PEEK, ULTEM und weitere Hochleistungsthermoplaste als Material für den 3D-Druck
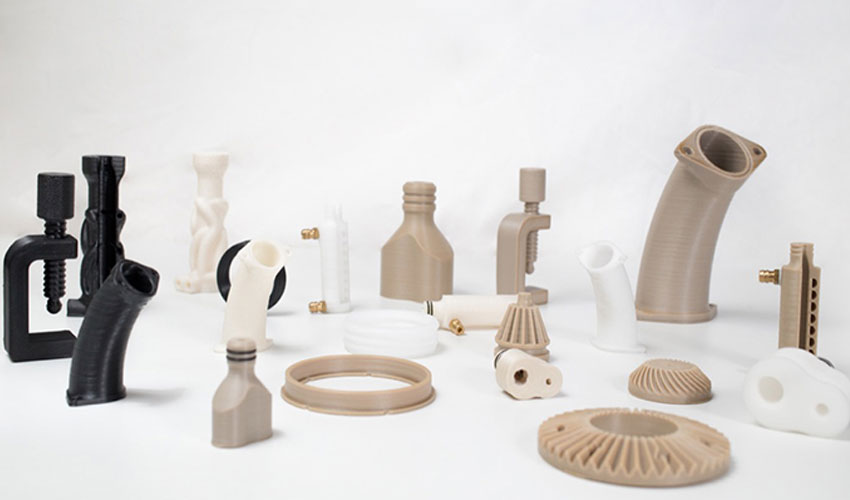
In den letzten Jahren sind Hochleistungsthermoplaste zu einem viel diskutierten Thema im 3D-Druck geworden, und der Markt für sie wächst rasant. Diese Materialien sind in der Branche aufgrund ihrer Festigkeit und Leichtigkeit attraktiv und es gibt eine Reihe verschiedener Materialien, die für die additive Fertigung verwendet werden können. Ein Beispiel ist Polyaryletherketon (PAEK), eine Familie von teilkristallinen Kunststoffen, die hohen Temperaturen standhalten und gleichzeitig eine enorme Festigkeit aufweisen. PAEK wird hauptsächlich in Form von Polyetheretherketon (PEEK) und Polyetherketonketon (PEKK) verwendet, zwei Materialien mit hoher Steifigkeit. Eine wesentlich kostengünstigere Alternative, Polyetherimid (PEI), auch bekannt als ULTEM, hat sich jedoch ebenfalls zunehmend verbreitet. Aber was genau sind Hochleistungskunststoffe? Wie kann man mit ihnen drucken? Wer sind die Hersteller? Im folgenden Leitfaden über die PAEK- und PEI-Familien erfahren Sie alles, was Sie über diese Materialien wissen müssen.
Herstellung und Eigenschaften von Hochleistungspolymeren
Das erste, was man über Hochleistungspolymere wissen sollte, ist, dass sie zwar gemeinsame Eigenschaften haben, aber nicht alle genau dasselbe sind. Generell lässt sich jedoch feststellen, dass Hochleistungsthermoplaste, insbesondere PEEK, so stark wie Stahl und 80 % leichter als Metall sind, was sie in der Fertigungsindustrie äußerst begehrt macht. Neben der außergewöhnlichen mechanischen und thermischen Beständigkeit von bis zu 250 °C im Dauerbetrieb sind PAEK-Werkstoffe im Gegensatz zu den meisten anderen Kunststoffen auch beständig gegen das Auflösen in Ölen und anderen Substanzen. Im Brandfall werden fast keine Gase oder schädlichen Dämpfe freigesetzt.
Und obwohl sie in der additiven Fertigung immer weiter verbreitet sind, ist es unbestreitbar, dass ihr Wachstum langsamer war als das anderer Polymere. Tatsächlich gibt es diese Materialien schon seit über drei Jahrzehnten, auch wenn sie durch Spritzguss oder maschinelle Bearbeitung verwendet wurden. Zunächst war Stratasys das einzige Unternehmen, das in der Lage war, Drucker herzustellen, die mit den hohen Temperaturen umgehen konnten, die zum Schmelzen von PAEK- und PEI-Polymeren erforderlich sind. Als sich der Markt jedoch zu öffnen begann, hatten auch andere Unternehmen die Möglichkeit, mit diesen Druckern zu experimentieren, was zu einer Massenvermarktung ihrer Erfindungen führte. Mit der Zeit und dem Abbau der Marktzutrittsschranken sehen wir, dass immer mehr Unternehmen in diesen Bereich einsteigen und mit der Herstellung von Druckern beginnen, die PAEK-Thermoplaste verarbeiten können.
Ein weiteres Material, PEI, wurde erstmals in den späten 1980er Jahren von der Kunststoffabteilung von General Electric entwickelt. Im Jahr 2007 erwarb jedoch SABIC, eines der größten öffentlichen Unternehmen Saudi-Arabiens, die Abteilung und damit die Rechte an der Marke ULTEM. Da das Material eine kostengünstigere Alternative zu PEEK darstellt, stieß es aus finanzieller Sicht sofort auf großes Interesse. In Verbindung mit seinen verschiedenen bedeutenden physikalischen Eigenschaften, wie hohe Hitze-, Lösungsmittel- und Flammenbeständigkeit, Durchschlagfestigkeit und Wärmeleitfähigkeit, stellte es eine hervorragende Lösung für technische Projekte dar. ULTEM ist zu einem bevorzugten Material für technische Anwendungen mit sehr hohen Anforderungen geworden, z. B. in der Luft- und Raumfahrtindustrie.
3D-Druck mit Hochleistungskunststoffen
Im Allgemeinen werden PAEK- und PEI-Polymere entweder mit FDM (Fused Deposition Modeling) oder SLS (Selective Laser Sintering) gedruckt. In Anbetracht der Hochtemperaturfähigkeit dieser Polymere ist es jedoch verständlich, dass kein gewöhnlicher 3D-Drucker diese Filamente verarbeiten kann. Ein PAEK/PEI-3D-Drucker muss über eine Extruderdüse verfügen, die Temperaturen von über 300 °C verarbeiten kann, da dies der Schmelzpunkt dieser Polymere ist. Außerdem muss das Heizbett mindestens 150 °C erreichen, damit das Objekt entnommen werden kann. Schließlich sind stärkere Kühlmechanismen erforderlich, um das richtige Temperaturgleichgewicht in der geschlossenen Kammer zu gewährleisten.
Die Nachbearbeitung von Hochleistungsthermoplasten ist notwendig und wie bei jedem komplexen FDM-Druckteil werden Stützstrukturen benötigt. Bei PAEK und PEI kann es jedoch aufgrund der Steifigkeit des Endprodukts schwierig sein, den Support zu entfernen. Daher wird oft eine Reihe von Werkzeugen verwendet, um das Teil fertig zu stellen.
Beim SLS-Verfahren hingegen wird das Teil nahezu perfekt gedruckt, ohne dass zusätzliche Werkzeuge benötigt werden. Allerdings müssen die Hersteller die Verformung in Betracht ziehen. Nachdem der Druck eines Objekts beendet ist und die Temperatur in der Kammer sinkt, neigen die Polymere dazu, sich zu verkleinern. Aus diesem Grund sind PAEK und PEI beim Druck kleiner Objekte sehr beliebt, doch je größer das Teil ist, desto stärker ist der Verformungseffekt. Dieser lässt sich zwar bis zu einem gewissen Grad durch die Optimierung der wichtigsten Druckparameter wie Geschwindigkeit und Temperatur kontrollieren, bleibt aber eine Herausforderung.
Abgesehen davon ist die Verwendung von Hochleistungsthermoplasten noch lange nicht ausgereift. Es gibt immer noch Aspekte des Herstellungsprozesses, an denen gearbeitet wird und die ständig verbessert werden. Neue Innovationen verbessern diese Erfahrung jedoch ständig. Eine Reihe von Unternehmen arbeitet derzeit an einer FDM-Lösung, bei der die Stützstruktur des Objekts aus einem anderen Material gedruckt wird, damit er nach dem Druckvorgang schneller und einfacher entfernt werden kann. Darüber hinaus haben andere Unternehmen wie Kimya damit begonnen, Materialkombinationen anzubieten, um das Beste aus mehreren Materialien zu nutzen. Auf diese Weise kann das Endprodukt beispielsweise zu 70 % aus PEEK und zu 30 % aus Kohlefaser bestehen.
Anwendungen
Wie zu erwarten, ist eine Werkstofffamilie mit so vielen bedeutenden Eigenschaften in einer Vielzahl von Branchen nützlich. Die Automobilindustrie hat schnell begonnen, die einzigartigen Fähigkeiten von PAEK und PEI für eine Vielzahl von Anwendungen zu nutzen. Einer der Bereiche, in denen PAEK und PEI am stärksten ins Gewicht fallen, ist die Herstellung von kostengünstigen Schnellwerkzeugen für Spritzguss, Thermoformung, Vorrichtungen und Halterungen. Dies ermöglicht es Unternehmen, kleine bis mittlere Stückzahlen zu geringen Kosten zu produzieren, ohne in die Herstellung großer Mengen investieren zu müssen. Auch die Herstellung kundenspezifischer Teile wird zunehmend nachgefragt, da sie an bestimmte Anforderungen angepasst werden können und komplexe Änderungen erhalten können, die ihren strukturellen Aufbau verbessern.
Wie viele andere 3D-Druckmaterialien werden auch die PAEK- und PEI-Familien häufig im medizinischen Bereich eingesetzt. PEEK ist bekannt für die Abschirmung von Magnetresonanztomographen (MRI). Es gilt auch als fortschrittliches Biomaterial, das für medizinische Implantate, Verstärkungsstäbe und Wirbelsäulenfusionsgeräte verwendet wird. Da es kochendem Wasser und überhitztem Dampf standhalten kann, eignet es sich hervorragend für Gegenstände, die bei extrem hohen Temperaturen sterilisiert werden müssen.
Hochleistungsthermoplaste werden auch in der Luft- und Raumfahrtindustrie häufig verwendet. Chemische Beständigkeit, hohe Festigkeit im Verhältnis zum Gewicht und niedrige Brand-, Rauch- und Toxizitätswerte machen solche Polymere zum idealen Ersatz für Metall, das häufig für Raumfahrzeugteile und Werkzeuge verwendet wird. Thermisch-akustische Isolierungen, strukturelle Halterungen, Klammern und Abstandshalter, Befestigungselemente, Verbindungsstücke und Rohrsysteme sind nur einige Beispiele, bei denen die Luft- und Raumfahrttechnik PAEK und PEI einsetzt und das Gewicht der Teile oft um 70 % reduziert. Andere Branchen, in denen fortschrittliche Thermoplaste zum Einsatz kommen, sind die Schifffahrt, die Nuklearindustrie, die Öl- und Gasindustrie und viele mehr.
Wichtigste Hersteller und Preise der Materialien
Wie nicht anders zu erwarten, haben viele der großen Chemieunternehmen den Wandel, der sich bei den Hochleistungsthermoplasten im Bereich der additiven Fertigung abzeichnet, bereits erkannt. Daher ist es keine Überraschung, wenn Namen wie Arkema, Lehmann & Voss und Solvay (um nur einige zu nennen) genannt werden, wenn es um die Herstellung von PAEK-Materialien geht. Wenn es jedoch um PEI geht, ist die Marke ULTEM von SABIC im Moment die einzige auf dem Markt verfügbare.
Bei den Druckern, die PAEK und PEI verarbeiten können, hat der chinesische Hersteller INTAMSYS viel Aufmerksamkeit auf sich gezogen, da er eine Reihe von professionellen und Desktop-3D-Druckern anbietet, die für Hochleistungspolymere geeignet sind. Aber auch der niederländische Tractus3D erfreut sich immer größerer Beliebtheit, ebenso wie der deutsche Gigant EOS, der vor kurzem einen neuen HTLS-Drucker (Hochtemperatur-Lasersintern) auf den Markt gebracht hat, der diese Materialien verarbeiten kann.
Wie zu erwarten, sind diese Hochleistungspolymere jedoch nicht gerade günstig. PEEK, UTLEM und PEKK sind einige der teuersten 3D-Druckmaterialien auf dem Markt. ULTEM ist zwar eine etwas preiswertere Alternative, doch eine 1 kg-Spule des Filaments beginnt bei über 180 € und kostet je nach Marke und Materialeigenschaften oft viel mehr. PEEK kostet inzwischen oft über 270 € und bis zu über 650 € für 1 kg des Materials, während PEKK im Durchschnitt zwischen 370 und 460 € für dieselbe Menge kostet.
Wenn Sie sich für Filament aus diesen Materialien interessieren, müssen Sie auch bedenken, dass Sie nicht mit jedem beliebigen Drucker drucken können. Sie müssen in einen Drucker investieren, der, wie oben erwähnt, speziell für Hochleistungspolymere entwickelt wurde. Diese Drucker sind verständlicherweise auch teurer als ein preiswertes FDM-Modell. Viele beginnen bei über 4.500 € und die meisten liegen weit darüber. Dennoch haben wir im Laufe der Jahre gesehen, dass mit dem Wachstum des Marktes auch die Auswahlmöglichkeiten für die Verbraucher zunehmen. Vielleicht werden wir in naher Zukunft erleben, dass die Preise sowohl für Drucker als auch für Materialien sinken, wenn Anwendungen mit Hochleistungspolymeren in der additiven Fertigung noch weiter verbreitet werden.
Was halten Sie von der Verwendung von thermoplastischen Hochleistungspolymeren im 3D-Druck? Können Sie sich vorstellen, dass andere Branchen in naher Zukunft ebenfalls umgestaltet werden? Lassen Sie uns gerne einen Kommentar da, oder teilen Sie es uns auf Facebook oder LinkedIN mit. Möchten Sie außerdem eine Zusammenfassung der wichtigsten Neuigkeiten im 3D-Druck und der additiven Fertigung direkt und bequem in Ihr Postfach erhalten? Dann registrieren Sie sich jetzt für unseren wöchentlichen Newsletter.
Es ist beeindruckend zu erfahren, wie PEEK aufgrund seiner hervorragenden mechanischen und chemischen Eigenschaften in anspruchsvollen Anwendungen wie Luft- und Raumfahrt, Medizin und Industrie eingesetzt wird. Da bin ich ich gespannt, was als nächstes kommt.