Scawo3D ermöglicht durch Inkjet-Betondruck mehr Freiheiten in der Architektur
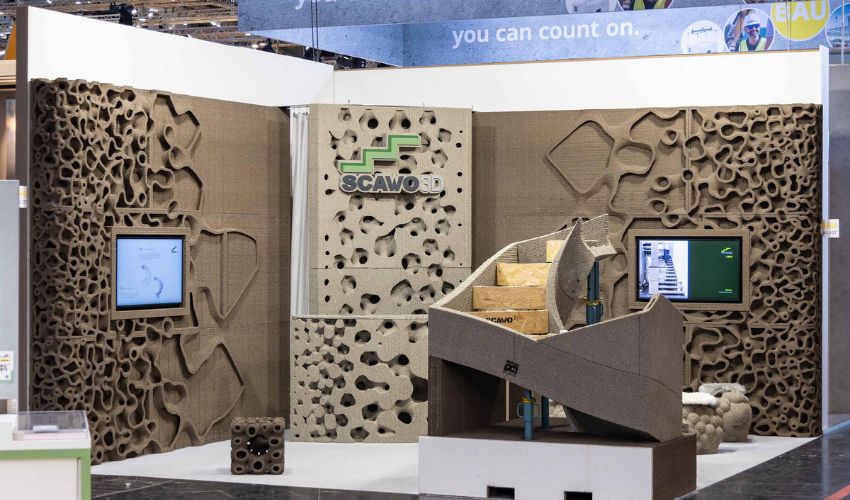
Wer sich mit 3D-Druck beschäftigt, dem ist der Trend rund um 3D-gedruckte Häuser wohl kaum entgangen. Zahlreiche Berichte und Beiträge über 3D-gedruckte architektonische Bauten lassen zur Annahme rühren, dass die additive Fertigung längst ins Bauwesen eingezogen sei. Tatsächlich treiben Forschungsergebnisse und innovative Unternehmen die Entwicklungen voran und tragen dazu bei, dass sich der 3D-Druck nachhaltig in der Architektur etabliert. Häufig kommt bei aktuellen Projekten der Extrusions-Druck zum Einsatz, indem riesige Druckroboter Schicht für Schicht moderne Bauten entstehen lassen. Scawo3D verfolgt hingegen einen anderen Ansatz. Das Unternehmen mit Sitz in Sarnthein in Südtirol hat mit seiner Technologie Selective Paste Intrusion einen Weg gefunden, Betonbauteile auf Pulverbett-Basis herzustellen. Das Unternehmen ist so in der Lage, einen isotropen Beton mit hohen Festigkeiten produzieren können, der auch wetterfest ist. Mit dieser Technologie sind der Fantasie keine Grenzen gesetzt und auch komplexe Geometrien können zu überschaubaren Produktionskosten umgesetzt werden. Wir haben mit Philip Schneider von Scawo3D gesprochen, um mehr über den innovativen Ansatz des Unternehmens zu erfahren.
3DN: Könnten Sie sich kurz vorstellen und erzählen, was Ihre Rolle bei Scwao3D ist?
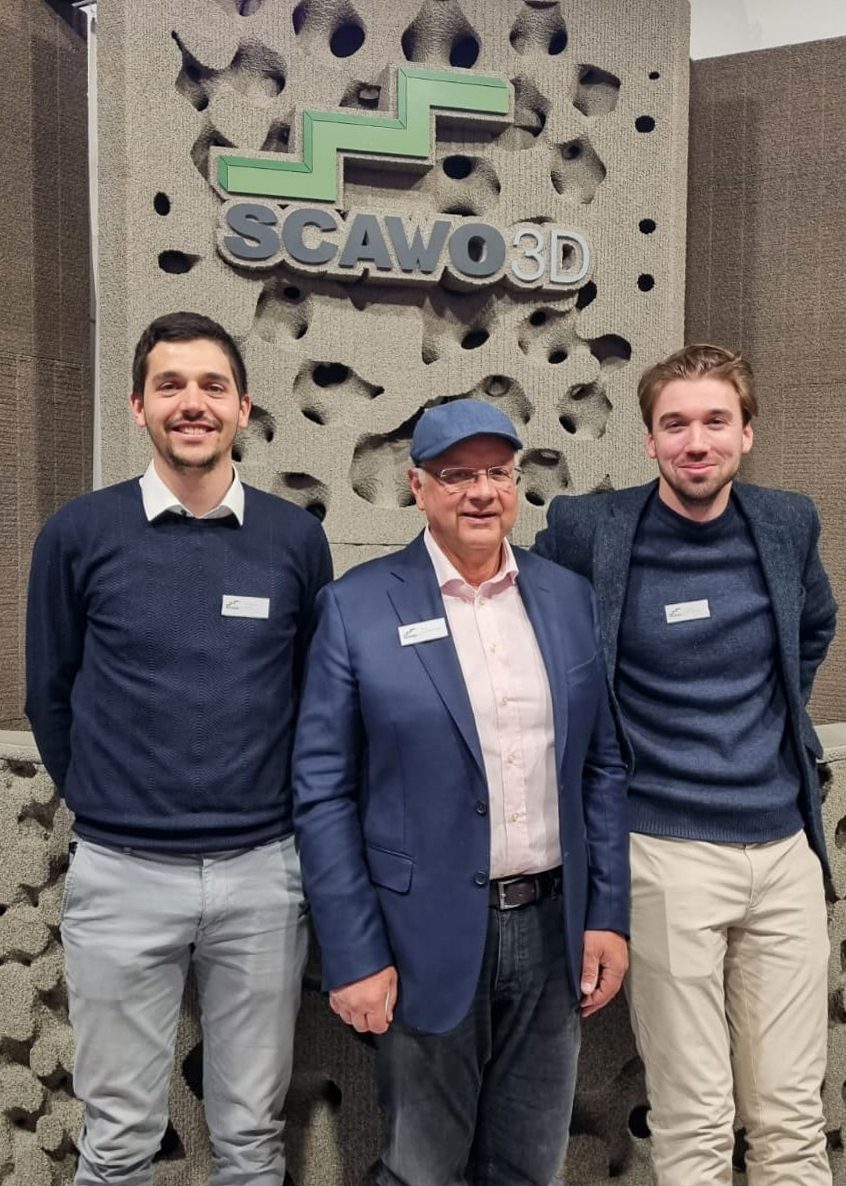
Team von Scawo3D (von links nach rechts): Andreas Spiess (Maschinenprogrammierung), Kurt Wohlgemuth (Firmeninhaber, Erfinder) und Philip Schneider (Architektur & Computational Design). (Bild: Scawo3D)
Hallo, ich bin Philip Schneider, ich habe Architektur mit den Schwerpunkten Computational Design und digitale Fabrikation an der Technischen Universität München studiert. Zum Beton-3D-Druck bzw. zu Scawo3D bin ich Anfang 2022 über den Entwurf einer 3D gedruckten Fußgängerbrücke während des Studiums gekommen, die schließlich zusammen mit Scawo3D umgesetzt wurde.
Scawo3D ist Erfinder des weltweit ersten Druckkopfs für Zementleim für ein neues Verfahren für den Beton-3D-Druck namens Selective Paste Intrusion (kurz SPI). Wir sind sowohl Entwickler und einziger Hersteller dieses Druckkopfs als auch Dienstleister im Beton-3D-Druck. Um unseren Kunden sowohl die bestmöglichen Maschinen an die Hand zu geben als auch unsere Dienstleistung preislich zugänglicher gestalten zu können, entwickeln und optimieren wir das Verfahren konstant weiter.
Im Unternehmen bin ich verantwortlich für Architektur und Computational Design, d.h., ich befasse mich mit potentiellen Anwendungen des SPI-Verfahrens für die Baubranche. Da unser Verfahren die Möglichkeit bietet, auch die komplexeste Geometrie in Beton zu realisieren, stellen sich erhöhte Anforderungen an die Software, die zur Modellierung und Planung zum Einsatz kommt. Es liegt auch in meiner Verantwortung, dass wir in Sachen Software für die Modellierung komplexer Geometrien ausgestattet sind und für bestimmte Anwendungsfälle auch eigene Lösungen entwickeln. Momentan arbeiten wir bspw. zusammen mit den Unternehmen Skeno GbR und Timo Harboe ApS an einem Plugin, basierend auf Rhinoceros und Grasshopper, zur Planung komplexer Freiformtreppen.
3DN: Warum haben Sie sich dazu entschlossen, den 3D-Druck zu implementieren?
Scawo war ursprünglich ein von uns patentiertes Verfahren zur Herstellung von CNC-gefrästen Schalungen aus EPS für Stahlbetontreppen. Nach einiger Zeit verhinderte die unzureichende Brandschutzklasse von EPS allerdings einen breiteren Einsatz in der Baubranche. Somit hat sich das Unternehmen entschlossen, ein 3D-Druck-Verfahren zu entwickeln, mit dem Beton hergestellt werden kann, der der höchsten Brandschutzklasse angehört. Ab diesem Zeitpunkt trug das Projekt den Namen Scawo3D.
Im Laufe des letzten Jahrzehnts wurde zuerst das SCA-Verfahren (kurz für Selective Cement Activation) entwickelt, bei dem ein Pulverbett aus Trockenmörtel selektiv aktiviert wird. Jedoch konnten nur Materialeigenschaften erreicht werden, die unzureichend für tragende Teile waren. Schließlich, nach weiterer Entwicklung, sind wir beim SPI-Verfahren angekommen, mit dem wir Mitte 2022 die Produktion aufgenommen haben. Während der Entwicklung blieben die Treppenschalungen weiterhin das Versuchsobjekt. Der Hintergedanke hierfür war, dass Treppen sowohl komplexe Geometrien als auch statische Anforderungen kombinieren. Funktioniert also einmal die Treppe, so dachten wir, lässt sich das Verfahren auch für andere Objekte einsetzen. Inzwischen können wir glücklicherweise sagen, dass dieser Gedankengang korrekt war.
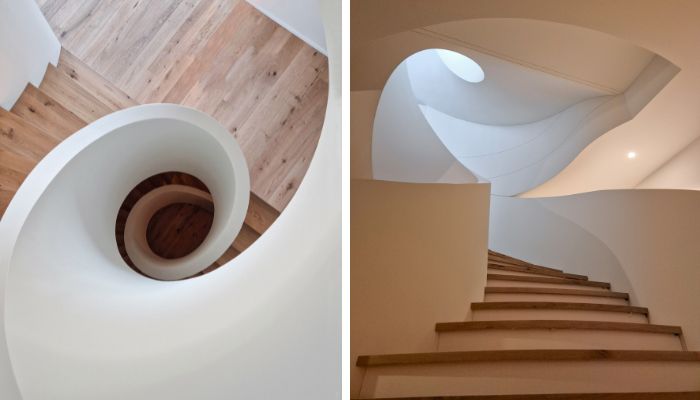
Fertiggestellte Treppe (Bild: Tschanen/André Wäspi).
3DN: Könnten Sie Ihr SPI-Verfahren näher erklären?
SPI ist ein neues Verfahren für den Beton-3D-Druck. Es unterscheidet sich vom bisher bekannten Extrusions-3D-Druck, das oftmals auch direkt auf der Baustelle eingesetzt wird. Unsere Anlage ist stationär und basiert auf einem Pulverbett. Das Prinzip funktioniert analog zu anderen Pulverbettverfahren, bspw. dem SLS-Verfahren für den 3D-Druck von Kunststoff. Nur wird unser Pulverbett mit einer Gesteinskörnung gefüllt und es wird Beton bzw. Mörtel gedruckt.
Während des Druckprozesses wird das Pulverbett Schicht für Schicht gefüllt. Auf jede Schicht wird abwechselnd lose Körnung und Zementleim aufgebracht. Der Zementleim, bestehend aus Zement, Wasser und Fließmitteln, wird durch unseren Druckkopf mit mehreren hundert Düsen selektiv aufgetragen und bindet die Körnung lokal. Anschließend wird wieder eine neue Schicht an loser Körnung aufgebracht und der Ablauf wiederholt, bis der Druck abgeschlossen ist. Während des gesamten Druckvorgangs sowie dem Aushärten dient die lose Körnung als Schalung für die gedruckten Teile. Dadurch können wir jede Geometrie drucken, ohne Einschränkungen durch Überhangwinkel oder Hohlräume.
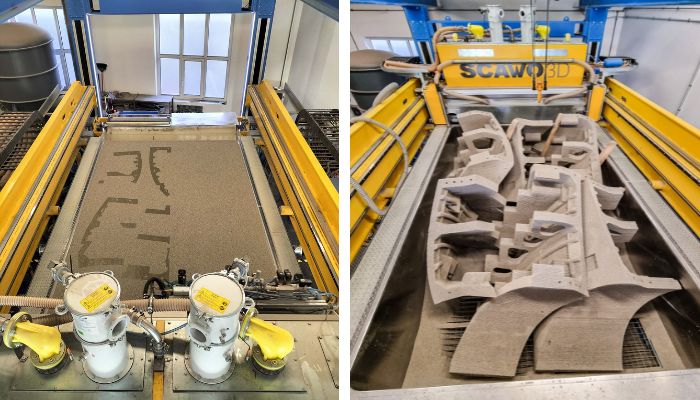
Links: Das 4 x 2,5 x 1,5 m große Druckbett während der Produktion der Treppenschalungen. Rechts: Schalungselemente für einen Treppenlauf von 3,5 m Höhe. (Bilder: Scawo3D)
Der Bauraum unseres Großdruckers fasst 15 Kubikmeter mit Abmessungen von 4 x 2,5 x 1,5 Metern und arbeitet momentan mit einer Schichthöhe von 3 Millimetern. Durch diese Kombination aus geringer Schichthöhe und der großen Anzahl an Düsen können wir Betonbauteile mit einer für den Bau sehr feinen Auflösung von 3 Millimetern fertigen. Trotz der hohen Auflösung fertigen wir aber doch verhältnismäßig schnell. 15 Kubikmeter können wir in acht Stunden drucken. Durch weitere Maschinenoptimierungen wird sich dies sehr bald aber schon auf vier Stunden reduzieren lassen.
Da das resultierende Material ähnliche Materialeigenschaften wie genormter Beton der Festigkeitsklassen C25/30 – C60/75 hat, lässt sich die Technologie ähnlich breit anwenden. Die hohen Druckfestigkeiten ermöglichen einen Einsatz von SPI-gedruckten Teilen mit tragender Funktion, die auch dem Wetter in unseren Breiten ausgesetzt werden können. Das bedeutet, dass Bauteile wie bspw. tragende Wände und Gewölbedecken sowie Fassaden realisiert werden können. Selbstverständlich können aber auch Designobjekte für Innen- und Außenbereich wie bspw. Gartenmöbel oder Skulpturen produziert werden.
3DN: Welche Vorteile ergeben sich durch den Inkjet-Betondruck im Vergleich zur Extrusion?
Der wohl größte Unterschied zwischen dem Extrusions- und dem SPI-Verfahren liegt darin, dass unser Verfahren deutlich weniger komplex ist. Das kommt einerseits daher, dass wir ausschließlich im Werk fertigen – zumindest momentan noch – und nicht direkt auf der Baustelle. Dies kann man nun als Vor- oder Nachteil sehen. Vorteilhaft daran ist jedenfalls, dass wir unter konstanten Bedingungen arbeiten, d.h., wir müssen weder Maschine noch Material an unterschiedliche Umgebungen mit schwankender Temperatur oder Luftfeuchtigkeit anpassen. Das Material, mit dem wir drucken, ist daher simpel und beinhaltet lediglich Zement, Wasser und bis auf einen geringen Anteil an Fließmitteln keine Chemie. Möglich ist das auch dadurch, dass die Zeit von Schicht zu Schicht immer dieselbe ist – es handelt sich nur um einige Sekunden. Die Offenzeit von herkömmlichem Zement ist also vollkommen ausreichend.
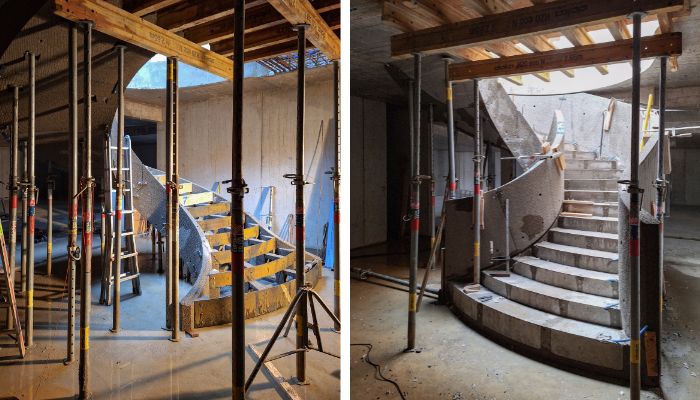
Montage der Treppenschalungen auf der Baustelle. (Bilder: Skeno/Scawo3D)
Aus der gleichbleibenden Zeit von Schicht zu Schicht ergibt sich auch schon der nächste Vorteil: Ganz egal, wie komplex die zu druckende Geometrie ist, oder wie voll unser Bauraum gepackt ist – die Druckzeit für einen Druck von 15 Kubikmetern bleibt immer die gleiche. Wir können mit der Auslastung eines Bauraums demnach den Preis steuern. Zu guter Letzt bietet die Fertigung im Werk den Vorteil, dass sich die Technologie auch für das Bauen im Bestand eignet. Hier trifft man oftmals auf schwer zugängliche Baustellen. Mit dem SPI-Verfahren brauchen für keinen Platz auf der Baustelle für ein großes Druckerportal, sondern können die Teile je nach Baustelle passend dimensionieren. Zusammengefasst gibt der „Inkjet-Betondruck“ dem Entwerfenden schlichtweg mehr Freiheiten.
3DN: Was waren die beeindruckendsten Projekte, die Sie bisher mit 3D-Druck umgesetzt haben?
Zwei Projekte möchte ich hier erwähnen: „Bridge the Gap“ ist in Zusammenarbeit mit dem Sonderforschungsbereich „Additive Manufacturing in Construction“ (AMC TRR 277) und der Technischen Universität München entstanden. Das Projekt hat erstmals demonstriert, wie Beton, der im Pulverbett 3D gedruckt wurde, auch als Tragwerk dienen kann. Es handelt sich um einen Prototyp für eine Fußgängerbrücke mit Tragweiten von 5 x 2,5 Meter, die in 21 Teilen gedruckt und anschließend trocken gefügt wurde, also ohne Mörtel oder anderes ausgleichendes Material in den Fugen. Bereits in der Planung wurden auch konstruktive Details für die integrierten Zugelemente bedacht, ebenfalls ohne permanenten Verbund. Durch diese Konfiguration ließ sich die gesamte Brücke innerhalb eines Tages montieren sowie mehrmals auf- und abbauen, ohne Teile beschädigen oder zerstören zu müssen. Das Projekt zeigt, wie man ein Material effektiv einsetzt – Beton verfügt über hohe Druckfestigkeiten, aber nur geringe Zugfestigkeiten – und dies sortenrein, um eine eventuelles Re- bzw. Downcycling zu erleichtern.
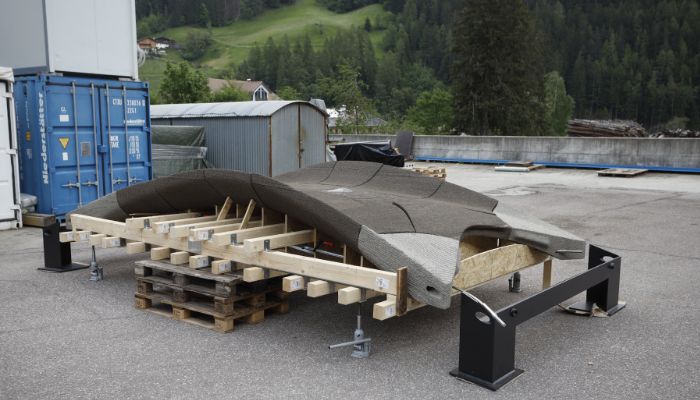
Erste Montage der Brücke auf eigens entwickelter Unterkonstruktion in Sarnthein. (Bild: AMC TRR 277 / Ema Krakovska)
Das zweite Projekt, die Treppe H., ist die bis dato größte Treppe, die wir mit unseren 3D-gedruckten Schalungen realisieren konnten: Eine Freiformtreppe mit elliptischem Grundriss und mehr als drei Meter Durchmesser über zwei Stockwerke. Das Bauunternehmen Tschanen AG aus der Schweiz kontaktierte uns, da die Alternativen das vorhandene Budget überschritten hätten. Dank einer guten Zusammenarbeit zwischen den Planern, dem Bauunternehmen und uns als Produzenten, konnten wir auch mit diesem Projekt beweisen, dass das SPI-Verfahren für verschiedene Anwendungen geeignet ist. Besonders von Vorteil war bei diesem Projekt der einfache Transport von handhabbaren Teilen – im Gegensatz zum Schwertransport einer gesamten Fertigteiltreppe – und die schnelle Montage vor Ort innerhalb weniger Tage. Während Scawo3D noch die Montage des ersten Treppenlaufs übernahm, war die Tschanen AG für den Einbau des zweiten Treppenlaufs bereits bestens gewappnet und schaffte es ebenso schnell. Für die anschließende Oberflächenbehandlung bieten die 3D-gedruckten Teile auch einen guten Untergrund: Der Gipser konnte den Putz direkt auf die Schalungen aufbringen, ohne große Unebenheiten ausgleichen zu müssen.
3DN: Was kann der 3D-Druck der Architektur bieten? Und wo liegen Herausforderungen?
Bisher waren Verfahren für den Beton-3D-Druck in ihren Einsatzgebieten beschränkt. Entweder ließen sich nicht alle Geometrien realisieren oder die Festigkeit sowie Wettertauglichkeit war maßgeblich durch den verfahrensbedingten Schichtenaufbau bzw. das Material beeinträchtigt. Beide Probleme haben wir mit dem SPI-Verfahren in den Griff bekommen. Daraus ergibt sich während des Entwurfsprozesses eine vollkommene Formfreiheit, wodurch sich Bauteile nicht nur ästhetisch anders denken lassen, sondern auch statisch. Das heißt, Betonbauteile können nun zu einem Grad statisch optimiert werden, der zuvor nur mit aufwendigen Schalungsarbeiten möglich war. Aus diesen Gründen bin ich der Meinung, dass der 3D-Druck in der Architektur das Potential hat, eine Revolution loszutreten – inspiriert von Bauweisen, die seit einiger Zeit in Vergessenheit geraten sind.
Durch das Zusammenspiel von Materialeigenschaften und Formfreiheit lässt sich die Massivbauweise bspw. neu denken und optimieren, hin zu weniger komplexen, aber dennoch wärmedämmenden und gleichzeitig tragenden Bauteilen aus nur einem einzigen Material. Geometrisch können diese Teile durchaus komplexer werden als bisher, allerdings mit weniger baulichen Schichten. Dadurch können Gebäude errichtet werden, die durch ihre erhöhte Langlebigkeit nachhaltiger und in Zukunft weniger wartungsintensiv sind. Auch ließe sich die Statik von Gewölbedecken durch computergestützte Methoden ausreizen und der Materialverbrauch in Gebäudedecken dadurch maßgeblich reduzieren, die übrigens den größten Materialanteil in einem Gebäude ausmachen. Beginnen könnte man damit, das teilweise etwas triste deutsche Stadtbild hier und da durch ornamentale Fassaden oder Kunst am Bau aufzuwerten.
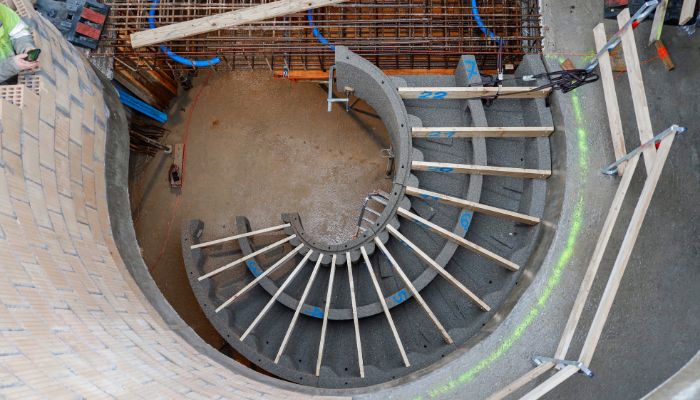
Montage der Treppenschalungen auf der Baustelle: Vollständig eingesetzter erster Treppenlauf ohne Brüstungen (Skeno/Scawo3D)
Die größte Herausforderung wiederum liegt darin, das noch recht neue Verfahren in größerem Maßstab in die Praxis zu überführen. Design- oder Kunstobjekte und auch überschaubare Konstruktionen wie Treppen werden bei uns bereits seit einiger Zeit angefragt und auch abgenommen. Wir sehen aber mehr Potential im SPI-Verfahren. Obwohl hydraulische Bindemittel bereits den Römern bekannt waren, brauchte es bis ins 19. Jahrhundert und die Industrialisierung, bis Zement sich einer breiteren Akzeptanz erfreuen durfte. Was ich damit sagen will: Wir sind am Anfang und es braucht nun mal seine Zeit.
Einerseits ist die Ausgangssituation gut für die additive Fertigung am Bau. Es herrscht Fachkräftemangel, während schnell mehr Wohnraum geschaffen werden muss, und das schenkt der dringend notwendigen Diskussion um Nachhaltigkeit endlich mehr Aufmerksamkeit. Prinzipiell sind also die Voraussetzungen geschaffen für eine neue Technologie, mit der anders und auch schneller gebaut werden kann. Die Kehrseite ist, dass die Branche, gerade in Deutschland, nach wie vor durch Normen strukturiert ist, die wenig durchsichtig sind und sich auf einen Wissensstamm stützen, der den heutigen Anforderungen, aber auch den heutigen Möglichkeiten in der Architektur nicht unbedingt gerecht wird.
Die TU München zeigte durch Projekte und Forschungsergebnisse, wo und wie die additive Fertigung am sinnvollsten im Bauwesen eingesetzt werden kann. In der Forschung tut sich also einiges. Und langsam kann man auch erahnen, dass einige dieser Erkenntnisse in die Praxis übergeleitet werden, bspw. durch Initiativen wie dem „Gebäudetyp E“ in Deutschland. Durch eine Auflockerung der Normen soll Planern und Bauherren mehr Freiheit gegeben werden, einfacher, ressourcenschonender und im besten Falle auch kostengünstiger zu bauen.
Dennoch warten wir aber auf Kunden außerhalb der Forschung, die Mut und zu Beginn auch die finanzielle Bereitschaft zeigen, sich einer neuen Technologie wie dem SPI-Verfahren anzunehmen. Wir haben und werden auch weiterhin demonstrieren, dass ein Bauen in größerem Maßstab in Form von tragenden Bauteilen möglich ist. Mehr zu Scawo3D erfahren Sie auf unserer Website.
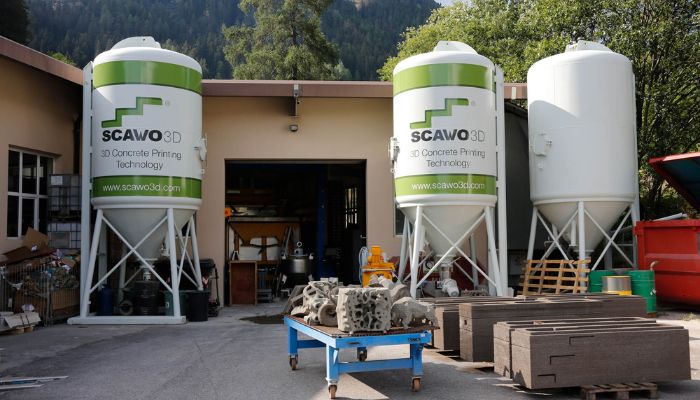
Produktion von Scawo3D in Sarnthein, Südtirol. (Bild: Scawo3D)
Was halten Sie von Scawo3D? Lassen Sie uns dazu einen Kommentar da, oder teilen Sie es uns auf Facebook oder LinkedIN mit. Möchten Sie außerdem eine Zusammenfassung der wichtigsten Neuigkeiten im 3D-Druck und der additiven Fertigung direkt und bequem in Ihr Postfach erhalten? Dann registrieren Sie sich jetzt für unseren wöchentlichen Newsletter.
*Titelbildnachweis: Messestand von Scawo3D auf der BAU 2025 in München (Bild: Skeno/Scawo3D)
„Mit dem SPI-Verfahren brauchen für keinen Platz auf der Baustelle für ein großes Druckerportal, sondern können die Teile je nach Baustelle passend dimensionieren. Zusammengefasst gibt der „Inkjet-Betondruck“ dem Entwerfenden schlichtweg mehr Freiheiten.“
Mit diesem Satz lässt sich wohl schon die zukünftige Dimmension dieses Verfahrens erahnen.
Also Bauten so planen & produzieren, dass diese dann mit einfacheren Mitteln zu Bauplatz transportiert & dort (in Fertigteilen) montiert werden könnten. Ich wünsche dem Team von Scawo3D und seinen Partnern größtmögliche Erfolge.