PA11 vs PA12: Welche Nylon-Art sollte man wählen?
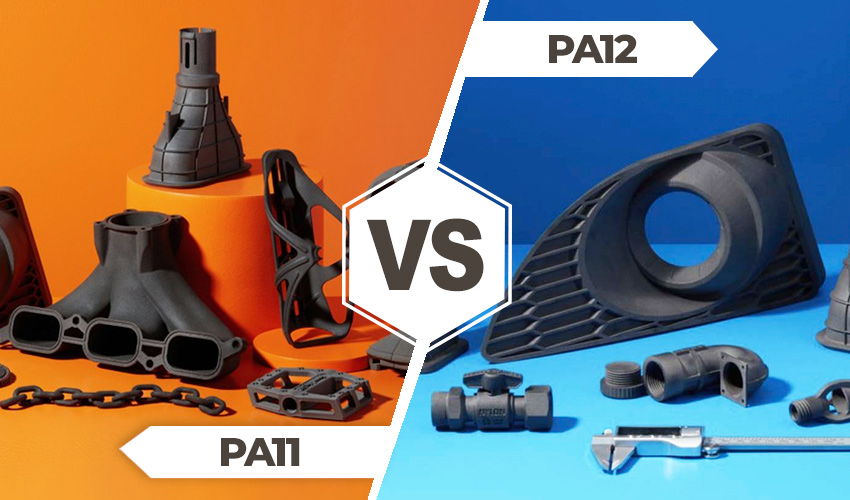
Nylon, auch als Polyamid (PA) bekannt, ist eine im 3D-Druck häufig angewendete thermoplastische Polymer- bzw. Kunststoff-Materialgruppe. Nylon wird insbesondere für seine Eigenschaften geschätzt, starken mechanischen Belastungen standhalten zu können, und für seine Hitzeresistenz, seine Reißfestigkeit sowie Abriebbeständigkeit. Daher findet das Material häufig in der Herstellung belastbarer Bauteile Anwendung, etwa in der Automobil– sowie Luft- und Raumfahrtindustrie, aber auch in der Medizintechnologie. Im 3D-Druck werden viele verschiedene Arten von Nylon angewendet, die sich in ihren Bezeichnungen je nach ihrer Anzahl der enthaltenen Kohlenstoffatome unterscheiden. Im FDM-Druck wird am häufigsten PA6 eingesetzt, wohingegen PA11 und PA12 in Pulver-Verfahren zum Einsatz kommen. Wenngleich sich die Anwendungsfelder von PA11 und PA12 überlagern, weisen die beiden Kunststoffe doch ein paar Unterschiede auf. In diesem Versus-Artikel stellen wir beide Materialien gegenüber und gehen auf ihre jeweiligen Eigenschaften, ihre Herkunft, ihre Druckanforderungen und schließlich auf die Anwendungen und Preiskategorien ein.
Herkunft und mechanische Eigenschaften
Polyamide werden anhand der Nomenklatur unterschieden und die Zahl hinter der gemeinsamen Kennzeichnung PA richtet sich nach der jeweiligen Anzahl der Kohlenstoffatome. PA11 und PA12 scheinen daher recht nah beieinander zu liegen. Dennoch unterscheiden sich die beiden Nylon-Arten in vielerlei Hinsicht- und das fängt schon bei der Herkunft bzw. Herstellung an. PA12 ist ein thermoplastischer, teilkristalliner und linear aufgebauter Kunststoff, der aus Erdgas- bzw. Erdöl gewonnen wird. Durch chemische Verfahren erhält man Laurinlactam, welches das Ausgangsmolekül für die Herstellung von PA12 darstellt. Die Chemischen Werke Hüls AG stellten 1963 in Zusammenarbeit mit den Emser Werken in Domat erstmals PA12 vor. Seither hat sich das Homopolymer, welches aus einer Monomerkomponente besteht, in vielen Anwendungen etabliert. Trotzdem gelangt PA12 aufgrund seiner Herkunft und deren Umweltauswirkungen immer häufiger ins Kreuzfeuer.
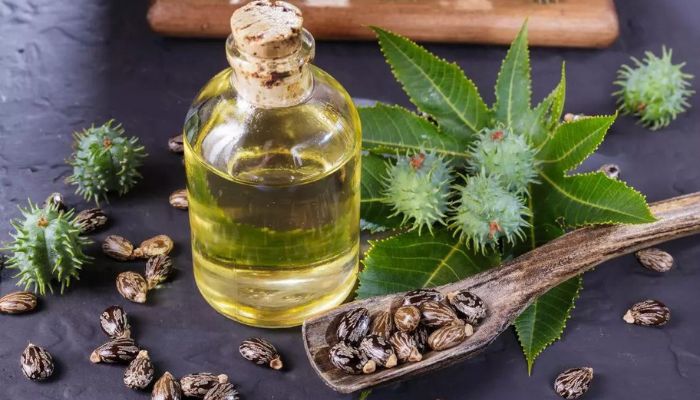
PA11 wird aus Rizinusöl gewonnen und gilt daher als umweltfreundlichere Alternative zu PA12. (Bild: Jellypipe)
Im Zuge des Fokus auf mehr Nachhaltigkeit und dem Bestreben einer “grüneren” Produktion, greifen Unternehmen zu alternativen Materialien mit ähnlichen Eigenschaften. Dies hat den Aufschwung von PA11 befeuert, denn dieses Polyamid ist in seiner Herkunft biologisch. PA11 wird aus erneuerbaren Rohstoffen hergestellt, welche aus pflanzlichen Derivaten gewonnen werden. Meist wird dafür Rizinusöl verwendet, welches wiederum aus den Samen des afrikanischen Wunderbaums “Ricinus communis” gewonnen wird, indem diese gepresst werden. Aus dem Rizinusöl wird durch eine Monomersynthese eine Aminosäure, nämlich die 11-Ainoundecansäure. Durch die anschließende Polymerisation der Monomere entsteht dann PA11. Dieses ähnelt in seiner Herkunft daher eher PA6 und liegt weit von seinem Kennzahl-Nachbarn PA12 entfernt. Wenngleich PA11 als die nachhaltigere Alternative aufgrund seiner biobasierten Herkunft gilt, ist es nicht biologisch abbaubar. Wie auch andere Polyamide muss es in einem spezialisiertem Sammlungssystem sortiert werden, bevor es zur Wiederverwertung aufbereitet werden kann.
Obwohl die Herkunft von PA11 und PA12 doch sehr unterschiedlich ist, nähern sie sich in Bezug auf ihre mechanischen Eigenschaften wieder an, weshalb sie in der Industrie häufig auch für ähnliche Zwecke eingesetzt werden. PA11 und PA12 gelten so als außerordentlich robust, fest und zäh und überzeugen durch ihr Gleit- und Verschleißverhalten und ihre chemische Beständigkeit. PA12 gilt als leichtester aller Polyamid-Kunststoffe und unterscheidet sich von den anderen Polyamiden durch seine geringe Konzentration an Amidgruppen. Außerdem hängt PA12 die anderen Polyamide in Bezug auf seine geringe Wasseraufnahme und Dichte ab. Obwohl auch PA11 verhältnismäßig wenig Wasser für ein Polyamid aufnimmt, kann es in dieser Hinsicht nicht mit PA12 mithalten. Seine Vorzüge liegen in seinen mechanischen Eigenschaften, welche die von PA12 übertrumpfen. PA11 weist eine hohe Duktilität auf und eine hervorragende Schlagfestigkeit. Es ist sehr abriebfest, ermüdungsfest und Teile aus PA11 glänzen durch eine höhere Isotropie. Es hält Temperaturen bis zu maximal 190° C statt, wenngleich die Dauertemperaturen im Bereich von -40° C bis 125°C liegen. Die fertigen PA11-Teile sind sowohl fest als auch flexibel, langlebig und verfügen über eine matte Oberfläche in opaker Farbe. Diese finden wir auch bei Teilen aus PA12. In beiden Fällen können die Teile eingefärbt werden.
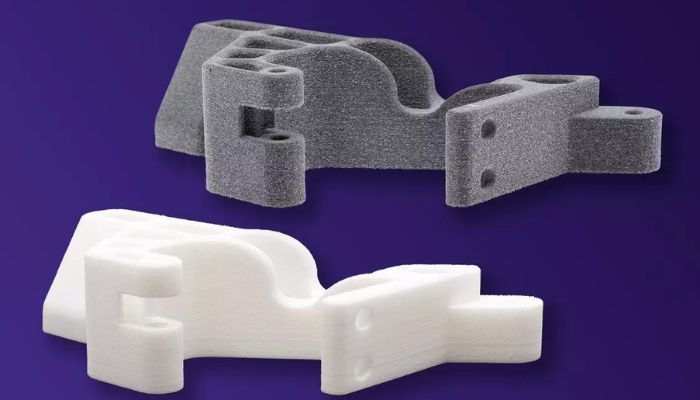
PA 12 (weiß) ist die leichteste Nylon-Art, wohingegen PA11 (grau) bessere mechanische Eigenschaften aufweist. (Bild: Jellypipe)
Hinsichtlich der Einsatztemperatur schneidet PA12 im Gegensatz zu PA11 schlechter ab, da es zwar dem Extrembereich von -50°C – 150°C standhält, sein Dauertemperaturgebrauch aber nur bei 50-80°C liegt. Wie PA11 ist es ebenfalls sehr abriebbeständig und weist einen hohen Ermüdungswiderstand auf. Es ist beständig gegen Fette, Öle, Lösemittel, Alkalien und Salzlösungen und daher sind gefertigte Teile aus PA12 sehr verschleißfest und gut schweiß- und klebbar. PA12 ist nicht nur das leichteste PA, sondern auch das beständigste gegen Spannungsrissbildung. Obwohl das Schlagverhalten von PA12 sehr gut ist, kann es nicht ganz an jenes von PA11 herankommen. PA12 kann im direkten Vergleich mit PA11 auch nicht ganz mithalten, was Festigkeit und Härte betrifft. Aus diesem Grund wird PA12 häufig durch Additive wie Glasfasern oder Carbonfasern verstärkt, um dieses Manko auszugleichen.
Beide Materialien sind meist gewebeverträglich und die daraus gefertigten Teile eignen sich für den Kontakt mit menschlicher Haut. Zu erwähnen ist jedoch, dass PA12 von manchen Herstellern auch lebensmittelecht ist und daher für Teile mit Lebensmittelkontakt verwendet werden kann, bei PA11 trifft dies nicht grundsätzlich zu. Es gibt aber PA11-Pulver, etwa das PA11 Blue von APC-Tec, die von der FDA für Lebensmittelkontakt zugelassen sind. In Bezug auf den Einsatz mit Lebensmitteln und dem Kontakt mit menschlichem Gewebe müssen demnach die einzelnen Angebote je nach Hersteller geprüft werden.
3D-Druck mit PA11 und PA12
Im 3D-Druck wird PA vorrangig als Filament und Pulver verarbeitet. Wir finden auch PA-Harz für das SLA-Verfahren, welches die Eigenschaften von PA-Thermoplasten imitiert. PA-Filament betrifft meist PA6, welches hauptsächlich in dieser Form und nur eingeschränkt als Pulver verfügbar ist und auch Verarbeitungsproblematiken mit sich ziehen kann. Bei den pulverbasierten Verfahren hingegen kommen in erster Linie PA11 und PA12 zum Einsatz. Das liegt an den thermoplastischen Eigenschaften des Materials, denn Nylon lässt sich besonders gut mittels Wärme verformen oder verbinden. Verschiedene Hersteller bieten so PA11 oder PA12 für den 3D-Druck mit Pulver an, darunter Selektives Lasersintern (SLS), Multi Jet Fusion (MJF), High Speed Sintering (HSS) und Selective Absorption Fusion (SAF). Diese Verfahren zeigen durch eine hohe Produktivität auf und das nicht für die Teile verwendete Pulver kann in einem bestimmten Ausmaß wiederverwertet werden. Bei SLS können ca. 50 % des Pulvers wiederverwertet werden, bei MJF liegt diese Rate noch höher, nämlich bei 70 %, wenngleich die tatsächlichen Raten je nach Materialhersteller variieren können. HP experimentiert derzeit mit Materialien, die zu 99 % wiederverwertbar sind.
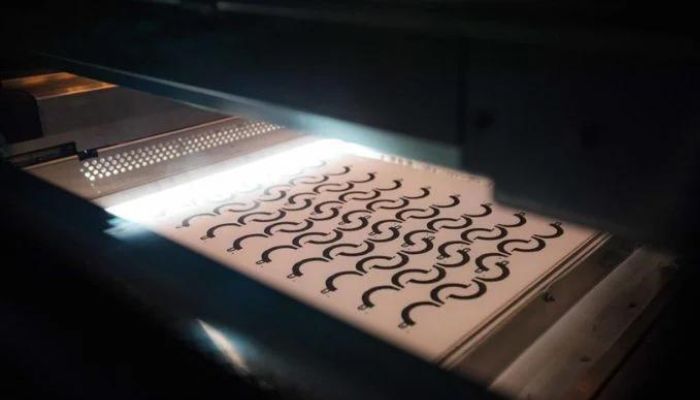
MJF-Verfahren (Bild: Hubs)
PA12 wird tendenziell häufiger in der additiven Fertigung genutzt als PA11. Dies liegt daran, dass PA12 zu einem früheren Zeitpunkt verfügbar war und sich sein Einsatz in vielen Unternehmen bewährt hat, aber auch daran, dass sein Schmelzpunkt niedriger liegt als der von PA11 und daher weniger Energieaufwand nötig ist. PA12 schmilzt bei 175-180° (je nach Hersteller), wohingegen PA11 erst bei rund 200° schmilzt. Außerdem ist für die Verarbeitung von PA11 eine inerte Atmosphäre empfehlenswert. Sind SLS-Polymere über einen längeren Zeitraum sehr hohen Temperaturen ausgesetzt, neigen sie nämlich zur Oxidation. Wird diese allerdings begrenzt, indem die Luft entfernt wird, verbessern sich die Materialeigenschaften der Druckteile und die Neuzuführungsrate kann zusätzlich verringert werden. Da PA11 eine höhere Temperatur zum Schmelzen erfordert als PA12, sind diese Vorteile vor allem beim Verarbeiten von PA11 interessant.
Es sei anzufügen, dass Maschinen nicht nach Belieben mit PA11 und PA12 zu füllen sind und diese Nylon-Varianten nicht miteinander mischbar sind. Durch die unterschiedlichen Schmelztemperaturen kann PA11 und PA12-Pulver nicht miteinander vermischt werden und es können in einem Druckauftrag nicht zwei verschiedene Materialien verarbeitet werden. Auch die Verarbeitung von unterschiedlichen Materialien in zwei aufeinander folgenden Aufträgen stellt eine Herausforderung dar, denn es bleibt immer etwas Restpulver im Bauraum des Druckers. Dieses muss präzise abgesaugt werden, da auch minimale Rückstände eines anderen Pulvers Schäden am Bauteil verursachen können. Dies zieht starke negative Konsequenzen in Bezug auf Qualität und Leistung mit sich, aber auch in Hinblick auf die Ökonomie. Aus diesem Grund entscheiden sich viele Anwender dazu, nur ein Material pro Maschine zu verwenden und gegebenenfalls in mehr Anlagen zu investieren. Allerdings gibt es ausgewählte SLS-Maschinen, die beide Materialien in einem Druckvorgang verarbeiten können und so in der Lage sind, Multi-Material-Teile zu fertigen, z.B. der SnowWhite2 von Sharebot.
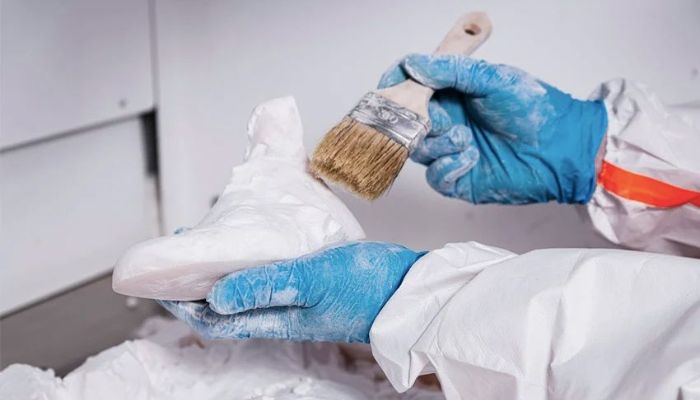
Ein wichtiger Schritt bei allen Pulver-basierten Verfahren ist die Nachbearbeitung. (Bild: Protiq)
Nachbearbeitung
Für welches Verfahren Sie sich für den Druck mit PA11 und PA12 auch entscheiden, die Nachbearbeitung ist ein unerlässlicher Schritt und betrifft sowohl die Teile aus PA11 als auch jene aus PA12. In diesem Punkt gibt es also keine Unterschiede zwischen den Materialien, denn einige Nachbearbeitungsschritte sind für beide zwingend erforderlich, wohingegen andere für beide optional sind. Egal, ob die Bauteile aus PA11 oder PA12 gefertigt wurden, erfolgt zunächst das Depowdering, bei dem die Teile vom Pulverkuchen entnommen werden und das Pulver rundherum abgesaugt wird. Dieses kann dann in gewissem Ausmaß in einem neuen Druckvorgang wiederverwertet werden. Verschiedene Verfahren erlauben dann die erweiterte Reinigung der Teile, da immer noch etwas Restpulver an den Teilen haftet, und eine verbesserte Oberflächenbeschaffenheit. Beispiele für Post Processing Verfahren sind Wasserstrahl-, Luftstrahlen- und Perlenstrahlenverfahren, aber auch das chemische Glätten und die Trommelpolitur. Es ist in einem weiteren Schritt auch möglich, die Bauteile aus PA11 und PA12 zu lackieren oder zu färben.
Anwendungen
Die beiden zu der gleichen Kunststoff-Gruppe zugehörigen Materialien sind in einer Vielfalt an Anwendungen im 3D-Druckverfahren zu finden, wobei auch ein paar Überschneidungen hinsichtlich ihrer Einsatzfelder vorliegen.
Im Bereich der Medizin werden sowohl PA11 als auch PA12-Pulver eingesetzt, sofern diese als biokompatibel vom Hersteller ausgewiesen sind. Sie werden für die Herstellung von Prothesen, Orthesen Medizinprodukte und medizinische Geräte verwendet. PA 11 wird im medizinischen Bereich jedoch stärker für seine Biokompatibilität und Flexibilität geschätzt als PA12, welches hingegen eine allgemein höhere Festigkeit aufweist.
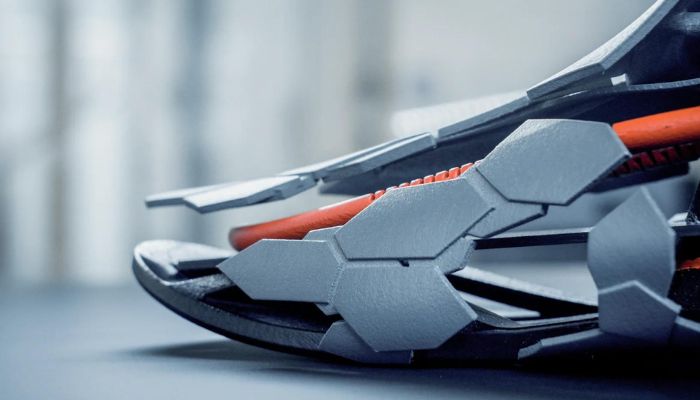
PA11 und PA12 werden häufig für Prothesen und Orthesen eingesetzt. (Bild: EOS)
Auch in der Automobilindustrie finden beide Materialen Anwendung im 3D-Druck. PA11 wird dort für Kunststoffbauteile für den Prototypenbau von Fahrzeugen, aber auch für die Serienproduktion verwendet. Es wird zudem aufgrund seiner Schlagzähigkeit und chemischen Beständigkeit für die Herstellung von crashrelevanten Fahrzeugteilen für den Innenbereich angewendet (PA11 splittert nicht), aber auch für den Außenbereich, etwa für Dichtungen, Motorkomponenten und Verkleidungen. Auch PA12 wird im 3D-Druck in der Automobilindustrie verwendet, nämlich für den Fahrzeugbau, insbesondere für Präzisions-Schläuche und –Rohre, vor allem für druck- und schlagfeste Kraftstoffleitungen. In der Luftfahrt findet PA11 im 3D-Druck aufgrund seiner Schlagfestigkeit und seines geringen Gewichts zur Herstellung von leichten, jedoch stabilen Bauteilen Anwendung, etwa für Verkleidungen und innere Strukturteile von Flugzeugen. PA12 wird in dem Bereich ebenfalls verarbeitet, typischerweise für den Flugzeugbau, wo es wie im Automobilbau für Präzisions-Schläuche und –Rohre – vor allem für druck- und schlagfeste Kraftstoffleitungen – verarbeitet wird. In den Bereichen der Automobil- und Luftfahrtindustrie wird PA11 im Gegensatz zu PA12 etwa für die mit ihm produzierten leichteren Bauteile und seinem Beitrag zur Kraftstoffeffizienz geschätzt, während die Vorteile von PA12 insbesondere in seiner Steifigkeit und Härte für belastbare Bauteile gesehen werden.
In der Sportindustrie werden ebenfalls beide Materialien verwendet – PA11 wegen seiner Abriebfestigkeit etwa für Skibeläge und Sohlen von Fußballschuhen sowie wegen seiner Kombination aus Festigkeit und Flexibilität für Sportgeräte. PA12 findet aufgrund seiner besonderen mechanischen Widerstandsfähigkeit bei niedrigen Temperaturen bei Wintersportausrüstungen wie Abfahrts- und Langlaufskischuhe oder Skibindungen Anwendung. Auch in dieser Industrie wird in der Nutzung von PA11 vor allem der Vorteil leichterer und dennoch robuster Teile gesehen, während sich PA12 durch seine Festigkeit und Steifigkeit kennzeichnet.
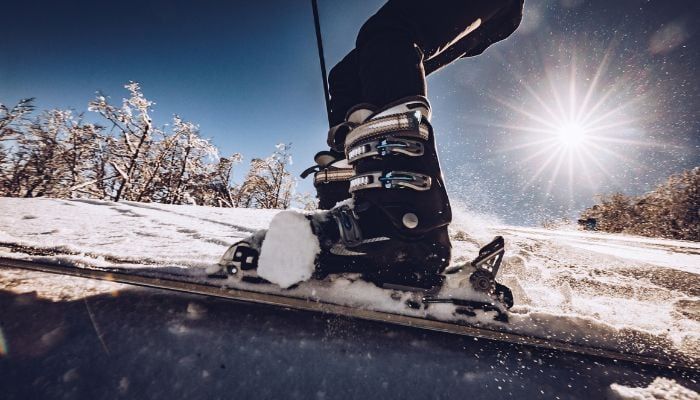
PA11 und PA12 werden auch im Sportbereich eingesetzt. (Prodways/Salomon)
Im Maschinenbau, der Elektrotechnik bzw. Elektronik sowie Verpackungsindustrie werden ebenfalls beide Materialien verwendet, wobei PA11 insbesondere für seine Langlebigkeit und PA12 für seine hohe Zähigkeit geschätzt wird. Beide Materialien werden in den Bereichen hingegen aufgrund ihrer chemischen Beständigkeit verwendet. PA12 findet in all diesen Bereichen etwa Anwendung für die Herstellung von Präzisionsschläuchen- und Rohren, insbesondere für druck- und schlagfeste Kraftstoffleitungen sowie für Antriebselemente in feuchter Umgebung bzw. Getriebeteile unter Wasser – wo eine hohe Maßhaltigkeit notwendig ist – sowie für Maschinenbau-Bauteile wie Scharniere und Zahnräder sowie Isolierfolien und aromadichte Folien. In der Elektrotechnik und Elektronik wird PA11 als Isolier- und Schutzmaterial für Kabel, Stecker und Gehäuse von elektronischen Geräten und wegen seiner besonders hohen Langlebigkeit generell für hochtechnische Anwendungen genutzt.
Im Maschinenbau kommen beide Materialien zum Einsatz. Aufgrund der Flexibilität von PA11 ist es beliebt im Einsatz für Schlauch- und Rohrmaterialien, welche für hydraulische Bremssysteme zugelassen sind, und für diverse bewegliche Elemente. Auch für Bauteile mit dünnen Wandstärken und Gitterstrukturen ist PA11 aufgrund seiner Flexibilität geeignet, da es dennoch dünne robuste Strukturen gewährleistet.
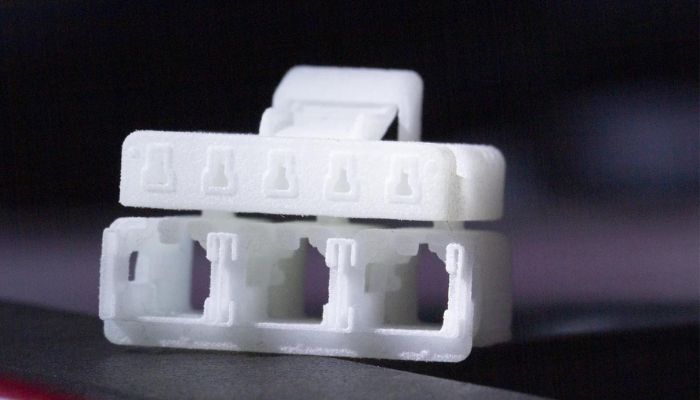
Nylon-Stecker (EOS)
Hersteller und Preise
Allgemein lässt sich feststellen, dass PA12 meist die teurere Variante der Nylon-Familie im Vergleich zu PA11 ist, da die Nachfrage nach PA11 aktuell noch geringer ist. PA11 ist etwa – meist in Pulverform – bei einigen Herstellern bereits für 50€/kg zu kaufen, bei anderen jedoch erst ab einem Preis von 200€/kg. Die Variationen im Preis für die gleiche Sorte Pulver hängen damit zusammen, ob es sich um Standard- oder verstärktes Pulver handelt. Vergleicht man die fertigen Bauteile aus den beiden verschiedenen Materialien preislich miteinander, lässt sich unschwer erkennen, dass aus PA11 in Serie gefertigte Teile deutlich günstiger sind als aus PA12, je nach Produktionsmenge etwa 30%. Bei der Herstellung von Einzelstücken lohnt es sich aus Kostenperspektive hingegen, PA12 zu verwenden.
Die beiden Materialien werden von einer Vielfalt von Herstellern zur Verfügung gestellt. Zu einigen der bekanntesten Hersteller des PA11-Materials gehören EMS-Grivory oder die französische Arkema-Group, welche PA11 unter dem Namen RILSAN® PA11 verkauft. PA12 bietet die Arkema ebenfalls an, ehemals unter demselben Namen wie PA11, heutzutage zur besseren Unterscheidung unter dem Namen RILSAMID®. PA12 wird auf dem Markt auch häufig als VESTAMID® oder VESTOSINT® gehandelt. Der Chemiekonzern BASF stellt ebenfalls sowohl PA12 als auch PA11 jeweils in Pulverform zur Verfügung. PA12 ist darüber hinaus auf Seiten von Herstellern wie Evonik zu finden, jedoch auch von 3DSystems und Farsoon, welche mit Chemieunternehmen entwickelte Pulver anbieten, diese materiellen Entwicklungspartnerschaften aber vertraulich behandeln.
Neben der Erfindung des umweltfreundlicheren Materials PA11 werden zunehmend Anstrengungen verschiedener Hersteller unternommen, die Produktion von PA12 biologischer und grüner zu gestalten. Der deutsche Anbieter von Anlagen und Werkstoffen EOS bietet beispielsweise PA12 als eine leistungsfähige Alternative für die im Spritzguss geschätzten Kunststoffe ABS oder PA6 an und hat die Produktionseffizienz des Materials kontinuierlich gesteigert – etwa durch die Senkung des CO2-Fußabdrucks durch die Nutzung erneuerbarer Energien. Auf dem Markt sind außerdem Polyamidpulver erhältlich, die mit Kevlar, Kohlenstofffasern oder sogar Glaskugeln versetzt wurden. HP stellt beispielsweise ein solches Thermoplast zur Verfügung, das mit 40% Glasperlen gefüllt ist und eine hohe Wiederverwertungsrate aufweist. Das Material ist unter dem Namen HP 3D High Reusability PA12 Glass Beads erhältlich. Vor Kurzem hat HP zudem bekanntgegeben, dass das Unternehmen ein neues zusammen mit Arkema entwickeltes PA12-Pulver mit dem Namen HP 3D HR PA 12 S auf den Markt bringt, welches sich durch seine hohe Wiederverwendbarkeitsrate von bis zu 85 % auszeichnet und somit Abfälle senkt.
Haben Sie bereits Erfahrungen mit PA11 und PA12 im 3D-Druck? Lassen Sie uns dazu gerne einen Kommentar da oder teilen Sie uns Ihre Meinung auf Facebook oder LinkedIN mit. Möchten Sie außerdem eine Zusammenfassung der wichtigsten Neuigkeiten im 3D-Druck und der additiven Fertigung direkt und bequem in Ihr Postfach erhalten? Dann registrieren Sie sich jetzt für unseren wöchentlichen Newsletter.