Pepsi setzt bei Flaschen auf die Vorteile der additiven Fertigung
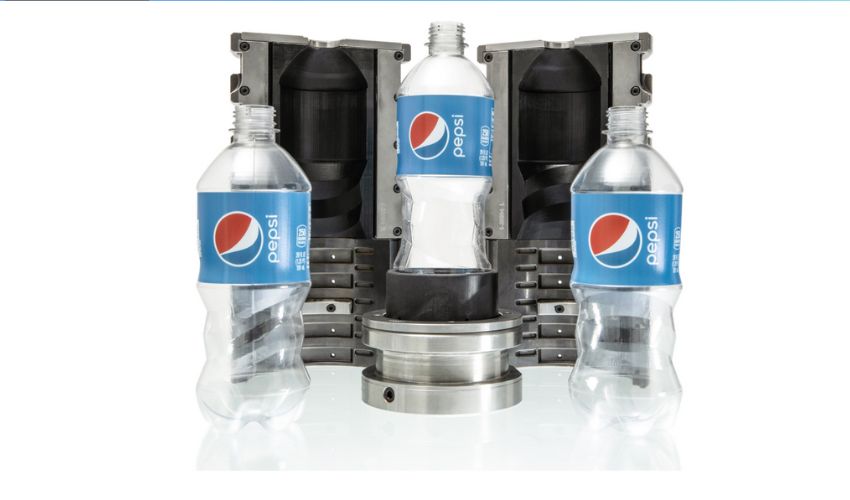
Wir alle kennen es und haben es schon mit Sicherheit einmal in unserem Leben konsumiert: Pepsi. Das ikonische Kult-Getränk aus den USA findet man nahezu in jedem Supermarkt – in Plastikflaschen. Auch wenn bereits der Geschmack des Getränks einzigartig ist, haben sich das in New York angesiedelte Unternehmen und dem Nexa3D-Partner Dynamism zusammen getan, um eine noch einzigartigere Lösung für die Verbesserung der Flaschen zu finden. Das Ziel war es in erster Linie, eine Kostenreduzierung und eine schnellere Produktion auf die Beine bringen zu können. Aus diesem Grund hat man hierfür den NXE 400 3D-Drucker und das xPEEK147 Material verwendet, die sich ideal für die Anwendung von Blasformen eignen.
Mehr als eine Milliarde Menschen in über 200 Ländern dieser Welt kommen tagtäglich in den Genuss von Pepsi-Produkten. Mit einem erzielten Nettoumsatz von mehr als 79 Mrd. US-Dollar im Jahr 2021 hat sich der amerikanische Konzern mit Dynamism nun der Herausforderung der schnellen Markteinführung innerhalb der Konsumgüterbranche annehmen zu können. Die sich ständig verändernden Kundenwünsche veranlassen Unternehmen wie PepsiCo sich stets mit neuen Flaschen- und Verpackungsdesigns zu beschäftigen. Die Problematik bei der herkömmlichen Fertigung: sie dauert äußerst lange. So kann es schon einmal bis zu sechs Wochen dauern, bis ein Prototyp final hergestellt werden kann. Um diesen Prozess allerdings zu verkürzen und wirtschaftlich interessanter zu gestalten, hat man sich bei PepsiCo nun für den Einsatz der additiven Fertigung entschieden. Nachdem allerdings auch dessen Anfänge für kostspielige Probleme sorgten, hat sich die Allianz zwischen PepsiCo und Dynamism einem hybriden Ansatz gewidmet.
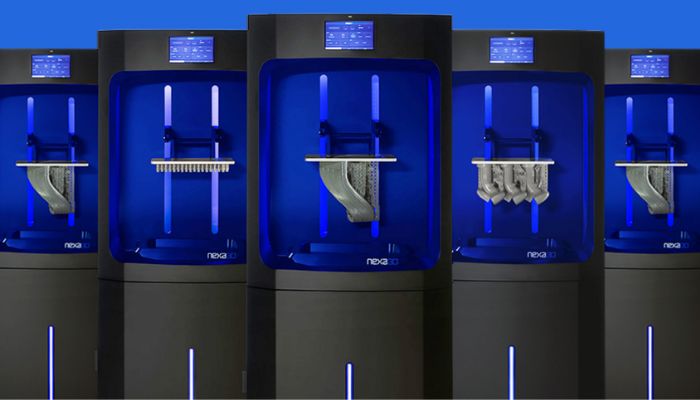
PepsiCo nutzt die NXE400 3D-Drucker von Nexa3D (Bild: Nexa3D)
Pepsi profitiert von additiven Vorteilen der Flaschenproduktion
Unter der Verwendung des NXE400 3D-Drucker von Nexa3D hat können etliche Indikatoren für eine verbesserte Leistungssimulation für Pepsi erzielt werden. Neben der Herstellung von hochwertigen, funktionalen Prototypen und fortschrittlicher Systemanalyse, profitiert man in diesem Fall konkret von einer reduzierten Entwicklungszeit für Prototypen auf 48 Stunden. Auch was die Kostenfrage angeht, so können diese von 10.000 US Dollar auf 350 US Dollar pro Werkzeugsatz gesenkt werden, wie auch die Erhöhung des Produktlebenszyklus dieser Werkzeuge, die für die Herstellung der Flaschenformen eingesetzt werden.
Max Rodriguez, Senior Manager of Global Packaging R&D, Advanced Engineering und Design bei PepsiCo gibt an, dass man mit einem von rund 30 %. Zu verdanken ist dies dem im Jahr 2020 patentierten Hybridmodell, welches eine universelle Formschale aus Metall umfasst, welche in die meisten kommerziellen Blasformmaschinen passt. Zwar ist die Kosten- und Zeiteffizienz laut Rodriguez ein wichtiger Grund für die Verwendung des 3D-Drucks, allerdings räumt er zusätzlich ein: „aber noch wichtiger ist es, die Flexibilität zu haben, eine Reihe von verschiedene Design-Iterationen in Rekordzeit zu durchlaufen, damit wir die Leistung bei allen nachgelagerten Aktivitäten bewerten können. Das ist es wirklich was uns hilft, schneller zu werden.“ Wenn Sie mehr über die additive Fertigung im Flaschenherstellungsprozess bei Pepsi erfahren möchten, dann finden Sie HIER die gesamte Case Study zum Nachlesen.
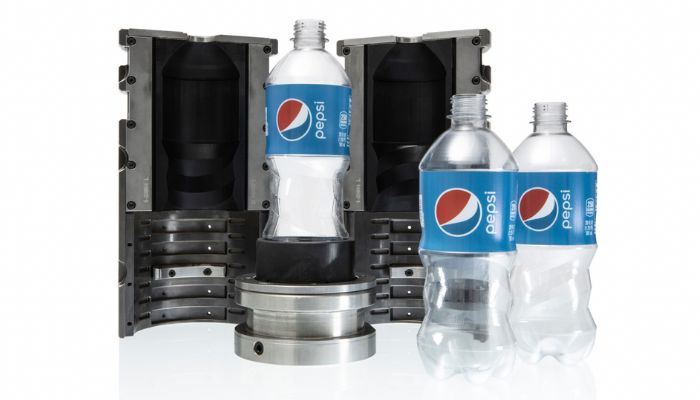
Bild: Nexa3D
Was denken Sie von der additiven Nutzung von Pepsi-Flaschen? Lassen Sie uns dazu gerne einen Kommentar da, oder teilen Sie uns Ihre Meinung auf Facebook, Twitter, LinkedIN oder Xing mit. Möchten Sie außerdem eine Zusammenfassung der wichtigsten Neuigkeiten im 3D-Druck und der Additiven Fertigung direkt und bequem in Ihr Postfach erhalten? Dann registrieren Sie sich jetzt für unseren wöchentlichen Newsletter.
*Titelbildnachweis: Nexa3D