PARI-Forscher zeigen, wie 3D-gedruckte dunkle Keramiken Hyperschalltechnologie vorantreiben
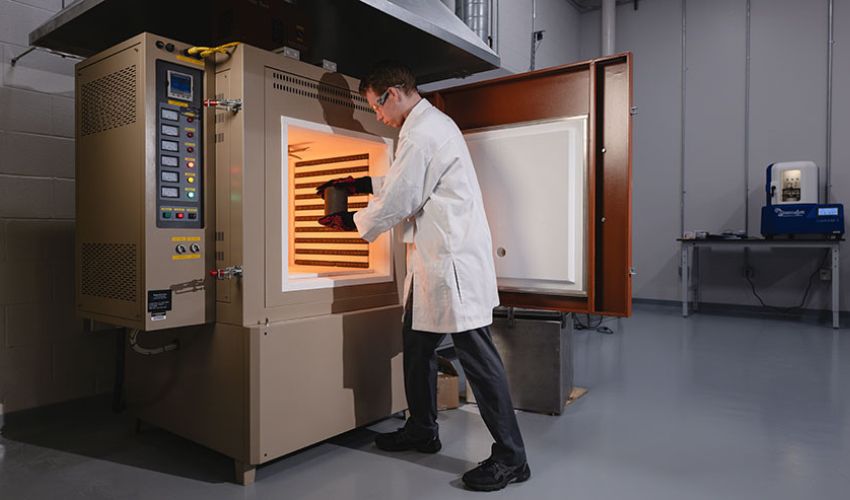
Hyperschalltechnologie gehört zu den herausforderndsten Bereichen der modernen Luft- und Raumfahrt. Fahrzeuge, die mit mehr als der fünffachen Schallgeschwindigkeit unterwegs sind, müssen extremen Bedingungen standhalten, darunter Temperaturen von über 2000°C und enorme mechanische Belastungen. Herkömmliche Materialien stoßen hier schnell an ihre Grenzen. Forscher am Purdue Applied Research Institute (PARI) entwickeln nun additive Fertigungsverfahren, um dunkle Keramiken in komplexen Formen für die Komponenten von Hyperschallfahrzeugen mittels 3D-Druck herzustellen. Dunkle Materialien wurden hierbei gewählt, da sie den extremen Bedingungen des Hyperschallfluges standhalten und weniger anfällig für Risse oder Abnutzung sind. Rodney Trice, Professor an der School of Materials Engineering der Fakultät für Ingenieurwissenschaften und leitender Experte für Keramikverarbeitung am Hypersonics Advanced Manufacturing Technology Center (HAMTC) von PARI, leitet die Forschung mit dem Ziel, Komponenten im großen Maßstab in 3D zu drucken, um die Effizienz und Leistung von Hyperschallfahrzeugen zu steigern.
Das Team verwendete 3D-Drucker am HAMTC, die auf der Technologie des Digital Light Processing (DLP) basieren und mit einem UV-Lichtprojektor arbeiten. Dieser bestrahlt eine dünne Schicht aus Keramikpulver und Harz, wodurch das Material aushärtet und das Pulver fixiert wird. Trice betont, dass durch diesen Prozess komplexe Designs und Geometrien mit glatten Oberflächen und einer Präzision im Mikrometerbereich hergestellt werden können. So ist es dem Team gelungen, unterschiedliche Formen zu produzieren, darunter Kegel und Halbkugeln, die sich für den Bau von Hyperschallfahrzeugen eignen. Dennoch brachte die Forschung Herausforderungen mit sich, insbesondere in Bezug auf die Interaktion der Farbe mit dem UV-Licht des 3D-Druckers. Helle Keramiken wie Aluminiumoxid reflektieren und streuen das Licht, wodurch eine gleichmäßige Aushärtung der gesamten Schicht ermöglicht wird. Dunkle Keramiken hingegen neigen dazu, Licht zu absorbieren, was den Aushärtungsprozess behindert. „Da dunkle Pulver das UV-Licht absorbieren, das zum Aushärten des Materials erforderlich wäre, können wir keine so dicke Schicht bilden. Dadurch erhalten wir geringere Aushärtungstiefen, was sich wiederum negativ auf die Zeit auswirkt, die für den Bau jedes Teils benötigt wird“, erklärt Trice.
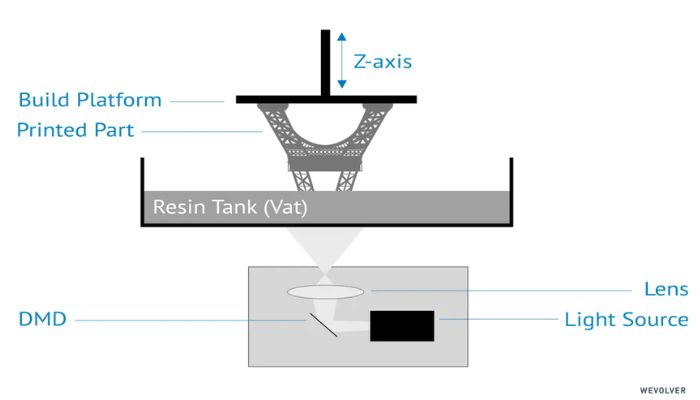
Die Darstellung des klassischen DLP-Verfahrens, das ursprünglich von EnvisionTEC kommerzialisiert wurde. (Bild: Wevolver)
Aus diesem Grund arbeitete er mit Matthew Thompson, einem Doktoranden der Werkstofftechnik, sowie Dylan Crump, einem Keramikforschungsingenieur am HAMTC, zusammen, um Harzsysteme, Oberflächenbehandlungen und andere Ansätze zur Erhöhung der Aushärtungstiefe zu erforschen. „Wir haben im Wesentlichen als Forschungs- und Entwicklungsprüfstand für diese Materialien gearbeitet. So haben wir Materialeigenschaften angepasst und Oberflächenmodifikationen vorgenommen, um ihre Leistung zu verbessern und den Druckprozess zu optimieren“, betont Thompson. Das Team arbeitet zudem daran, Probleme in der Nachbearbeitungsphase zu vermeiden, die sich bei größeren Bauteilen als besonders schwierig erweisen. So können beispielsweise Delaminationen, also das Ablösen oder Auftrennen eines Teils in Schichten, oder Rissbildung auftreten. „Wir versuchen, Lösungen zu finden, wie wir entweder eine Pipeline zur Herstellung dieser Teile einrichten oder Strategien entwickeln, die von den tatsächlichen Anwendern genutzt werden können. So erhalten Entwickler einen Ausgangspunkt, um Zeit bei der Forschung und Entwicklung für jedes neue System zu sparen“, erklärt er weiterführend. HIER erfahren Sie mehr über die Forschung.
Was halten Sie von der Forschung am PARI und den 3D-gedruckten dunklen Keramiken? Lassen Sie uns dazu einen Kommentar da, oder teilen Sie es uns auf Facebook oder LinkedIN mit. Wenn Sie mehr zum 3D-Druck in der Luft- und Raumfahrt lesen möchten, schauen Sie auf unserer Landing Page vorbei. Möchten Sie außerdem eine Zusammenfassung der wichtigsten Neuigkeiten im 3D-Druck und der additiven Fertigung direkt und bequem in Ihr Postfach erhalten? Dann registrieren Sie sich jetzt für unseren wöchentlichen Newsletter.
*Titelbildnachweis: Purdue University/Charles Jischke