Wie kann die Rückverfolgbarkeit in der additiven Fertigung durch die Integration digitaler Produktpässe verbessert werden?
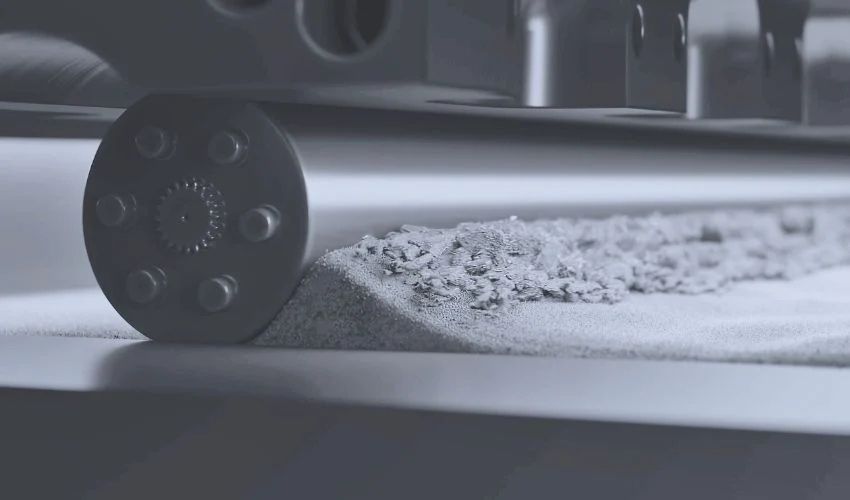
Einer der größten Vorteile der digitalen Fertigung ist die Möglichkeit, Teile über ihre gesamte Lebensdauer hinweg leichter nachzuverfolgen. Die Rückverfolgbarkeit von Produkten ist entscheidend für die Qualitätssicherung, die Einhaltung regulatorischer Vorgaben und die Transparenz in der Lieferkette. Dennoch kann es für Anwender schwierig sein, dieses Potential voll auszuschöpfen und eine wirklich sichere und überprüfbare Dokumentation des Lebenszyklus eines Teils zu erhalten. Deshalb haben wir mit Henrik Peiss und Dr. Ulrich Jahnke darüber gesprochen, wie digitale Produktpässe in die Binder Jetting Technologie von Desktop Metal integriert werden können, um eine Echtzeitverfolgung zu ermöglichen. Wir diskutieren, wie dieser Ansatz die Authentizität verbessert, Zertifizierungsprozesse optimiert und den Weg für eine breite industrielle Nutzung ebnet.
3DN: Könnten Sie sich kurz vorstellen?
HP: Mein Name ist Henrik Peiss. Seit 2021 arbeite ich bei Desktop Metal in Deutschland als EMEA Application Team Lead sowie als Sales & Technical Manager für die DACH-Region und Osteuropa. Mein Hintergrund liegt im Maschinenbau, und in den letzten 13 Jahren war ich weltweit in verschiedenen Rollen in der additiven Fertigungsbranche tätig.
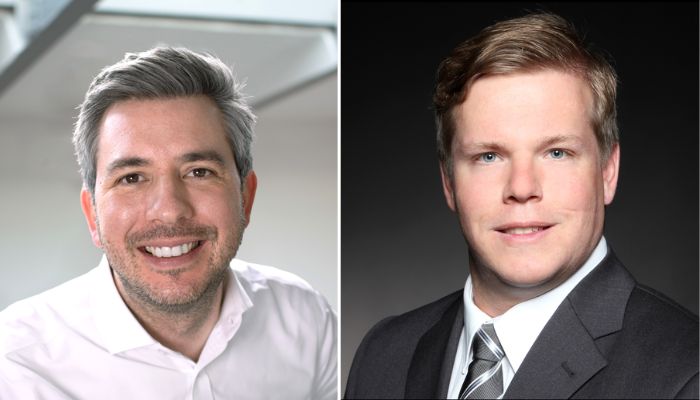
Dr. Ulrich Jahnke (links) und Henrik Peiss (rechts)
UJ: Mein Name ist Dr. Ulrich Jahnke. Ich habe über 15 Jahre Erfahrung im 3D-Druck und in der gesamten Prozesskette der additiven Fertigung, was mir ermöglicht hat, eine tiefgehende Expertise in diesem dynamischen Bereich zu entwickeln. Mein akademischer Werdegang begann mit einem Abschluss in Ingenieurinformatik, gefolgt von Forschungsaktivitäten an der Universität Paderborn, speziell im Direct Manufacturing Research Center (DMRC).
2018 habe ich mit zwei Partnern Additive Marking gegründet, getrieben von der Vision, Rückverfolgbarkeit direkt in 3D-gedruckte Komponenten zu integrieren. Diese Initiative zielt darauf ab, die Prinzipien der Industrie 4.0 auf der Werkbank-Ebene umzusetzen. Unsere innovative Technologie überbrückt die digitale und die physische Welt, indem sie digitalen Identitäten für greifbare Vermögenswerte zuweist, die sowohl additiv als auch konventionell produziert werden.
Seit 2020 setze ich mich leidenschaftlich dafür ein, die Vision von Additive Marking zu verwirklichen und strebe nach umfassender End-to-End-Rückverfolgbarkeit, nicht nur innerhalb der additiven Fertigung, sondern auch über den breiteren industriellen Bereich hinweg. Heute umfasst unser Service- und Produktportfolio auch die Automatisierung von Laserbeschriftung, Punktschriftmarkierung und Etikettierungsprozessen sowie das Management digitaler Produktpässe durch unsere Additive Marking Suite. Natürlich bieten wir nicht nur Hard- und Software für die Markierung und das Scannen an, sondern auch Lösungen, bei denen eine methodische Mischung aus Schulung und Beratung ein verpflichtender Bestandteil ist.
3DN: Warum ist die Produktverfolgbarkeit in der additiven Fertigung wichtig?
HP: Die additive Fertigung (additive manufacturing, AM) ist ein Batch-basierter Prozess. Zum Beispiel arbeiten wir bei einem einzelnen Druckauftrag im Binder Jetting Verfahren mit einer bestimmten Charge Pulver und Binder-Flüssigkeit sowie den entsprechenden Umgebungsbedingungen und dem Maschinenverschleiß. Um die Rückverfolgbarkeit für die Qualitätskontrolle sicherzustellen, ist es wichtig, ein Teil bis zu einem bestimmten Druckauftrag und sogar bis zu einer spezifischen Position des Teils innerhalb dieses Druckauftrags zurückverfolgen zu können.
Dies ist besonders wichtig, wenn Teile für Industrien wie Luft- und Raumfahrt, Verteidigung oder Medizintechnik produziert werden. Die Qualitätsstandards in diesen Branchen erfordern Qualitätsprüfungen und Dokumentationen für jedes einzelne Teil. Die additive Fertigung als digitale Fertigungstechnologie bietet einzigartige Möglichkeiten für die automatische Kennzeichnung von Teilen während des Prozesses der digitalen Druckvorbereitung.
UJ: Ich stimme Henrik zu. Die Produktverfolgbarkeit in der additiven Fertigung spielt eine entscheidende Rolle für die Sicherstellung der Qualitätskontrolle, der Betriebseffizienz und der Einhaltung von Vorschriften. Einer der Hauptvorteile der Verfolgbarkeit ist, dass sie es den Herstellern ermöglicht, jedes Teil entlang seiner gesamten Produktionskette und sogar über den gesamten Lebenszyklus hinweg zu verfolgen – angefangen bei der Datenvorbereitung, Produktion, Nachbearbeitung und Qualitätssicherung bis hin zu Logistik, Nutzungsphase und Recycling. Diese umfassende Verfolgung ist in der additiven Fertigung besonders wichtig, da die Materialeigenschaften und die Maßgenauigkeit eines Bauteils während des Fertigungsprozesses bestimmt werden.
Selbst Parameter, die auf den ersten Blick weniger relevant erscheinen, wie die Bauorientierung und die Positionierung im Bauvolumen, können diese Eigenschaften beeinflussen. Deshalb ist es so notwendig, die Verfolgbarkeit vom ersten Moment der Produktion eines Teils an zu gewährleisten. Und genau hier liegt die Stärke und der einzigartige Vorteil der additiven Markierung: Sie ermöglicht eine direkte Teileidentifikation während der Produktion, ohne dass zusätzliche Kennzeichnungsprozesse erforderlich sind.
Im Gegensatz zur traditionellen Fertigung, bei der Kennzeichnungsprozesse Risiken von Verwechslungen oder Fehlern mit sich bringen können, kann die maschinenlesbare Identifikation der Additive Marking Suite direkt in das Bauteil während des digitalen und physischen Fertigungsprozesses eingebettet werden. Dies reduziert das Potential für Fehler und stellt sicher, dass das Bauteil effizient verfolgbar bleibt.
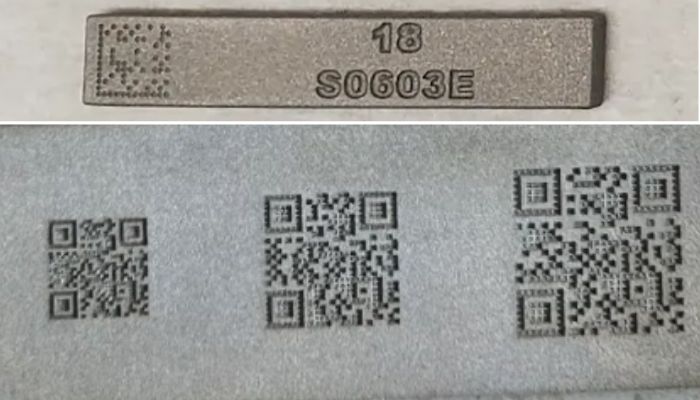
Oberflächentestcoupon mit integriertem Dot-Matrix-Code von Additive Marking, der mit dem digitalen Pass-X-Produktpass des Teils verknüpft ist (oben). Durch Additive Marking erzeugte QR-Codes unterschiedlicher Größe auf einem anderen MBJ-Teil (unten).
Rückverfolgbarkeit ist besonders wichtig in Branchen, in denen Sicherheit und gesetzliche Vorschriften unverhandelbar sind. Sie ermöglicht es den Herstellern, Mängel oder Abweichungen schnell zu identifizieren und zu beheben, wodurch effiziente Rückrufe oder Ersatzlieferungen bei Bedarf möglich werden.
Darüber hinaus stärkt die Rückverfolgbarkeit die Integrität der Lieferkette, unterstützt das effiziente Management digitaler Bestände und erleichtert die Verfolgung von Ersatzteilen. Durch das Scannen eines eingebetteten Codes auf einem Teil, beispielsweise. mit unserer DPM Scan Pro Scan Engine, die für iOS, Android sowie für die stationäre Integration mit industriellen Kamerasystemen verfügbar ist, können Hersteller sofort auf die zugehörigen Dateien in einem digitalen Lager zugreifen, was die Teileidentifikation vereinfacht und Ausfallzeiten reduziert.
3DN: Können Sie uns mehr über digitale Pässe und deren Funktionsweise erzählen?
UJ: Digitale Pässe sind ein revolutionäres Konzept im Bereich der Produktverfolgbarkeit, insbesondere in der additiven Fertigung. Ein digitaler Pass dient als umfassende digitale Aufzeichnung für jedes Bauteil und enthält wichtige Informationen wie Materialspezifikationen, Fertigungsprozesse und Bearbeitungsparameter, Qualitätskontrolldaten, die Wartungshistorie des Bauteils usw. Diese Informationen werden in einem sicheren digitalen Format gespeichert und können während des gesamten Lebenszyklus des Produkts über den im Bauteil, Produkt oder der Maschine eingebetteten Code abgerufen werden.
Indem alle relevanten Produktdaten auf einer einzigen, zugänglichen Plattform wie pass-x.eu zusammengeführt werden, ermöglichen digitale Produktpässe den Herstellern, die Produktqualität, Kundenzufriedenheit und die gesamte betriebliche Effizienz zu verbessern. Auf pass-x.eu wird Interoperabilität mit parallel gehosteten Plattformen durch gemeinsame Standards gewährleistet! Zu den bemerkenswerten Vorteilen gehören:
- Sicherstellung der Einhaltung von Vorschriften und gesetzlichen Bestimmungen, z.B. der Ökodesign-Verordnung für nachhaltige Produkte, der Allgemeinen Produktsicherheitsverordnung, der Batterie-Verordnung usw.
- Volle Rückverfolgbarkeit und Transparenz während des gesamten Produktlebenszyklus und Nutzung von Lebenszyklusinformationen in der nächsten Entwicklungsstufe
- Unterstützung von Nachhaltigkeit und Kreislaufwirtschaft durch Hilfe beim Recycling und der Wiederverwendung
- Stärkung des Kundenvertrauens durch Transparenz und sogar Bereitstellung von Cross-Selling-Möglichkeiten
- Optimierung des Ersatzteilmanagements und der Lebenszyklusverfolgung
HP: Die digitalen Bauteilpässe können als eine Umsetzung des digitalen Zwillingskonzepts zusammengefasst werden und fungieren als zentraler Punkt der Datenspeicherung/Verknüpfung für alle digitalen Informationen rund um ein einzigartiges, spezifisches Bauteil.
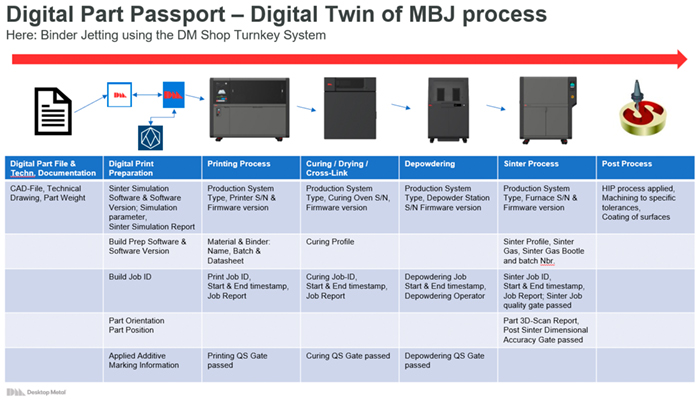
MBJ-Prozessdiagramm und zugehörige Prozessschrittdaten, die in den digitalen Teilpass eines Bauteils integriert wurden.
Aus der Sicht des Nutzers ist ein digitaler Bauteilpass, wie er von Additive Marking implementiert wird, der logische zweite Schritt nach der Rückverfolgbarkeit von Bauteilen basierend auf einzigartigen Serienmarkierungen auf den Bauteilen. Der Pass ermöglicht einfachen Zugriff und die Speicherung einzigartiger Informationen zu einem bestimmten Bauteil und ist digital über eine einzigartige maschinenlesbare Markierung auf dem Bauteil zugänglich. Es ist möglich, spezifische Abschnitte des Passes einzurichten, wobei einige nur für den Hersteller sichtbar sind, während andere für alle Nutzer zugänglich sind.
Mit ihm kann der Nutzer Qualitätsberichte eines Bauteils, Produktionsdaten, entsprechende Materialdatenblätter, Benutzerhandbücher oder Wartungspläne des Bauteils einsehen. Wenn ein Web-Shop-Link ebenfalls in den digitalen Pass integriert ist, kann der Nutzer das Bauteil oder die entsprechenden Vorräte direkt nachbestellen.
3DN: Welche Vorteile bietet dies speziell im Bereich des Binder Jetting?
HP: Binder Jetting als Additive Manufacturing 2.0-Technologie konzentriert sich auf die Serienproduktion von hunderten oder sogar mehr Bauteilen. Die Bedeutung der Rückverfolgbarkeit einzelner Bauteile nimmt zu, wenn diese in die oben genannten Branchen geliefert werden. Abgesehen von der Nutzung in diesen Bereichen hilft die Rückverfolgbarkeit der Bauteile auch im täglichen Betrieb eines digitalen Produktionszentrums für additive Fertigung: Abgeschlossene Produktionsschritte und interne QA-Check-Gates können einfach durch die Verwendung der maschinenlesbaren Codes auf den Bauteilen durchgeführt und dokumentiert werden.
Ein allgemeiner Vorteil des Binder Jetting in Kombination mit digitaler Bauteilkennzeichnung ist die Tatsache, dass Binder Jetting kleinere Bauteilmarkierungen ermöglicht, die durch das Schrumpfen während des Sinterprozesses bedingt sind. Das bedeutet, dass der Druck eines Bauteils sowie dessen digitale Markierung in einem um 20 % vergrößerten Zustand erfolgt. Beim Sintern schrumpft das Bauteil um 20 % und damit auch die Markierung. Dies wird besonders wichtig, wenn sehr kleine Bauteile markiert werden sollen, was mit anderen Technologien wie LBPF nicht möglich ist.
UJ: Die Rückverfolgbarkeit im Binder Jetting bietet mehrere bedeutende Vorteile, insbesondere angesichts der Komplexität der Prozesskette von der Datenvorbereitung bis zum fertigen Bauteil. Da Binder Jetting mehrere Stufen umfasst, wie Datenvorbereitung, Materialauswahl, Schichtablagerung, Aushärtung usw., ermöglicht die Rückverfolgbarkeit die Qualität über alle Phasen hinweg zu verfolgen, um zukünftige Druckvorgänge zu optimieren und eine gleichbleibende Qualität über alle Produktionsdurchläufe hinweg zu gewährleisten, insbesondere bei komplexen Geometrien oder Hochleistungsmaterialien.
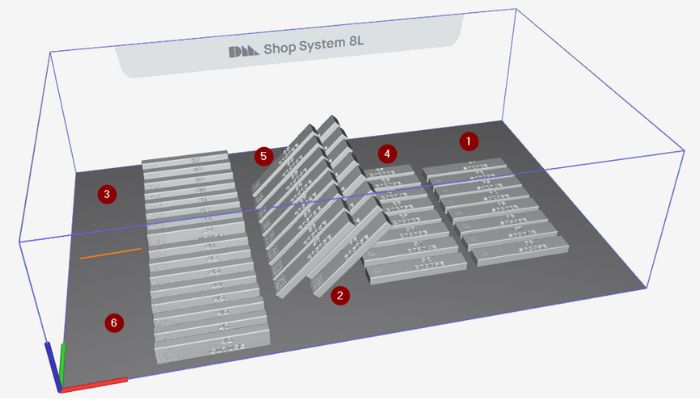
Desktop Metal Shop System Bauvolumen gefüllt mit Oberflächentestproben, die mit Punktmatrixcodes markiert sind. Die Teile sind in verschiedenen Ausrichtungen angeordnet.
Aufgrund der hohen Auflösung, die im Binder Jetting Prozess erreicht werden kann, können maschinenlesbare Codes auf kleinsten Oberflächenbereichen realisiert werden und erfüllen beispielsweise die Anforderungen der GS1-Spezifikationen, um mit gängigen Regulierungsbehörden wie der Medizinprodukteverordnung konform zu sein. Darüber hinaus sind Versionskontrolle und Designiteration im Binder Jetting ebenso wichtig wie in allen anderen agilen Fertigungstechniken. Das direkte Einbetten von Druckmarken in die digitalen Produktdaten vor der Produktion ist der einfachste Weg, um Transparenz und Verantwortlichkeit zu gewährleisten.
3DN: Könnten Sie uns ein praktisches Beispiel erklären, das den Lebenszyklus eines Teils umfasst?
HP: Für mich ist eine interessante Anwendung ein kundenspezifisches Teil, das mit einer Markierung versehen ist, die mit seinem digitalen Pass verbunden ist. Der Ursprung dieses Teils wäre ein [Internet-]Benutzer, der die gewünschten Teileparameter in die [webbasierte] Software des Konfigurators [z. B. in einem Webshop] eingibt, die die Form, Textur, Material und Beschichtung eines parametrischen Designs definiert. Sobald der Benutzer das Design zur Produktion speichert, wird eine eindeutige Seriennummer generiert, die einen einzigartigen digitalen Pass für das Teil initiiert.
Dieser Pass würde die vom Benutzer definierten Anpassungsparameter des Teils als erste Einträge erhalten. Wenn das digitale Teil in die Produktionsvorbereitung übergeht, werden die Softwareversionen und die angewendeten Einstellungen der Druckvorbereitungssoftware sowie die Simulationseinstellungen und -ergebnisse der Teileproduktion zum Pass hinzugefügt. Die additive Fertigung über Binder Jetting ist ein mehrstufiger Prozess; daher würden Produktionsstatusberichte für Binder Jetting [Druckprotokoll & Zeitraffer, Profil + Log des Härtofens, Depowder-Inspektion QS-Check-Ergebnisse und Sinterprofil & -log sowie Ofenposition in den digitalen Pass des Teils integriert]. Nachbearbeitungsschritte wie der angewendete HIP-Prozesszyklus und -protokolle oder die aufgebrachte Beschichtung [RAL-Nummer usw.] sowie z. B. 3D-Scan-basierte Messberichte würden ebenfalls hinzugefügt.
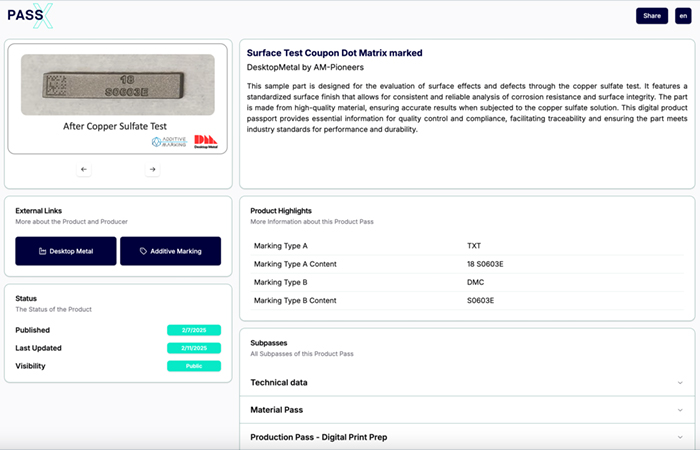
Die Additive Marking pass-x Produktpass-Website in der internen Setup-Ansicht. Gezeigt wird der Setup-Modus der MBJ-Produktionsdaten eines Oberflächentest-Coupons.
Diese Informationen können als Produktionsdokumentation zusammengefasst werden und wären später nur für den Hersteller zugänglich. Nach der Produktion würde das Teil in einer Baugruppe montiert und das Endprodukt an einen Kunden verkauft. Montageinformationen sowie die Seriennummer des Endprodukts und der CO2-Fußabdruck des Teils würden zum digitalen Produktpass des Teils hinzugefügt.
Während der Nutzung des Teils kann die Teilemarkierung von einem Benutzer gescannt werden, und der verknüpfte webbasierte digitale Produktpass öffnet sich in einem Internetbrowser. Der für den Benutzer sichtbare Inhalt des digitalen Produktpasses würde dem Benutzer beispielsweise das Benutzerhandbuch, Wartungspläne für das Teil oder die Baugruppe, einen Link zu einem Webshop zum Bestellen benötigter Verbrauchsmaterialien oder zum Nachbestellen des Teils in seiner genauen Anpassung anzeigen. Nach dem Ende der Lebensdauer des spezifischen Teils enthält der digitale Produktpass die erforderlichen Informationen darüber, wie das Teil zu entsorgen oder zu recyceln ist.
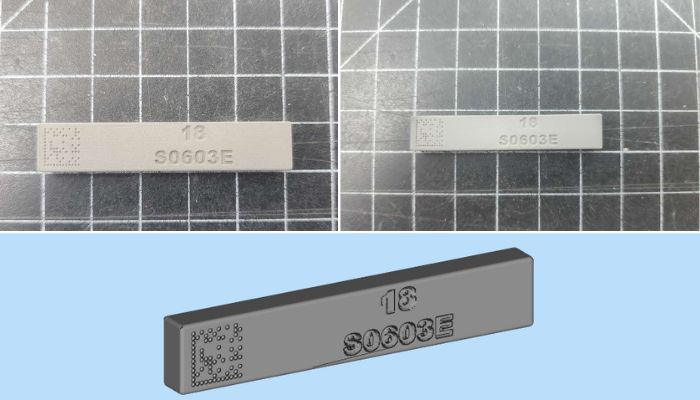
Dot-Matrix-Code-markierter Oberflächentest-Coupon während der MBJ-Produktion. Bereits im Grünzustand (links) sind die Codes auf den Teilen maschinenlesbar und können gescannt werden, um die Teile nach dem Bestehen der Qualitätskontrollen der Produktionsschritte „einzuchecken“. Das rechte Bild zeigt das Teil nach dem Sintern – Teil und Code sind um ca. 20 % auf ihre endgültigen Abmessungen geschrumpft. Unten ist das Teil in der digitalen Produktionsphase zu sehen, verfügbar im oben genannten Link.
UJ: Ein weiteres praktisches Beispiel aus meinem täglichen privaten und geschäftlichen Leben betrifft Ersatzteile für verschiedene Anwendungen. Es muss nicht unbedingt ein hochpreisiges Teil sein. Nehmen wir ein einfaches Ersatzteil für eine 24/7-Produktionsanlage. Dieses Teil würde eine Reihe von Phasen durchlaufen, vom Design über die Nachbearbeitung, Tests und die endgültige Validierung, wobei ein digitaler Produktpass seinen gesamten Lebenszyklus verfolgt.
Das Design des Teils wird mit CAD-Software erstellt. Der digitale Produktpass wird bereits im Vorfeld bei der Bestellung des Designs und der Spezifikation der Anforderungen aktiviert. Als erste Dateneingabe werden die CAD-Datei (Version), die Materialwahl, die geometrische Spezifikation sowie die gewünschte Fertigungstechnik im digitalen Produktpass (DPP) vollständig dokumentiert. Das Erstellen einer oder mehrerer individueller Ausführungen dieses Teils mit eingebetteten individuellen Seriennummern (menschlich und/oder maschinenlesbar) wird erneut eine Dateneingabe für den DPP erzeugen: Materialcharge, Lieferantenname und Zertifikate, Materialeigenschaften dieser spezifischen Charge sowie alle relevanten Daten, die vom AM-System aufgezeichnet wurden.
Nächster Schritt: Verknüpfung aller Nachbearbeitungsinformationen wie Zeitstempel für jede Station, Prozessparameter, persönliche Qualifikationen und später die Berichte der Qualitätssicherung (QA).
All diese Daten, die mit dem physischen Bauteil verknüpft sind, sind einfach zugänglich, indem man die individuelle Markierung scannt, was den weiteren Lebenszyklus erleichtert. Einige Beispiele sind:
Zertifizierung und Konformität: Nun kann eine dritte Partei die Konformitätsdokumentation verknüpfen.
Der Benutzer des Bauteils, der das Bauteil als Teil einer Baugruppe verwenden möchte, hat auch nur einen Scan entfernt Unterstützung für die Montage.
Die Bestellung auf Abruf war noch nie so einfach. Scannen Sie den Code, werden Sie zu pass-x.eu weitergeleitet und bestellen Sie ein neues Ersatzteil, während Sie das defekte Teil melden. Der Hersteller erhält Informationen über die Lebensdauer des defekten Teils, was für das Redesign nützlich ist.
Kreislaufwirtschaft und Abfallmanagement sind immer herausfordernd, hier wäre es möglich, das Material eines Bauteils zu identifizieren. Wiederum: Nur ein Scan, und die Bauteile können effizient recycelt werden, da das Material gut bekannt ist und im Materialpass eines digitalen Produktpasses verknüpft ist.
3DN: Haben Sie noch abschließende Worte an unsere Leserschaft?
HP: Vielen Dank, dass Sie mich zu diesem Interview eingeladen haben. Mehr über Desktop Metal und Binder Jetting sowie wie wir Traceability integrieren, erfahren Sie HIER.
UJ: Danke für das nette Interview! Ich freue mich darauf, den Nutzern zu helfen, die Rückverfolgbarkeit weiter zu verbessern und digitale Produktpässe zu nutzen! Erfahren Sie mehr über uns HIER.
Was denken Sie über die Rückverfolgbarkeit von Produkten in der additiven Fertigung? Lassen Sie uns dazu einen Kommentar da, oder teilen Sie es uns auf Facebook oder LinkedIN mit. Möchten Sie außerdem eine Zusammenfassung der wichtigsten Neuigkeiten im 3D-Druck und der additiven Fertigung direkt und bequem in Ihr Postfach erhalten? Dann registrieren Sie sich jetzt für unseren wöchentlichen Newsletter.
*Bildnachweise: Desktop Metal/Additive Marking