Steif oder elastisch? Dieses Kunststoffmaterial ändert dank 3D-Druck seine Eigenschaften
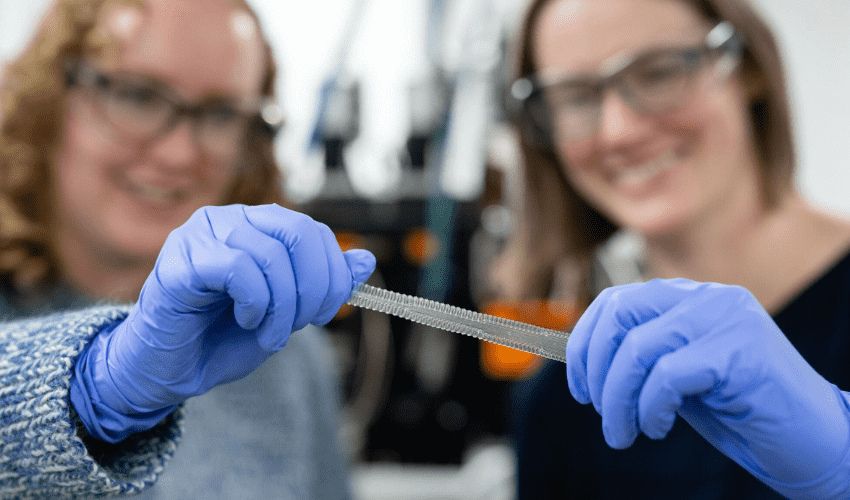
In den letzten Jahren haben sich viele universitäre Forschungsprojekte der Entwicklung multifunktionaler Materialien durch additive Fertigung zugewandt. Im medizinischen Bereich ist es beispielsweise wichtig, Gewebe zu entwickeln, die Organe oder Knochenstrukturen regenerieren können, sowie hochmoderne biomedizinische Geräte zu entwerfen. Gleichzeitig konzentrieren sich in anderen Bereichen die Bemühungen auf die Schaffung neuer 3D-druckbarer Architekturen, die ein breites Spektrum an potentiellen Anwendungen bieten.
Um dies zu demonstrieren, haben Alice Fergerson und das Ingenieurteam der Princeton University unter der Leitung von Emily Davidson ein Kunststoffmaterial entwickelt, das sich an verschiedene Flexibilitätsgrade anpassen kann. Dieses Material, das aus einer Klasse von Polymeren namens TPE besteht, ermöglicht das Design und die Herstellung von flexiblen, 3D-gedruckten Strukturen, deren Steifigkeit moduliert werden kann. Mithilfe des 3D-Drucks konnten die Ingenieure die physikalischen Eigenschaften des Materials steuern, sodass sich das Gewebe wiederholt in eine Richtung dehnen und falten kann, während es in einer anderen Richtung steif bleibt.
Die Eigenschaften des Kunststoffmaterials
Das von dem Ingenieurteam der Princeton University ausgewählte thermoplastische Elastomer ist ein Blockcopolymer, das im geschmolzenen Zustand geformt werden kann. Beim Abkühlen verfestigt es sich und bildet eine elastische Struktur. Dieses Phänomen lässt sich durch das Verhalten der inneren Komponenten des Copolymers erklären, die aus Homopolymeren bestehen und sich wie Öl und Wasser trennen, anstatt sich zu vermischen. Die Forscher machten sich diese Eigenschaft zunutze und schufen ein Material, das aus starren Zylindern besteht, die in einer elastischen Matrix verteilt sind. Dadurch bleibt das Material flexibel, behält aber seine inneren Eigenschaften bei.
Die starren zylindrischen Strukturen dieses Kunststoffmaterials sind fünf bis sieben Nanometer dick und in eine elastische Polymermatrix eingebettet. Um diese Größenordnung besser zu verstehen, hier zwei Vergleiche: Ein menschliches Haar hat einen Durchmesser von etwa 90.000 Nanometern, während eine DNA-Helix einen Durchmesser von etwa ein Nanometer hat. Die Forscher untersuchten auch, wie die Druckgeschwindigkeit und die kontrollierte Extrusion des Materials genutzt werden können, um die physikalischen Eigenschaften des gedruckten Materials zu modulieren. Mithilfe des 3D-Drucks können die Zylinder im Nanometerbereich ausgerichtet werden, wodurch ein Material entsteht, das lokalisierte Steifigkeit bietet und gleichzeitig weiche und elastische Bereiche beibehält.
Seine selbstheilenden Eigenschaften
Der interessanteste Aspekt dieses Prozesses ist das thermische Glühen des Kunststoffs und seine selbstheilenden Eigenschaften. Alice Fergerson erklärte, dass das thermische Glühen die Eigenschaften des Materials nach dem Drucken deutlich verbessert. Durch dieses Verfahren können im Labor gedruckte Objekte mehrfach wiederverwendet werden und sich sogar selbst reparieren, wenn sie beschädigt werden. Um diese Selbstreparatureigenschaften nachzuweisen, schnitten die Forscher eine flexible Probe des gedruckten Materials aus und reparierten es durch Glühen. Ihren Beobachtungen zufolge wies das reparierte Material keine nennenswerten Unterschiede zum ursprünglichen Material auf.
Davidson weist darauf hin, dass ähnliche Materialien, die in anderen Zusammenhängen verwendet werden, sehr teuer sind und eine komplexe Verarbeitung erfordern, wie z. B. eine kontrollierte Extrusion mit anschließender Behandlung mit ultraviolettem Licht. Die Kosten für diese Materialien können bis zu ca. 2,50 US-Dollar pro Gramm betragen. Im Gegensatz dazu kostet das in diesem Projekt verwendete thermoplastische Elastomer nur etwa einen Cent pro Gramm und kann mit kommerziellen 3D-Druckern gedruckt werden. Das macht das Material nicht nur kostengünstig, sondern auch für kostengünstige Drucklösungen zugänglich.
Eines der Hauptziele des Projekts war es, flexible Materialien mit lokal einstellbaren mechanischen Eigenschaften zu entwickeln und dabei einen kostengünstigen und leicht skalierbaren Ansatz für die Industrie zu verfolgen. Emily Davidson ist der Ansicht, dass diese Methode zur Gestaltung fortschrittlicher flexibler Materialien in verschiedenen Bereichen Anwendung finden könnte, z. B. in der flexiblen Robotik, bei medizinischen Geräten, Prothesen und auch bei personalisierten Hochleistungsschuhsohlen. Der nächste Schritt für das Forschungsteam besteht darin, neue 3D-druckbare Architekturen zu schaffen, die mit Anwendungen wie tragbarer Elektronik und biomedizinischen Geräten kompatibel sind.
Was halten Sie von diesem Kunststoffmaterial? Lassen Sie uns dazu einen Kommentar da, oder teilen Sie es uns auf Facebook oder LinkedIN mit. Möchten Sie außerdem eine Zusammenfassung der wichtigsten Neuigkeiten im 3D-Druck und der additiven Fertigung direkt und bequem in Ihr Postfach erhalten? Dann registrieren Sie sich jetzt für unseren wöchentlichen Newsletter.
*Bildnachweise: Princeton Engineering