Ist der Durchbruch für den 3D-Druck mit Wolfram gelungen?
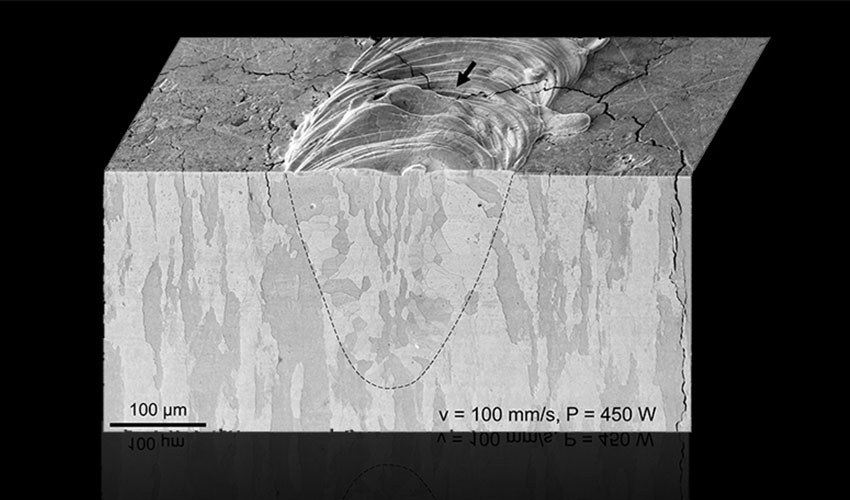
Forscher der Lawrence Livermore National Laboratory (LLNL) haben nach Gründen gesucht, warum Wolfram bei der Verwendung im 3D-Druck zur Bildung von Rissen neigt. Für die Untersuchung nutzten sie eine Kombination von thermomechanischen Simulationen mit Hochgeschwindigkeitsvideos. Dadurch war es ihnen möglich den Übergang von Duktilität zu Sprödigkeit (DBT) während des 3D-Drucks in Echtzeit zu visualisieren. Sie fanden heraus, dass Mikrorisse während des Erwärmen und Abkühlens von Wolfram entstehen.
Was ist Wolfram?
Wolfram ist ein weiß glänzendes Schwermetall, das sich durch eine moderate thermische Ausdehnung sowie einen hohen Schmelzpunkt und eine hohe Wärmeleitfähigkeit auszeichnet. Um genau zusagen, ist Wolfram das chemische Element mit dem höchsten Schmelz- und Siedepunkt. Durch seine thermomechanischen Eigenschaften der Legierung, in Kombination mit der hohen Dichte und der niedrigen Sputter-Erosionsrate, ist es gut geeignet für Anwendungen in extremen Umgebungen. Daher wird Wolfram zum Beispiel für die Glühwendel in Glühlampen verwendet. Da Wolfram bei der additiven Fertigung jedoch zur Sprödigkeit und Mikrorissbildung neigt, ist die Anwendung des seltenen Metalls noch nicht weit verbreitet.
Was ist der Grund für die Rissbildung?
Die LLNL Forscher haben es geschafft die Mikrorisse mit Variablen wie Eigenspannung, Dehnungsrate und Temperatur in einen Zusammenhang zu bringen. Dadurch haben sie herausgefunden, dass der DBT-Übergang der Grund für die Rissbildung ist. Der DBT-Übergang ist ausschlaggebend für die Bestimmung der Grenzen des unteren thermischen Arbeitsbereichs eines Druckmaterials. DBT tritt unweigerlich auf, wenn Metalle abkühlen, nachdem sie hohen Temperaturen ausgesetzt wurden, wie sie beispielsweise beim 3D-Druck auftreten. Die niedrigeren Temperaturen führen zu einem dramatischen Verlust der Duktilität, was zu Eigenspannungen und Mikrorissen führt.
Die experimentellen Beobachtungen und rechnerischen Modellierungen wurden mit dem Diablo-Finite-Elemente-Code von LLNL durchgeführt. So fanden die Forscher heraus, dass Mikrorisse in Wolfram in einem kleinen Fenster zwischen 450 und 650 Grad Kelvin auftreten und von der Dehnungsrate abhängen, die direkt von den Prozessparametern beeinflusst wird. Sie konnten auch die Größe der Fläche, die durch Risse beeinflusst wird, und die Morphologie des Rissnetzes mit lokalen Eigenspannungen in einen Zusammenhang bringen
Wird man zukünftig besser mit Wolfram 3D-drucken können?
Die Arbeit der Forscher könnte ein detailliertes, grundlegendes Verständnis des Einflusses von Prozessparametern und Schmelzgeometrie auf die Rissbildung liefern. Es zeigt, welchen Einfluss die Materialzusammensetzung und die Vorwärmung auf die strukturelle Integrität von Teilen, die mit Wolfram gedruckt wurden, haben. Das Fazit der Forscher lautet, dass die Zugabe bestimmter Legierungselemente dazu beitragen könnte, den DBT-Übergang zu reduzieren und das Metall zu verfestigen, während das Vorwärmen dazu beitragen könnte, die Mikrorissbildung zu mindern. Darüber hinaus könnte auch die Kontrolle des Sauerstoffgehaltes der Baukammer wichtig sein, um die Dehnungsraten zu senken.
Der Co-Chefermittler des Teams, Manyalibo „Ibo“ Matthews, blickt optimistisch auf die zukünftige Nutzung von Wolfram: „Aufgrund seiner einzigartigen Eigenschaften hat Wolfram eine bedeutende Rolle bei missionsspezifischen Anwendungen für das Energie- und Verteidigungsministerium gespielt. Diese Arbeit trägt dazu bei, den Weg zu einem neuen Verarbeitungsgebiet für die additive Herstellung von Wolfram zu ebnen, was einen bedeutenden Einfluss auf diese Missionen haben kann.”
Glauben Sie, dass Wolfram zukünftig mehr verwendet wird für den 3D-Druck? Möchten Sie eine Zusammenfassung der wichtigsten Neuigkeiten im 3D-Druck und der Additiven Fertigung direkt und bequem in Ihr Postfach? Registrieren Sie sich jetzt für unseren wöchentlichen Newsletter und folgen Sie uns auf Facebook und Twitter um stets auf dem Laufenden zu bleiben! Außerdem sind wir auch auf LinkedIN, Xing und auf Youtube zu finden.