Prōtóplasto zeigt neue Perspektiven für den Einsatz von Kunststoffen in der Architektur auf
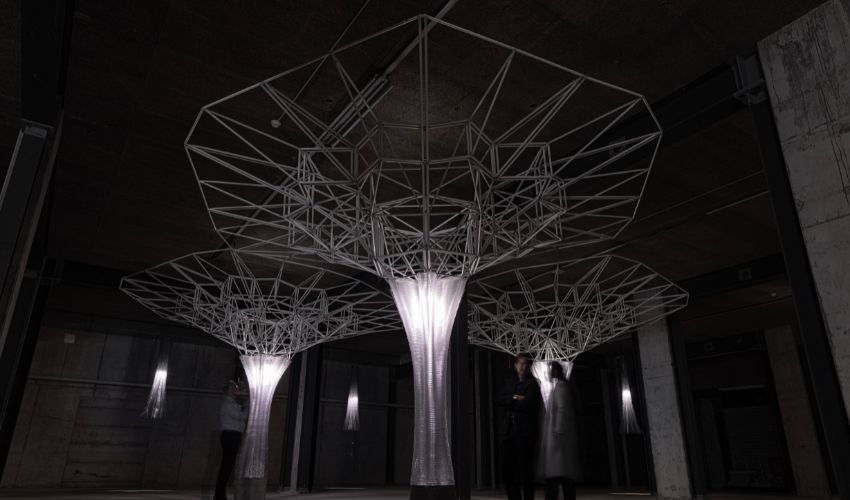
Das Bauwesen ist auf eine limitierte Auswahl an Bauwerkstoffen beschränkt, allen voran Beton. Die Materialforschung und innovative Projekte ermöglichen zwar eine beständig umfangreichere Materialpalette, dennoch bleiben Herausforderung bestehen, wenn es um Ziele wie Leichtbau, Nachhaltigkeit und Materialeffizienz geht. Kunststoffe sind deshalb für die Architektur interessant, da sie ein vorzügliches Verhältnis von Gewicht zu Festigkeit bieten, kostengünstig und wiederverwertbar sind. Vor allem faserverstärkte Werkstoffe ermöglichen leichte, aber stabile Konstruktionen und ein spannendes Anwendungspotential im Bauwesen. Durch den verstärkten Einzug des 3D-Drucks in die Architektur ergeben sich so neue Möglichkeiten, Plastik auch für das Bauwesen zu nutzen. Wie das gehen und aussehen kann, zeigt das Projekt Prōtóplasto, das in einer Kollaboration der ETH Zürich, Halter AG, Castioni Kunststoffe und SAEKI Robotics AG entstanden ist.
Prōtóplasto ist eine Medieninstallation, welche temporär im Innovationszentrum “Futurama” in Aargau in der Schweiz zu sehen ist. Dabei handelt es sich um ein Bausystem, das Leichtbau, Transparenz und 3D-Druck kombiniert und neue Wege für die Architektur der Zukunft aufzeigt. Die Teile der Konstruktion wurden in verschiedenen 3D-Druckverfahren aus Kunststoffen gefertigt, welche sich durch ihre Materialeffizienz auszeichnen und für eine nachhaltige Architektur stehen. Die gesamte Installation kann nach ihrem Abbau außerdem nach Materialien getrennt, recycelt und wiederverwertet werden. Damit schließt sich der Kreis, denn “Prōtóplasto“ leitet sich vom Griechischen „πρωτόπλαστος“ ab und steht für „das zuerst Geformte“.
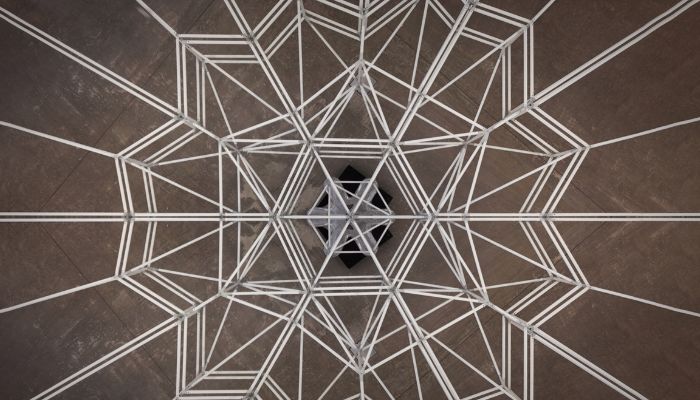
M. Kladeftira
Ein Zusammenspiel aus innovativen Technologien
Die Medieninstallation erstreckt sich über eine Fläche von 65 m2 und besteht aus 2,2 m hohen Pilzsäulen zu je 3,8 kg/m2, die einen Pavillon bilden. Dafür waren 535 Glasfaserstäbe und 291 Verbindungsstücke nötig, welche jeweils per 3D-Druckverfahren gefertigt wurden. Dadurch konnten besonders leichte Komponenten erzielt werden. Die gesamte Konstruktion wiegt nur 250 kg und kann gänzlich ohne Gerüst von Menschenhand und Drohnen zusammengebaut werden. Tatsächlich war nicht nur der 3D-Druck an diesem Resultat beteiligt, denn es flossen mehrere innovative Technologien in das Projekt ein – und zwar von Anfang an! Von der Konzeption über die Fertigung der Bestandteile bis zur geometrischen Anordnung der Elemente von Prōtóplasto war die Entwurfsberechnung entscheidend. Digitale Computer Tools erlaubten es den Designern, Prōtóplasto in verschiedenen Umgebungen zu testen und Augmented Reality erleichterte das Planen und Visualisieren. Beim Herstellungsverfahren galt es, eine gusslose und abfallfreie Methode zu finden, die dennoch leichte Bauteile ermöglichte, und so fiel die Wahl auf die additive Fertigung.
Für die Produktion der ultraleichten Säulen kam der 3D-Hohlkerndruck (Hollow-Core 3D Printing, HC3DP) zum Einsatz. Bei diesem Extrusionsverfahren werden Polymere in Röhrenform gedruckt, welche an hohle Perlen erinnern, die zu 99 % aus Luft bestehen. Eine spezielle Düse formt den Kunststoff zu einer hohlen Perle, welche durch eingeblasene Druckluft anschwillt und das Zusammenfallen der dünnen Wände verhindert, wenn das Material abkühlt. Daraus ergeben sich transparente Bauteile, die äußerst leicht sind, aber dennoch stabil genug, um eine Last von bis zu 200 kg tragen zu können. Bei diesem patentierten Verfahren von SAEKI wird der Materialverbrauch erheblich reduziert, wobei gleichzeitig die Aufbauraten erhöht werden können. Die Druckgeschwindigkeit ähnelt der des 3D-Betondrucks und im Vergleich zu Pellet-Systemen kann durch die hohlen Perlen 80 % Material gespart werden.
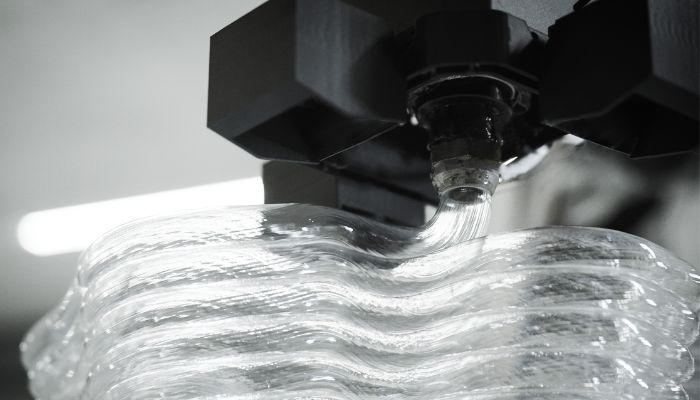
Hollow Core 3D Printing (Bild: Girts Apskalns)
Die per HC3DP gefertigten Säulen fußen auf einem Betonfundament, das mit HC3DP-Schalung gegossen wurde und münden nach oben hin in ausladende Dächer. Für die Verbindungsstücke zu den Dachelementen wurde ebenfalls ein 3D-Druckverfahren herangezogen, nämlich MJF. Die Verbindungsstücke aus PA12 zeichnen sich durch ihr geringes Gewicht und die intuitive Montage aus, da sich die Verbindungen mit den Dachmodulen durch den Einfluss der Schwerkraft selbst verriegeln. Somit sind bei der Montage keine Stützen nötig.
Prōtóplasto beeindruckt nicht nur durch seine Symbiose von innovativen technologischen Ansätzen – darunter u.a. 3D-Druck, AR, Generatives Design – sondern auch durch seine Ästhetik. In Kombination mit dem geringeren Materialverbrauch, Leichtbau und dem ganzheitlichen Kreislaufansatz zeigt Prōtóplasto neue Perspektiven für die Verwendung von Kunststoffen in der Architektur auf. Mehr zu Prōtóplasto finden Sie HIER.
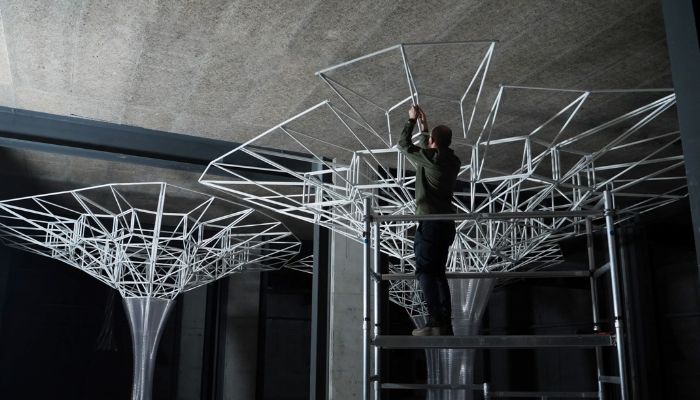
Montage der Dachelemente (Bild: Girts Apskalns)
Was halten Sie von Prōtóplasto? Lassen Sie uns dazu gerne einen Kommentar da oder teilen Sie uns Ihre Meinung auf Facebook oder LinkedIN mit. Möchten Sie außerdem eine Zusammenfassung der wichtigsten Neuigkeiten im 3D-Druck und der additiven Fertigung direkt und bequem in Ihr Postfach erhalten? Dann registrieren Sie sich jetzt für unseren wöchentlichen Newsletter.
*Titelbildnachweis: A. Jipa