MIT-Ingenieure drucken 3D-Glasbausteine für den Bau von Gebäuden
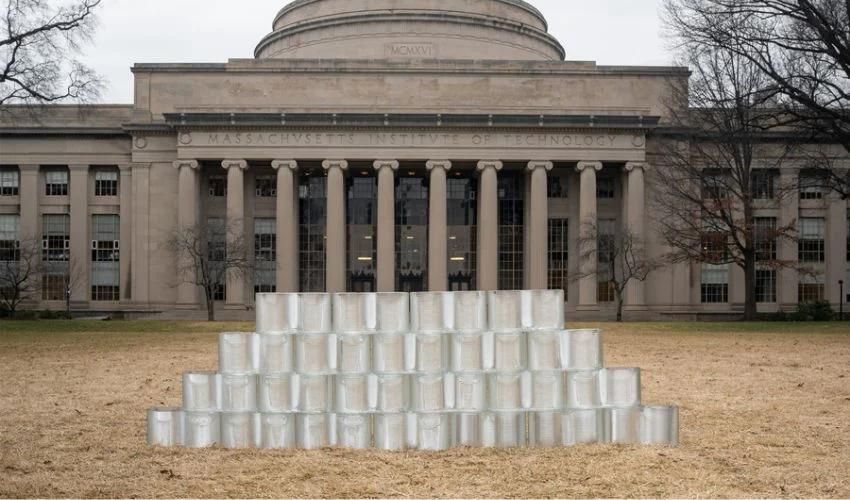
Glas ist bemerkenswert, denn solange es nicht verunreinigt ist, kann es unendlich oft recycelt werden, ohne dass sich seine Eigenschaften ändern. Das macht einen Teil des Reizes seiner Verwendung in der additiven Fertigung aus. Im Vergleich zum traditionellen Glasguss können AM-Methoden eine größere Designflexibilität und geringere Kosten ermöglichen. Mit diesen Eigenschaften im Hinterkopf wollten die Ingenieure des MIT testen, ob die Verwendung von AM-Glas zur Herstellung von strukturellen Bauelementen möglich ist. Deshalb entwickelten sie 3D-gedruckte Glasbausteine, die wie LEGO-Steine gestapelt und ineinander gesteckt werden können.
Die Forschung wurde von den MIT-Ingenieuren Daniel Massimino, Ethan Townsend, Charlotte Folinus, Michael Stern und Kaitlyn Becker durchgeführt. Gemeinsam stellten sie starke, mehrschichtige Bausteine aus Kalk-Natron-Glas her, die jeweils die Form einer Acht haben. Jeder Stein hat zwei runde Zapfen wie ein LEGO-Stein, sodass sie endlos angeordnet und neu arrangiert werden können, was eine reiche Kompositionsvielfalt und einen langen Lebenszyklus ermöglicht. Wenn sie nicht neu angeordnet werden, können die Steine eingeschmolzen und erneut gedruckt werden.
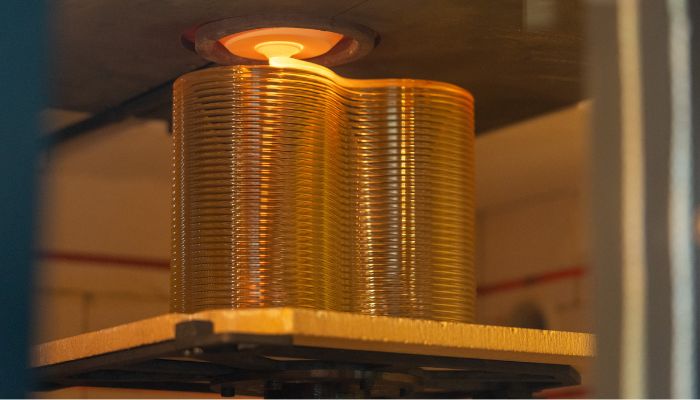
Drucken des Glasbausteins mit dem benutzerdefinierten 3D-Druckverfahren (Bild: Ethan Townsend)
In einem Artikel von MIT News erklärte Massimino: „Mit der Achterform können wir die Bausteine einschränken und sie gleichzeitig zu Wänden zusammensetzen, die eine gewisse Krümmung aufweisen.“ Das rekonfigurierbare Glasmauerwerk der Ingenieure entspricht dem Konzept des zirkulären Bauens, d. h. der Idee, dass Baumaterialien, wo immer möglich, wiederverwendet werden sollten, um die mit der gesamten Konstruktion eines Gebäudes verbundenen Kohlenstoffemissionen zu reduzieren. Die Nachhaltigkeit der Glassteine war ein treibender Faktor für die Forschung.
Die Material-Mischung macht’s
Die MIT-Ingenieure verwendeten einen kundenspezifischen Glas-3D-Drucker namens Glass 3D Printer 3 (G3DP3), der von der MIT-Ausgründung Evenline bereitgestellt wurde. Das Gerät verwendet einen Ofen, um zerkleinerte Glasflaschen in eine druckbare Form zu schmelzen und sie dann schichtweise aufzutragen. Der Drucker kann ein maximales Volumen von 32,5 x 32,5 x 38 cm drucken, das für die Herstellung von Mauersteinen in voller Größe geeignet ist.
Das Team druckte drei Arten von Bausteinen – vollständig hohle, gegossene und vollständig gedruckte – und stellte fest, dass „hohle Mauersteine einen unmittelbareren Weg zur Umsetzung bieten, während vollständig gedruckte Steine das Potential haben, eine vollständig gläserne, transparente und kreisförmige Methode zur Herstellung von Bauelementen zu bieten.“
Sie testeten die Stärke der Blöcke mit einer industriellen Hydraulikpresse und stellten fest, dass die stärksten Blöcke dem gleichen Druck wie ein Betonblock standhalten konnten. Die stärksten Blöcke waren diejenigen mit einer separaten, ineinander greifenden Funktion an der Unterseite des Blocks aus einem anderen Material. „Glas ist ein kompliziertes Material, mit dem man arbeiten muss“, sagte Becker in demselben Artikel von MIT News. „Die ineinander greifenden Elemente aus einem anderen Material waren in diesem Stadium am vielversprechendsten.“ Derzeit wird geprüft, ob weitere ineinander greifende Elemente aus Glas gedruckt werden können, aber das ist kein Hindernis für eine Ausweitung des Projekts.
Die Ingenieure bauten eine Glaswand auf dem MIT-Campus, um das Potential der 3D-gedruckten Glasbausteine zu zeigen. In Zukunft wollen sie größere und komplexere Strukturen mit den Steinen bauen und glauben, dass sie für Fassaden und Innenwände verwendet werden könnten. Weitere Informationen finden Sie im Artikel von MIT News oder in der hier veröffentlichten Studie.
Was halten Sie den Lego-Glasbausteinen des MIT? Lassen Sie uns dazu einen Kommentar da, oder teilen Sie es uns auf Facebook oder LinkedIN mit. Möchten Sie außerdem eine Zusammenfassung der wichtigsten Neuigkeiten im 3D-Druck und der additiven Fertigung direkt und bequem in Ihr Postfach erhalten? Dann registrieren Sie sich jetzt für unseren wöchentlichen Newsletter.
*Titelbildnachweis: Ethan Townsend/MIT News