleitfähigkeit für das Verfahren. Ein weiterer interessanter Aspekt der additiven Fertigung mit Aluminium ist, dass es eine natürliche Oxidschicht bildet, die bei anderen Metallen erst später an den Kanten auftritt, was bedeutet, dass diese dünne Schicht den Prozess verlangsamt.
Bei der direkten Energieabscheidung handelt es sich um ein ähnliches Verfahren, jedoch wird hier das Material gleichzeitig mit der Abscheidung in der Düse geschmolzen und liegt in Form von Pulver oder Draht für die Herstellung vor. Normalerweise ermöglicht diese Technologie eine höhere Produktionsgeschwindigkeit und niedrigere Kosten pro Mengeneinheit.
Beim Binder Jetting liegt das Material in Pulverform vor, das nicht geschmolzen wird. Damit die Partikel aneinander haften, wird in diesem Fall ein Binder mit Hilfe eines Druckkopfes an bestimmten Stellen auf die Schicht gesprüht. Nach dem Druck ist außerdem ein Sinterungsschritt erforderlich. Wenn die Teile aus dem 3D-Drucker kommen, sind sie sehr zerbrechlich und porös und müssen einer Wärmebehandlung unterzogen werden, um ihre endgültigen mechanischen Eigenschaften zu erhalten.
Beim Kaltgasspritzen liegt das Metallmaterial ebenfalls in Pulverform vor, aber da es in diesem Fall nicht geschmolzen oder verschmolzen werden muss, können wir Wärmeverformungen vermeiden und eine Schutzatmosphäre ist nicht erforderlich.
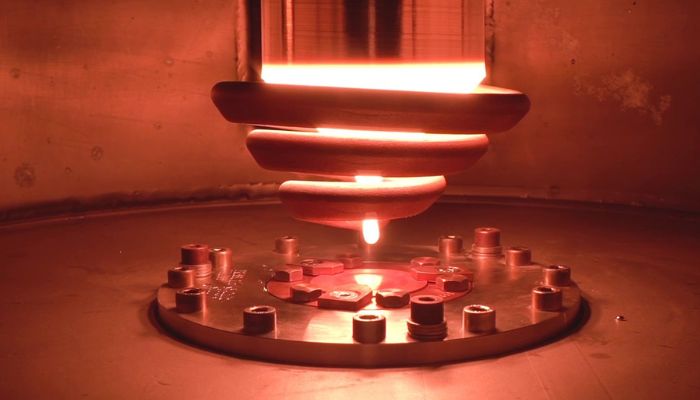
Bild: Sandvik
Nachbearbeitung
Um das optimale Ergebnis zu erzielen, ist es notwendig, die Teile einem Nachbehandlungsprozess zu unterziehen. Für Titanium und Aluminium gibt es keine spezifischen Unterschiede in der Nachbearbeitung, weshalb sich die folgenden Schritte auf beide Materialien beziehen.
Da Titanium und Aluminium häufig für Anwendungen gefertigt werden, die einer mechanischen Belastbarkeit ausgesetzt sind, sind die Techniken der Verfestigungs- und Kugelstrahlen besonders von Vorteil. Bei der ersten Methode werden kleine Metall- oder Keramikkugeln gegen die Oberfläche des Werkstücks geschleudert, wodurch eine kontrollierte Verformung in der Oberflächenschicht des Teils entsteht. Dadurch wird unter anderem die Haftung nachfolgender Beschichtungen verbessert und die Wahrscheinlichkeit von Rissen und Brüchen verringert. Beim Kugelstrahlen wird nur die oberste Materialschicht abgetragen. Dies kann das ästhetische Erscheinungsbild des Teils verbessern, Schmutz und Korrosion entfernen und die Oberfläche für nachfolgende Beschichtungen vorbereiten.
Eine weitere Möglichkeit wäre, den Metalldruck mit traditionellen Fertigungsmethoden zu kombinieren. Hierzu eignet sich die CNC-Bearbeitung als Nachbehandlungsprozess, da somit enge Toleranzen und die gewünschte Oberflächengüte gewährleistet werden können. Insbesondere bei der DED-Technologie erhält man Rohlinge mit einer sehr rauen Oberfläche, da das Metall direkt während des Extrusionsprozesses geschmolzen wird. Daher ist immer eine CNC-Bearbeitung erforderlich, um eine glatte und definierte Oberfläche zu erhalten.
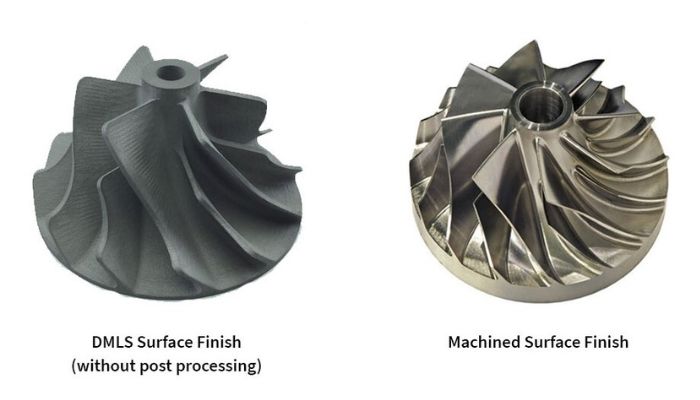
Bild: FacFox
Das Lösungsglühen ist eine Wärmebehandlungsoption. Hierbei wird das gedruckte Teil auf eine hohe Temperatur erhitzt und dann wieder schnell abgekühlt. Dadurch verändert sich das Mikrogefüge, was zu einer besseren Duktilität – das ist die Eigenschaft eines Werkstoffs, sich unter Belastung zu verformen, bevor es bricht – führt. Insgesamt können somit bessere mechanische Eigenschaften erzielt werden. Zu erwähnen ist ebenfalls, dass das Verfahren insbesondere für Aluminiumteile verwendet wird.
Das Sintern ist auch für Aluminium und Titan erforderlich, wenn sie in 3D-Druckverfahren wie FDM oder dem Binder Jetting verwendet werden. Nach der Druckphase müssen die Teile einem Entbinderungsprozess unterzogen werden, um die Polymere vom Metallbinder zu trennen. Anschließend werden die Teile in einem Sinterofen auf eine bestimmte Temperatur erhitzt, die knapp unter der Schmelztemperatur liegt, wodurch das endgültige Objekt verfestigt wird. Das Ergebnis sind Teile mit sehr geringer Porosität, da die Hohlräume, in denen sich das Bindemittel befand, während des Prozesses geschlossen werden, was zu einer Verdichtung führt.
Anwendungen von Titanium und Aluminium
Die Luft- und Raumfahrtindustrie profitiert insbesondere von der Verwendung von Titan in der additiven Fertigung. Hierbei lässt sich das Gewicht von hochbelasteten Strukturen deutlich reduzieren, wodurch sich das Material vor allem für die Herstellung von Düsentriebwerken, Gasturbinen und vielen weiteren Flugzeugkomponenten eignet. So ging beispielsweise Boeing eine Partnerschaft mit Norsk Titanium ein, um große Strukturbauteile für den 787 Dreamliner zu fertigen. Bei der verwendeten Technologie handelt es sich um das DED-Verfahren, hierbei wurde Titandraht mit Plasmabrennern geschmolzen, um das Endteil zu fertigen. Die Anwendung birgt gleich mehrere Vorteile: die Technologie ist Berichten zufolge nicht nur 50-100 Mal schneller als pulverbasierte Systeme, sondern verbraucht ebenfalls 25-50% weniger Titan im Vergleich zum Schmiedverfahren. Das könnte dazu führen, dass Boeing bis zu 3 Millionen US-Dollar pro Flugzeug einsparen könnte.
Auch wenn Titan derzeit häufiger für den 3D-Druck in der Weltraumforschung angewandt wird, ist eine Zunahme der Anwendungen mit Aluminium in der Branche bemerkbar. Um bei dem Beispiel von Boeing zu bleiben, so fertigt das Unternehmen 3D-gedruckte Teile aus Aluminiumlegierungen her, die während der Abkühlungsphase mit Nanopartikeln beschichtet werden. Dadurch kann eine extrem belastbare Aluminiumlegierung ohne Warmrissbildung geschweißt werden. Die gefertigten Rahmen sind deutlich leichter, wodurch es für Flugzeuge möglich wäre, Treibstoff besonders effizient zu verwenden und mit gleichbleibender Menge weitere Strecken zu fliegen.
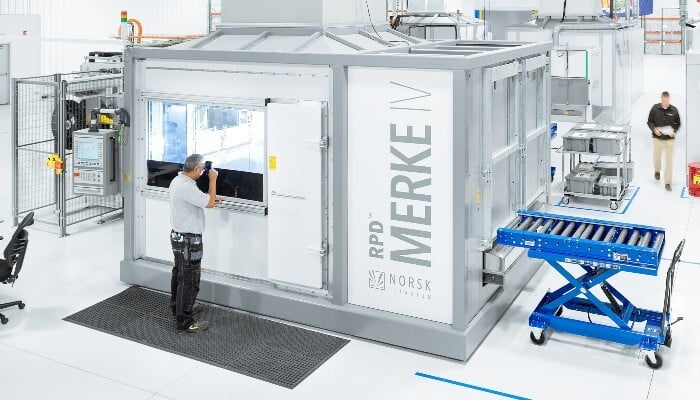
Diese Maschine stellt Teile für die Boeing 787 her (Bild: Norsk Titanium)
In der Automobilbranche stellt der hohe Preis von Titan ein kleines Hindernis für den Anwendungsbereich der breiten Masse dar, da die Kostenfrage eine besonders wichtige Rolle bei den preissensiblen Endverbrauchern einnimmt. Nichtsdestotrotz ist zu sehen, dass das Material auch hier nun öfters verwendet wird, jedoch wird das kostspielige Material hauptsächlich im Luxussegment genutzt. Zurzeit werden Teile in 3D gedruckt, bei denen das Verhältnis von Gewicht und Leistung entscheidend ist. Als Beispiel kann hier Bugattis Bremssattel, ein zentraler Bestandteil des Bremssystems, angeführt werden. Dieser wurde in nur 45 Stunden mit der SLM-Technologie gedruckt und soll ca. 40% leichter sein als ein herkömmlich gefräster Bremssattel aus Aluminium. Trotz der Leichtigkeit wird ebenfalls gewährleistet, dass das Teil aus Titan belastbar und temperaturbeständig ist. Aluminium hingegen ist deutlich häufiger in der Industrie vorzufinden. Porsche hat mit dem Material Hochleistungs-Aluminiumkolben für sein 911-Flaggschiff, den GT2 RS, 3D-gedruckt. Durch die Verwendung der Technologie kann dem 700 PS starken Biturbo-Motor bis zu 30 PS mehr Leistung verliehen werden. Gleichzeitig wird der Wirkungsgrad verbessert. Frank Ickinger von der Abteilung für die Vorentwicklung des Antriebs bei Porsche erklärte: „Dank der neuen, leichteren Kolben können wir die Motordrehzahl erhöhen, die Temperaturbelastung der Kolben senken und die Verbrennung optimieren“. Ebenfalls hat Porsche im Jahr 2020 ein Gehäuse für einen Elektroantrieb vollständig aus 3D-gedrucktem Aluminium hergestellt. Dieser konnte alle Qualitäts- und Belastungstests des Unternehmens bestehen.
In der Medizin ist Titan ein besonders attraktives Material, da es neben der hohen Festigkeit und Korrosionsbeständigkeit auch giftfrei ist und somit für orthopädische und Zahnmedizinische Implantate verwendet werden kann. Vor allem eine poröse Struktur des Materials, die durch den 3D-Druck möglich ist, stellt einen bemerkenswerten Vorteil dar, da diese Beschaffenheit die Struktur des menschlichen Knochens nachahmt. Das türkische Unternehmen TrabTech stellt trabekulare Implantate, unter anderem auch ein Hüftimplantat, aus Titan her. Diese ermöglichen eine schnelle Heilung, indem zum Wachstum von Knochen und Gewebe beigetragen werden. Zudem bietet das Material eine hohe Biokompatibilität. Die Verwendung von Aluminium hingegen ist im Vergleich zu Titanium eher unüblich in der medizinischen Branche. Trotzdem kann es für orthopädische Implantate und zahnmedizinische Anwendungen genutzt werden.
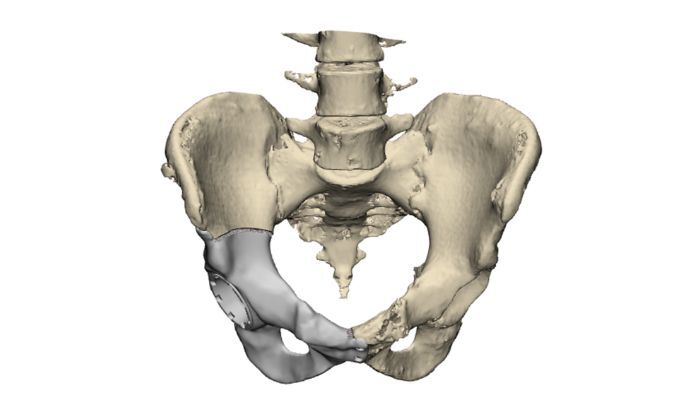
TrabTech stellt trabekulare Implantate aus Titan her (Bild: TrabTech)
Preis und Hersteller
Einer der Nachteile von Titanium ist der Preis, denn das Material befindet sich in einem der höheren Preissegmente. So müssen Sie laut dem Wohlers Report 2021 bei einem Kilogramm Pulver der Titanlegierung Ti-6AI-4V oder bei Rein-Titan Grad 2 mit ca. 329 bis 472 US-Dollar rechnen. Aluminium hingegen ist deutlich günstiger, so lässt sich die Aluminiumlegierung AISi7 für 94 $/kg Pulver und AISi10Mg für 98$/kg erwerben.
Bezüglich der Hersteller ist Heraeus Additive Manufacturing zu nennen. Das deutsche Unternehmen spezialisiert sich auf die Verarbeitung von Edelmetallen und stellt unter anderem Titan 6Al-4V, Grad 5 und Grad 23 her. Diese beiden Titan-Arten werden ebenfalls von PyroGenesis Additive und AP&C hergestellt. Ein weiterer Hersteller, welcher Titan Beta 21S und Rein-Titan anbietet, ist GKN. Was die Vermarktung von Aluminium angeht, so sind Uniformity Labs und Equispheres zu nennen. Die beiden Unternehmen stellen die häufig verwendete Aluminium-Legierung AISi10Mg her. Das Aluminium-Legierungspulver der Serie 7000 wird zudem von APWorks produziert.
Was halten Sie von der Verwendung von Titan und Aluminium für den 3D-Druck? Lassen Sie uns gerne einen Kommentar da, oder teilen Sie es uns auf Facebook oder LinkedIN mit. Möchten Sie außerdem eine Zusammenfassung der wichtigsten Neuigkeiten im 3D-Druck und der additiven Fertigung direkt und bequem in Ihr Postfach erhalten? Dann registrieren Sie sich jetzt für unseren wöchentlichen Newsletter.
Mein Mann arbeitet im Stahlbau. Es ist interessant, dass Titan aus Erzen gewonnen werden muss. Dies habe ich nicht gewusst.