Schnell, günstig, Multimaterial: AIM3D verbindet 3D-Druck und Spritzguss
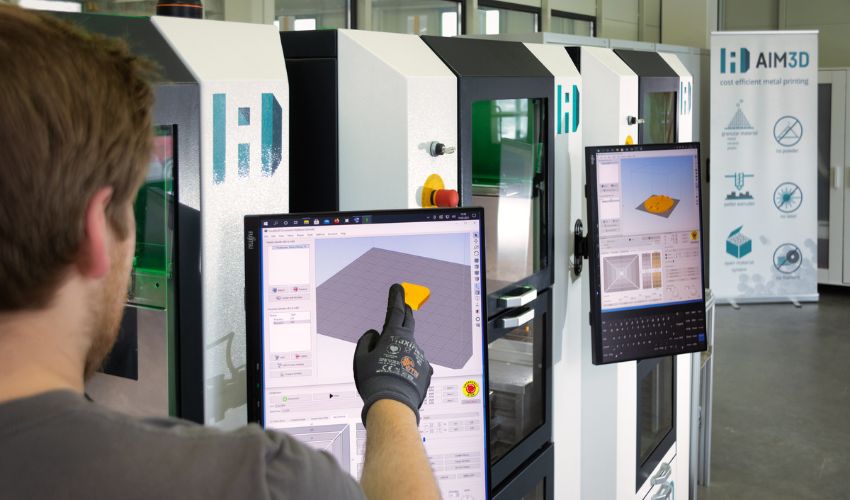
AIM3D ist ein Spin-Off der Universität Rostock und wurde von Wissenschaftlern eben dieser Uni gegründet. Die erste Finanzierungsrunde des Startups für den Drucker ExAM 255 ging 2018 mit 1,4 Millionen Euro erfolgreich über die Bühne. Mit einem einfachen 3D-Drucker wollten sich die Wissenschaftler aber nicht begnügen. Ihre Ziele sind vielfältig: sie wollen Metallteile kosteneffizient herstellen, die Serienfertigung revolutionieren und noch dazu Materialgrenzen überwinden. Beim ersten Produkt, der Maschine ExAM 255 handelt es sich daher um einen Multimaterialdrucker, der alle schmelzbaren Materialien verarbeitet, darunter Keramik, Metall und Kunststoffe. Verwendet wird dazu Standard-Spritzgussmaterial. Damit dies gelingt, hat AIM3D einen eigenen Druckkopf und eine eigene Drucktechnologie, basierend auf dem CEM-Verfahren (Composite Extrusion Modeling), entwickelt. Dieses Verfahren kombiniert die Vorteile des Spritzguss mit additiver Fertigung und ermöglicht so den Einsatz von üblichem Spritzgussgranulat.
Der Ansatz, komplexe Formen möglichst billig zu produzieren, geht Hand in Hand mit dem Vorsatz von AIM3D, nämlich den 3D-Druck von der Kostenseite her zu revolutionieren. Dafür zeigt das Startup zunehmend mit neuen Innovationen auf. Für die zweite Finanzierungsrunde des neuen Industriedruckers ExAM 510 konnten bereits die HZG Group und andere Frühphaseninvestoren gewonnen werden. Im Gespräch mit Dr. Vincent Morrison, Co-Gründer von AIM3D, erfahren Sie mehr über den spannenden Werdegang von AIM3D und was das Startup in Zukunft noch vor hat.
3DN: Könnten Sie sich kurz vorstellen und berichten, wie Sie zum 3D-Druck gekommen sind?
Mein Name ist Vincent Morrison und ich bin zusammen mit meinem Kollegen Clemens Lieberwirth einer der Gründer von AIM3D. Ich habe damals als einer der ersten Studenten an der Universität Rostock die Vorlesungen zu „Generativen Fertigungsverfahren“ gehört. Damals, das war 2008, nannte man die additive Fertigung im deutschsprachigen Raum noch häufig so. Es folgten dann die Betreuung der Praktika in dieser Vorlesung und später die Arbeit als wissenschaftlicher Mitarbeiter an dem Lehrstuhl, der sich mit der additiven Fertigung beschäftigte. Ich selber war zwar im Fachbereich Hydraulik/Fluidtechnik des Lehrstuhls tätig, hatte jedoch so fast täglich Berührungen mit der additiven Welt.
Der Background aus der Wissenschaft hat bei der Unternehmensgründung natürlich sehr geholfen, da wir an der Universität gelernt haben über den Tellerrand herauszuschauen und Probleme analytisch zu betrachten. Außerdem muss man sagen, dass die Universität Rostock nicht nur der Ort war, an dem sich das Kernteam kennengelernt hat, sondern dass die Universität uns auch die technischen Möglichkeiten gegeben hat, das Verfahren zu entwickeln, mit dem wir arbeiten. So waren viele Teile der ersten Extruder additiv auf MEX-Systemen und einer Arcam EBM Maschine hergestellt. Ohne diese Möglichkeiten hätten wir niemals in einer solchen Geschwindigkeit unser Kern-Know-How aufbauen können.
3DN: Wie hat sich Ihr Unternehmen seit der Gründung weiterentwickelt? Was waren die größten Meilensteine?
Das Unternehmen AIM3D startete 2017 mit fünf Mitarbeitern und ohne konkretes Produkt. Es gab nicht mal einen richtigen Prototyp, da die bis dahin entstandenen Extruder nur Mikrogranulat verarbeiten konnten, welches kein industrieller Standard ist. Heute haben wir zwei sehr gute Maschinen in ihren jeweiligen Anwendungsfeldern und 18 Mitarbeiter sowie viele zufriedene Kunden. Ich denke, die wichtigsten Meilensteine auf diesem Weg –neben den erfolgreichen Finanzierungsrunden–, waren die Markteinführung der ExAM 255 für den MIM- und CIM-Bereich sowie Kunststoffe bis PA6 und der Start der Betaphase der ExAM 510, die mit hoher Konstanz ULTEM™ 9085 Granulat von Sabic und auch PEEK verarbeiten kann. Hier wird der nächste Meilenstein zur Formnext 2023 der Serienstart der ExAM 510 sein.
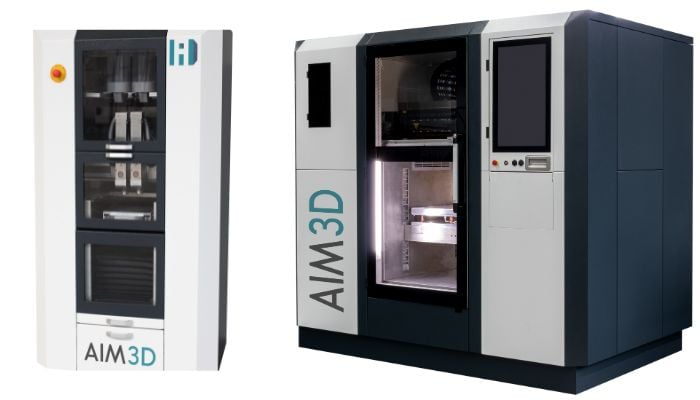
Links der Drucker ExAM 255 und rechts der Drucker ExAM 510.
3DN: Könnten Sie Ihr eigenes Druckverfahren näher erörtern?
Das geht zum Glück sehr einfach und schnell. Denken Sie einfach an einen Filamentdrucker, den viele für einige hundert Euro aus dem Internet oder lokalen Geschäften kennen und vielleicht sogar zu Hause haben. Unterhalb der Düse ist der Prozess quasi identisch mit nur wenigen Detailunterschieden. Aber oberhalb der Düse liegt der entscheidende Unterschied! Anstelle von ein paar Zahnrädern, die ein Filament in die Düse drücken, findet man bei uns eine Förderschnecke, welche direkt industrielles Granulat aufschmilzt und durch die Düse fördert. Das Granulat ist exakt das gleiche, das sonst in die Spritzgussmaschinen eingefüllt wird. Das ermöglicht also, sehr viele Werkstoffe additiv zu verarbeiten oder auch sehr gut experimentelle Werkstoffe additiv zu entwickeln und in Kleinserienproduktionen einzusetzen.
Außerdem können wir mit dem Schneckenextruder viel mehr Druck auf die Düse bringen. Durch diesen Umstand und ohne die Beschränkungen von Filamenten auf der chemischen Seite, können wir wesentlich schneller drucken und höhere Füllgrade an Metallpartikeln, Glas- oder Kohlefasern oder anderen Zusätzen im Material verarbeiten. Die Technik hat zwar einen höheren Einstiegspreis, rechnet sich aber bei entsprechendem Durchsatz. Daher paaren wir unsere Extruder mit schnellen und präzisen Achssystemen und bauen so industrielle additive Fertigungssysteme für den Dauereinsatz in der Industrie.
In Bezug auf den Multimaterialdruck folgen wir absolut keinem Credo, dass Granulate besser sind als Filamente, sondern kombinieren sogar beides in unseren Druckern. In Summe erhält man so zwei Drucksysteme, die an einem Tag MIM- und CIM-Werkstoffe in einem Bauteil kombinieren können und am darauffolgenden Tag ohne Umrüstung direkt Kunststoffteile herstellen können. Die ExAM 510 kann durch ihre drei Extruder sogar zwei Baumaterialien mit löslichen Stützmaterialien kombinieren. Das kann gerade bei Bauteilen mit Hart-Weich-Kombinationen sehr hilfreich sein. Am Ende zählt sicher diese Vielfältigkeit für die Anwender und das Potential, die Maschinen gut auszulasten und so einen kosteneffizienten Prozess zu haben.
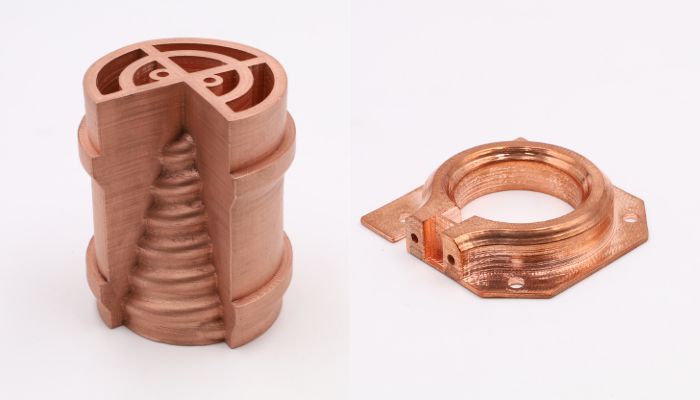
Die Drucklösungen von AIM3D verarbeiten Kunststoffe, Keramik, Stahl und Kupfer, wie hier am Bild.
3DN: An welche Sektoren wenden Sie sich mit Ihren Verfahren und Ansätzen?
Das kann man eigentlich gar nicht richtig einschränken. Am Ende sind die Stückzahlen entscheidend und wir wissen von unseren Kunden, dass diese häufig im Bereich bis 3.000 Stück pro Serie liegen. Die ist natürlich im Aerospace-Bereich häufig zu finden, aber auch in den Sparten Transport und Automotive, wenn es um Nutzfahrzeuge oder High-Performance-Cars geht. Durch die breite Auswahl an Werkstoffen kann das System aber fast in jeder Branche Anwendung finden. Das offene Materialsystem auf Granulatbasis ermöglicht am Ende auch im Forschungsbereich und in der Materialentwicklung z.B. der Kunststoffindustrie viele spannende Projekte und Weiterentwicklungen.
3DN: Könnten Sie mehr zu Ihren derzeitigen Projekten erzählen? Was hat es mit Ihrem Voxelfill-Projekt auf sich?
Ein konkretes Projekt nach der erfolgreichen zweiten Finanzierungsrunde ist nun der Serienstart der ExAM 510, mit welcher wir stark auf den Markt rund um die ULTEM™ Kunststofffamilie abzielen. Hier zeigen unsere Untersuchungen, dass wir reproduzierbar vergleichbare Festigkeiten bei höheren Bruchdehnungen erreichen können, als es die Filamentsysteme schaffen. Außerdem rechnet sich der Einsatz der ExAM 510 hier bereits nach weniger als 100kg Druckmaterial.
Zum Voxelfill-Projekt dürfen wir glücklicherweise auch schon recht viel erzählen. Die Grundidee ist, die MEX-Verfahren – also wieder Filamente und Granulate – von einem schichtbasierten Verfahren in ein volumenbasiertes Verfahren zu überführen. Hierzu bauen wir erst „hohle“ Bauteile, welche über Kammern im Inneren verfügen. Das kann man sich vorstellen, wie ein klassisches Filamentbauteil mit Infill. Diese Kammern füllen wir nach ein paar Schichten im Anschluss mit Material auf, wir spritzen sozusagen Material in eine Kavität, so wie der Spritzguss es macht. Das Ganze macht den Prozess nicht nur bis zu drei mal schneller, sondern soll auch deutlich mehr Festigkeit in die Bauteile bringen. Dies gilt insbesondere für fasergefüllte Werkstoffe, da wir durch diesen Schritt die Fasern auch in Z-Richtung orientieren können, was bisher nicht möglich war. Derzeit entwickeln wir eine entsprechende Software, damit wir bald unsere bestehenden und neuen Systeme mit diesem Feature ausstatten können.
3DN: Haben Sie noch abschließende Worte an unsere Leserschaft?
Viele kluge Köpfe stellen sich die Frage, wo sich die additive Fertigung in den nächsten Jahren hin entwickeln wird. Ich hoffe wir schieben uns noch mehr in Richtung industriellem Prozess und Fertigung. Viele Anwender haben hier in den letzten Jahren die richtigen Schritte gemacht und auch die Akzeptanz der Technologie steigt immer weiter. Das ist nicht nur bei den Firmen festzustellen, sondern auch bei den Endkunden. Für die Hersteller bedeutet das aber umso mehr, dass wir alle gemeinsam die Prozessstabilität unserer Maschinen und der gesamten Prozesskette verbessern müssen. Vielen Dank daher an alle, die daran arbeiten, dass die additiven Fertigungsverfahren immer anerkannter werden und an alle neuen Teilnehmer in der additiven Welt. Bedauerlicherweise können aber auch die additiven Systeme nicht einfach alles drucken. Es geht leider nicht ohne Einschränkungen. Aber mit fertigungsgerechtem Design kann man additiv unglaubliche Fortschritte erreichen. Mehr dazu finden Sie HIER.
Was halten Sie von AIM3D? Lassen Sie uns dazu einen Kommentar da, oder teilen Sie es uns auf Facebook oder LinkedIN mit. Möchten Sie außerdem eine Zusammenfassung der wichtigsten Neuigkeiten im 3D-Druck und der additiven Fertigung direkt und bequem in Ihr Postfach erhalten? Dann registrieren Sie sich jetzt für unseren wöchentlichen Newsletter.
Bildnachweise: AIM3D